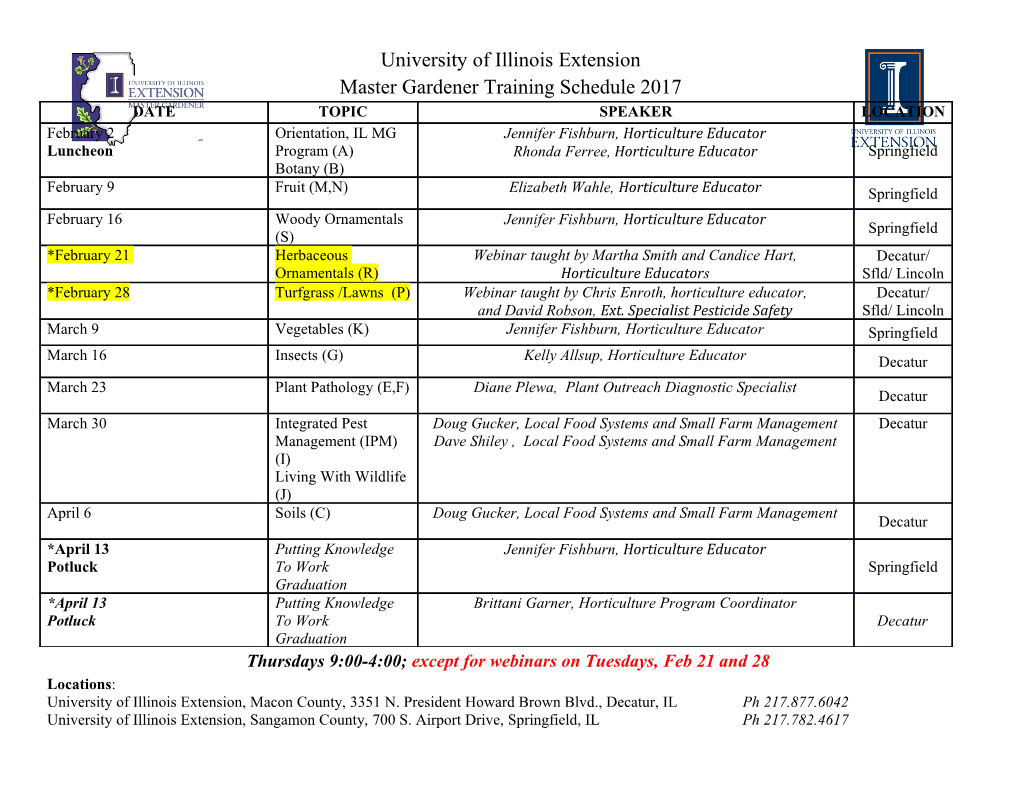
Space Elevators A Study in Cable Design and More Nathaniel Hontz Mohar Kalra [email protected] [email protected] Rachel Lange Niyant Narang [email protected] [email protected] Danny Maguire [email protected] New Jersey Governor’s School of Engineering and Technology 2016 Abstract Conventional rocketry faces many 1. Introduction limitations. Infrequent launches, pollutants dispersing in the atmosphere, and the high 1.1 Goals cost of launches all make more developed access to space difficult. A space elevator This study aims to analyze the can solve these problems with a unique feasibility of building a space elevator by payload delivery system. Simply put, a utilizing technology that is currently space elevator is a long cable that can stretch available. As of today, the space elevator from the surface of the Earth out into space. proposal has remained entirely theoretical. Climbers can ascend this extraordinarily In fact, the basic design has advanced little strong cable for a variety of purposes. This since its initial formal proposal in 2000 [1]. study has calculated the dimensions and This is largely a result of the lack of structure of the entire elevator. One of the materials to construct a real space elevator. key objectives in this paper is to determine a The space elevator design hinges on the tether design constructed of newly- ability of its tether to support itself over tens developed carbon nanotubes and epoxy that of thousands of kilometers in Earth’s orbit, combines strength, efficiency and but as of yet there exist few materials adaptability in the relatively unfriendly capable of realistically fulfilling this environments of space. Furthermore, this requirement. Theoretically, the tether can be study has examined and proposed solutions made of any material, but as the tether’s to many of the common issues associated altitude increases, it would have to widen with the space elevator concept. Lastly, this substantially to support its own weight. As paper encourages further investigation in the such, most studies on space elevators focus development and mass production of carbon on technologies that might exist decades in nanotubes, as well as the economic the future. This study, however, will address feasibility of space elevators in the near the matter of cable construction using future. materials available to engineers today. In order to accomplish this, various cable 1 configurations have been modeled in enable long-distance transfer of energy to SolidWorks, a computer aided design the climbers. The deployment of the elevator software, to test their ability to handle stress. will be a delicate procedure as well. Other In addition, this research seeks to provide complications include weather, atomic solutions to other issues associated with the oxygen corrosion, space debris, satellites, elevator, such as climber propulsion and radiation, and political regulation [1]. cable deployment. 2.2 Assumptions 1.2 Reasons for a Space Elevator For the purposes of this study, it is Everything that can be done with assumed that cable materials can be rockets can be done cheaper and with larger replicated on a large scale with the same payloads using a space elevator [1]. length and strength as have been produced Additionally, many missions that cannot be in laboratories. This paper does not assume accomplished with rocket launches will the existence of any properties that have not become possible with the use of space been experimentally observed. Furthermore, elevators. The environmental impacts of a suitable epoxy for cable construction is launching rockets, including the fuel burned assumed to exist and able to be mass and the engines falling back to Earth, will produced. disappear since space elevators can easily transport cargo and humans without major 2.3 Relevant Physics environmental concerns. Space-based solar panels can provide cheap, clean power to The space elevator remains vertical Earth’s surface. An increase in through a centrifugal “force” that appears to communications and research will arise due act outwards on the cable. In reality, this to the plethora of new satellites that can be force is simply an observation resulting from launched from the elevator. In addition, the inertia of a system. As an object swings space elevators will allow for relatively easy in a circular motion, its velocity is disposal of dangerous nuclear or toxic waste perpendicular to its acceleration, which is in the isolated vacuum of space. Moreover, towards the body that it travels around. In the space elevator can lead to a realistic this type of motion, the “string” that solution to space debris, a growing problem connects the object in motion to the center which poses a serious danger of collision for of the circle it forms remains taut due to the satellites and interference for future inertia resulting from the moving object’s excursions into space. velocity. This is the concept behind the space elevator. By anchoring a base point on 2. Background the equator of Earth, where the tangential velocity on the surface will be the fastest, 2.1 Challenges with Elevator Design the cable that connects the top of the space elevator to the Earth will remain taut due to The greatest challenge of building a its high tangential speed. However, to space elevator is the construction of the long overcome Earth's gravitational pull, the cable required to support the climbers. There centrifugal force must be greater than the are few materials that offer even a gravitational pull on the elevator. This possibility for practical use. Furthermore, a occurs at an altitude of 35,786 kilometers, power system must be developed that will also known as geosynchronous orbit (GEO). 