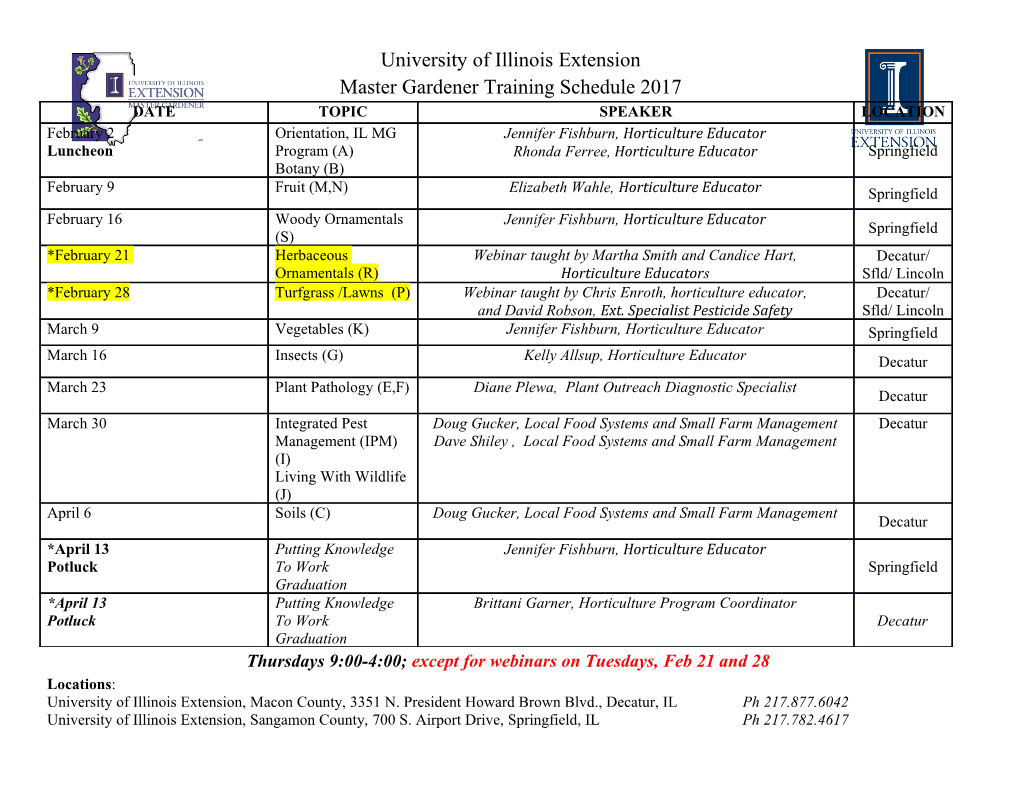
Materials – Wrought materials production Table of contents 5 Wrought materials production .................................................................................................. 2 5.1 What to find in this section ............................................................................................... 2 5.2 Automotive sheet .............................................................................................................. 3 5.2.1 Automotive sheet production – Rolled material with special property profile ................................................................... 3 5.2.2 Automotive sheet production – Process steps influence microstructure and properties .................................................. 4 5.2.3 From ingot to strip and panel .................................................................................... 6 5.2.4 Special sheet surfaces ............................................................................................ 13 5.3 Extrusion ........................................................................................................................ 22 5.3.1 Automotive extrusions – Process steps and microstructure ................................... 22 5.3.2 Casting of extrusion log .......................................................................................... 24 5.3.3 Cutting logs to billets / Preheating to extrusion temperature / Extrusion ................ 25 5.3.4 Extrusion presses ................................................................................................... 26 5.3.5 Factors influencing on quality of extrusions ............................................................ 27 5.3.6 Die tooling ............................................................................................................... 28 5.3.7 Extrusion with mandrel ........................................................................................... 30 5.3.8 Post extrusion operations ....................................................................................... 31 5.4 Forging ........................................................................................................................... 32 5.4.1 Automotive die forging – Characteristics of the closed-die forging process ........... 32 5.4.2 Automotive die forging – Process and microstructure ............................................ 34 5.4.3 Automotive die forging – Composition and microstructure ..................................... 35 5.4.4 Automotive die forging – Forging stock .................................................................. 36 5.4.5 Automotive die forging – Forging temperatures and rate of deformation ............... 38 5.4.6 Automotive die forging – Forging presses .............................................................. 40 5.4.7 Automotive die forging – Die tooling ....................................................................... 41 5.4.8 Automotive die forging – Economic aspects ........................................................... 43 5.5 Impact extrusion ............................................................................................................. 45 Version 2002 © European Aluminium Association ([email protected]) 1 5 Wrought materials production See also: AAM – Materials – 6 Special materials production > Longitudinally welded tubes AAM – Materials – 6 Special materials production > Metal Matrix Composites AAM – Materials – 6 Special materials production > Laminates / Sandwiches AAM – Materials – 6 Special materials production > Foam AAM – Materials – 6 Special materials production > Tailored blanks 5.1 What to find in this section This section describes the processes for production of major semi-finished automotive products, i.e. for sheet, extrusions, forgings and impact extrusions. (Special materials' production, such as welded tubes, MMC, Laminates, Foam and Tailored Blanks, are treated in a subsequent section.) The purpose is to illustrate the production processes, which lead to special qualities and shapes and to a variety of surface finishes, as background for material selection and fabrication. When specifying or designing such products, it is important - for economic reasons - to consider the characteristics of the production processes. Semi-finished automotive products are specialty materials with closely controlled properties and tolerances for specific customer requirements and are to be distinguished generally from standard mill products and stock materials for general purpose applications. Right figure: Run-out table of an extrusion press with cooling/quenching equipment for in-line heat treatment of extrusions. Left figure: Coiling of hot rolled strip. Version 2002 © European Aluminium Association ([email protected]) 2 5.2 Automotive sheet 5.2.1 