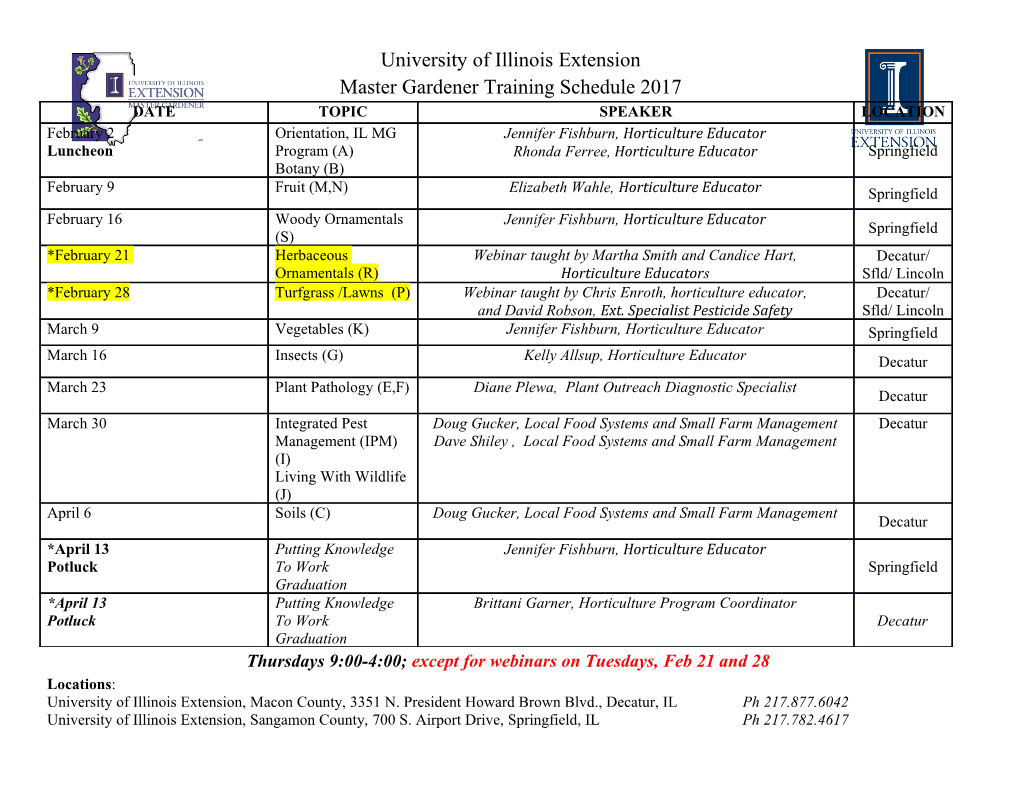
05WAC-61 Design and Flight Testing of Inflatable Wings with Wing Warping Jamey D. Jacob, Andrew Simpson, and Suzanne Smith University of Kentucky, Lexington, KY 40506 Copyright c 2005 Society of Automotive Engineers, Inc. ABSTRACT The paper presents work on testing of inflatable wings for unmanned aerial vehicles (UAVs). Inflatable wing his- tory and recent research is discussed. Design and con- struction of inflatable wings is then covered, along with ground and flight testing. Discussions include predictions and correlations of the forces required to warp (twist) the wings to a particular shape and the aerodynamic forces generated by that shape change. The focus is on charac- terizing the deformation of the wings and development of a model to accurately predict deformation. Relations be- Figure 1: Goodyear Model GA-468 Inflatoplane. tween wing stiffness and internal pressure and the impact of external loads are presented. Mechanical manipula- tion of the wing shape on a test vehicle is shown to be an effective means of roll control. Possible benefits to aero- craft was developed as a military rescue plane that could dynamic efficiency are also discussed. be dropped behind enemy lines to rescue downed pilots. Technology development, including delivery of dozens of INFLATABLE WINGS aircraft, continued until the early 1970s. PREVIOUS WORK While the concept of inflatable The Apteron unmanned aerial vehicle with inflatable structures for flight originated centuries ago, inflatable wings was developed in the 1970s by ILC Dover, Inc. wings were only conceived and developed within the last The Apteron (Figure 2) had a 1.55 m (5.1 ft) wingspan, few decades. While lighter-than-air vehicles also include a 373 W (0.5 hp) engine, a 3.18 kg (7 lb) gross weight inflatable structures, our focus herein is on inflatable struc- and was remotely-controlled via elevons mounted on the tures used solely for lift generation. Various aspects of trailing edge. The Apteron was successfully flight tested, inflatable structures are discussed elsewhere [1] while a but was never put into production. review of inflatable wing and related technologies is in- cluded in Cadogan et al. [2] To provide context for the Flight tests of deployment and low-altitude (800-1,000 ft) results of this paper, a selection of design concepts is in- flight of the I2000 UAV using inflatable wings were con- cluded below emphasizing recent developments in inflat- ducted in 2001 by researchers at NASA Dryden. The able wings. wings were developed by Vertigo, Inc. for the Navy as a gun launched observation vehicle . The skeleton of Inflatable wings were successfully demonstrated in the the wing was made of inflatable tubes, surrounded with 1950s with the Goodyear Inflatoplane (Model GA-468 is crushable foam to provide the airfoil cross-section. After shown in Figure 1 and is also on display in the Patuxent the aircraft was released, the five-foot span inflatable wing River Naval Air Museum). The 6.7 m (22 ft) wingspan air- was successfully deployed in about one-third of a second. To maintain suitable wing strength and stiffness, nitrogen 1 Figure 2: ILC Dover Apteron UAV. Figure 4: Non-Inflated wing and inflated wings. Figure 3: In flight deployment of NASA Dryden I2000 in- flatable wing. gas pressurization of 1380-1725 kPa (200-250 psi) was required. [3] The deployment is shown in Figure 