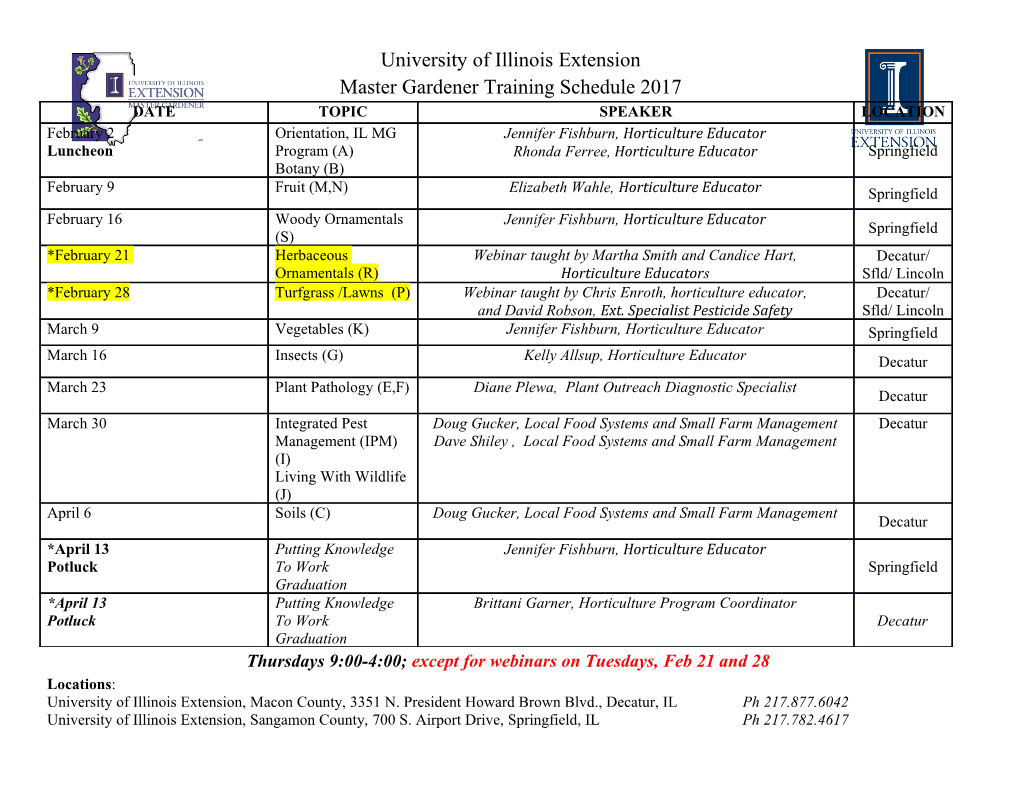
Reprinted From: PRODUCTS FINISHING Magazine Making Ti Tougher ADVANCES IN SELECTIVE PLatING ON TItaNIUM AEROSPACE ALLOYS By Darrin Radatz, Ani Zhecheva and Sid Clouser SIFCO Applied Surface Concepts igh strength and low weight, coupled with the ability to H readily form a tenacious surface oxide film, make titanium and its alloys useful in many appli- cations in the aerospace, industrial and medical fields. One of the most useful titanium alloys contains 6% aluminum and 4% vanadium (Ti-6Al-4V). A limitation of titanium alloys is relatively poor resistance to adhe- sive wear, which results in galling and cold welding, poor fretting behavior and a high coefficient of friction. Tribological performance can be improved by applying sur- face treatments and coatings while retaining the positive attributes of the underlying substrate. Coatings are also applied on titanium for heat reflection, emissivity, corro- sion resistance in hot acidic envi- ronments, conductivity, lubricity, brazing and resizing. One way to apply coatings to titanium alloys for aerospace and Brush plating is commonly used to repair and recondition aerospace components. As Received Abraded Etched Scanning electron micrographs of Ti-6Al-4V surface after each process step. Abrasion, anodic etching and cathodic activation result in a dense nickel strike layer with a slightly nodular morphology. Activated Nickel Plated other applications is selective an acid fluoride-containing electro- techniques. These included dry or brush plating, a metallization lyte. The toxicity of fluoride, and wet abrasion with red 3M Scotch- technique that uses a small volume the rapidity with which the oxide Brite, wire brushing and abrasive of solution contained in a fabric re-forms after removal, are issues blasting with aluminum oxide and matrix between the anode and with this method. silicon carbide. cathode in a plating cell. The Surface roughening can improve Chemicals used to formulate small volume of plating solution, coating adhesion, and can be pretreatment solutions and plat- coupled with the proximity of the accomplished by abrasion, grit ing baths were reagent grade anode and cathode, allows use of blasting and etching. Surface without further purification. We brush plating in applications that preparation is key to achieving used deionized water for solution would be impractical or impossible robust adhesion of any coating to makeup and rinsing, and first with other electroplating or coat- titanium. applied a nickel strike layer using ing methods. an acid nickel sulfate plating solu- BRUSH PLatING RESEARCH tion and a rectifier capable of being SURFACE PREPARatION SIFCO Applied Surface Concepts switched rapidly between cathodic Titanium is very reactive and has performed multiple experi- and anodic modes. rapidly forms an oxide film when- ments on titanium surface prepa- The anode was a noble metal- ever the metal surface is exposed ration and selective plating. We coated titanium mesh supported to air or any environment contain- obtained titanium sheets 1.1 mm by a polypropylene block. Holes ing available oxygen. This oxide thick and tubes 0.83 mm thick in drilled through the block allowed layer should be removed before three substrate materials: Ti-6Al-4V, solution to flow through the anode electroplating or other surface Ti-6Al-6V-2Sn and commercially structure onto the workpiece. The treatment, but