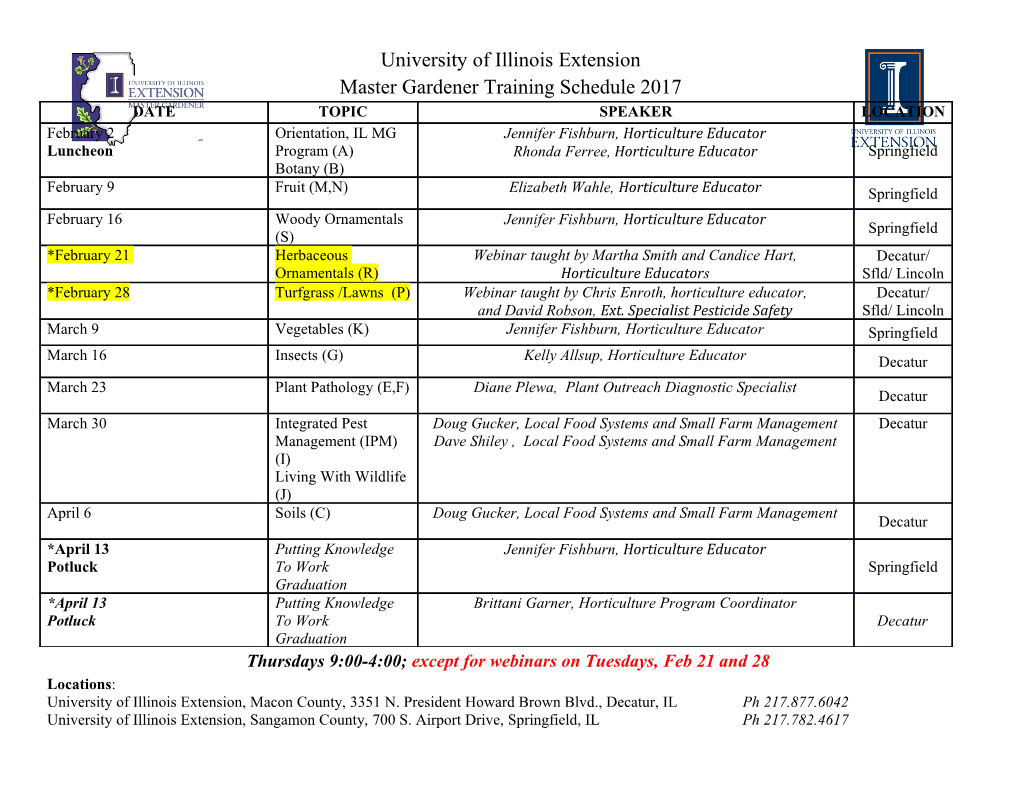
|||||||||||||||| US005258.687A United States Patent (19) 11 Patent Number: 5,258,687 Duggan et al. (45. Date of Patent: Nov. 2, 1993 54 MERCURY WAPOR DISCHARGE DEVICE (56) References Cited 75 Inventors: George L. Duggan, Bedford; David A. U.S. PATENT DOCUMENTS Goodman, Amesbury; Nanu Brates, 3,170,081 2/1965 Rokosz ................................ 313/631 Malden, all of Mass. 4,044,276 8/1977 Keeffe et al. ... ... 33/346R 0. 4,210,840 7/1980 Bhalla .................................. 313/328 (73) Assignee: GTE Products Corporation, Danvers, 4,783,611 11/1988 Vogels et al......... ... 33/628 X Mass. 5, 11,108 5/1992 Goodman et al. .............. 313/628 X * Notice: The portion of the term of this patent Primary Examiner-Sandra L. O'Shea subsequent to May 5, 2009 has been Assistant Examineral-Ashok Patel disclaimed. Attorney, Agent, or Firm-Robert E. Walter; William H. McNeil (21) Appl. No.: 714,795 22 Feded: Jun,un. -3,13, 1991 In57 a mercury vapor arcABS discharge CT tube having a pair of 51) Int. Cli................................................ H01J 1/16 electrodes, an emissive material disposed on the elec 52 U.S. C. ........................ 313/346 R; 313/346 DC; trodes consists essentially of a single phase compound of 313/344; 313/628; 313/630,313/631; 313/639 BaxSri-Y2O4 where x is from about 0.25 to about 0.95. 58) Field of Search ............ 313/346R, 346 DC, 571, 313/628, 631, 638, 310,344, 350, 335, 630, 639 3 Claims, 1 Drawing Sheet U.S. Patent Nov. 2, 1993 5,258,687 2 7 - A 5,258,687 1. 2 MERCURY WAPOR DSCHARGE DEVICE BRIEF DESCRIPTION OF THE DRAWINGS FIG. 1 is an elevational view of a high pressure mer CROSS REFERENCE TO RELATED cury vapor arc discharge tube in accordance with this APPLICATIONS invention. FIG. 2 is an expanded sectional view of an electrode U.S application entitled Vapor Discharge Device, configuration containing the emission material. filed Dec. 14, 1990, as Ser. No. 07/627,529, now U.S. Pat. No. 5,111,108, relates to an emissive material of DESCRIPTION OF THE PREFERRED barium/strontium/yttrium oxide on an electrode. O EMBODIMENT As shown in FIG. 1, the high pressure mercury vapor FIELD OF THE INVENTION arc tube 1 is made of high silica glass, for example, The present invention relates to an emissive material quartz, includes press seals 2 at each end. An electrode for use in a mercury vapor discharge lamp. 3 at each end of the arc tube 1 is connected to a molyb 15 denum ribbon or foil 4 which is connected, in turn, to DESCRIPTION OF THE PRIOR ART external lead-in-wire 5. The arc tube 1 includes a start ing electrode 6. The ribbon 4 is utilized to obtain a glass High intensity discharge mercury vapor lamps have a to metal seal. In the preparation of the arc tube 1, typi quartz arc tube containing mercury as the light emitting cally, the ribbon 4 and electrode 6 components are member. The mercury vapor lamp arc tube uses only 20 welded together and the resulting structure is inserted mercury as the fill component except for a starting gas, into the end of the silica tube 1 which is heated to about typically argon. The resulting lamp discharge