Automotive sheet production – Rolled material with special property profile Literature: Furrer, P. and Bloeck, M.: Aluminium-Karosseriebleche. Landsber: Verl. Moderne Industrie, 2001, (Die Bibliothek der Technik; Bd. 220) ISBN 3-478-93250-5 Automotive sheet material is a specialty material In order to comply with the requirements of the car manufacturer aluminium automotive sheet materials have been developed with special property profiles, which are the result of combined characteristics of the base material and the sheet surface (s. figure below). Source: M. Bloeck and G. Marshall, Alcan Sheet production comprises several discrete steps: ingot casting, hot rolling, cold rolling and finishing (heat treatment, surface preparation and/or cutting). Version 2002 © European Aluminium Association ([email protected]) 3 5.2.2 Automotive sheet production – Process steps influence microstructure and properties Base material properties are directly related to microstructure which is strictly controlled by alloy composition and the processing parameters. Examples of key processing parameters are given in the accompanying table. The sheet surface characteristics have a significant influence on: friction behaviour, i.e. during ◦ transport of the panels, ◦ forming, ◦ mechanical joining, joining performance, e.g. during welding, bonding, adhesion of coatings and lacquers, optical appearance after lacquering, corrosion resistance Source: M. Bloeck and G. Marshall, Alcan Evolution of Microstructure The essential microstructural features developing during the complete chain of thermo- mechanical processing steps from ingot casting through ingot homogenisation, hot rolling, cold rolling and intermediate or final annealing are grain structure constituent phase particles precipitations and textures. Version 2002 © European Aluminium Association ([email protected]) 4 Typical process chain for rolled products Source: L. Löchte, VAW aluminium AG Bonn Version 2002 © European Aluminium Association ([email protected]) 5 5.2.3 From ingot to strip and panel Cast House Raw metal for production of ingots: Mixture of primary aluminium and sorted fabrication scrap or secondary aluminium gained by melting of scrap from recycled products. Casting: Alloying elements are added (when needed) to the melt to attain precise composition control. The molten Aluminium is filtered and degassed immediately before casting. DC casting stands for Direct Chill casting. For example an aluminium smelter or cast house will produce between 100-600 kt of sheet ingots annually with an individual ingot weighing up to 27 t. A casting centre will cast up to five ingots in a single operation Casting of aluminium ingots Source: M. Bloeck, Alcan, 87331 From ingot to rolling slab The cast ingots are typical sawn at head and foot to remove head skrinkage and start of cast foot region. The cast surface imperfections and metallurgical inhomogeneities are also removed by scalping the rolling faces to a predefined depth that depends on alloy and product requirements. Strip casting It is also possible to produce a coil of aluminium by a semi-continuous route using a block, belt or roll caster. The semi-fabricated product is a coil in the 3 to 10 mm range which would subsequently be cold rolled to final gauge. Casting a thin strip product can have economic advantages but there are metallurgical drawbacks associated with rolling a cast surface, lack of homogenisation and chemical segregation linked to some alloys. For these reasons continuous casters have yet not been adopted for automotive sheet. Version 2002 © European Aluminium Association ([email protected]) 6 Rolling ingots are retracted from casting pit Source: M. Bloeck, Alcan, 87333 Version 2002 © European Aluminium Association ([email protected]) 7 Hot Rolling Preheating: the slabs are preheated at 480-580oC for several hours for homogenization of the microstructure. Hot rolling: the preheated slabs are hot rolled using exactly defined pass reductions and controlled temperature conditions. In most rolling plants hot rolling is done on a reversing mill (up to ~ 25 mm strip gauge) followed by rolling on a tandem mill. In some rolling plants hot rolling is performed on a reversing mill only. Depending on the hot rolling concept, the gauge of the hot rolled strip can vary between 3-12 mm. The hot rolled strip is hot coiled and cooled down to RT. Cold rolling: The hot rolled strip is cold rolled to final gauge in several passes. Cold deformation leads to an increase of the material strength. Therefore, for some alloys an interanneal is performed to allow further rolling. Hot rolling on a reversing mill Coiling of the hot rolled strip Version 2002 © European Aluminium Association ([email protected])
Details
-
File Typepdf
-
Upload Time-
-
Content LanguagesEnglish
-
Upload UserAnonymous/Not logged-in
-
File Pages45 Page
-
File Size-