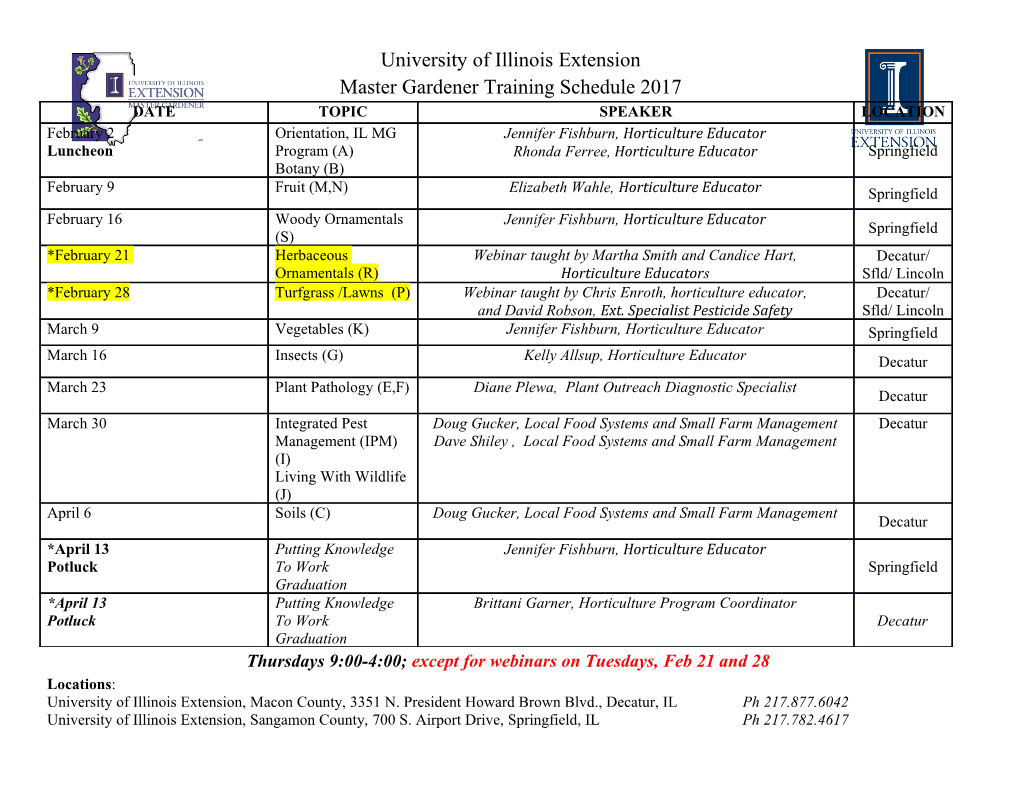
Robotic Vacuum Cleaner Design to Mitigate Slip Errors in Warehouses By Benjamin Fritz Schilling Bachelor of Science in Mechanical Engineering New Mexico Institute of Mining and Technology, New Mexico, 2016 Submitted to the Department of Mechanical Engineering in partial fulfillment of the requirements for the degree of Master of Engineering in Advanced Manufacturing and Design at the MASSACHUSETTS INSTITUTE OF TECHNOLOGY September 2017 © 2017 Benjamin Fritz Schilling. All rights reserved. The author hereby grants to MIT permission to reproduce and to distribute publicly paper and electronic copies of this thesis document in whole or in part in any medium now known or hereafter created. Signature of Author: Department of Mechanical Engineering August 11, 2017 Certified by: Maria Yang Associate Professor of Mechanical Engineering Thesis Supervisor Accepted by: Rohan Abeyaratne Quentin Berg Professor of Mechanics & Chairman, Committee for Graduate Students 1 (This page is intentionally left black) 2 Robotic Vacuum Cleaner Design to Mitigate Slip Errors in Warehouses By Benjamin Fritz Schilling Submitted to the Department of Mechanical Engineering on August 11, 2017 in partial fulfillment of the requirements for the degree of Master of Engineering in Advanced Manufacturing and Design Abstract Warehouses are extremely dusty environments due to the concrete and cardboard dust generated. This is problematic in automated warehouses that use robots to move items from one location to another. If the robot slips, it can collide with other robots or lose track of where it is located. Currently, to reduce the amount of dust on the floor, warehouses use industrial scrubbers that users walk behind or ride. This requires manual labor and a regular scheduled maintenance plan that needs to be followed to mitigate the dust accumulation. Therefore, an industrial robotic vacuum cleaner that can continuously clean the warehouse floors is proposed. The five key parts to a vacuum are inlet duct, brush roller, filtration, storage, and suction. This thesis will discuss in detail the design and development of the filtration, storage, and suction of the robotic vacuums that were developed in this project. The thesis will go through design considerations and computational fluid dynamics that were conducted to validate and improve the design. Then, it will discuss the experimental results of the robotic vacuum cleaners. Thesis Supervisor: Maria Yang Title: Associate Professor of Mechanical Engineering 3 (This page is intentionally left black) 4 Acknowledgements I would like to take this opportunity to express my gratitude to the people that have been supportive throughout my educational experience here at MIT and throughout my life. First, I would like to thank my family for their continuous support, encouragement, and unconditional love. I would especially like to thank my parents, Scott and Lori Schilling, and my brother Isaac Schilling, for their insurmountable support throughout my life. Without them, I would not have been able to accomplish or do the things that I have done thus far. Thank you for pushing me to pursue my dreams. I would like to thank my thesis advisor, Professor Maria Yang, who has provided helpful guidance throughout my thesis project. I would also like to thank Jose Pacheco and Professor David Hardt, who gave me the opportunity to be a part of the Master of Engineering in Advanced Manufacturing and Design. I would like to express my gratitude to the company for providing me with a fabulous experience and an enjoyable project. I would especially like to thank Jude for his insightful engineering guidance, patience, and mentorship of our group at the company. I would also like to thank Peter for supporting, guiding, and providing engineering guidance throughout the project. Thanks to Craig for doing the electronics and making the firmware work for our prototypes. Thanks to Dragan, Gabriel, Jennifer, and Allan for providing their engineering expertise and assistance. I am thankful to Ron and Mark for assisting in fabricating parts in the machine shop and allowing us to use the machine shop to build our prototypes. Finally, I would like to thank everyone at the company who helped my team and I with the project and made it a rewarding experience. Last, but definitely not least, I would like to thank my wonderful teammates, Barbara Maia Araujo Lima, Jody Fu, and Youngjun Joh for their excellent collaboration and engineering ideas. I had a fabulous time working with this group, and without this team we would not have been able to accomplish what we did. 5 (This page is intentionally left black) 6 Table of Contents Abstract ........................................................................................................................................... 