yields the 2050 C. and pinched onto the ribbon 4. After pinch well known mercury high pressure line spectrum with sealing, the arc tube is exhausted of air and filled with infrared, visible and ultraviolet radiation. Such lamps argon, and, depending on wattage, an accurate dose of typically have tungsten electrodes with an emissive 25 mercury. material disposed on each electrode. U.S. Pat. No. The lamp lumen maintenance, starting, and life are all 4,044,276 to Keeffe et al. describes an emission mix for dependent to some extent on the quality of the main high pressure mercury lamps comprising barium oxide, electrodes 3. As illustrated in FIG. 2, the electrode calcium oxide and hafnium oxide. A mixture of barium comprises a tungsten rod 7 having an inner tungsten coil 30 8 encircling a portion of rod 7 and secured thereto. carbonate, calcium carbonate, and hafnium dioxide is Outer tungsten coil 9 is threaded on coil 8. In the pre coated on the electrode. The resulting emissive oxide ferred embodiment, the coil is formed of a screw mixture is formed after firing in hydrogen at 1500 C. to wrapped base section of tungsten wire with an over decompose the carbonates. The resulting emissive oxide screw section which is backwound over the base sec deteriorates when exposed to ambient atmosphere by 35 tion. The rod 7 is disposed on the axis of the windings. trapping water vapor. As a result, unless the fired elec The emitting or emissive material 10 is disposed in the trodes are immediately processed into sealed arc tubes, voids or recesses between coils 8 and 9. Coil 8 may have their effectiveness will diminish rapidly with time. It is some open turns, as shown in FIG. 2, to accommodate believed that both barium and calcium oxides, which more emitting material 10. are known to react vigorously and exothermally with The emissive material disposed on each electrode water vapor, contributes to the instability of the emis consist essentially of a single phase reaction product and sive mixture by forming hydroxides. Additionally, ex compound having a formula Bay.Sri-Y2O4 wherein x posure of barium oxide in air to carbon dioxide may is from about 0.05 to about 0.95. More preferably x is result in the reformation of barium carbonate so as to from about 0.5 to about 0.75. Although these latter 45 compositions having a higher barium concentration are add to the instability of the mixture. Due to the instabil more reactive with moisture, they are preferred since ity of the emissive mixture, difficulties in achieving the higher barium concentration results in a more emis manufacturing uniformity and consistent lamp perfor sive electrode. The higher barium content, the greater mance may be encountered. the mass loss rate. Desirably, mass loss rate of the emit 50 ter is sufficient to maintain a supply of electroactive SUMMARY OF THE INVENTION alkaline earth metal species to the cathode emitting It is an object of the present invention, to provide an surface over the life of the lamp, but sufficiently low so emissive material that has enhanced stability in air. as to be present on the electrode for the life of the lamp. It is a