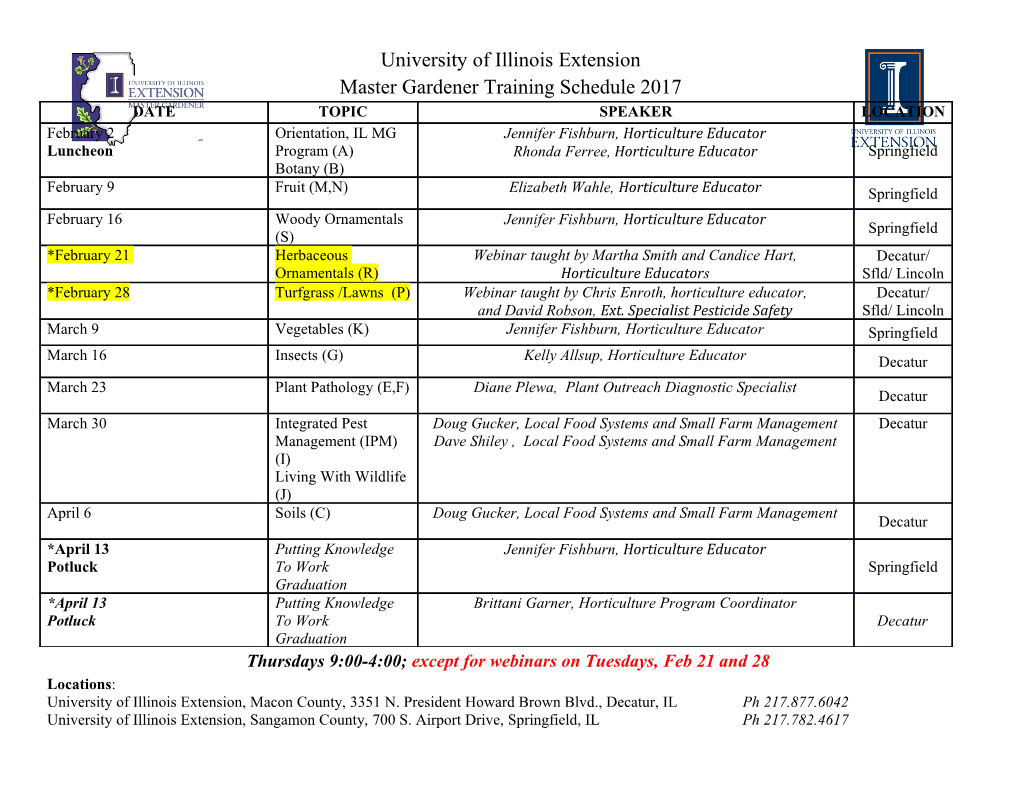
Thermophotovoltaic System Simulation with Realistic Experimental Considerations Evan Schlenker*, Zhiguang Zhou†, Peter Bermel† *Department of Electrical and Computer Engineering, Bucknell University, Lewisburg, PA 17837, USA †School of Electrical and Computer Engineering, Purdue University, West Lafayette, IN 47907, USA Abstract Thermophotovoltaic (TPV) systems are a promising type of energy generation method that convert heat into electricity via thermal radiation. TPV has potential to benefit the economy, the energy sector, and the environment by converting waste heat from other power generation methods into electricity. Simulations of these systems can play a key role in designing TPV systems and validating their experimental performance. Current simulation tools can model important aspects of TPV systems fairly accurately, but generally make certain simplifying assumptions that are challenging to reproduce in experiments. Developing a simulation tool that accurately captures thermal emission and reflection in complex, realistic geometries will facilitate understanding and further development of TPV systems. An existing tool developed at Purdue, known as TPVtest, has now been modified and streamlined to create a new tool, TPVexpt, to help achieve this goal. New features in TPVexpt include: (1) the input of shunt and series resistance of a PV cell and consideration of the associated losses when calculating power output; and (2) the input of arbitrary size and position rectangular heater, emitter, and PV diode for view factor calculations to accurately model radiative heat transfer. TPVexpt combines an accessible GUI with TPV analysis that accounts for thermal non-idealities and realistic geometries to produce more accurate power and efficiency predictions for TPV systems. Finally, TPVexpt has been partially validated against real-world TPV experiments up to 800 °C; additional work is needed here to verify the generality of this approach, and to aid current and future researchers in advancing TPV technology. Introduction Thermophotovoltaic (TPV) systems convert heat into electricity via thermal radiation [1-3]. They have potential to operate with high efficiency in compact areas, even below 1 square centimeter. Their solid state operation may also be valuable for long-term or remote commercial or industrial applications, due to low maintenance requirements. Analytical work has suggested that extremely high conversion efficiencies are possible with this technology. A great deal of modeling incorporating new technologies has been carried out to predict the limits of system performance under various constraints. However, in a real TPV system, structures are not as simple as two squares in proximity - thermal emission and reflection can occur from multiple regions in these devices. The pathways grow exponentially with the number of reflections, leading to highly complex calculations [4,5]. Nonetheless, considering these factors correctly can help further the progress to understand the detailed loss mechanism scientifically and to realize more efficient TPV systems in real-world applications. Thus, it is critical to develop a numerical model that considers the various interactions that can take place and calculate only the most important contributions, while estimating the residual error of the calculation. TPV cells are solid-state p-n junction semiconductor devices that absorb thermal radiation emitted by a heated element and convert said heat into electricity. Thermal energy supplied by various sources such as combustion, the sun, or waste heat is channeled to an emitter. An ideal emitter exhibits blackbody behavior, where the characteristics of the emitted radiation depend only on the temperature of the emitter. The emitter is typically operated in the temperature range of 1000-1573 K, producing primarily mid-infrared radiation. Because of Wien’s and Stefan- Boltzmann’s laws of thermal radiation, increasing the emitter temperature will result in higher energy photon production and potential for greater output power density. The emitted photons propagate towards the PV cell, which should be at a significantly lower temperature than the emitter (approximately 300 K), since the PV cell is most efficient at lower temperatures. Photons with energy higher than the PV cell bandgap (shorter wavelengths) are absorbed by the cell and converted to electricity via the photoelectric effect, while photons with lower energy than the bandgap (longer wavelength) are either not absorbed or converted to heat, which reduces PV operation efficiency and wastes incident energy. In order to achieve high efficiency operation it is necessary to design the TPV system so the majority of emitted photons have energies greater than the PV cell bandgap. Much PV research has been devoted to