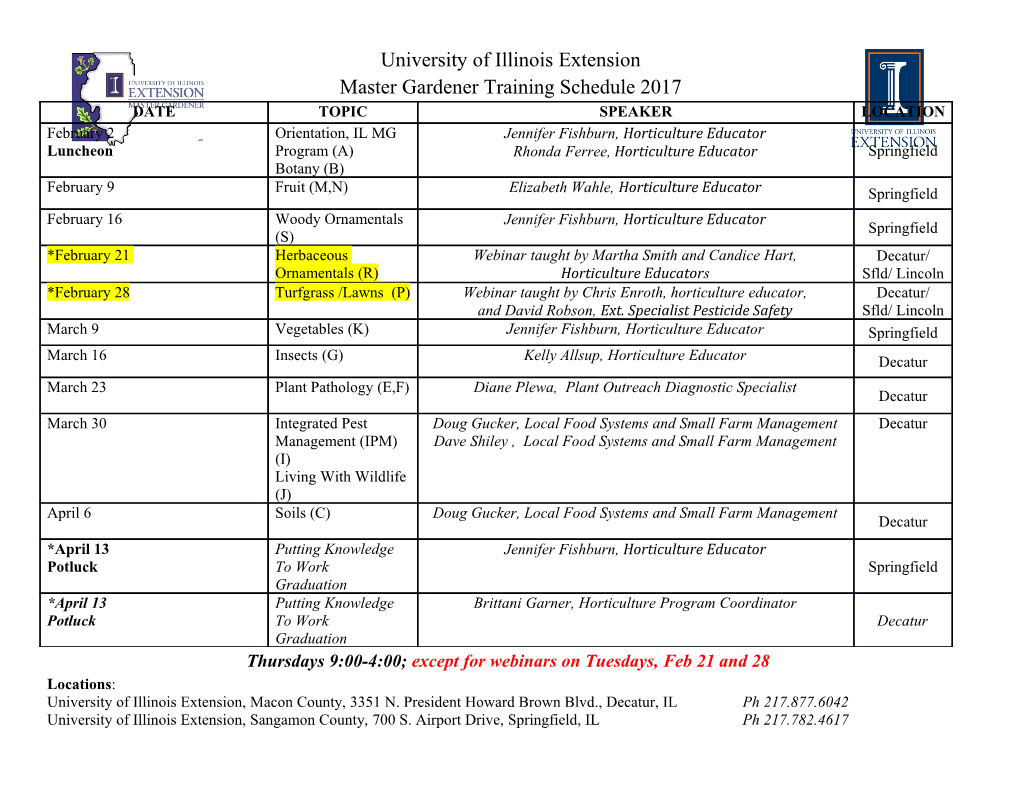
NASA Contractor Report 306s -!- .dl Analysis of a Theoretically Optimized TransonicAirfoil M. E. Lores, K. P. Burdges, and G. D. Shrewsbury CONTRACT NAS2-8697 NOVEMBER 1978 TECH LIBRARY KAFB, NM 00b1772 NASA Contractor Report 3065 Analysis of a Theoretically Optimized Transonic Airfoil M. E. Lores, K. P. Burdges, and G. D. Shrewsbury LockheedGeorgiaCompa~y Marietta,Georgia Prepared for Ames Research Center under Contract NAS2-8697 National Aeronautics and Space Administration Scientific and Technical Information Office 1978 Numerical optimization was usedin conjunction with an inviscid, full potent'ial equation, transonic flow analysis computer code to design an upper surface contour fora conventional airfoil to improve its supercritical performance. The modified airfoil was tested in the Lockheed-Georgia Com- pressible Flow Wind Tunnel. The majority of the test was done at eleven million Reynolds number anda four percent tunnel top and bottom wallporosity. A limited amount of testing was done to obtain data at other Reynoldsn umbe rs and wall porosities. The modified airfoilIs performance was evaluated by comparisonw ith test data for the baseline airfoiland for an airfoil developed by optimization of only the baseline airfoil'sleading edge. While the leading edge modification performed as expected, the upper surface re-designdid not produce all of the expected performance improvements. Although the drag divergence Mach number was increased, the modified airfoil exhibitedmore'drag creep than for the baseline section. This larger drag creep is attributable to the early formu- lation (at approximately L=.68) of a relatively strong leading edge shock wave. Theoretical solutions computed using a viscous, full potential equation transonic airfoil code were compared to experimental data for the baselineair- foil and the upper surface modification. These correlations showedthat the theory predicted the baseline airfoil's aerodynamics fairly well,but failed to accurately compute results for the upper surface modification. This fail- ure is shown to be attributable to the inability of the theory to properly treat the thick trailing edge boundary layer associated with the upper surface modification. Numerical optimization is concluded to offer the means for efficiently designing advanced airfoils. However, until a completely reliable viscous air- foil analysis technique is developed, optimization can be used with confidence only when the character of the viscous flow is significantlyalteredduringnot the optimization process. ii TABLE OF CONTENTS Page SUMMARY ................................ i i INTRODUCT I ON ............................. 1 SYMBOLS ................................ 4 AIRFOILDESIGN ............................ 5 ProblemDefinition ........................ 5 NumericalOptimization ...................... 6 EXPERIMENTALTESTS .......................... 10 Apparatus and TestProcedures .................. 10 Tests andMethods ........................ 12 RESULTS AND DISCUSSION ........................ 14 C141H7274 Airfoil Aerodynamics .................. 14 Comparison ofAirfoils ...................... 15 DesignMethod Evaluation ..................... 17 CONCLUDINGCOMMENTS .......................... 21 REFERENCES .............................. 22 APPENDIX A: PLOTTEDTEST DATA .................... 61 iii . I NTRODUCT I ON Efficienttransonic performance continues to bean importantdesign requirementfor manynew aircraft.Specialized airfoils whose contoursare dependentupon design conditions are needed toachieve the desired transonic performance. To designthese airfoils rapidly and effectively,aerodynamicists musthave availableaccurate and easy-to-usetheoretical design methods.The nonlinearityof the partial differential equations that describe transonic flows hashampered thedevelopment of such theoreticaldesign methods. However, advances incomputational fluid dynamics, together with the availability of large and fastcomputers, have resultedin the recent availability of anumber oftransonic design techniques. Airfoildesign methodscan be categorized as eitherinverse or direct procedures.Inverse methods involve the specification of a desiredpressure distribution and thecalculation of the corresponding airfoil. The need to specify a priori a pressuredistribution that will resultin a physically realisticoptimized airfoil is a disadvantageof inverse procedures. inverse methodshave been formulatedeither by usinghodograph equations or by solving theproblem in the physical plane (e.g., refs. 1 and 2, respectively).Since hodographformulations are applicable only to shock-free flows, they are of limitedusefulness in transonic design. Also, considerable user expertise is requiredto employhodograph design methods. Physical-plane solutions suffer computationaldifficulties in the leading