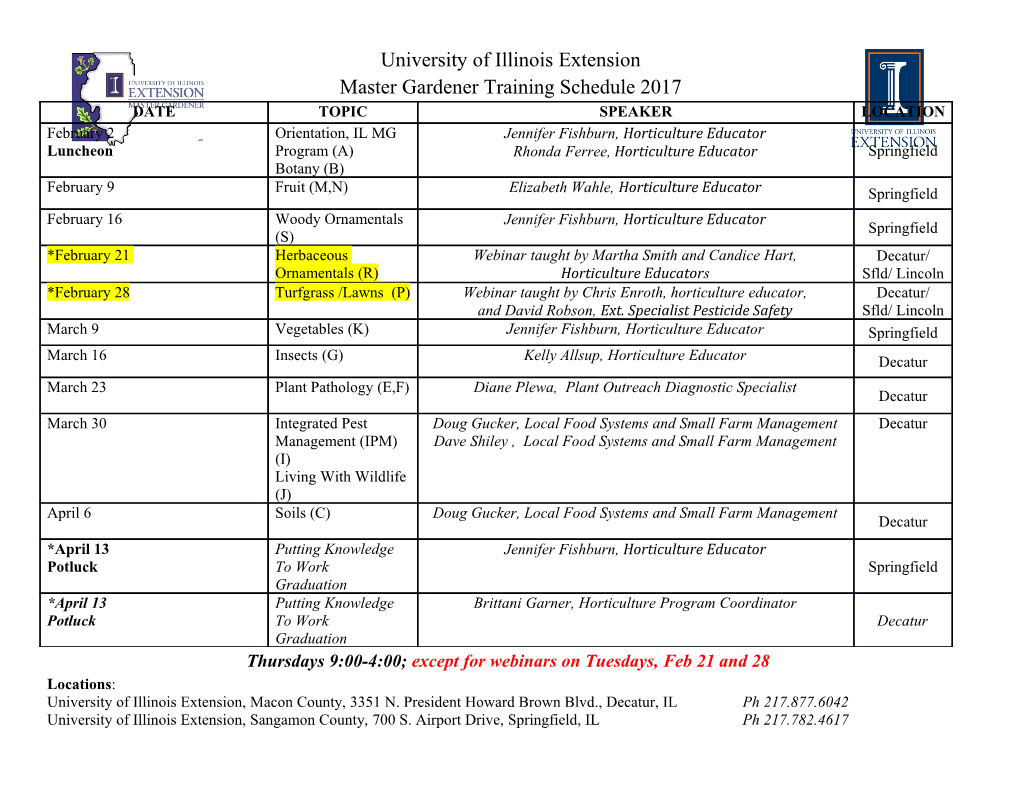
ZEBRAFISH Volume 16, Number 3, 2019 ª Mary Ann Liebert, Inc. DOI: 10.1089/zeb.2017.1520 Three-Dimensional Printing of Vitrification Loop Prototypes for Aquatic Species Nolan J. Tiersch,1 William M. Childress,2 and Terrence R. Tiersch2 Abstract Vitrification is a method of cryopreservation that freezes samples rapidly, while forming an amorphous solid (‘‘glass’’), typically in small (lL) volumes. The goal of this project was to create, by three-dimensional (3D) printing, open vitrification devices based on an elliptical loop that could be efficiently used and stored. Vitrification efforts can benefit from the application of 3D printing, and to begin integration of this technology, we addressed four main variables: thermoplastic filament type, loop length, loop height, and method of loading. Our objectives were to: (1) design vitrification loops with varied dimensions; (2) print prototype loops for testing; (3) evaluate loading methods for the devices; and (4) classify vitrification responses to multiple device configurations. The various configurations were designed digitally using 3D CAD (Computer Aided Design) software, and prototype devices were produced with MakerBotÒ 3D printers. The thermoplastic filaments used to produce devices were acrylonitrile butadiene styrene (ABS) and polylactic acid (PLA). Vitrification devices were characterized by the film volumes formed with different methods of loading (pipetting or submersion). Frozen films were classified to determine vitrification quality: zero (opaque, or abundant crystalline ice formation); one (translucent, or partial vitrification), or two (transparent, or substantial vitrification, glass). A published vitrification solution was used to conduct experiments. Loading by pipetting formed frozen films more reliably than by submersion, but submersion yielded fewer filling problems and was more rapid. The loop designs that yielded the highest levels of vitrification enabled rapid transfer of heat, and most often were characterized as being longer and consisting of fewer layers (height). 3D printing can assist standardization of vitrification methods and research, yet can also provide the ability to quickly design and fabricate custom devices when needed. Keywords: 3D printing, vitrification, aquatic species Introduction its simplicity, vitrification can be performed in remote loca- tions with minimal instrumentation requirements.1 nnovation followed by customization and standardi- The ability to work in diverse settings, including fieldwork, Ization is necessary for aquatic species to advance in in- is crucial to efforts for conservation of endangered species, ternationally practiced fields such as cryopreservation. and vitrification offers an effective way to freeze and store Conventional cryopreservation relies on a relatively slow samples for laboratory use with aquatic biomedical models. Downloaded by University of Alabama at Birmingham: Lister Hill Library from www.liebertpub.com 11/15/19. For personal use only. formation of crystalline ice (‘‘equilibrium freezing’’), while Despite this, vitrification is underutilized in aquatic species vitrification rapidly releases heat to form an amorphous solid due to the dearth of suitable devices. Available devices often (glass).1 Vitrification typically exposes samples to liquid ni- lack essential features such as appropriate sizing, ease of trogen, providing a rapid and efficient method of cryo- handling, and