its tenacity makes pure Grade 2 titanium. We used the anode-to-cathode gap, which was removal problematic. sheets and tubes in the as-received determined by the thickness of the A common method to remove condition and mechanically fin- fabric matrix between the anode oxide from titanium is exposure to ished the surfaces using several and cathode, was approximately Our experience selectively plat- ing a nickel deposit on titanium 60 µm Grade 2 is representative of the issues involved with obtaining adherent coatings on titanium. Acid Nickel The Grade 2 titanium surface was blasted with 180-grit silicon carbide Acid Copper and activated before plating. The test coupon survived tape and 350 µm bend tests, however, separation between the nickel deposit and the substrate observed in cross-section, considered to involve the titanium oxide film, makes adhesion sus- pect. Nickel brush plated over the 35 µm oxide film had poor adhesion in localized areas. We then tried mechanical meth- Nickel Strike/Plate ods to improve adhesion by increas- ing the substrate surface area and Ti 6-4 Base exposing a fresh, clean titanium surface. Mechanical working of the Cross section through a nickel strike/brush copper/brush nickel coating on surface by abrasion with grinding Ti-6Al-4V shows no delamination between layers. This type of coating is often media, wire brushes or by blasting used to repair surface defects. with silicon carbide or wet or dry alumina increased surface area, and deposit adhesion improved versus an unworked surface. Adhesion was 5 mm (0.2 in.). Fabrics evaluated then examining the interface still not high enough to routinely included red, brown and grey 3M between titanium and plating with survive the 180° bend test. Scotch-Brite, cotton, polyethylene an inverted metallurgical micro- terephthalate and gauze. scope. We used a stylus profilometer ACID EtCHING Adhesion of the plated metal to to measure roughness. Titanium undergoes active dis- the titanium substrate was tested One objective of the work was to solution in strong acids, and we according to AMS 2451A and develop a fluoride-free electrolyte used hydrochloric and sulfuric ASTM B 571. Adhesion was evalu- for surface preparation of titanium. acids to increase substrate surface ated using the chisel-knife, tape, Accordingly, we evaluated sulfuric, area and remove the oxide film. quench and bend tests. Titanium nitric, sulfuric/nitric mixtures, The substrate surface was matte sheets were bent 180° around a sulfamic, ammonium bifluoride after the acid etches. Hydrogen diameter equal to the thickness and phosphoric acid at various evolution during active dissolu- of the sheet in the bend test. concentrations. Visible oxide films tion in the acids indicated that Parts were quenched from 250°C formed during anodic treatment in the titanium surface was free of (480°F) into room-temperature some of the acid solutions which oxide. Low deposit adhesion was water, and the tape was pulled with could not be cathodically reduced. observed on the chemically-etched a quick motion at a 180° angle to Presence of the film coincided with titanium surfaces. the surface. A sharp cold chisel was poor deposit adhesion. We then undertook to identify an used to penetrate the coating. A electrochemical treatment method good result in each of these tests INITIAL RESULTS with the capability to increase the shows no separation of plating from Results showed that the