2 Therefore, the center of mass of the elevator This program is a computer aided design must be over 35,786 kilometers above the tool that allows users to create and simulate surface of the earth. To minimize the 3D objects. Moreover, tensile forces can be amount of cable required, a counterweight at measured using the simulation feature of the end of the space elevator is necessary to SolidWorks and stresses on various points in pull the center of mass up above GEO and the cable design were studied to determine keep the elevator from collapsing back into the best design for a space elevator. Despite Earth. Nevertheless, the ribbon must be able the fact that the properties of carbon to support the tension from both below and nanotubes are not programmed into the above [2]. Recent discoveries of new software, a custom material was configured nanomaterials allow for the strength in SolidWorks that emulated the properties required. of carbon nanotubes. This custom material During deployment, the angular was used to test various cable designs. momentum of the spacecraft will be However, SolidWorks was not designed to conserved if no external torque is applied, as handle a structure of this magnitude and the spacecraft rotates once per orbital designs could not be modeled to the desired period. As the craft extends the cable, its specifications. Whereas thousands of tubes moment of inertia changes, slowing its might be present in a cross-section of a real rotation and eventually causing a cable, only a few dozen could be mapped in catastrophic failure. This mechanism must the program. In addition, weaves, which be taken into account. utilize semi-unstressed nanotubes, were impossible to simulate accurately. Unfortunately, this resulted in quantitative inconsistencies between designs. Nevertheless, invaluable qualitative information was gained. 4. Cable Design 4.1 Material The material used in a space elevator is the most important aspect of the project. For a long time, progress could not be made in the field due to a lack of appropriate materials. Even steel and Kevlar could not be applied to the construction of a cable due Figure 1: Earth and space elevator to the required taper ratio, the relationship combination showing increasing cable between the width of the cable at thickness [3] geosynchronous orbit and the width of the cable at the base point on Earth. For most 3. Software materials, the specific strength, or strength to weight ratio, is too low; the increase in SolidWorks was utilized to create 3D width that will be needed as the cable models of cable designs, as well as a scale supports more and more of its own weight model of the Earth-space elevator system. will be too large. Ever since the conception 3 and development of the carbon nanotube, to base calculations. In addition to the the space elevator has been a realistic number of graphene layers, the pattern in possibility. Carbon nanotubes have the which the graphene is bonded together also greatest specific strength of any material has a significant impact on the mechanical currently in existence and can enable a taper and electrical properties of the nanotube. ratio of 1.5 in theory [1]. For comparison, The three types of configurations for steel will have a taper ratio of 1052, which is SWNTs are armchair, zigzag, and chiral, well over the width of the universe [4]. which are based on the vector axis from Furthermore, the material that makes up the which a graphene sheet is rolled. In terms of tether must be resistant to the variety of the feasibility of a space elevator today, environments that sections of the cable will zigzag SWNTs are the best option because experience. The space elevator must be able they deform the least [7]. Deformation is to withstand numerous abuses, including bad for the construction of a space elevator severe weather within the atmosphere, because the tensile strength of the cable radiation in the Van Allen Belts, and debris cannot be predicted accurately after in space. Carbon nanotubes meet the deformation occurs and could cause physical requirements necessary to endure unknown consequences.
Details
-
File Typepdf
-
Upload Time-
-
Content LanguagesEnglish
-
Upload UserAnonymous/Not logged-in
-
File Pages20 Page
-
File Size-