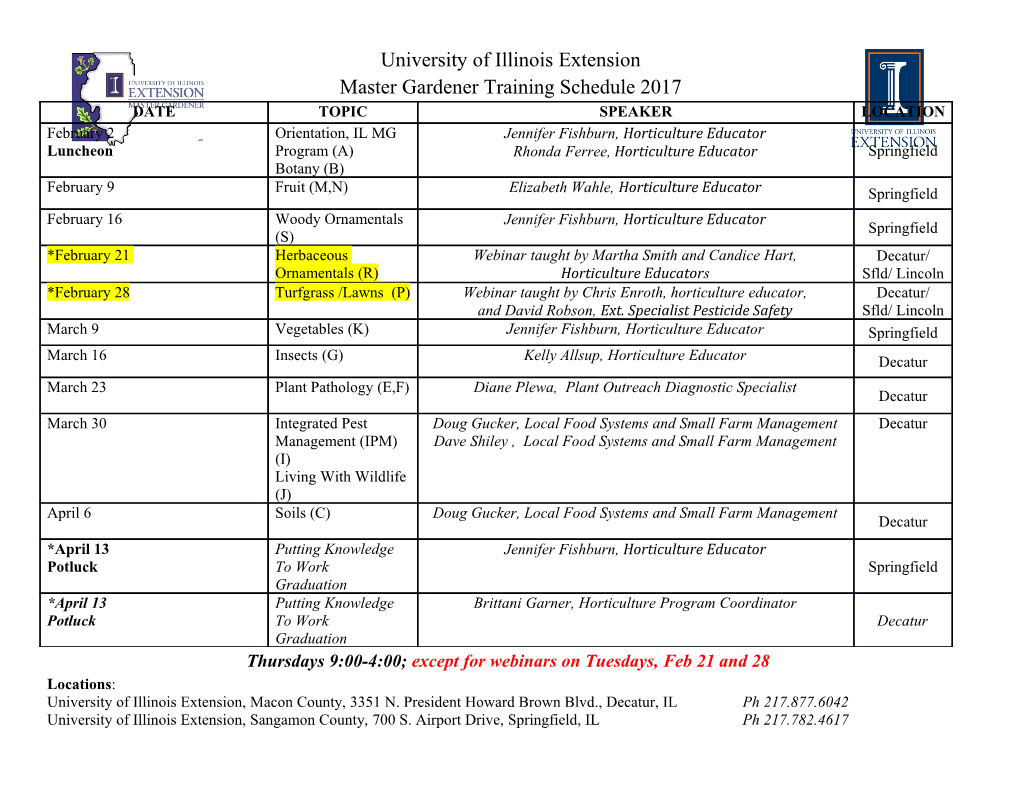
Digital Comprehensive Summaries of Uppsala Dissertations from the Faculty of Science and Technology 1635 Protective Tribofilms on Combustion Engine Valves ROBIN ELO ACTA UNIVERSITATIS UPSALIENSIS ISSN 1651-6214 ISBN 978-91-513-0243-0 UPPSALA urn:nbn:se:uu:diva-342549 2018 Dissertation presented at Uppsala University to be publicly examined in Polhemsalen, Lägerhyddsvägen 1, Uppsala, Friday, 13 April 2018 at 13:15 for the degree of Doctor of Philosophy. The examination will be conducted in English. Faculty examiner: Dr Mikael Åstrand (Infranord AB). Abstract Elo, R. 2018. Protective Tribofilms on Combustion Engine Valves. Digital Comprehensive Summaries of Uppsala Dissertations from the Faculty of Science and Technology 1635. 83 pp. Uppsala: Acta Universitatis Upsaliensis. ISBN 978-91-513-0243-0. Inside the complex machinery of modern heavy-duty engines, the sealing surfaces of the valve and valve seat insert have to endure. Right next to the combustion, temperatures are high and high pressure deforms the components, causing a small relative motion in the interface. The wear rate of the surfaces has to be extremely low; in total every valve opens and closes up to a billion times. The minimal wear rate is achieved thanks to the formation of protective tribofilms on the surfaces, originating from oil residues that reach the surfaces - even though these are not intentionally lubricated. The increasing demands on service life, fuel efficiency and clean combustion, lead to changes that may harm the formation of tribofilms, which would lead to dramatically reduced service lives of the valves. This calls for an improved understanding of the formation of tribofilms and how their protective effects can be promoted. The best protective effect is provided by tribofilms formed from engine oil additives. This is not a typical lubricating effect, but protection by formation and replenishment of a solid coating. Oils without additives cannot form solid films that offer the same protection. Tribofilms are formed from oil residue particles that land, agglomerate and so gradually cover the surfaces. Once covered, the surfaces stay protected relatively long also if no new residues reach the surface. In fact, the tribofilms have a higher wear resistance than do the component surfaces. If the tribofilms become worn off, the underlying surfaces wear quickly, but as long as new residues reach the surfaces, the tribofilms can rebuild and maintain the wear protection indefinitely. This tribofilm formation and endurance can be promoted by texturing the surfaces. A texture can improve the amount of oil residues captured and their surface coverage, reducing random occurrence of wear and the demand for new residues to maintain the tribofilm. The tribofilm formation is also affected by the additive content of the engine oil, where especially high sulfur content is found to promote tribofilm coverage. A custom engine oil with high additive content could be used for efficient tribofilm formation during running-in of engines. Keywords: Internal combustion engine, valve, sealing surface, tribofilm, oil residue, test rig Robin Elo, Department of Engineering Sciences, Applied Materials Sciences, Box 534, Uppsala University, SE-75121 Uppsala, Sweden. © Robin Elo 2018 ISSN 1651-6214 ISBN 978-91-513-0243-0 urn:nbn:se:uu:diva-342549 (http://urn.kb.se/resolve?urn=urn:nbn:se:uu:diva-342549) Till Elsa List of Papers This thesis is based on the following papers, which are referred to in the text by their Roman numerals. I The importance of oil and particle flow for exhaust valve wear – An experimental study P. Forsberg, R. Elo and S. Jacobson Tribology International, 69 (2014) 176-183 II Formation and breakdown of oil residue tribofilms protecting the valves of diesel engines R. Elo and S. Jacobson Wear, 330-331 (2015) 193-198 III Surface texturing to promote formation of protective tribofilms on combustion engine valves R. Elo, J. Heinrichs and S. Jacobson Proceedings of the Institution of Mechanical Engineers, Part J: Journal of Engineering Tribology, 232(1) (2018) 54-61 IV Wear protective capacity of tribofilms formed on combustion engine valves with different surface textures R. Elo, J. Heinrichs and S. Jacobson Wear, 376-377 (2017) 1429-1436 V Tribofilm formation on combustion engine valves – influence of additive content in the oil R. Elo and S. Jacobson In manuscript Reprints were made with permission from the respective publishers. Author’s contributions to the papers Paper I Substantial part of experimental work. Part of planning, eval- uation and writing. Paper II All experimental work. Major part of planning, evaluation and writing. Paper III Major part of planning, evaluation, writing and experimental work. Paper IV Major part of planning, evaluation, writing and experimental work. Paper V All experimental work. Major part of planning, evaluation and writing. Contents 1 Introduction ................................................................................................ 