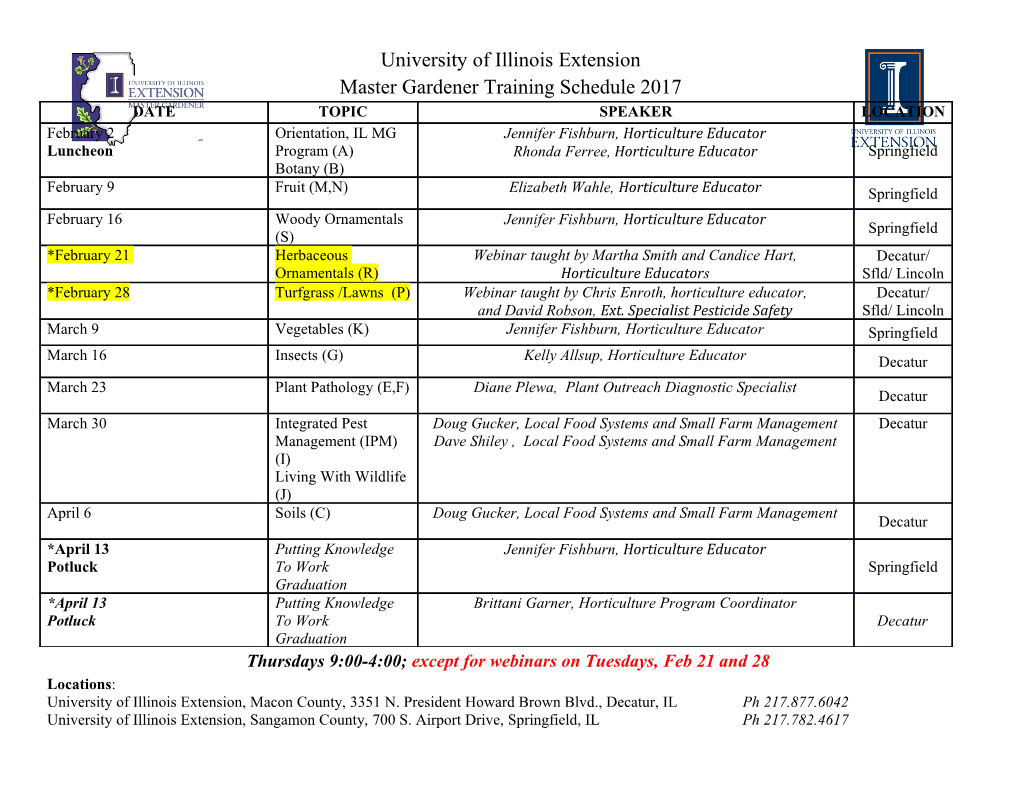
Tire and force distribution modeling and validation for wheel loader applications John Spencer and Bernhard Wullt Mechanical Engineering, master's level 2017 Luleå University of Technology Department of Engineering Sciences and Mathematics Acknowledgements We would like to thank our supervisors, Andre Fernandez and David Berggren, at Volvo CE as well as Jan-Olov Aidanp¨a¨aat LTU. Your help and support during the thesis work has been of high importance for our work. We would also like to thank Lennart Skogh and his test department, who helped us out a lot with the measurements and the testing. Last but not least, we would like to give a big thank you to Kausihan Selvam and Auayporn Elfving at Volvo CE for giving so freely of their time. You have been a great help to us! Thanks! Abstract This thesis describes the development of a machine force distribution estimator and the calibration of tire models for wheel loader applications. Forces generated in the contact patch between the tires and the ground are crucial for under- standing and controlling machine dynamics. When it's not possible to directly measure these contact patch forces they are estimated from other sensor data. Validated models of the contact patch forces are also used in machine dynamics simulations and are very relevant to model based development. Vehicle dynamics is of crucial importance to the automotive industry. In contrast the modeling of these forces has not been very important to the construction equipment industry and as such wheel loaders haven't been studied as much as conventional cars. In order to model the forces in the contact patch, suitable tire models have been studied and calibrated. The tire models have been calibrated by using two different sources, field data and test rig data. Two steady state tire models were chosen for the field data. These were the brush model and the Magic Formula. The resulting fit from the data was not ideal, but this was due to that the given data were of low accuracy. The Magic Formula was used for the test rig data, which gave a good overall fit. The results from the test rig measurements were then used in a transient model, the single contact point model, and the MF-Tyre software. The models were implemented in Simulink and were validated against experimental data. They showed good correspondence, but deviated for some levels of slip. Another important aspect of the wheel loader is the force distribution over the entire machine. Two estimators have been developed, one to estimate the vertical forces on each tire, the normal force estimator and one to calculate the turning behavior due to different force outputs on the tires, the turning torque estimator. The normal force on each tire is information that is important for the tire model, but it can also be used to estimate when the wheel loader risk tipping on its side. The turning torque estimation is useful for control systems to optimize the driving behavior of the machine. Compared against measured data from an actual wheel loader the normal force estimator showed a high accuracy in estimating the individual wheel vertical forces. The turning torque estimator could estimate the behavior of the torque but had problems when estimating the magnitude. Table of Content 1 Introduction 1 1.1 Thesis work . .1 1.1.1 Scope . .2 1.2 Literature review . .3 2 Theory 4 2.1 Tire model: Tire fundamentals . .4 2.1.1 Introduction to tire quantaties . .4 2.1.2 Tire forces and moments . .5 2.2 Tire model: Tire models . .7 2.2.1 The Magic Formula . .7 2.2.2 MFSWIFT . .9 2.2.3 The brush model . 