Si and GaAs semiconductors, which have too large of a bandgap for TPV applications dealing with relatively low energy incident photons, associated with operating temperatures of 1500 K or below. Lower bandgap semiconductors such as GaSb, InGaAs, and InGaAsSb are therefore more prevalent in TPV systems, due to their lower and thus more suitable bandgap energies [2]. Matching the properties of the thermal radiation with the PV cell is of great importance in maximizing TPV system efficiency. Selective emitters, filters, and photon recycling can all function to increase TPV efficiency, potentially by orders of magnitude. Selective emitters attached to the radiator allow for spectral shaping, essentially suppressing emission of below bandgap photons and enhancing emission of above gap photons [3]. This can be achieved by implementation of photonic crystals (PhCs). PhCs come in a wide variety of types (1D, 2D, 3D) and materials (semiconductors, rare earth metals). Simulation has shown that using PhCs made from refractory metals (which are ideal for TPV use since they can withstand high temperatures) can significantly improve TPV efficiency when used as a selective emitter [6]. PhCs can also be utilized as a front-side filter deposited on the front of the PV diode that allow energies above the bandgap to pass through to the PV diode and reflect photons with energies below the bandgap [7]. This reflection of low energy photons back to the emitter for reabsorption is known as photon recycling. Spectral utilization in photon recycling may be quantified with filter efficiency, defined as the ratio of above bandgap optical power received by the PV cell to the total amount of optical power absorbed by both the PV cell and the filter [8]. Fabricating materials and testing all combinations of PhC materials, PV materials, filters, and photon recycling methods is tedious and time consuming. Accurate simulations of TPV systems can dramatically accelerate the discovery of higher-performance designs. GaSb has been extensively tested to yield the temperature dependent material parameters that can be used for accurate TPV simulation, including carrier concentration and mobility and absorption coefficient [9]. A program called TPVtest that uses a finite difference time-domain (FDTD) simulation developed by MIT known as MEEP can be used to consider the performance of different emitter materials and properties of TPV systems [6]. TPVtest does not consider thermal emission and reflection in its analysis. TPVtest incorporates a compact model based on SURF Final Report 2 Evan Schlenker experiment, but cannot predict the effects of new PV cell architectures. Instead, this can be understood using other simulation tools, such as PC1D, ADEPT, or AMPS. They have previously been used to analyze the effects of Auger recombination (results when excess energy from absorbed photons is given to another carrier and causes thermal vibration loss) and to predict the effects of PV series resistances over a range of temperatures [10]. While the above simulations and models are useful and fairly accurate, there are a number of factors that can cause the simulated/predicted TPV system behavior to differ from experimental results. For example, surface diffusion in a nanostructured selective emitter causes reshaping of features with high curvature, which shifts resonance peaks towards lower wavelengths and eventually decreases their spectral emissivity [11]. Thermal emission and reflection is another source of loss and non-ideal behavior. Geometric and thermodynamic concepts and theory can be used to analyze radiative heat exchange between surfaces with specular reflection [4]. Implementing thermal analysis into a new simulation tool will allow for more accurate TPV simulation. Developing a tool to accurately model thermophotovoltaic performance in complex and realistic geometries could play an important role in progressing the scientific understanding of the loss mechanisms present in real experiments, and to help optimize existing system designs for improved performance. Methodology TPVtest is a TPV system simulation tool created in 2013 [12]. The tool employs MEEP, which is a Finite Difference Time Domain (FDTD) method that simulates electromagnetic wave propagation [13]. It also implements the Stanford Stratified Structure Solver (S4), a frequency domain code to solve the linear Maxwell’s equations in layered periodic structures [14]. TPVtest simulations require the view factor from the PV cell to the emitter as a user defined input. This can be very difficult to calculate. It also assumes that the PV cell and emitter are both equivalently sized squares, which is often not the case in a TPV system. The heater
Details
-
File Typepdf
-
Upload Time-
-
Content LanguagesEnglish
-
Upload UserAnonymous/Not logged-in
-
File Pages13 Page
-
File Size-