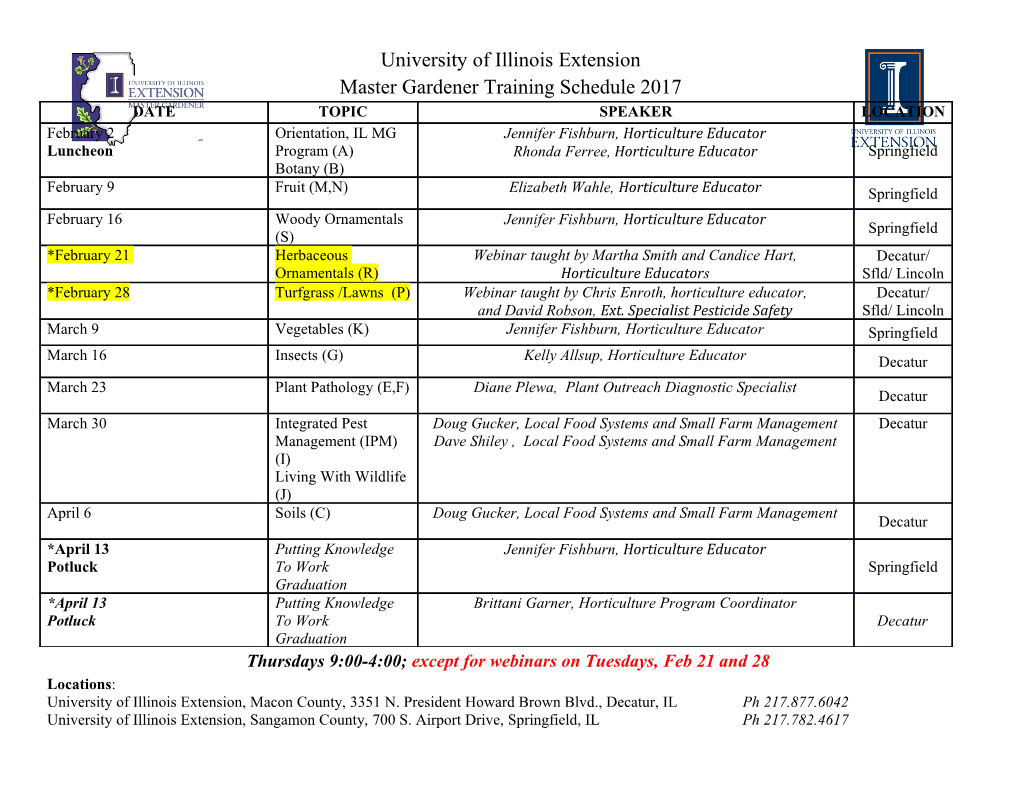
EM FBT-97/1 SE9707435 RECEIVED SEP 2 9 Wff © STI The formation of nitrogen compounds at gasification conditions, with and without internal catalysts E Bjorkman C Larsson MASTER OF THS oocvmn m mam® 29-04 NUTEK, 1 17 86 Stockholm, Tel 08-744 95 00 (Fran 1 november 1992 nytt nummer: 08-681 91 00) RaDDorterna kan bestallas fran Studsviksbiblioteket, 61 1 82 Nykopinq. Tel 0155-22 10 90, 22 10 00, Fax 0155-26 30 44 DISCLAIMER Portions of this document may be illegible in electronic image products. Images are produced from the best available original document. 1997-05-20 Narings- och teknikutvecklingsverket Titel: The formation of nitrogen compounds at gasification conditions, with and without internal catalysts Forfattare: Bjdrkman, E. and Larsson, C. TPS Termiska Processer AB, 611 82 Nykoping RAPPORT INOM OMRADET FORBRANNING/FORGASNING Rapportnummer: FBT-97/1 Projektledare: Eva Bjorkman Projektnummer: A5551-1 (3) Projekthandlaggare Rolf Ingman pa NUTEK: Postadress Besoksadress Telefon Fax Internet e-post 117 86 Stockholm Liljeholmsvagen 32 08-681 91 00 08-19 68 26 http://www.nutek.se [email protected] TPS Termiska Processer AB TPS-96/48 Bjdrkman, E. Larsson, C. 1996-10-28 THE FORMATION OF NITROGEN COMPOUNDS AT GASIFICATION CONDITIONS, WITH AND WITHOUT INTERNAL CATALYSTS SUMMARY The objective of the project is to substantially decrease the emissions of nitrogen oxides from biomass IGCC by minimising the conversion of fuel nitrogen to ammonia and hydrogen cyanide in the gasification process. To reach the objective, the influence from different parameters on the formation of ammonia and hydrogen cyanide from fuel nitrogen has been studied. The parameters studied are the bed material, different functional forms for the nitrogen and the oxygen concentration. The results so far indicate that it is possible by simple methods, to influence the formation of NH3 and HCN by for example modifying the bed material, but that the functional form of the nitrogen is of minor importance. Approved by: TPS Termiska Processer AB TPS-96/48 Bjdrkman, E. Larsson.C. 1996-10-28 1 BACKGROUND The dominating nitrogen compounds that can be found in the fuel gases produced from gasification processes, are ammonia and hydrogen cyanide. These compounds will be converted to nitrogen oxides in the gas turbine combustor in the IGCC process. The NOX emissions after the gas turbine combustor can be reduced by conventional flue gas cleaning, i.e. SCR (Selective Catalytic Reduction), but it is advantageous if this can be avoided. The decomposition of ammonia already in the fuel gas is desirable, but are difficult as most of the active materials are deactivated by the gas. One example are dolomite which decompose ammonia in dry gas but not with steam present (1). It would be preferable if the fuel nitrogen could be converted to N2 directly in the gasifier. Depending on the fuel, the relation between ammonia and hydrogen cyanide differs. Small amounts of hydrogen cyanide produced during low temperature gasification of biomass (2) (compared to coal). The conversion of fuel nitrogen to NH3 has been found to be 17-24% for peat, 10-20 % for bark and 15-17 % for coal, from pyrolysis with slow heating