11 2.2.4 Single contact point model . 13 2.3 Tire model: Algorithms for parameter estimation . 13 2.3.1 Differential evolution . 14 2.4 Force distribution: Normal force . 14 2.4.1 Defining the basis for the normal force distribution model . 14 2.4.2 Finding the center of gravity . 15 2.4.3 Shifts in center of gravity . 16 2.4.4 Normal force on each tire . 20 2.4.5 Roll-over . 25 2.4.6 Pile Entry . 25 2.5 Force distribution: Acceleration from wheel sensors . 26 2.6 Force distribution: Turning torque . 27 3 Method 30 3.1 Tire model: Test vehicle . 30 3.2 Field measurments . 30 3.2.1 Tire used for measurements . 30 3.2.2 Measurement systems . 30 3.2.3 Experiments . 32 3.2.4 Complementary field test data . 32 3.3 Tire model: Test rig measurements . 33 3.3.1 Tire used for measurements . 33 3.3.2 Main setup . 33 3.3.3 Pure longitudinal force characteristics . 35 3.3.4 Relaxation length . 36 3.3.5 Validation . 36 3.4 Tire model: Optimization routine for parameter identification of tire models . 36 3.5 Tire model: Parameter and model identification of field measurements . 36 3.5.1 Reference tire model . 37 3.5.2 Magic Formula parameters . 37 3.5.3 Brush model . 38 3.6 Tire model: Data processing of test rig measurements . 38 3.6.1 Processing of force characteristics measurements . 38 3.6.2 Processing of relaxation length measurements . 38 3.7 Tire model: Parameter and model identification of test rig measurements . 39 3.8 Tire model: Model validation of test rig measurements . 39 4 Results 41 4.1 Tire model: Processed field measurements . 41 4.2 Tire model: Parameter and model identification from field measurements . 41 4.2.1 Magic Formula parameters . 41 4.2.2 Brush model . 44 4.2.3 Comparison of tire models . 46 4.3 Tire model: Parameter and model identification from test rig measurements . 47 4.3.1 Magic Formula parameters for nominal load and inflation pressure . 47 4.3.2 Magic Formula parameters for variation of load and nominal inflation pres- sure ........................................ 48 4.3.3 Comparison of resulting fitted curves for variation of loads . 50 4.3.4 Magic Formula parameters for nominal load and variation of inflation pres- sure ........................................ 51 4.3.5 Comparison of resulting fitted curves for variation of inflation pressures . 52 4.3.6 Relaxation length . 53 4.4 Tire model: Model validation of models from test rig measurements . 53 4.5 Force distribution: Normal force estimation results . 54 4.5.1 Normal force estimator vs Simulation . 54 4.5.2 Transient torque case . 54 4.5.3 Transient steering angle case . 55 4.5.4 Using the old measurement data data . 56 4.5.5 Using newer complimentary data . 58 4.5.6 Roll over . 60 4.5.7 Pile entry . 61 4.6 Force distribution: Turning torque results . 62 5 Discussion 64 5.1 Tire model: Field measurements . 64 5.2 Tire model: Test rig measurements . 64 5.3 Force distribution: Normal force . 65 5.3.1 Compared against simulation . 65 5.3.2 Compared against the old tests . 