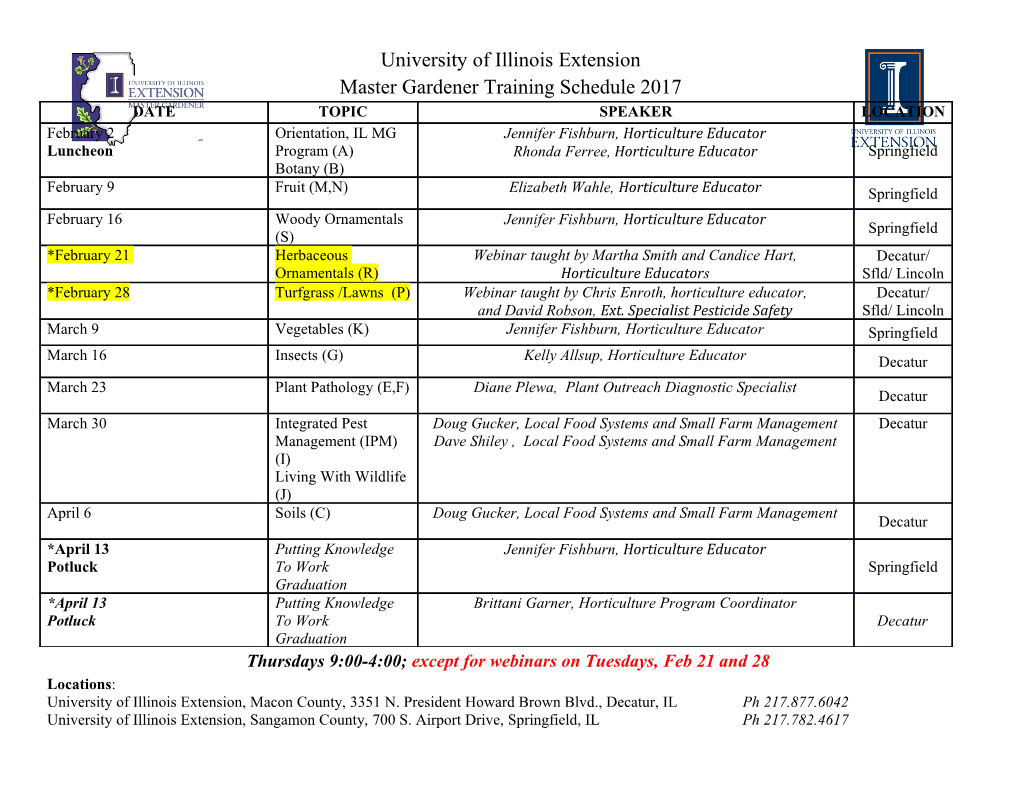
International Scholarly Research Network ISRN Materials Science Volume 2012, Article ID 894072, 5 pages doi:10.5402/2012/894072 Research Article Enhanced Size-Dependent Piezoelectricity in Nanostructured TiO2 Films V. Dallacasa Department of Computer Science, University of Verona, Strada Le Grazie, 15, 37134 Verona, Italy Correspondence should be addressed to V. Dallacasa, [email protected] Received 25 January 2012; Accepted 16 February 2012 Academic Editors: Y. Masuda and R. Mota Copyright © 2012 V. Dallacasa. This is an open access article distributed under the Creative Commons Attribution License, which permits unrestricted use, distribution, and reproduction in any medium, provided the original work is properly cited. We have developed a nanogenerator that is driven by mechanical forces to produce continuous direct-current output. The nanogenerator was fabricated with titanium dioxide nanoparticle arrays forming a Schottky barrier with a conducting electrode with a small gap. Under uniaxial mechanical compression, nanogenerators have shown repeatable and consistent electrical outputs with energy-conversion efficiency of order of magnitude at least comparable to similar nanogenerators based on piezoelectric materials. Flexoelectricity due to inhomogeneous strain induced in the nanostructured TiO2 film has been identified as one possible mechanism of the high apparent piezoelectricity in the nanoparticles. The approach presents an adaptable, mobile, and cost-effective technology for harvesting mechanical energy from the environment. At the present stage it offers a potential solution for powering nanodevices. 1. Introduction which is expected at the nanoscale [3–6] for systems which are non-piezoelectric in bulk form. Recently, an approach for converting mechanical energy into electrical energy has been suggested by using piezoelectric zinc oxide (ZnO) nanowire arrays [1, 2]. This technique 2. Generator Design and Fabrication has illustrated the feasibility of utilizing inorganic nanoma- terials with semiconducting and piezoelectric properties for 2.1. Design. The overall layout of the generator is shown nanogenerators. The conversion of energy can be achieved in Figure 1. A sandwich structure is obtained with an array by creating a Schottky junction between ZnO and a metallic of aligned TiO2 nanostructures of films between two con- corrugated zigzag electrode which realizes a rectifying con- ducting ITO/glass electrodes. The ITO coating enhanced the tact. Results have been obtained with ultrasound waves with conductivity of the electrodes and at the same time created typical output powers P ∼ 1pW/mm2 and sound waves a Schottky contact at the interface of TiO2 and the top with typical intensity 100 decibels which generate electricity electrode. in the order of 1–50 mV. It is believed that various novel applications including devices for the recharging of mobile 2.2. Fabrication Process. The device was fabricated by the phones, the operation of micro and nanodevices, and for the deposition of a nanostructured TiO2 film on a ITO/glass energy storage in batteries and capacitors become possible if substrate that forms an electrode. A colloidal paste was pre- prototype devices can be optimized to enhance their power pared by starting from nanostructured commercial powders input. It