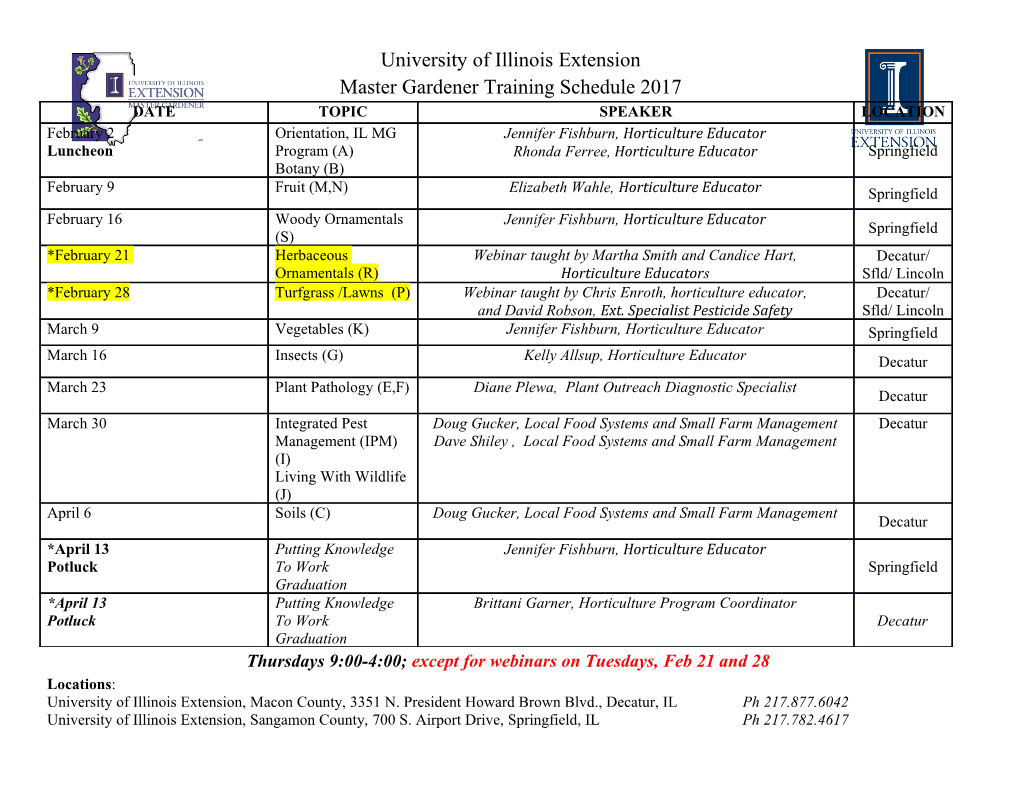
Aircraft turbine engine control systems development: Historical Perspective Jackson Lutambo1, Jiqiang Wang 1, 2, Hong Yue3, Georgi Dimirovsky4 1. Jiangsu Province Key Laboratory of Aerospace Power System, Nanjing Universityof Aeronautics and Astronautics,Nanjing,210016, China 2. AVIC Shenyang Engine Design & Research Institute, Shenyang 110015, China 3. The University of Strathclyde, Glasgow, UK 4. Dogus University of Istanbul, Istanbul, Turkey E-mail: [email protected], [email protected], [email protected], [email protected] Abstract: This paper describes the development of aircraft turbine engine control systems from the historical point of view to the present. With the increasing emphasis on aircraft safety, enhanced performance, and affordability, as well as the need to reduce the environmental effect caused by aircraft, there are many new challenges being faced by the designers of aircraft propulsion systems. The paper provides an overview of the various technological development activities in aircraft engine control and diagnostics, both current and some accomplished in the recent past. The motivations for each of the research efforts, the research approach, technical challenges, and the key progress to date are summarized. Keywords: Control system, Gas Turbine Engine, Hydromechanical System, FullAuthority Digital Electronic Control (FADEC), Digital Electronic Engine Control (DEEC) 1.0 Introduction still the main control strategy in many systems. The goal of any engine control system is to allow the Other control signals are often open loop scheduled, engine to perform at maximum efficiency for a given or used only for limiting engine parameters. condition. The complexity of this task is proportional Interaction among the various control loops are most to the complexity of the engine. Historically, jet often neglected in the design of control law and the engines have been controlled by hydromechanical resulting problems are solved by a large number of control systems which consisted of simple fixes and special cases andthis still works mechanical linkages controlled by the pilot. As the satisfactorily for the engines used today [1]. engines have become more complex, with more The trend towards increasingly complex jet engines control signals and higher demands on performance will undoubtedly continue in order to meet increasing and functionality, electronic control systems have demands on performance, fuel consumption and been introduced [1].The modern aero-engine used functionality. The interaction between the engine and today for aircraft propulsion has evolved into its aircraft systems will also increase, with mission- current form over the past 60 years, and Control specific control and with the control of thrust technology has played a critical role in improving the direction. To utilize the potential of these engines, it performance, reliability, operating lifetime, and is also necessary to use more advanced control safety. Today all modern aero engines are controlled concepts than conventionally used today. The trend is by Full Authority Digital Electronic control (FADEC) towards control concepts often referred to as ‘smart systems, or a combination of electronic and engines’ andthe multivariable controllers are most hydromechanical systems. The control functions often the core of these advanced control concepts[1]. implemented in many of these systems have not This paper discuss some of the developments which changed that much. The principle of using only fuel have taken place since the introduction of turbine flow for speed control and limit the amount during engine as the main propulsion device on the aircraft transients, as in the first hydromechanical systems is with regards to the control systems. † We wish to acknowledge the support of the Natural 2.0 The birth ofTurbine Engine Control Science Foundation of Jiangsu Province (No. BK20140829); Systems Jiangsu Postdoctoral Science Foundation (No.1401017B); and The 1930’s saw the evolution of independent design the Scottish Government which funded this project through the and development work on gas turbine engines in Royal Society of Edinburgh in partnership with the NNSFC; Fund for Science of Dogus University Great Britain and Germany. Sir Frank Whittle patented his gas turbine engine in 1930 and after several years of development, a version of the same was first installed on an aircraft in 1941 [2]. Hans growth of electronics and computer technology with von Ohain had a patent for his engine in Germany in their enhanced reliability enabled full authority 1936 and the first flight with this engine had taken digital electronics to be used. A historical perspective place in 1939 [2]. The first gas turbine engine of the advancement in control technologies for developed by Whittle [2] had a simple throttle lever aircraft gas turbine engines related to the US scenario that controlled fuel flow into the engine. To has been outlined in [6]. A simple engine speed- accommodate the functional requirements when fitted power lever angle loop is illustrated in Figure 1. on aircraft, design of fuel control system had to take into account effects of altitude, temperature and forward speed [3]. At the same time, continued requirements to improve gas turbine engine performance, production and life limiting processes had their impacts on gas turbine technologies [3]. In the 1950s, aircraft engine control systems were based on hydromechanical technologies and were complex PLA – Power Lever Angle, FF – Fuel Flow, N – Rotational artifacts. They encompassed a large number of Speed, MV- metering valve, Nd – N-Demand, MVd – MV- components and subcomponents, and they were demand, Nact – N-actual, MVact – MV-actual application-specific, such that a change in the design of the engine required a change in the design of the Figure 1: Typical engine speed-Power Lever Angle (PLA) control system. Hydromechanical control systems loop reached a technological ceiling in a relatively short time. The maturity of the technology enabled 3.0 Hydromechanical Fuel Control engineers to understand, articulate, and modularize The jet engine was first adopted as a source of thrust the interfaces between the engine and the in aircrafts in the 1930s. Simple mechanical fuel hydromechanical control system. Furthermore, controls comprising cams and levers were used in performance improvements derived primarily from reciprocating engines, which constituted the majority operational experience rather than from scientific or at the time [9]. The control required by jet engines technological breakthroughs had their impacts on was comparatively complex, and the existing turbine technology[4]. In the mature stage of technology was inadequate. Even in the case of early development reached in the 1970s, hydromechanical post-war turbojet engines, variables of fuel flow or control systems were characterized by a relatively bleed valve could only be controlled. Subsequently, low rate of technological change and increasingly advances in the level of precision and miniaturization predictable interdependencies with the other in the areas of mechanics and oil hydraulics led to components. Although hydromechanical control progress in the control technologies of aircraft systems had achieved relatively high reliability, they engines. Till the 1970s, the operating mechanism for displayed limitations. Higher-thrustengines that were engine control merely consisted of a being developed during the 1970s were characterized hydromechanical system that combined mechanics, by a larger number of parameters that needed such as the axis, gear, spring, bellows, cam, governor, accurate measurement and computation. In particular, and valve adjustment screws, with fuel pressure the increasing bypass ratio (i.e., the ratio of mass [9].Hydromechanical control systems consist flow through the fan or bypass duct to that through primarily of a fuel metering unit and an engine speed the core) of the newly developed engines posed sensor. The fuel metering unit maintains even fuel several problems for the calculation and control of pressure on both ends of the fuel metering valve by thrust during engine operation. To avoid over-boost adjusting the fuel flow through the valve. This and over-temperature, more frequent adjustmentsof method of regulating fuel remains in use today, even the power lever were required, and traditional though the mainstream technology has shifted to hydromechanical control systems could not manage digital electronic controls. Engine RPM is detected these problems. The complexity of thrust calculations, through a mechanism in which the centrifugal force the high accuracy andquick-response time required, of a rotor governor directly connected to the and the fact that most parameters (turbine enginedetects the displacement of the cam using a temperature, fan speed, altitude) were available in combination of springs and a device to measure fuel electronic form therefore rendered digital electronics pressure. With advances in steam engine technology, more suitable for control systems [5]. In order to a simple mechanism for RPM detection was already introduce redundancy and enable greater safety in prevalent and was employed in jet engines, with operation, certain electric supervisory devices and changes in its material composition and additional limiter controls were introduced. The subsequent miniaturization. Furthermore, a three-dimensional cam was developed with a notched surface that Lewis Research
Details
-
File Typepdf
-
Upload Time-
-
Content LanguagesEnglish
-
Upload UserAnonymous/Not logged-in
-
File Pages6 Page
-
File Size-