titanium substrate surface area in a con- the basis metal. alloy, acid type and concentration trolled manner and provide an The tensile adhesion of a 50-µm and pretreatment conditions all oxide-free surface that enabled thick nickel coating on Ti-6Al-4V impacted adhesion of an electrode- good deposit adhesion. The result- was measured following ASTM C posited coating on titanium and ing electrochemical treatment 633 and using adhesive EC2086, alloy substrates. includes both an electrolyte and an anodic/cathodic etch/activate TABLE 1 Brush plating procedure for nickel coatings on Ti-6Al-4V methodology to promote micro- etching of the titanium surface to Operation Material Conditions increase surface area and reduce Abrade Scotch-Brite Wet with Etch/Activate Solution the surface oxide. Treatments anodically polarized Etch Etch/Activate 14 V anodic, 10 sec the titanium surface to microetch/ Activate Solution 4–8 V cathodic, 1 min roughen it. This was immediately followed by a cathodic treatment Strike Plate Acid Nickel 8–18 V cathodic, 0.078 A∙hr/cm2 in the same solution to reduce oxide, then introducing a nickel electrolytes can be switched from etch/activate process. A machined strike plating solution. Treatments activation to strike plating. surface requires little in the way were carried out under potential The plating procedure used to of mechanical work before etch/ control. We identified mixtures of make this deposit is given in Table activate. Deep scratches should be sodium chloride, nickel salts, and 1. Important considerations for this avoided during abrasion—they can hydrochloric and citric acids that process are to keep the titanium develop pits in the anodic etch. met the objectives of an etch/acti- under potential control at all times, Rinsing is not included between vate electrolyte. The nickel strike keep the plated area 100% covered the process steps in Table 1 because, and buildup were plated using the by the wrapped anode, use rapid when the titanium surface is Future research work should continue to develop principles for good adhesion of plated deposits to titanium alloys acid nickel sulfate brush plating TABLE 2 Average tensile adhesion of nickel deposits on Ti-6Al-4V solution. Nickel plated readily into the microroughness features. Surface Type of Acid Nickel Solution Adhesion, psi Adhesion was checked by tape Machined Sulfate 7,400 and bend tests, and the nickel deposit did not separate from the Blasted Sulfate 6,500 Ti-6Al-4V substrate. Thin panels of Blasted Sulfamate 6,600 Ti-6Al-4V and Ti-6Al-6V-2Sn broke in one 180° bend without separa- EC2086 epoxy 13,000 tion or peeling of the deposit. Grade 2 titanium can be bent a full 180° without breaking. The bend switching from anodic to cathodic, removed from the electrolyte, the test was more rigorous in revealing allow no rinsing between steps and oxide film readily forms in either low adhesion than the tape test. do not reuse the solution. air or water. This interferes with Several factors contribute to the Tests produced further under- adhesion between the deposit and excellent adhesion: mechanical standing of both the chemistry and the substrate. The solutions we used interlocking, increased surface mechanical processing needed in this work are compatible and a area and lack of an oxide film.
Details
-
File Typepdf
-
Upload Time-
-
Content LanguagesEnglish
-
Upload UserAnonymous/Not logged-in
-
File Pages6 Page
-
File Size-