11 2 Tribology ................................................................................................... 13 2.1 Friction, wear and lubrication ............................................................ 13 2.2 Strategies for extremely low wear rates ............................................. 14 3 Internal combustion engines ...................................................................... 16 3.1 Different types of modern engines ..................................................... 16 3.2 Efficient internal combustion ............................................................. 17 3.3 Engine oil ........................................................................................... 18 3.3.1 Base oil ....................................................................................... 18 3.3.2 Engine oil additives .................................................................... 19 4 The valve system in internal combustion engines ..................................... 21 4.1 Valve and valve seat insert ................................................................. 22 4.1.1 Materials ..................................................................................... 23 4.2 Wear of the valve system ................................................................... 26 5 Tribofilms .................................................................................................. 33 5.1 Ability to rebuild ................................................................................ 35 5.2 Composition ....................................................................................... 36 5.3 Tribofilm properties ........................................................................... 38 5.4 Challenges for tribofilms .................................................................... 41 6 Experimental .............................................................................................. 43 6.1 The valve rig ....................................................................................... 43 6.2 Field tested samples ........................................................................... 47 6.3 Analysis techniques ............................................................................ 49 6.3.1 Light optical microscopy ............................................................ 49 6.3.2 Scanning electron microscopy .................................................... 50 6.3.3 Energy dispersive X-ray spectroscopy ....................................... 51 6.3.4 Electron spectroscopy for chemical analysis .............................. 53 6.3.5 Nano indentation ......................................................................... 54 6.3.6 Cross sectioning techniques ........................................................ 54 7 Contributions ............................................................................................. 57 7.1 Effect of oil additives ......................................................................... 57 7.2 Formation of tribofilms ...................................................................... 59 7.3 Textured surfaces ............................................................................... 62 7.4 Effect of additive compositions .......................................................... 68 8 Conclusions ................................................................................................ 71 9 Sammanfattning på svenska ....................................................................... 73 10 Acknowledgements .................................................................................. 78 11 References ................................................................................................ 80 Abbreviations BIB broad ion beam CI compression ignition EDS energy dispersive X-ray spectroscopy ESCA electron spectroscopy for chemical analysis FIB focused ion beam fps frames per second LOM light optical microscopy NI nano indentation ppm parts per million rpm revolutions per minute SAPS sulfated ash, phosphor and sulfur SEM scanning electron microscopy SI spark ignition VSI valve seat insert ZDDP zinc dialkyldithiophosphates 1 Introduction Internal combustion engines are used all over the world to convert the ener- gy stored in fuel into torque. This torque can be used to propel vehicles, drive machinery, or be converted into electricity by generators. The technique has been in common use since the latter half of the 19th century and it is not difficult
Details
-
File Typepdf
-
Upload Time-
-
Content LanguagesEnglish
-
Upload UserAnonymous/Not logged-in
-
File Pages84 Page
-
File Size-