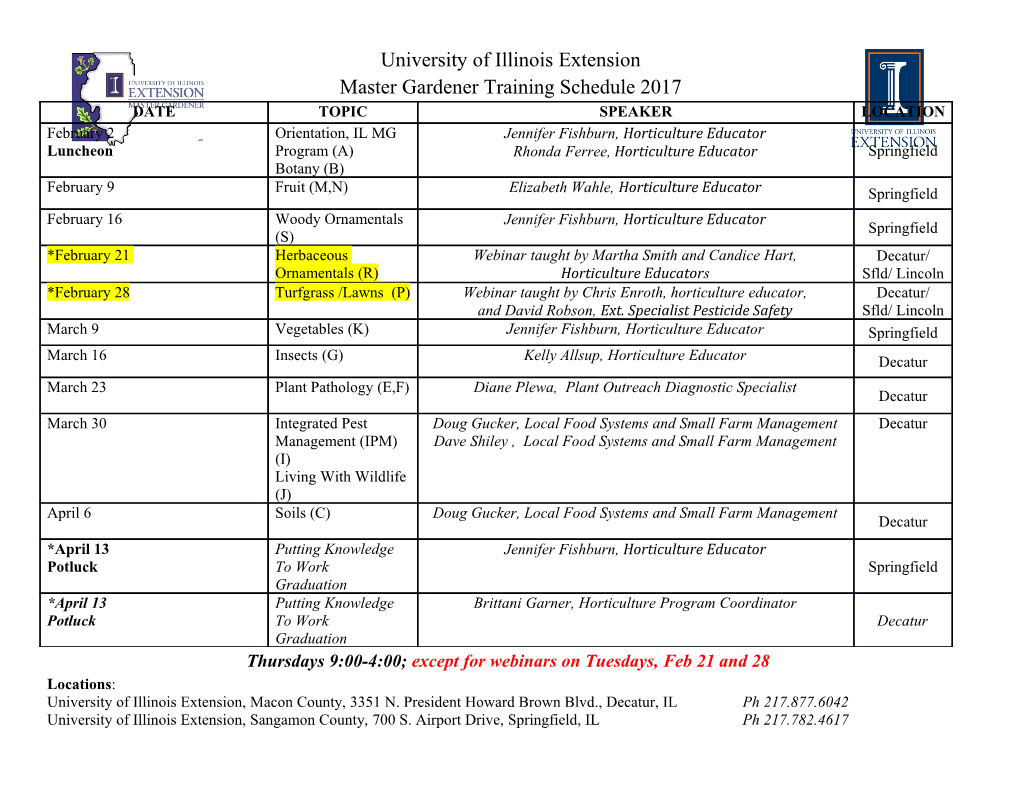
VOLUNTEER RESOURCE INFORMATION ISSUE 3: A FAT BURGUNDY BOTTLE OVEN MAY 2020 Source: www.stokemuseums.org.uk › pmag › collections THE BOTTLE OVEN Bottle oven no.1 is the sole surviving kiln of an original seven which saw Middleport Pottery become known as the ‘Seven Oven Works’ and dominated the skyline of this part of The Potteries for around eighty years. Of the original ovens, three large biscuit ovens were built in a row in the relatively spacious yard between the biscuit range and glost range while a further four glost ovens were located in the now built- over yard between the glost range and the archive/warehouse range. A pdf of the report above is The positioning of these kilns, making them integral to the process available on flow of the works, was one of the key innovations of A.R. Wood’s request original plan. Each of the ovens at Middleport was of a type which can be described as an updraught oven. These consist of a bottle-shaped brick structure called the hovel* within which was an inner chamber with a domed roof, in which the leather hard green ware was placed within saggars. *The hovel at bottle oven no.1 is of the fat burgundy bottle type (Dobraszczyc 1984, 7). Fires were lit in firemouth openings at the foot of the oven by the fireman, from which flues led to bags, small firebrick chimneys which directed flames from the fire below into the oven and protected the saggars nearby. Once the smoking period, in which all of the water was baked out of the clay, was over the entrance, known as the clammins, was bricked up. For the next two days the heat rose up through the saggars, attaining temperatures of around 1100°C, and out of the top of the oven. The temperature was manipulated by controlling the draught, by either opening or closing dampers in the crown of the oven. Once firing was complete, the clammins was taken down and the oven emptied (‘drawn’). At Middleport, the biscuit fired ware was then moved on to the middle, glost and Port Street ranges for decorating and glazing. The coal-fired ovens at Middleport Pottery were some of the last to be fired in The Potteries. After passing of the Clean Air Acts in the mid-1950s most pottery works were given seven years to move on to gas and electric kilns. The eastern-most glost kiln was demolished in 1949 to allow for the introduction of the Allied gas-fired tunnel kiln within the ground floor of the middle range. The remaining glost ovens and the western two biscuit ovens were demolished in 1965 with biscuit oven No.1 (to the east) surviving due only to its being integral to the structure of the adjacent middle range. Despite this, Burgess & Leigh did later apply for listed building consent to demolish bottle oven no. 1, however their application was turned down by Stoke-on-Trent Council, who stated that the oven was ‘one of the finest examples of the few potters updraught bottle kilns remaining in the city; a striking townscape feature which is clearly visible from the principal road, rail and waterway approaches to the city; it has considerable archaeological value as the most important component in a group of nineteenth century industrial buildings’ (op cit. Princes Regeneration Trust 2012, 32). The