3. INFLATABLE WINGS AT UNIVERSITY OF KENTUCKY Figure 5: ILC Dovers multi-spar Inflated wing and packed The University of Kentucky has been working with ILC configuration. Dover, Inc. on the development and testing of inflatable wings. Two variants have been developed and tested: inflatable only wings that require constant pressurization One potential application directing aspects of the devel- to maintain shape and inflatable/rigidizable wings that opment of inflatable/rigidizable wing technology is use harden into a persistent shape once inflated. The latter on a “Mars Airplane.” [8, 9, 10, 11] Current plans for were tested first. UV-curable resins under development Mars exploration include smaller Scout missions to ex- for spacecraft applications were considered for the inflat- pand the explored area. One concept under considera- able/rigidizable wings. [2, 4, 5, 6, 7] The wings are con- tion is an unmanned spacecraft launched to Mars to re- structed of a composite material that becomes rigid on ex- lease an aircraft designed to fly an exploratory mission posure to UV light. The wings are assembled by sewing over a wider range than a lander/rover and from a closer woven material to create the airfoil and internal baffling. distance than an orbiter. Motivated by the requirement for For the inflatable/rigidizable wings, a layered material was a minimal packed-volume-to-weight ratio, an alternate ap- used consisting of an external containment film, layers proach for the proposed folding wing designs is an inflat- of resin-impregnated woven fabric selected for handling able composite wing impregnated with a UV-curable resin. characteristics, and an internal containment layer. An in- With this approach, wings are pressurized for deployment flatable urethane bladder is inserted, with long finger-like then rigidized with exposure to UV radiation from the sun. sections filling each baffle of the sewn wing. Figure 4 Once rigid, the wings no longer require pressurization to shows the inflatable/rigidizable wing before inflation and maintain their shape. [12] the wing while inflated during laboratory testing. This multi-spar design does not use foam spacer material and Feasibility of these concepts are being tested through so packs compactly. The inflatable non-rigidizable design a series of high-altitude experiments. The flight ex- is shown in Figure 5. The design is similar to the rigidiz- periments that validated this technology included three able version, but does include the impregnated resin and stages: 1) balloon-launched ascent to deployment alti- external containment film. tude, 2) deployment of inflatable-rigidizable wings and 2 WARPING INFLATABLE WINGS The current research efforts are focused on warping an inflatable non- rigidizable wing to provide roll control through wing warp- ing. Inflatable wings were developed by ILC Dover, Inc. which were not impregnated with the UV curable resin for use in other applications where higher wing loading is re- quired. Since the wings do not harden, constant internal pressure is required to resist flight loads. As the wings are entirely inflatable, they do not contain ailerons. Thus, vehicles employing inflatable wings must generate a roll moment by other means. However, as the wings are non- rigid, it is possible to actively manipulate the shape of the Figure 6: Recovery of second-generation inflat- wings to provide this roll