has been estimated that the performance can be (Degussa) [7]. To optimize the separation of TiO2 clusters, improved by two-three orders of magnitude [2]. mechanical machining in aqueous phase, in organic phase, In this paper we report results of TiO2-based nanogen- or both and/or sonication of a concentrated emulsion of erators operated under static mechanical forces. The output TiO2 was used. Such emulsion was then applied to the power of such nanogenerators can be attributed to piezoelec- ITO/glass substrates (Optical Filters Ltd., England). The tricity in the TiO2 nanoparticles due to the flexoelectric effect deposition was achieved by a dr. blade or spray deposition 2 ISRN Materials Science Top ITO electrode (nm) 250 200 C A 150 D A TiO2 layer 100 BB A 50 0 3 ITO electrode 2 (µ m ) 1 3 3.5 0 1.5 2 2.5 Negative charge 0 0.5 1 Positive charge (µ m ) Figure 1: Setup of the generator. Nanoparticles are schematically Figure 2: AFM scan of TiO2 films at the micron scale. Nanoparticles described by cusps that can be bended/compressed by the top are schematically described by cusps. electrode. method. To optimize the homogeneity of the film structure and its conductivity, a sintering procedure was used by heating the devices overnight at a temperature T = 550◦C. With this technique, films with typical thickness 10–20 μm (nm) are obtained. 30 Detailed optical microscope inspection indicate that the 15 6 5 final TiO2 films present a uniform distribution with tightly 0 4 sinterized grains. 7 AFM microscopy indicates that at the μm scale the films 6 3 5 (µ m ) are constituted by a disordered array in the xy plane with 4 2 3 cusps (Figure 2). At larger resolution they exhibit a nanomet- µ 2 1 ( m ) 1 ric structure with nanocrystals having comparable dimen- 0 0 sion ∼30 nm within the xy plane and in the z-direction, if 12 −2 they were distributed compactly, a surface density 10 cm Figure 3: AFM scan of ITO conducting films on glass. A on the average would result. nanometric structure is apparent. A similar nanostructure is revealed for the ITO electrode, with slightly smaller density 1010 cm−2 and diameter and height 100 nm and 5 nm, respectively (Figure 3). Each of the structures appears as aligned nanocrystals properties [1]. Under external stress by the top electrode, distributed irregularly in size and orientation strongly resem- a strain field is created in the nanoparticles. This results in bling the configuration shown in Figure 1. an electric field along the z-direction inside the nanoparticle The top electrode was an ITO/glass identical to the and on its surface through the piezoelectric effect. Under substrate and completed the sandwiched structure. compression/dilation, the electric potential distribution is × 2 Typical dimensions of the devices are or order 5 5cm . approximately between V−(V+) and V+ (V−) towards the The commercial ITO/glass substrates and top electrodes top electrode. (Optical Filters Ltd., England) have typical surface resistance The potential is created by the relative displacement of 20 Ω and a resistivity ρ = 20·10−4 Ωcm, such values being the Ti cations with respect to the O2 anions in the crystal compatible with those reported in the literature [8]. structure; these ionic charges cannot freely move and When used as the substrate for deposition of the oxide, cannot recombine without releasing