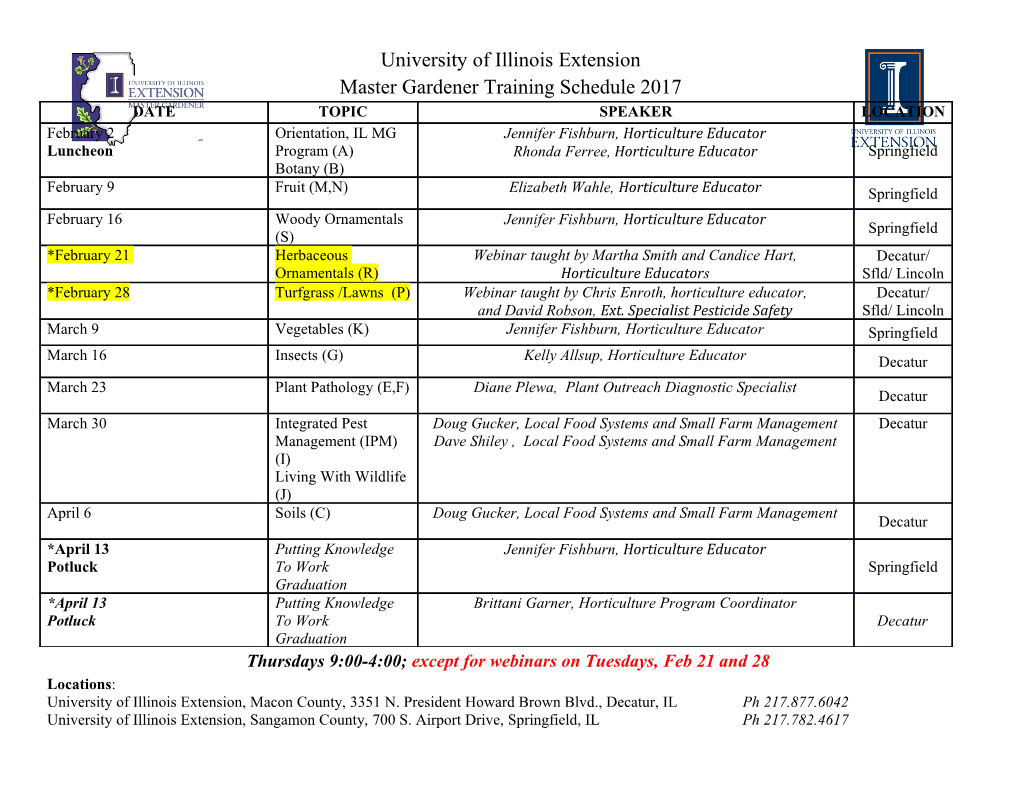
THERMAL MODELING OF A STORAGE CASK SYSTEM: CAPABILITY DEVELOPMENT Prepared for U.S. Nuclear Regulatory Commission Contract NRC–02–02–012 Prepared by P.K. Shukla1 B. Dasgupta1 S. Chocron2 W. Li2 S. Green2 1Center for Nuclear Waste Regulatory Analyses 2Southwest Research Institute® San Antonio, Texas May 2007 ABSTRACT The objective of the numerical simulations documented in this report was to develop a capability to conduct thermal analyses of a cask system loaded with spent nuclear fuel. At the time these analyses began, the U.S. Department of Energy (DOE) surface facility design at the potential high-level waste repository at Yucca Mountain included the option of dry transfer of spent nuclear fuel from transportation casks to the waste packages (DOE, 2005; Bechtel SAIC Company, LLC, 2005). Because the temperature of the fuel and cladding during dry handling operations could affect their long-term performance, CNWRA staff focused on developing a capability to conduct thermal simulations. These numerical simulations were meant to develop staff expertise using complex heat transfer models to review DOE assessment of fuel cladding temperature. As this study progressed, DOE changed its design concept to include handling of spent nuclear fuel in transportation, aging, and disposal canisters (Harrington, 2006). This new design concept could eliminate the exposure of spent nuclear fuel to the atmosphere at the repository surface facilities. However, the basic objective of developing staff expertise for thermal analysis remains valid because evaluation of cladding performance, which depends on thermal history, may be needed during a review of the potential license application. Based on experience gained in this study, appropriate heat transfer models for the transport, aging, and disposal canister can be developed, if needed. Two computational fluid dynamics software packages, FLUENT® (Fluent, Inc., 2005) and FLOW-3D® (Flow Science, Inc., 2005) were evaluated for modeling the cask system. The HI-STAR 100 cask system (Holtec International, 2002) is used as the representative cask system for developing numerical models in this study. At the time of these analyses, the design of a transportation, aging, and disposal canister was not available; however, it was expected that the design of the proposed canister would be analogous to a dry storage cask system such as HI-STAR 100. The results in this report are not a definitive thermal analysis of the fuel assemblies in the cask system; they are used only to understand the simulation tools and mechanisms of heat transfer in a cask system. Three cases were simulated: (i) the closed- cask model, (ii) the open-cask model, and (iii) the fuel-assembly model. The FLUENT code in a two-dimensional axisymmetric mode was used for the first two cases, and the FLOW-3D code was used for thermal analysis of the fuel-assembly model. Results from the closed-cask simulation compared well with those reported by Holtec (Holtec International, 2002), suggesting that the model in FLUENT (Fluent, Inc., 2005) was properly constructed. In the open-cask simulation, the results indicated that internal convection strongly influences heat transfer from