bottle oven stands redundant but in reasonable condition. Source: Middleport Pottery, Burslem, Stoke-on-Trent. Historic Building Recording Ironbridge Archaeology IAS No. 324 – Final Report pp 59-60/356 ************************************ Industrial Relations in the Pottery Industry ‘Good from Oven’ A contentious issue that plagued industrial relations in the pottery industry throughout the 19Cth was the payment by ‘good from oven’, whereby the central pieceworkers such as throwers, turners & pressers were only paid for their work if the wares they had shaped emerged as firsts from firing, a stage of the process over which they had no control. In 1872 Mintons took the lead by abandoning ‘good from oven’ and instituted the self-explanatory ‘good from hand’ As a result of this and other actions the firm was not involved in the disputes of either 1880 or 1892. The issue was again the source of dispute in the industry in 1908 and it was not finally abolished until 1919. Source: The Potteries, c. 1850-1900. - PhD submission by A D Popp Sheffield Hallam University 1997 ************************************ A Report by H M Factory Inspectorate in 1959 INDUSTRIAL HEALTH A SURVEY OF THE POTTERY INDUSTRY OF STOKE-ON-TRENT Pottery has been made in North Staffordshire for at least 600 years. The industry was founded here on local clays and developed because there were large supplies of coal in the area suitable for firing pottery. Much of the early ware was unglazed, but some was dusted with powdered lead ore which when fired produced a rich yellowish glaze; other ware was salt-glazed. During the 18th century a better quality, or whiter, ware was developed by the introduction of ball clay from Devon and the use of calcined flint, and by about 1770 cream-coloured pottery was being made from a body which contained the same materials as the earthenware body of today—ball clay, china clay, flint and Cornish stone—a body which, because of its high content of free silica, has caused so much ill- health to so many people. The disease now known as silicosis or pneumoconiosis was 100 years ago known as potters rot. Pneumoconiosis means fibrosis of the lungs due to silica dust, asbestos dust or other dust and includes the condition of the lungs known as dust reticulation. It is now the greatest single health hazard affecting potters. Many people who have not visited the Potteries link the area with the Black Country; this, however, is separated from the Potteries by many miles of open country and the extensive Cannock Chase. They think of the Potteries as an area of bottle-ovens and factory chimneys belching out black smoke day and night and the whole area constantly bathed in gloom and fog. Today the atmospheric pollution as judged by ordinary observation is probably no worse and no better than that of any other industrial area of a similar size. The amount of smoke arising from pottery firing has been progressively reduced by the continuing replacement of the coal- firing bottle-oven by electric or gas-fired intermittent and tunnel ovens. During the period of the survey there were 572 coal-fired ovens orPdf kilns available still in use, but the industry estimates that at the present time it is on request burning at