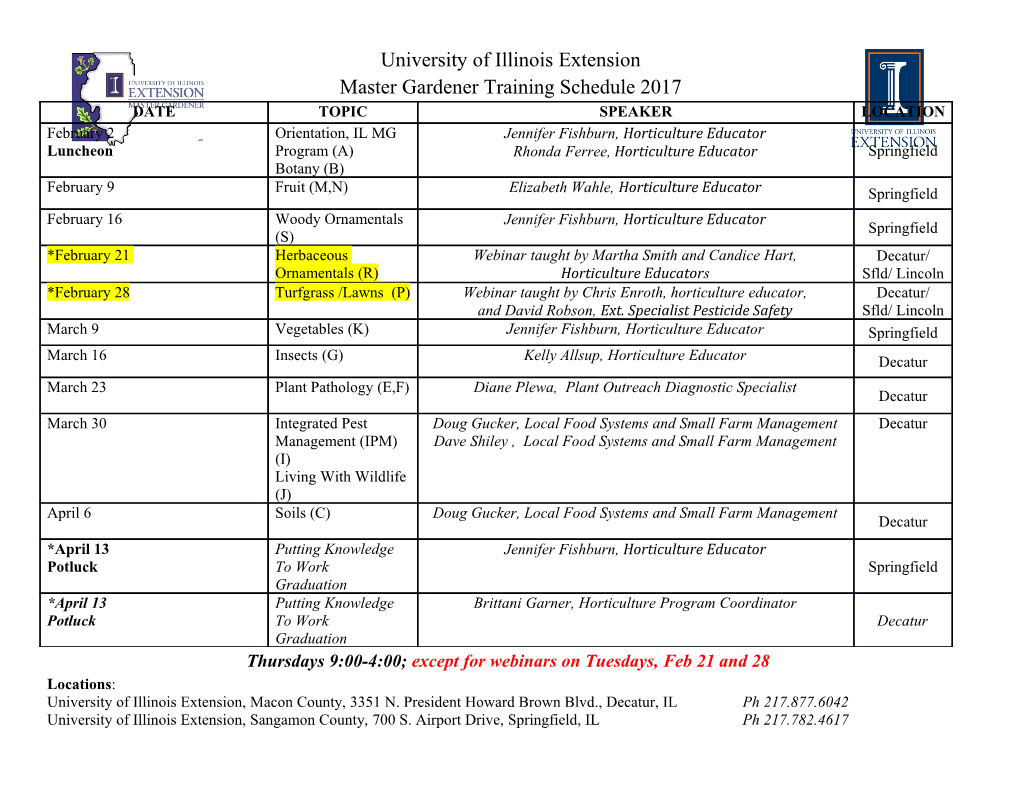
ADVANCED COMPOSITE ENGINEERING & MANUFACTURE LIGHTER | FASTER | STRONGER LIGHTER | FASTER | STRONGER ABOUT US MD, Simon J. Farren Established in 2000 in Colchester, Essex by former Lotus engineer Simon Farren, Reverie started by designing and producing niche track day and aftermarket Carbon Fibre performance parts, primarily for Lotus models. Growing quickly, in 2001 Reverie started offering composite engineering and manufacturing services to small car manufacturers. Caterham Cars commissioned Reverie to design and manufacture a complete induction silencer system for their R500 with K-Series engine. Between 2003 and 2005, Reverie was proudly involved in winning a large motorsport composite project for Foggy PETRONAS Racing, involving the manufacture of 150 full panel sets for the FP1 homologation special motorbike. All delivery times and quality targets were met for both the OEM manufacturing company and the FP1 race team. More recently, after gaining ISO9001:2015 certification, Reverie was tier 1 selected to manufacture Carbon Fibre OEM key fobs for McLaren (MP4/12 P1) to very high clear coated paint specifications. This large contract involved manufacturing over 24,000 units. WHY CHOOSE REVERIE? An established market leader with passionate, professional and highly skilled staff who offer expertise in a variety of fields including design & manufacture, automotive, motorsport, telecoms, marine, military, leisure and other composite products. Reverie will work with you to achieve world leading products that we are all proud of. Reverie supply LMP1/WRC Motorsport, not F1, which means we are not seasonal and will therefore not increase or inflate our prices or interrupt your supply. WHY THE AUTOCLAVED PROCESS? We predominantly use pre-impregnated epoxy thermoset composite materials to ensure that high fibre contents can be achieved consistently. We also vacuum bag and autoclave nearly all components to further ensure low void contents and trapped volatiles to maximise interlaminar shear properties by forcing the various layers in the fibre/resin matrix together. This process results in high quality lightweight parts achievable time and time again, with low void content and surface pin-holing. CLIENTS PAST & PRESENT WE HAVE WORKED WITH » OUR PROCESS » CUSTOMER REQUIREMENTS We split our manufacturing process Information is key and at the start of any project we will take you, the client, into key steps: through the necessary processes step by step and openly discuss your project with you including operating conditions, quality requirements, tolerances and appropriate specifications. Customer Requirements Initially, we need to establish where the project is at (whether it is just an idea which needs to be designed and developed, or a fully developed part ready Feasibility & Research for manufacture). At this stage, we ask for 3D CAD models (IGES/STEP), 2D DWG/PDF, any physical models, forecasted production volumes and all relevant Process Control documents in order for us to provide an accurate quote and advise on the best manufacturing route forwards. Design/Development For physical models, we can use our FARO arm or 3D scanner to digitize models into CAD software that accurately captures the original form and allows us to Material Selection study the part for manufacturing and tooling feasibility. Prototyping/Tooling » FEASIBILITY & RESEARCH Cutting/Laminating Depending on the complexity of the project or part, additional feasibility and research studies may need to be undertaken in order to ensure successful Curing/Finishing/Paint production and repeatability including FMEA stress analysis, CFD, researching new materials and processes or ways of tooling as needed. Assembly » PROCESS CONTROL Inspection All new project components have parent/child part numbers, routings, resources, labour skill types/levels, BOMs assigned and CAD files attached. This ensures Delivery full traceability and production capacity planning can be carried out using data capturing MRP/ERP software. We have dedicated process control flow charts, works instructions and procedures all meeting ISO9001:2015. » DESIGN/ DEVELOPMENT You may already have a designed part and associated CAD files that require manufacturing, however we also offer a full design and development service if there is only a physical model to go from. Utilizing the latest CAD packages, including SolidWorks and Hypermill/ HyperCAD, allows us to undertake surface and solid modelling and we can also supply visual renders if required. All files are issue controlled and stored in a secure PDM vault. We are able to reverse engineer components to tight tolerances verified by our FARO Fusion arm which can take an unlimited number of precise measurement points. If needed, we also have a 3D scanner that allows us to capture and