fuel assemblies. However, these results remain to be verified by developing a three-dimensional heat transfer model of the HI-STAR 100 cask system. Natural convection was also a significant heat transfer mechanism in the fuel-assembly model, indicating that natural convection must be included in the heat transfer model for determining the thermal history fuel and cladding in a transportation, aging, and disposal canister. References: Bechtel SAIC Company, LLC. “Commercial Spent Nuclear Fuel Handling in Air Study.” 000–30R–MGRO–00700–000–000. Las Vegas, Nevada: Bechtel SAIC Company, LLC. 2005. ii DOE. “Categorization of Event Sequences for License Application.” 000–00C–MGRO–00800–000–00B. Rev. 00B ICN00. Las Vegas, Nevada: Office of Civilian Radioactive Waste Management. 2005. Flow Science, Inc. “FLOW-3D® Version 9.0.” Santa Fe, New Mexico: Flow Science, Inc. 2005. Fluent, Inc. “FLUENT® Version 6.2.16.” Lebanon, New Hampshire: Fluent, Inc. 2005. Harrington, P. “Design and Engineering Update.” Presented to the U.S. Department of Energy, Nuclear Waste Technical Review Board. McLean, Virginia. May 2006. Holtec International. “Final Safety Analysis Report for the HI-STAR 100 Dry Spent Fuel Storage System.” Marlton, New Jersey: Holtec International. 2002. iii CONTENTS Section Page ABSTRACT ................................................................ ii FIGURES..................................................................vi TABLES.................................................................. vii ACKNOWLEDGMENTS .....................................................viii 1 INTRODUCTION .................................................... 1-1 1.1 Background ................................................... 1-1 1.2 Objective..................................................... 1-2 1.3 Scope and Organization of the Report .............................. 1-2 1.4 Assumptions.................................................. 1-3 2 DESCRIPTION OF THE CASK SYSTEM AND MODEL PARAMETERS .......... 2-1 2.1 Geometric Description .......................................... 2-1 2.1.1 Inner Canister ........................................... 2-1 2.1.1.1 Fuel Basket .................................... 2-1 2.1.1.2 Fuel Assembly .................................. 2-2 2.1.2 Overpack............................................... 2-3 2.2 Material Properties ............................................. 2-4 2.2.1 Thermal Conductivities .................................... 2-4 2.2.2 Surface Emissivities ...................................... 2-5 2.2.3 Fluid Properties .......................................... 2-5 2.2.3.1 Thermal Conductivity, Viscosity, and Heat Capacity .... 2-5 2.2.3.2 Density........................................ 2-7 2.3 Concrete Pad ................................................. 2-8 2.4 Thermal Conditions ............................................ 2-8 2.4.1 Heat Load of the Cask .................................... 2-8 2.4.2 Ambient Condition ........................................ 2-8 3 MODELING APPROACH .............................................. 3-1 3.1 Description of Computational Fluid Dynamics Codes ................... 3-1 3.1.1 FLUENT ............................................... 