65 5.3.3 Compared against the new tests . 65 5.3.4 Roll over . 66 5.3.5 Pile entry . 66 5.4 Force distribution: Turning torque . 66 6 Conclusions 67 6.1 Tire model: Field measurements . 67 6.2 Tire model: Test rig measurements . 67 6.3 Force distribution: Normal force estimation . 68 6.4 Force distribution: Turning torque . 68 7 Future work 69 7.1 Tire model . 69 7.2 Force distribution estimator . 69 References 72 Appendices 73 A Tire model: Data processing for field measurements 73 B Tire model: Processed field measurement data 79 C Tire model: Structural properties from field measurements 83 D Tire model: Parameters and bounds for field measurements 84 E Tire model: Parameters and bounds for test rig measurements 85 F Kalman filter 86 Variable list Name Symbol Unit Half contact patch length ac m Longitudinal distance between wheel and COG a m Lateral distance between wheel and COG b m Stiffness factor B - 2 Longitudinal stiffness cpx N/m Shape factor C - Longitudinal slip stiffness CF κ N Lateral slip stiffness CF α N Normalized change in load dfz - Normalized change in inflation pressure dpi - Peak factor D N Slope factor E - Unit vector e - Longitudinal Force Fx N Steady state force Fxss N Lateral Force Fy N Vertical Fore Fz N Nominal load Fzo N a Normal force from asphalt data Fz N g Normal force from gravel data Fz N Gravity constant g m/s2 Weighting function G - Population for differential evolution Gi - Cost function J - Stiffness Kxκ N Moment around the longitudinal axle Mx Nm Moment around the lateral axle My Nm Moment around the vertical axle Mz Nm Mass m kg Curbed mass, L-60 mc kg Bucket mass, L-60 mb kg Gross mass, L-60 mg kg Added mass, L-60 ml kg Mass of tire mt kg Revolutions per second of cardan shaft ncs rps Inflation pressure of back tire pb bar Pressure in piston pc bar Inflation pressure of front tire pf bar Inflation pressure tire pi bar Nominal inflation pressure pio bar Longitudinal parameters for shape factor PCx - Longitudinal parameters for peak factor PDx - Longitudinal parameters for slope factor PEx - Longitudinal parameters for stiffness factor PKx - Longitudinal parameters for inflation pressure PP x - Longitudinal parameters for horizontal offset PHx - Longitudinal parameters for vertical offset PV x - Loaded radius r m Unloaded radius rf m Rotation matrix R - Horizontal factor SH - Vertical factor SV - Slip point S - Longitudinal deflection u m Velocity v m/s Speed of wheel V m/s m/s Slip speed Vs m/s Linear speed of rolling Vr m/s Max speed for L-60 Vmax m/s Velocity cylinder Vcyl km/h Velocity vector V m/s Tire contact patch width w m Wheel position wp m Longitudinal position x m Longitudinal position of center of mass Xcog m Lateral position y m Lateral position of center of mass Ycog m Measured value in cost function Ymeasured N Model output in cost function Ymodel N Vertical position z m Vertical position of center of mass Zcog m Side-slip angle α rad Camber angle of tire γ rad Steering angle δ deg Longitudinal composite function θx - Pitch θ deg Longitudinal slip κ - Location of peak longitudinal force κm - Transient longitudinal slip κ0 - Friction coefficient, asphalt.
Details
-
File Typepdf
-
Upload Time-
-
Content LanguagesEnglish
-
Upload UserAnonymous/Not logged-in
-
File Pages96 Page
-
File Size-