further object of the invention to achieve en If the amount of the emitter is undesirably low, the lamp hanced consistency in the operation of mercury lamps 55 suffers from poor lumen maintenance due to tungsten manufactured from electrodes coated with the emissive evaporation caused by overheating of the electrodes as electrode emission declines. material of the present invention. Preferably, the molar ratio of (Ba--Sr)Y is less than In accordance with the present invention, there is about 0.5, and more preferably about 0.5 to about 0.3. provided a high pressure mercury vapor arc discharge At ratios above 0.5, alkaline earth oxide rich phases tube comprising a pair of electrodes sealed through such as BaO, SrO, or BasY4O9 may be formed. Such opposite ends thereof, a fill within said tube consisting phases are very reactive with moisture in the air and are essentially of mercury and a starting gas, and means to desirably avoided. At ratios less than about 0.5, an ex connect current to each electrode of said pair of elec cess of Y2O3 is present in the reaction mixture to assure trodes, and an emissive material disposed on said pair of 65 complete reaction of the barium and strontium com electrodes consisting essentially of a single phase com pounds to avoid the formation of the simple oxides of pound of BaSr1-Y2O4 whereinx is from about 0.05 to barium and strontium. The final reacted emissive mate about 0.95. rial desirably contains excess yttria. Typically, yttria is 5,258,687 3 4. present in amounts less than about 10 molar percent. mix is then placed in an alumina crucible. The crucible Preferably, the quantities of barium carbonate, stron is placed into a furnace and heated for 6 hours to about tium carbonate and yttrium oxide are reacted to pro 1500 C. After 23 hours of heating at 1500 C., the fur duce an emitter composition, having about 2 to about 6 nace is cooled over a 6-hour period of time and the molar percent Y2O3 in the reacted mixture of the emit 5 crucible removed. The resulting material was identified ter material. by x-ray diffraction analysis to be almost entirely the It is contemplated that the emissive material may single phase compound having the above formulation, incorporate minor amounts, preferably less than about BaSr1-Y2O4, wherein is 0.50 with a about 4% of twenty five percent, and more preferably less than yttrium oxide being present. The material was mixed about five per cent by weight of additional ingredients O with zirconia grinding media as previously set forth in which do not deleterious affect the performance of the methanol and roller milled at 60 rpm for about 6 hours. emissive material. Such additional ingredients, in addi The resulting slurry was separated from the milling tion to yttria, may also include other rare earth oxides, media with the milling media being rinsed in methanol. hafnium oxide, zirconium oxide, and other oxides such The average particle size of the reacted emissive mate as aluminum oxide, calcium oxide, and mixtures thereof.
Details
-
File Typepdf
-
Upload Time-
-
Content LanguagesEnglish
-
Upload UserAnonymous/Not logged-in
-
File Pages4 Page
-
File Size-