rate. During the same conditions the conversion of fuel nitrogen to HCN was 5- 11% for coal and considerably less from peat and bark (3). Differences in the conversion of fuel nitrogen to HCN and NH3 have generally been explained in terms of nitrogen functionality (4,5). HCN is expected to be the principal nitrogen-containing pyrolysis product when the tuel-N is present in pyridinic or pyrrolic structures (aromatic structures), and NH3 when the fuel-N is present in amino groups. It has also been suggested that as the fuel rank decreases the number of amino groups in the fuel increases and therefore, the conversion of fuel n-^ogen to NH* gams importance. Since the thermal stability of amino groups is lower than that of aromatic nitrogen compounds, NH3 should be released before i iCN, nevertheless experiments have shown that HCN is formed before NH3 (6). Fuel oxygen seems to play an important role in the fuel nitrogen chemistry, especially phenolic OH groups in the structure increases the conversion of nitrogen to NH3(7,8). To catalyse the formation of N2 from fuel nitrogen by internal catalysis is highly desirable. Internal catalysis of solid phase combustion/gasification reactions, mostly on coal, has been studied previously. Some of the more recent results are presented in Table 1. Table 1 Summary of recent literature in the catalytic gasification/combustion field. catalyst fuel process effect mineral matter coal combustion no effect on NO formation (9) FeOOH coal gasification increased solids reactivity (10,11) Ca, K coal gasification increased solids reactivity (12) Ca, Sr, Ba carbon gasification increased solids reactivity (13) FeSCU wood gasification increased solids reactivity (14) Ca synth.char oxidation increased solids reactivity (15) CaO coal oxidation increased solids reactivity (16) mineral matter coal combustion no effect (17) Ni-aluminate biomass pyrolysis fast reaction and catalytic reforming (18) Na coal gasification increased solids reactivity (19) Fe coal pyrolysis reduced NH3 production (20) As can be seen from the table, there is only one report on the effect of internal catalysis on the formation of nitrogen products. In that one, a FeCI3 solution was precipitated on to brown coal. The authors achieved a 50-60% conversion of the fuel nitrogen to N2 when the coal was pyrolysed in helium. Without the iron but else with the same experimental conditions, the conversion to N2 is less than 3%. The explanation given in TPS Termiska Processer AB TPS-96/48 Bjorkman, E. Larsson, C. 1996-10-28 the publication is that at 900°C the iron is completely reduced and present as ultra fine iron particles (20-50 nm), which are responsible for the efficient conversion to nitrogen. The objective of this proposed project is to substantially decrease emissions of nitrogen oxides from biomass IGCC by maximising the conversion of fuel-nitrogen to nitrogen gas in the gasification process. To reach the objective, the influence from different parameters on the formation of ammonia and hydrogen cyanide from fuel nitrogen have been studied. The studied parameters are the bed material, different functional forms for nitrogen, and the oxygen concentration. 