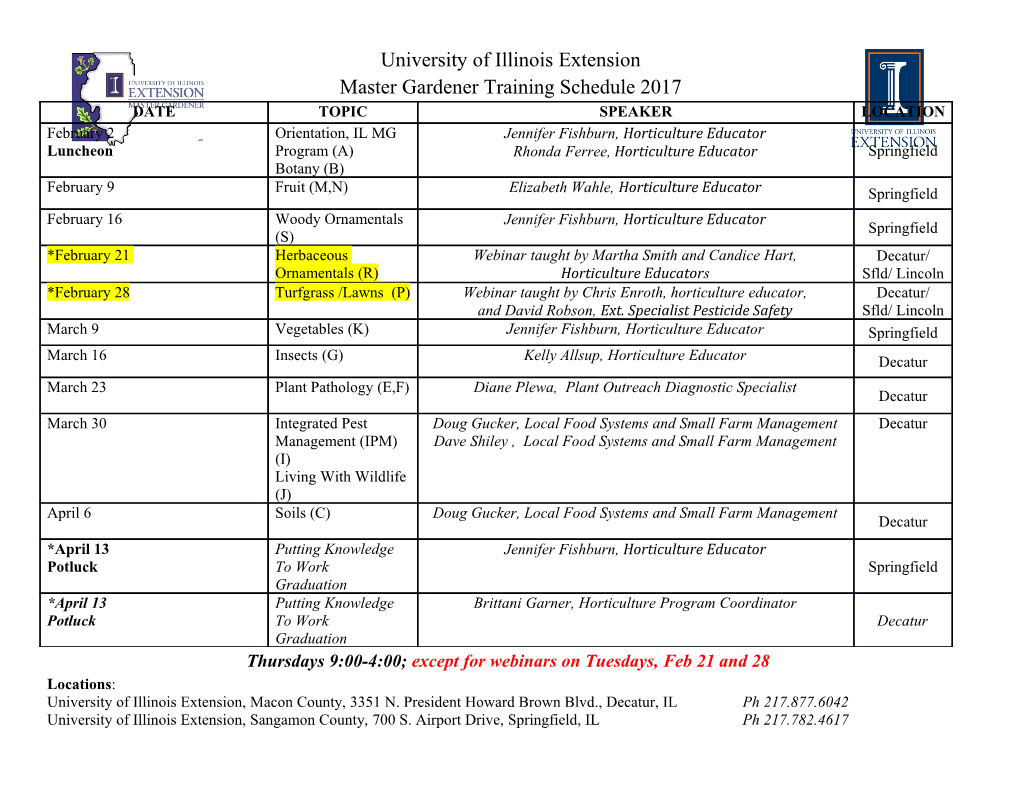
3rd Internat. Congress on Science & Technology of Steelmaking, Charlotte, NC, May 9-12, AIST, Warrendale, PA, 2005, pp. 847-861. Modeling of Continuous-Casting Defects Related to Mold Fluid Flow Brian G. Thomas Department of Mechanical and Industrial Engineering 140 Mech. Engr. Bldg., MC-244, 1206 W. Green St. Univ. of Illinois at Urbana-Champaign Urbana, IL61801, U.S.A. Tel: 217-333-6919, Fax: 217-244-6534 [email protected] Keywords: Continuous Casting, Submerged Entry Nozzle, Mold Flow, Gas Injection, Air Aspiration, Level Fluctuations, Inclusion Entrapment, Meniscus Hooks, Surface Defects, Slag Entrainment, Computational Fluid Dynamics, Models, Solidification ABSTRACT The quality of continuous-cast steel is greatly influenced by fluid flow in the mold, particularly at the meniscus. Recent examples of computational model applications at the University of Illinois are presented to investigate the formation of several different types of defects related to flow phenomena. The amount of gas injection into the tundish nozzle to avoid air aspiration is quantified by modeling. Computational model calculations of superheat transport and surface level fluctuations are presented. Meniscus defects, such as subsurface hooks and their associated inclusions, may form if the superheat contained in the steel is too low, or if top-surface level fluctuations are too large. A thermal stress model has been used to compute the distortion of the meniscus during a level fluctuation. Gas bubbles and inclusion particles may enter the mold with the steel flowing through the submerged nozzle. In addition, mold slag may be entrained from the top surface. These particles may be removed safely into the slag layer, or may become entrapped into the solidifying shell, to form sliver or blister defects in the rolled product. Transient, turbulent flow models have been applied to simulate the transport and entrapment of particles from both of these sources. The insights gained by these modeling efforts aid greatly in the development of processing conditions to avoid the formation of these defects. INTRODUCTION In the continuous casting of steel, the task of the flow system is to transport molten steel at a desired flow rate from the ladle into the mold cavity and to deliver steel to the meniscus area that is neither too cold nor too turbulent. In addition, the flow conditions should minimize exposure to air, avoid the entrainment of slag or other foreign material, aid in the removal of inclusions into the slag layer and encourage uniform solidification. Achieving these somewhat contradictory tasks needs careful optimization. Fluid flow in the mold is controlled by many design parameters and operating conditions. Nozzle geometry is the most important, and includes the bore size, port angle, port opening size, nozzle wall thickness, port shape (round, oval, square), number of ports (bifurcated or multiport), and nozzle bottom design). The flow pattern also depends on parameters which generally cannot be adjusted to accommodate the flow pattern, such as the position of the flow control device (slide gate or stopper rod), nozzle clogging, casting speed, strand width, and strand thickness. Fortunately, other parameters besides nozzle geometry can be adjusted to maintain an optimal flow pattern. These include the injection of argon gas, nozzle submergence depth, and the application of electromagnetic forces. In choosing optimal settings for these parameters, it is important to understand how they all act together to determine the flow characteristics. An increase in casting speed, for example, might be compensated by a simultaneous increase in submergence depth (or electromagnetic force), in order to maintain the same surface flow intensity. Thus, all of the flow-control parameters must be optimized together as a system. In designing the flow system, it is important to consider transients. Sudden changes are the main cause of the flow instabilities which generate surface turbulence and other problems. Because flow parameters are more easily optimized only for steady operation, each of the parameters which affects fluid flow must be carefully controlled. It is especially important to keep nearly constant the liquid steel level in the mold, powder feeding rate (to keep a constant liquid slag layer thickness), casting speed, gas injection rate, slide gate opening, and nozzle position (alignment and submergence). It is also important to choose flow conditions which are resistant to transients and their detrimental effects, although this is difficult to predict. Many quality problems that originate during the continuous casting of steel can be directly attributed to poor control of fluid flow conditions in the mold [1]. In order to optimize these flow design and operation conditions, it is crucially