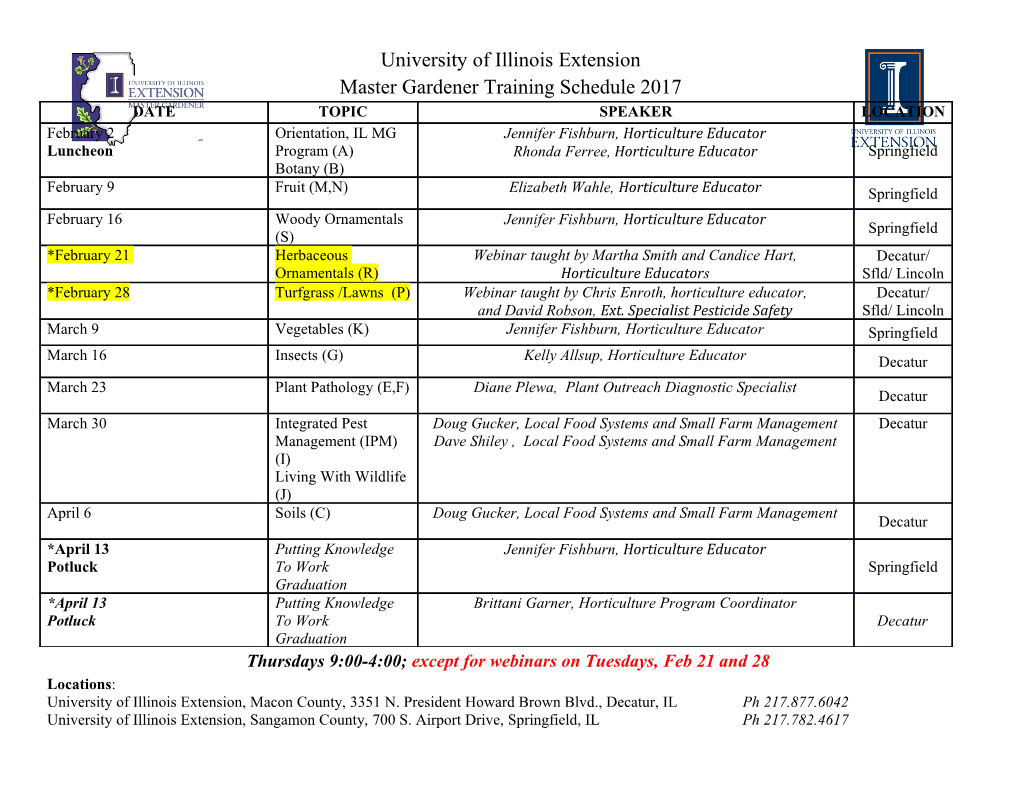
2,347,299 lice Patented Aug. 12, 1958 2 of zero. This gradual reduction preferably takes place over a relatively long period of time, on the order of 2,847,299 at least one hour and preferably longer. The reducing agent is also preferably fed uniformly to the surface of PRODUCTION or METALS the fused salt during a major portion of the long reduc Wayne H. Keller, Wahan, and Irwin S. Zonis, Belmont, tion period. Mass.,_assignors to National Research Corporation, We have discovered that in such a system crystal growth Cambridge, Mass, a corporation of Massachusetts is strongly promoted if the reducing agent be supplied to No Drawing. Application April 28, 1955 the thorium halide fused salt solution via an interposed Serial No. 504,677 10 shielding layer of fused salt which is substantially free of the thorium halide and which is preferably localized 6 Claims. (Cl. 75—84.1) by a diaphragm in direct contact with the solution. In one preferred embodiment of the invention, the shielding layer of fused salt is maintained as a distinct layer by This invention relates to the production of metals and 15 means of a diaphragm which permits only very limited more particularly to the production of thorium. This circulation between the upper (thorium-free) layer and application is in part a continuation of our copending the lower (thorium-containing) layer. This diaphragm applications Serial No. 373,512, ?led August 11, 1953, may be, for example, a nickel disc of a diameter almost and Serial No. 434,648, ?led June 4, 1954. as large as the reactor diameter. In another embodiment A principal object of the present invention is to pro of the invention, the diaphragm is formed in situ and vide an improved process for producing high yields of comprises a porous thorium crust. In this case, a solu thorium by the reduction of a thorium compound dis tion of thorium tetrachloride in fused sodium chloride is solved in a fused salt. ' provided in a reactor, and liquid sodium is fed to the Another object of the invention is to provide a process surface of the molten salt solution as a thin ?lm dis of the above type which is simple and cheap to operate 25 tributed substantially uniformly over the surface while and which gives a product which can be water leached the fused salt solution remains quiescent. Under these to separate the thorium from the by-product salt. conditions, a crust of sintered, ?ne thorium particles forms Still another object of the invention is to provide an ’ rapidly at the surface of the salt bath, extending over improved process of the above type which is equally said surface and adheringto the walls of the reactor and applicable to the production of alloys of thorium. to any other apparatus elements in and adjacent the Other objects of the invention will in part be obvious - surface of the bath. This crust is porous and incorporates and will in part appear hereinafter. a layer of fused salt which is substantially free of The invention accordingly comprises the process ‘in thorium chloride, at least adjacent and above the top of volving the several steps and the relation and the order the crust. of one or more of such steps with respect to each of 35 As the process continues, the level of the salt bath the others which are exempli?ed in the following .de will rise due to the manufacture of more by-product salt, tailed disclosure, and the scope of the application of but the crust remains Where it was formed, adhered to the which will be indicated in the claims. walls of the reactor, and the thorium crust becomes For a fuller understanding of the nature and objects covered by a layer of molten salt which (due to Strati?ca of the invention, reference should be had to the follow 40 tion and diffusion limitations placed on the contents of ing detailed description. thebath due to the presence of the crust) is substantially In the present invention, advantage is taken of the well free of thorium chloride. Consequently, further feed known ability of certain metals such as the alkali metals of sodium is to the surface of this thorium-chloride-free and alkaline earth metals to reduce compounds of layer of salt above the thorium crust. thorium. For simplicity of illustration, the-invention will 45 When the crust and shielding layer of thorium-halide be particularly described in connection with the forma free salt have been established, thorium crystals begin to tion of thorium by the reduction of a thorium halide dis form, growing out of the under surface of the crust and solved in a fused salt. Equally, the reducing agent will outwardly from the walls of the reactor. The produc be described as a preferred alkali metal and more par tion of thorium ?nes, such as initially form