2 EXPERIMENTAL The experiments have been performed with a fixed bed quarts reactor placed in a small electric furnace, see Figure 1. To achieve comparable residence times, the same bed height was used in the experiments. The fuel used was a mixture of ethanol and the desired nitrogen source (aniline, pyridine, propyl amine ) on 1:1 volume base. The model fuel was injected into the bed in the reactor with a GC capillary. The fuel feeding rate was 3.5 ml/h. A mixture of N2 and 2% O2 was used as a carrier gas (flow rate 11/min, which gives a air/fuel ratio of approximately 0.2). The product gas was analysed on FTIR, the studied components were NH3, HCN, NO, CO, CO2, CH4, C2H4. The investigated temperature interval was between 750-900°C. The experimental set-up made it possible to study the influence of different variables such as nitrogen source, oxygen concentration, temperature, bed material and air/fuel ratio. bed material • quarts wool »^^ \ .—quarts filter ! ... c r , . , * —to FTIR capillary for fuel injection ' \ electric furnace flow direction Figure 1 The experimental set-up The bed material used was dolomite, quarts sand, AI2O5, Ni-catalyst, olivine sand, CaO and CaO doped with 10 mole-% K, Na or Fe. When doping was required, the doping material was added as a water solution and then dried according to following scheme; Step 1: 10°C/min to 150°C, total time 120 minutes. Step 2: 5°C/min to 300°C, total time 240 minutes. Step 3: 2°C/min to 800°C, total time 240 minutes Step 4: 25°C/min to 25°C, total time 60 minutes then the catalyst was crushed and sieved to fraction 0.7 to 1.4 mm. The CaO based bed materials were used in smaller amounts (1 gr. instead of 9 gr.), but they were mixed with quarts sand to achieve comparable the bed heights. TPS Termiska Processer AB TPS-96/48 Bjdrkman, E. Larsson, C. 1996-10-28 3 RESULTS AND DISCUSSION To get a more understandable report, it has been divided into four different parts, first is the study of the effect of doping a basic bed material, secondly the influence of the nature of the nitrogen, third effect of the oxygen concentration and finally a mapping study of different catalyst. Since there are four different small subchapters we have put together the presentation of the results with the discussion. 3.1 Doping the bed material It is known from previous studies that oxides can have catalytic effects. As an example, MgO is a basic oxide and it can abstract a hydrogen from methane at temperatures around 800°C, which produces a hydrogen radical and a methyl radical (21). In the present work CaO and doped CaO was used as the bed material. With the aim to increase the basicity of the bed material, and we used potassium (K) and sodium (Na) as the doping agent. Furthermore, for comparisons reasons, we also doped CaO with iron (Fe). The results showed that the amount of formed NH3, HCN and NO were not sensitive to the basicity of the bed material but iron had a clear catalytic effect, see Figure 2. CaO CaO + Na ppm 1000 Figure 2 The amount of gaseous nitrogen compounds in fuel gas produced from aniline. Bed material was doped CaO TPS Termiska Processer AB TPS-96/48 Bjorkman, E.
Details
-
File Typepdf
-
Upload Time-
-
Content LanguagesEnglish
-
Upload UserAnonymous/Not logged-in
-
File Pages14 Page
-
File Size-