affordability for new applications such as preservation. Sample integrity is preserved against cryogenic freezing of fish gametes or embryos.3 The lack of suitable temperatures by the addition of concentrated vitrification so- vitrification devices has constrained research to being per- lutions, in balance with their potential toxicity to cells or tis- formed with devices made for other purposes, such as inoc- sues.2 Desirable chemicals for use in vitrification solutions ulation loops used in microbiology4 or plastic strips used for possess properties promoting glass formation, and because of human embryos.5 Three-dimensional (3D) printing may be a 1St. Michael the Archangel High School, Baton Rouge, Louisiana. 2Aquatic Germplasm and Genetic Resources Center, School of Renewable Natural Resources, Louisiana State University Agricultural Center, Baton Rouge, Louisiana. 252 3D PRINTED VITRIFICATION DEVICES 253 FIG. 1. Examples of schematic diagrams used to design 3D printed vitrification loop prototypes. Widths of all loops were the same, but the length of the loops (at the end of the handles) varied between 23.5 mm (Long; top) and 15 mm (Short; bottom). 3D, three dimensional. practical method to address the lack of viable vitrification Initially, a wide variety of early prototype test devices devices, by fabrication of devices specifically designed for were digitally designed with various loop dimensions by use vitrification in aquatic species. of commercially available 3D CAD software (Autodesk In- 3D printing technology is just beginning to be applied to ventorÒ professional 2016—student edition, San Rafael, cryopreservation,6 and as such the experiments in this study CA). The basic design was an elliptical loop at the end of a addressed essential nonbiological aspects of materials, design, handle. Eventually, a series based on a total of 18 different fabrication, and testing of prototype configurations (loops), loop configurations was selected for further study, with a total and did not involve gametes. A published vitrification solution length of each device (handle and loop) set at 132.5 mm. The was used to examine the feasibility of using 3D printed loops loops were designed as ellipses with a width of 2 mm (outer to produce vitrification. Acrylonitrile butadiene styrene (ABS) dimension). Loop configurations comprised three nominal and polylactic acid (PLA)7 are the most common thermo- lengths (short, 15 mm; intermediate, 19 mm; and long, plastic filament materials, and most 3D printers currently 23.5 mm) (Fig. 2), and six nominal heights (0.2, 0.4, 0.6, 0.8, available are compatible with them. They can withstand the 1, and 1.2 mm) produced by printing of 1–6 layers (0.15– extreme temperature changes associated with liquid nitrogen 0.2 mm/layer). exposure, and thus were the logical choices for this work. For extrusion, the thermoplastic filament is guided into the Printing of prototype loops for testing 3D printer head and heated to a molten state. The mobile printer head ejects the molten filament onto a build platform at The types of thermoplastic filament materials used to produce a controlled rate. The filament is stacked in thin layers and the prototype loops were ABS and PLA (Makerbot Industries, hardens to produce designs exported from 3D CAD (Computer Brooklyn, NY) and are available at a cost of about $20–48 per Aided Design) software. Engineering of devices for specified kg. The spools of filament (1.75 mm diameter) were