the crust, ticularly as sodium. The reduction reaction between 50 decreases substantially. sodium and thorium tetrachloride proceeds rapidly and The feed of sodium is preferably continued until suf at relatively low temperatures (i. e., temperatures on the ?cient sodium has been fed to reduce substantially all of order of the melting point of the by-product halide). the dissolved thorium chloride to thorium metal. It is However, in the present invention, the reaction condi also preferred that the thorium chloride solution be rel tions are so adjusted that the product thorium consists 55 atively concentrated at the start of the reduction so as of crystals of thorium which have a size su?iciently large to assist in forming a self-supporting, porous initial crust. _ so as to permit simple leaching with water (containing After the crust and thorium-chloride-free salt layer have a small percentage of acid) to dissolve the by-product been formed, the feed rate ‘of sodium to the reactor can halide. The size of the individual crystals is such that be ‘considerably increased, if desired. However, from the surface-to-volume ratio is relatively low, thereby pre 60 the standpoint of mechanical simplicity and safety, a venting contamination of the product due to the presence constant, relatively slow rate of feed of sodium is pre of surface oxide. The nature of the product is also such ferred. that its surface activity appears to be very low. After the sodium feed is stopped, the reactor is allowed In accordance with the present invention, a thorium to cool and the solidi?ed contents are leached by means compound, preferably a halide thereof, is dissolved in of acidi?ed water, thus removing the salt. The remain a fused salt. The dissolved halide of thorium is then ing product consists essentially of a mass of loosely ad~ reduced slowly and progressively to thorium metal by herent, interlaced crystals of thorium extending down addition of a reducing agent such as sodium, potassium, wardly from the crust layer of sintered thorium particles magnesium and the like. The thorium halide content and outwardly from the reactor Walls. of the fused salt is thus gradually reduced from an aver It will be evident from the foregoing that the diaphragm age thorium valence of four (when the starting material (which, inv the second example just, de_scribed,_is formed is thorium tetrachloride) to an average thorium valence Df sintered thorium ?nes) performs two major functions. 2,847,299 3 4 First, it helps to segregate the fused layer low in thorium the sodium substantially uniformly across the surface chloride. Second, it forms a supporting stratum from of the fused salt charge in the reactor. The reactor is which the thorium crystals, may grow. purged of air and charged with 25 pounds of sodium In order to describe more fully preferred methods of chloride and 80 pounds of thorium tetrachloride. This is practicing the invention, there are set forth below several heated to 900° C. and sodium is gradually sprayed non-limiting examples which are merely illustrative of across the surface of the molten salt at the rate of ap numerous other methods of practicing the invention: proximately 2 pounds per hour for 91/2 hours. The feed of sodium is then stopped and the reactor is maintained Example I at a temperature of about 900° C. for about 3 hours. 44.0 grams of a solution of thorium tetrachloride in The charge is then cooled and the product is leached sodium chloride (having the composition NaZThCIS) is in 2% nitric acid solution to recover a crop of relatively placed in the bottom of a 12 inch by 13/8 inch I. D. large thorium crystals. ' stainless steel tube which is closed at one end. A 1.14 While several speci?c examples have been given above, inch diameter nickel disc is supported on top of the numerous alternative methods may be employed without sodium chloride-thorium tetrachloride mixture. 2 inches 15 departing from the spirit of the invention. The tem of molten sodium chloride is poured into the stainless perature of the reaction mass may be varied widely from steel cylinder above the disc. This sodium chloride slightly above the melting point of the salt to tempera amounted to 83.9 grams. A sodium feeding crucible tures on the order of 1000° C. and above. Numerous is mounted about 11/2 inches above the fused salt barrier reducing agents other than the sodium may be employed. layer. This crucible has a hole at the bottom which is For example, potassium, calcium, magnesium, lithium and ?lled with a fused salt plug (13 grams of sodium chloride) various combinations of these elements may be utilized.
Details
-
File Typepdf
-
Upload Time-
-
Content LanguagesEnglish
-
Upload UserAnonymous/Not logged-in
-
File Pages3 Page
-
File Size-