3 Acknowledgements ......................................................................................................................... 5 List of Figures ................................................................................................................................. 9 List of Tables ................................................................................................................................ 10 Definition of Key Terms ............................................................................................................... 11 Chapter 1 : Introduction ................................................................................................................ 14 1.1 Motivation ...................................................................................................................... 14 1.2 Objective ........................................................................................................................ 15 1.3 Functional Requirements................................................................................................ 15 1.4 Scope .............................................................................................................................. 15 1.5 Task Division ................................................................................................................. 15 Chapter 2 : Background Information ............................................................................................ 17 2.1 Current Robotic Vacuums on the Market ...................................................................... 17 2.2 Inertial Separation .......................................................................................................... 19 2.3 Blower Selection ............................................................................................................ 19 2.4 Scroll Design .................................................................................................................. 21 Chapter 3 : Mechanical Design of Vacuum Bin and Blower Assembly ....................................... 23 3.1 Bin .................................................................................................................................. 23 3.2 Trapdoor ......................................................................................................................... 24 3.2.1 Finite Element Analysis to Determine O-Ring Compression on Trapdoor ............ 25 3.3 Filters and Filter Plate .................................................................................................... 27 3.4 Blowers........................................................................................................................... 29 3.5 FEA to Determine the Theoretical Compression on the O-Rings .................................. 30 3.5.1 Front Plate FEA ...................................................................................................... 31 3.5.2 Filter Plate FEA ...................................................................................................... 33 3.5.3 FEA Blower Cover Plate ........................................................................................ 35 3.5.4 Theoretical Percent Compression ........................................................................... 36 3.5.4.1 Force Required to Compress AS568A-280 O-Rings with a Shore A Hardness of 50A ........................................................................................................................ 36 3.6 Second Prototype Bin and Blower Assembly ................................................................ 38 3.7 Blower Housing.............................................................................................................. 39 7 3.8 Cleaning Hatch ............................................................................................................... 40 3.9 Filter ............................................................................................................................... 41 3.10 Piston Seals .................................................................................................................... 41 Chapter 4 : Experimental Results and Analysis ........................................................................... 42 4.1 Particle Separation.......................................................................................................... 42 4.1.1 Computational Fluid Dynamic Setup...................................................................... 42 4.1.2 CFD Results ............................................................................................................ 44 4.1.3
Details
-
File Typepdf
-
Upload Time-
-
Content LanguagesEnglish
-
Upload UserAnonymous/Not logged-in
-
File Pages84 Page
-
File Size-