edge regionwhich are usually avoid- edby specifyingthe airfoil geometrynear the leading edge. Sinceproper leading edge designis needed todesign optimized transonic airfoils, this approach limitsthe usefulness of physical plane inverse solutions in transonic designwork. The above-mentioned difficulties are avoided in direct design methods. inthis design approach, a numericaloptimization algorithm is coupledwith a suitableaerodynamic analysis method todesign airfoils that are in some sense optimizedfor .specific flight conditions. For example, an airfoil con- tour canbe determined which minimizes drag at a specific lift coefficient withthe pitching-moment coefficient constrained to be withinacceptable limits. Perhaps the most promisingdirect design method is underdevelopment at NASA-Ames byHicks and hisassociates. The method isdescribed and-example designsare discussed in references 3 and 4. Briefly,the method involves coupling a numericaloptimization scheme developedby Vanderplaats (ref. 5) withproven airfoil analysis methods. The abilityto useany theoretical analysis methodand any numericaloptimization'algorithm makes thetechnique very versatile. Currently,the transonic full potential codedeveloped by Jameson (ref.6) isbeing used toprovide the neededaerodynamic data. Viscous effects, known to be importantin transonic flow calculations, are neglected in Jameson's analysis method. An inviscidaerodynamic module is usedbecause currently availableviscous transonic airfoil analysis programsare not completely re- liable, and theyrequire more computationtime than inviscid techniques. Experiencewith applying the procedure to design subsonic airfoils has indi- catedthat aerodynamic performance predicted by inviscid methods will be manifested when a viscousanalysis of the resulting airfoil is performed. Thereis, nevertheless, aneed toexperimentally verify the performance of transonicairfoils designed usingthe inviscid procedure. Because of its versati lity,Hicks' method should be usefulboth in tran- sonicdesign projects in wh ichperformance improvements inexisting aircraft aresought by airfoilmodif ication, and inprojects in which new airfoils for advanced aircraftare required. The first applicationis being investigated in a projectbeing conducted by Lockheed. Withthe aid of Hicks, Lockheed researchersrecently appl ied the procedure to the redesign of the forward 12% ofthe C-141 airfoilleading edge. Thisapplication was selected because that airfoil exhibits a largedrag creep which might be reducedby a limitedmodi- ficationof the leading edge. Thiswork was successfulin that the predicted dragcreep was reduced tothe same levelobtained by a trial and correction processin which analysis methodswere used toevaluate many candidateleading- edge modifications,but in a fractionof the time. The airfoil leading-edgedesign using Hicks' method was obtainedby mod ifyingonly the C-141 airfoil uppersurface. In contrast, the airfoils des ignedusing the trial-and-correction procedure involved simultaneous upper 2 and lowersurface modifications. Consequently, Hicks' modification may be easierto incorporate as an aircraft change. Further, because it has a larger leading-edgeradius, Hlcks' airfoil may providebetter low-speed stall charac- teristicsthan either the basic C-141 sectionor the other proposed airfoil modifications. The Hicks'modification to the C-141 airfoil leading-edge,as well as the basic C-141 section, havebeen testedin the LockheedCompressible Flow Wind- Tunnel (CFWT) attransonic speedsunder an internal Lockheed research program. Airfoilsurface pressure distributions and theattendant forces and moments were obtainedfor an extensiverange of Mach numbersand lift coefficients. These datasubstantiated the theoretically predicted performance improvements resultingfrom numerical optimization. The windtunnel test data showed that a 7% improvement in (ML/D) may have resultedfrom the modification of the upper surfaceof the forward 12% ofthe airfoil. In addition to producing an effic- ientairfoil modification, numerical optimization required about half the comp- utation time and resultedin a25% reductionin engineering hours when compared to a conventionaltrail-and-correction approach. The purpose of the workreported herein was to determine the applicability ofnumerical optimization in an extensiveredesign of a conventionalairfoil to improve itssupercritical performance. The problemselected was there-contour ingof the entire upper surface of the baseline C-141A wingairfoil section. Thisproblem was selected because the availability of the workalready done on the C-141 airfoil uppersurface leading-edge modification premitted an efficient comparison of the use of numericaloptimization for limited
Details
-
File Typepdf
-
Upload Time-
-
Content LanguagesEnglish
-
Upload UserAnonymous/Not logged-in
-
File Pages104 Page
-
File Size-