stored in a applications requires tradeoffs, a system of balancing un- 63-L plastic bin with a latched lid (Hefty, 7105HFT-10-111-44, Macedon, NY) with desiccant (DampRid, FG01K, Mem- wanted with desired qualities. We chose to evaluate 3D printed Ò devices that were constrained in size to fit within the dimen- phis, TN) to minimize humidity. Two MakerBot 3D printers sions of a standard cryopreservation container, the 0.5-mL French straw (IMV Technologies, Paris, France). Thus, this work was focused on design, fabrication, and feasibility testing of 3D printed loops for the first time for vitrification. Given that the goal of this project was to create custom 3D printed open vitrification devices that could be efficiently used and stored, our objectives were to (1) design prototype vitrifi- cation loops with varied dimensions; (2) print prototype loops for testing; (3) evaluate loading method for the devices; and (4) classify vitrification responses to multiple device configura- tions. Relatively long and thin loops proved to be most effective to produce glass when using vitrification solution in volumes of 1to19lL. The prototype loops and methods used in this study offer a path to standardization for cryopreservation of aquatic Downloaded by University of Alabama at Birmingham: Lister Hill Library from www.liebertpub.com 11/15/19. For personal use only. species by utilizing the increasingly widespread availability and reproducibility of 3D printing. Materials and Methods Design of prototype vitrification loops with varied dimensions Our design criteria were to create (1) devices with di- FIG. 2. The loop configurations consisted of one to six layers (nominal 0.2 mm/layer) and three loop lengths mensions that fit within those of a 0.5-mL French straw; (2) (short—15 mm, intermediate—19 mm, and long— varied loop dimensions to hold a range of film volumes; and 23.5 mm). Top view: short, intermediate, and long loops (3) triangular handles to facilitate processing and storage. (ABS). Side view: long loops printed with 6, 3, or 1 layer. A Although these prototype devices were of the same total reference line was used to assist visualization of the side lengths, handle lengths were varied to allow for differences in view of the single-layer loop (bottom). ABS, acrylonitrile loop length (Fig. 1). butadiene styrene. 254 TIERSCH, CHILDRESS, AND TIERSCH (Replicator 2—PLA filament printer, and Replicator 2X— balanced salt solution at an osmolality of 300 mOsmol/kg was ABS filament printer, New York, NY) were used to produce a used as a diluent (HBSS300: 0.137 M NaCl, 5.4 mM KCl, total of 72 prototype loops, by printing two replicates of each 1.3 mM CaCl2,1.0mMMgSO4,0.25mMNa2HPO4,0.44mM configuration (3 lengths · 6 heights · 2 thermoplastics). The KH2PO4, 4.2 mM NaHCO3, and 5.55 mM glucose, pH 7.2). All print time for each device was roughly 3 min, as loop con- solutions were stored at 4°C between testing, and were thor- figurations slightly affected print times (1–2 s/layer). The rate oughly mixed before each use. of failure to print two replicates of each device was calcu- Classifications of vitrification quality were assigned to lated by dividing the number of failed prints by the total frozen films formed with vitrification solution by each number of prints [No. of failed prints(x)/total number of loading method.
Details
-
File Typepdf
-
Upload Time-
-
Content LanguagesEnglish
-
Upload UserAnonymous/Not logged-in
-
File Pages10 Page
-
File Size-