least half-a-million tons of raw coal a year less than it was before the war, and over 1,500 bottle-ovens have been replaced by smokeless ovens and kilns. ************************************ THE CLEAN AIR ACT 1956 When The Clean Air Act became law in 1956 pottery manufacturers were given a seven year period to convert from coal to other types of fuels viz gas, electric & oil. As a result a many of the decommissioned bottle kilns were demolished, many to provide space on the factory sites for the new kilns to be introduced. Demolition of a bottle oven at Sampson Bridgwood's Anchor Pottery in Goddard Street in the East Vale area of Longton October 1962 These are hovel ovens where the oven stands in the centre of a separate circular “hovel”, which is really a chimney to create an updraught. In the photograph, most of the hovel has been demolished but the back wall still stands. Intact, the hovel would have been up to 70 feet high. The oven is the circular structure with iron bands (bonts) and fireholes visible. Bonts were iron bands around the oven, strengthening it and preventing warping with the heat. The rounded top part of the oven in the photograph has been demolished. The walls of the ovens could be over 1 foot thick. The Anchor Pottery produced both bone china and earthenware. Today the pottery site is housing. Source: Anchor Pottery Demolition ********************************* How many bottle ovens are left in Stoke-on-Trent? The definitive list is “The National Index Bottle ovens and kilns in UK with upstanding remains” A developing list, compiled by Peter Wakelin, March 2020 Included in the list is the Pomoma Pottery, Lower Street, Newcastle- under-Lyme Relocated to Brampton Museum The base is just right of the main museum building NAME Edited List to show ADDRESS PLACE QTY number of (Relocated to Brampton Bottle Ovens with Pomona Pottery Newcastle, Staffs 2 upstanding remains Museum) in S-o-T from Moorland Pottery Moorland Road, Burslem Stoke-on-Trent 1 The National Index Acme Marls Bournes Bank, Burslem Stoke-on-Trent 3 2020 Furlong Mills Furlong Lane, Burslem Stoke-on-Trent 2 Full pdf available on request Price and Kensington Top Bridge Works, Longport Stoke-on-Trent 1 Middleport Pottery Port St, Middleport Stoke-on-Trent 1 Middleport Mill Milvale St, Burslem Stoke-on-Trent 1 Oliver's Mill (1x Single & 1x Double Newport Lane, Burslem Stoke-on-Trent 2 chamber) March 2020 Moorcroft Sandbach Rd, Cobridge Stoke-on-Trent 1 Falcon Pottery, Weatherbys Town Rd, Hanley Stoke-on-Trent 1 [Updraught] Falcon Pottery, Weatherbys Town Rd, Hanley Stoke-on-Trent 1 [Muffle] Dudson's Hanover Street, Hanley Stoke-on-Trent 1 Smithfield Pottery Warner St, Hanley Stoke-on-Trent 1 Johnson Brothers Trent Pottery Eastwood Rd, Hanley Stoke-on-Trent 2 Joiners Sq Works, Allied Lichfield St, Hanley Stoke-on-Trent 1 Insulators Etruria Bone Mill, Shirley's Lower Bedford St, Etruria Stoke-on-Trent 1 Cliffe Vale Pottery, Twyfords Shelton New Rd, Stoke Stoke-on-Trent 2 Spode Works Church St, Stoke Stoke-on-Trent 1 Dolby Mill Lyton St, Stoke Stoke-on-Trent 1 Falcon Works Stoke Sturgess Street,
Details
-
File Typepdf
-
Upload Time-
-
Content LanguagesEnglish
-
Upload UserAnonymous/Not logged-in
-
File Pages11 Page
-
File Size-