important to understand how defects arise, and how they are affected by changes in the flow pattern affect those defects. This paper summarizes some of these problems and illustrates the use of computational flow models in gaining insight into them, using recent examples developed through the Continuous Casting Consortium at the University of Illinois. Flux DEFECTS RELATED TO FLUID FLOW Submerged Entry Nozzle Rim copper Flux Powder A schematic of the continuous casting process is given in Fig. 1, mold which illustrates some of the phenomena which lead to defects Liquid Flux due to fluid flow in mold region of the process. Jets of molten Resolidified entrainment Flux steel are directed into the liquid by the nozzle ports and traverse nozzle argon Oscillation port across the mold cavity to impinge on the solidifying steel shell bubbles Mark near the narrow faces. Gas bubbles in the jet lower its density, jet providing lift which may alter the flow pattern. The jets Contact impinging against the narrow face may cause shell thinning, and Resistances even breakouts, if the superheat is too high and the interfacial gap Air Gap Molten Steel Pool [2] is excessive . The momentum of the upward flow along the Solidifying Steel narrow faces can raise the meniscus level there, causing a Shell nonlinear profile along the top surface. Where this level is too Nozzle Inclusion high, the infiltration of liquid mold flux into the interfacial gap particles and becomes more difficult, which can lead to nonuniform meniscus Support bubbles Roll heat flux, longitudinal cracks, and other surface defects. Water Ferrostatic Pressure Excessive surface turbulence may cause rapid fluctuations of the Nozzle Spray CL surface level. This can disrupt stable solidification at the Bulging meniscus, leading to deep oscillation marks, surface depressions, Roll surface cracks, and local entrapment of mold slag leading to Roll Contact delamination defects. In addition, high speed flow across the top surface may shear droplets of liquid mold slag into the flow, Fig. 1. Flow Phenomena in the continuous-casting mold region where they may become entrained in the liquid steel. On the other hand, if the surface velocities are insufficient, or if the local superheat contained in the molten steel near the meniscus is too low, then the meniscus may partially freezes to form deep oscillation marks and meniscus “hooks”. These hooks are detrimental because they may entrap particles into the solidifying meniscus. Superheat also affects the nucleation and growth of equiaxed grains, which controls the solidification structure, and defects such as centerline segregation. The transport of solute with the fluid is also of crucial importance to macrosegregation problems, especially towards the final solidification point lower in the strand. In addition to steel and superheat, the jets carry bubbles and inclusion particles into the mold cavity. If the flow pattern enables the particles to reach the top surface, they should be harmlessly removed into the liquid slag layer, so long as the slag is not saturated and the surface tension forces are not excessive. Alternatively, inclusions and bubbles may become entrapped into the solidifying steel shell, where they cause slivers, “pencil-pipe” blisters, and other costly defects. Inclusion particle behavior is complicated by their attachment to the surface of bubbles, which encourages removal, but also creates potentially-dangerous large clusters, which may also be created through collisions. COMPUTATIONAL MODELING OF FLUID FLOW Governing Equations Computational models to simulate fluid flow phenomena in three dimensions generally start by solving the continuity equation and Navier-Stokes equations for incompressible Newtonian fluids, which are based on conserving mass (one equation) and momentum (three equations) at every point in a computational domain. This yields the pressure and velocity components at every point in the domain. The domain is discretized into small computational cells which should exactly match the true shape of the flow region of the process, in this case the nozzle and liquid pool of the continuous casting mold and upper strand. When this is performed with a sufficiently-refined grid to directly capture the details of the transient fluid flow pattern, this is called “direct numerical simulation”. Because this generally leads to excessive execution times, the computational grid is generally coarsened, and a “subgrid model” is B.G. Thomas, 3rd Internat. Congress Sci. & Tech. Steelmaking, Charlotte, NC, May 9-12, AIST, Warrendale, PA, 2005, pp. 847-861. 848 used to account for the effects of turbulence which occur at time and length scales smaller than an individual
Details
-
File Typepdf
-
Upload Time-
-
Content LanguagesEnglish
-
Upload UserAnonymous/Not logged-in
-
File Pages15 Page
-
File Size-