the strain. The potential the ITO structure acts as a template to the arrangement of difference is maintained as long as the deformation is in place the oxide on it. Good adhesion is obtained for TiO2 films and no foreign free charges (such as from the ITO contact) indicating a good crystal structure matching. are injected. From the other hand, when ITO is used as the top The positive (negative) voltage created by the charges acts electrode, its nanometric array structure is penetrated on as an applied bias on the top electrode leading to polarization contact by the smaller TiO2 array leading to an optimized of the Schottky diode at the interface and passage of contact and good mechanical interaction with the film. current through the barrier. The current is the result of ΔV driven flow of electrons between the electrode and the 3. The Operating Principle semiconductor TiO2. The flow of the free electrons through the nanoparticle will neutralize the ionic charges distributed The physical principle for creating charges on the nanopar- in the volume and on the surface of the nanoparticles and ticles is a coupling of piezoelectric and semiconducting thus reduce the magnitudes of the potentials V+ and V−. ISRN Materials Science 3 4. Measuring System 02468 0.68 0.68 When the top electrode has a configuration as shown in Figure 1, by scanning the electrode back and forth, we can 0.64 0.64 reproduce the processes discussed above. Under uniaxial 0.6 0.6 stress, the electrode will exert both vertical and lateral 0.56 0.56 forces on the nanoparticles, and there will be generation (V) V 0.52 0.52 of electricity. During the scan nanoparticles may either be Δ bent on making contact with the electrode (A- and D-type 0.48 0.48 in Figure 1) or contact the electrode without being bent (B- 0.44 0.44 type) or remain isolated without any contact (C-type). The B nanoparticles constitute a parallel resistance of the device; 0.4 0.4 the C nanoparticles are an infinite resistance not entering in 0246 the process. ΔF (N) The ITO electrode in contact with the TiO2 array was Exp manipulated by a probe station. Pressure was applied on Linear fit the sandwich through a calibrated force gauge (Lutron Electronics) of capacity 49 N. The voltage and resistance have Figure 4: Induced voltage change versus applied force (static). been measured by an high-impedance voltmeter (Kitley). A typical device configuration was studied by positioning 0246 the ITO electrode on the nanostructure, and applying uniax- 5.45 5.45 ial compression stress the spacing was controlled to obtain a 5.4 5.4 reasonable contact by the monitoring of the resistance of the Y = Yo + Ro∗exp(−ΔF/Fo) R2 = . junction. The pressing head of the gauge was of cylindrical 5.35 0 99796 5.35 form of diameter d = 5 mm. In order to distribute the Yo = 5.10 ±00. 1 4 ) Ro = 0.29 ±00. 1 5 force over the whole junction, a rigid layer is interposed Ω 5.3 5.3 6 Fo = 1.65 ±0.259 between the head and the top electrode. The actual area of (10 5.25 5.25 the junction which is compressed is estimated not larger than R 1cm2, slightly larger than the head dimension due to the 5.2 5.2 lateral propagation of the applied force but smaller than the 5.15 5.15 area of the whole device.
Details
-
File Typepdf
-
Upload Time-
-
Content LanguagesEnglish
-
Upload UserAnonymous/Not logged-in
-
File Pages6 Page
-
File Size-