moment. able/rigidizable high-altitude test article. Another motive for altering the wing shape is to improve the airfoil efficiency. Principally, efficiency is maximized by increasing the lift L and decreasing the drag D or max- imizing the lift-to drag ratio (L/D) for any configuration. A given airfoil profile has vastly differing lift and drag char- acteristics over the possible ranges of Reynolds Number (Re) and Mach number (M). Thus, airfoils are typically designed for a narrow range of flight conditions. Alter- natively, airfoils can be designed that perform adequately over a wide range of conditions, but do not perform well in any. By altering the shape of the wing, the L/D ratio can be changed across the length of the wing. Assymmet- ric shape changes generates differential lift between the two semi-spans while deforming the semi-spans symmet- rically would provide an altered lift distribution that could be optimized for maximum L/D. The differential loading Figure 7: Inflatable wing high-altitude test article at scenario can potentially be used to generate the required 98,000’. roll moments for the aircraft. WING DESIGN continued ascent to near 100,000 ft, and 3) release from the balloon and gliding descent under autonomous con- INFLATABLE WING CONSTRUCTION The inflatable trol. Note that ground-level atmospheric density on Mars wing is designed such that constant internal wing pres- is similar to that at 100,000 ft on Earth. Balloon-launched sure is required to maintain wing shape. High stiffness is high-altitude experiments to date include the first-ever achieved with low inflation pressure by maximizing inflated demonstration of inflatable/rigidizable wing technology on sectional moment of inertia. Since the wing is constructed May 3, 2003 with successful deployment of inflatable of a flexible fabric material, it can be stowed by folding wings at 55,000 ft, curing on continuing ascent to 89,603 or rolling. Previous inflatable wing designs required high ft and descent to recovery. [13] gage pressures to maintain wing shape. This typically re- quires the use of heavy seals and gaskets and thicker More recent efforts considered tailoring the composite than desired wall thicknesses for the wing material. It layering design for weight reduction. [13] A second also means that any leak, however small, will result in the demonstration experiment on May 1, 2004 resulted in rapid depressurization of the wing and loss of structural deployment and curing of the second-generation inflat- integrity. able/rigidizable wings. Figure 6 shows the test article after flight inflation and rigidization at the recovery site. The present wing design uses the presence of internal Flight characteristics, aerodynamic performance, aero- span-wise baffles or inflation cavities to help maintain dynamic analysis and wind-tunnel testing for the inflat- structural stiffness at lower internal pressures. The outer able/rigidizable wings are detailed elsewhere. [14, 15]A wing (restraint) and internal baffles are constructed from third flight using a Vectran non-rigidizable wing was com- high strength fibers such as Kevlar. The current incar- pleted on April 30, 2005 and reached altitudes of over nation as tested herein is made of Vectran, a manufac- 98,000 feet (Figure 7).
Details
-
File Typepdf
-
Upload Time-
-
Content LanguagesEnglish
-
Upload UserAnonymous/Not logged-in
-
File Pages10 Page
-
File Size-