import complex surfaces into computer models. MATERIAL SELECTION Materials are selected based on cost, quality, operating parameters, structural requirements (toughness/ strength), durability, fire retardancy and availability. After material selection, full production control laminate and trim drawings are produced. PROTOTYPING If a proof of concept is needed, we can 3D print prototypes in ABS or standard PLA filament. Alternatively, we can use bureau services for SLS/ SLA models which allows testing for functionality, saving considerable time and money if the design needs tweaking. We can also make a low cost epoxy CNC tool and produce a composite component for one-off samples. » TOOLING, JIGS MANUFACTURE Design of the tooling occurs hand in hand with the design of the part (if we are involved in the part design process) and is discussed with you right from the start or we can design tooling to suit your part files. The material selected for tooling depends on a number of different factors including expected part quantities (one-off, batch or full-scale production), part complexity and curing requirements. For low volume production, CNC machined epoxy tooling block is often suitable however for medium to large production quantities we can also CNC machine tooling from aluminium or produce autoclaved composite tooling from male epoxy CNC patterns. Our tooling is designed using SolidWorks and HyperCAD/MILL allowing us to run draft analysis and provide tool manufacture run times. We also apply the correct expansion scaling factor to allow for cure temperatures. Steel drill bushes are used where needed in tools or drill jigs to improve accuracy and life of the tool. Patterns and tools are machined on site with our accurate HAAS VF4 3+1 axis (with on-machine measurement probing) or our Thermwood M67-55 5-axis router. All tools/jigs we create are logged and labelled on our MRP system for complete traceability and are linked to works order BOMs to ensure a smooth manufacturing process. » CUTTING » LAMINATING » CURING Once the parts are fully designed, signed off by you and the tooling has been manufactured, the project is ready to go into a first-of part sample before full production. PRE-PREG CUTTING & KITTING Using sophisticated SigmaNEST nesting software and 2 x CNC tables allows us to maintain consistent repeatability, minimize wastage, accurately control fibre direction and enable conformance to drawings. PRE-PREG LAMINATION We have an 880Sq ft clean room where plies from the CNC cut kit are hand-layed into the moulds by our skilled technicians. Plies and vacuum bagging are stringently cross checked by another employee of the same or higher skill level to ensure the production process runs smoothly and any mistakes are rectified before cure. Barcoded traceability part stickers are laminated and cured into the components. AUTOCLAVED MOULDING Our factory contains two autoclaves of different sizes, having the advantage of allowing the optimum size of autoclave to be chosen for a particular job, ensuring the best quality part and the most economical cost to you, the client. Autoclave curing the thermoset pre- pregs takes place at up to 100psi to give the best Fibre volume fraction and lowest void content. » TRIMMING » PAINTING » FINISHING RESIN INFUSION MOULDING (RIM) As well as autoclave moulding, we can also offer resin infusion moulding which is suitable for larger parts using dry fabrics and vacuum infused epoxy resin to achieve lower costs without potential thermal expansion or distortion issues. TRIMMING Once parts have been cured and released from the moulds, they are then sent to our dedicated trimming rooms. Our experienced trimmers remove any excess material and resin flash to EOP scribe lines using jigs and fixtures to prepare the part for final fitting or painting. Inserts, fasteners and other items are assembled to the moulding to complete the part. This will then be finished as required, either highly polished or rubbed down to a matte surface ready for painting. PAINTING/POLISHING Parts are prepared for painting by abrasive sanding or vapour blasting and then painted in our large spray booth (L4500mm x W3500mm x H2400mm) allowing us to be able to finish parts to high specification, coloured or clear coated using a wide range of paints and state of the art paint guns. We are able to meet very demanding levels of surface finish and peel and only use the highest quality polishing consumables to meet or exceed your specifications. » INSPECTION » QUALITY CONTROL We are equipped to provide complete inspections of finished parts to the required standards and specifications and provide simple or detailed ‘FAIR’ reports against client 3D CAD. For inspection, we have
Details
-
File Typepdf
-
Upload Time-
-
Content LanguagesEnglish
-
Upload UserAnonymous/Not logged-in
-
File Pages24 Page
-
File Size-