3-1 3.1.2 FLOW-3D .............................................. 3-1 3.2 Model Setup .................................................. 3-2 3.3 Model Boundary Conditions ...................................... 3-2 3.3.1 Closed-Cask Model ....................................... 3-2 3.3.2 Open-Cask Model ........................................ 3-4 3.3.3 Fuel-Assembly Model ..................................... 3-4 3.4 Model Simplifications ........................................... 3-4 3.5 Effective Thermal Conductivity of Fuel Region ........................ 3-4 4 MODEL DESCRIPTION AND RESULTS.................................. 4-1 4.1 Closed-Cask Model ............................................. 4-1 4.1.1 Model Parameters ........................................ 4-2 4.1.2 Model Results ........................................... 4-3 iv CONTENTS (continued) 4.2 Open-Cask Model ............................................. 4-5 4.2.1 Model Parameters ........................................ 4-9 4.2.2 Results ............................................... 4-10 4.3 Fuel-Assembly Model .......................................... 4-14 4.3.1 Model Parameters ....................................... 4-16 4.3.2 Results ............................................... 4-17 5 SUMMARY......................................................... 5-1 6 REFERENCES...................................................... 6-1 v FIGURES Figure Page 2-1 (a) Two-Dimensional and (b) Three-Dimensional View of the HI-STAR 100 Cask System........................................................ 2-2 4-1 (a) Schematic Representation of the Closed-Cask Model Physical Domain and (b) Axisymmetry Model of the Cask System in FLUENT ...................... 4-2 4-2 Temperature Distribution Inside the HI-STAR 100 Casket System (a) Without Insolation and (b) With Insolation ........................................ 4-4 4-3 Normalized Fuel Burnup Rate Along the Length of a Pressurized Water Reactor Fuel Assembly. The Figure Shows the Burnup Data Listed in Table 2.1.8 ........ 4-5 4-4 (a) The Physical Domain of the Open-Cask Model and (b) The Computational Domain of the Open-Cask Model ........................................ 4-6 4-5 A Schematic Representation of an MPC–24 Fuel Basket (Holtec International, 2002) and Its Equivalent Representation in Open-Cask Model ................. 4-7 4-6 The HI-STAR 100 Cask System With Three Concentric Cylindrical Fuel Regions . 4-9 4-7 Temperature Distribution Inside an Open HI-STAR 100 Cask System (a) No Flow Condition (i.e., Only Radiation and Conduction Heat Transfer) ................ 4-10 4-8 Temperature Distribution Inside an Open HI-STAR 100 Cask System (a) K-Epsilon Turbulent Flow Model and (b) K-Omega Turbulent Flow Model ..... 4-11 4-9 Temperature Distribution Inside an Open HI-STAR 100 Cask System With Radiation and Conduction Heat Transfer (a) Without Flow ................... 4-13 4-10 Temperature Distribution Inside an Open HI-STAR 100 Cask System With the (a) K-Epsilon Turbulent Flow Model and (b) K-Omega Turbulent Flow Model ..... 4-13 4-11 Cross Section of the
Details
-
File Typepdf
-
Upload Time-
-
Content LanguagesEnglish
-
Upload UserAnonymous/Not logged-in
-
File Pages48 Page
-
File Size-