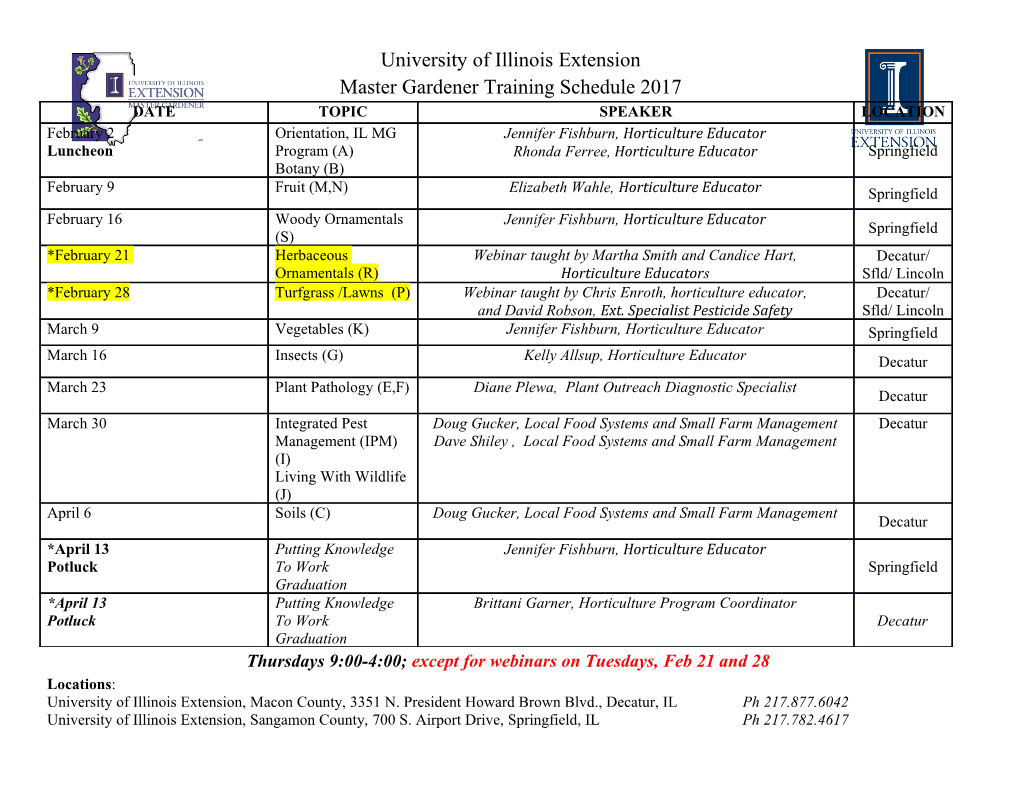
Juniper Online Journal Material Science ISSN: 2575-856X Review Article JOJ Mater Sci Volume 4 Issue 4 - May 2018 Copyright © All rights are reserved by Abdul Nazeer DOI: 10.19080/JOJMS.2018.04.555642 A Review on Secondary Process of Hot Extrusion on Aluminum Metal Matrix Composite Abdul Nazeer1* and Mir Safiulla2 1Research Scholar, Mechanical Engineering, Ghousia college of Emgineering, Ramnagaram, Karnataka, India 2Professor & Head R& D, Mechanical Engineering, Ghousia college of Emgineering, Ramnagaram, Karnataka, India Submitted: April 22, 2018; Published: May 02, 2018 *Corresponding author: Abdul Nazeer, Research Scholar, Mechanical Engineering, Ghousia college of Emgineering, Ramnagaram, Karnataka, India, Email: Abstract activesMetal are matrix carried composites on processing (MMCs) of Aluminum have made metal a lot matrix attention composite in engineering Since in materials last few year due lotits ofsignificantly work is carried improved on AMC’s. properties The present including paper aimshigh specificto summarize strength, different specific processing modulus, methodsdamping andcapacity emphasis and good is given wear on resistance effect of hot compared extrusion to asunreinforced a secondary alloys. process Recent of aluminum developments Al6061 and other engineering industries. and stir casting processing technique. Extensive applications of cast composite has been found in automotive, aerospace field, Transportation Keywords: Aluminum matrix composite; Stir Casting; Extrusion Abbreviations: MMCs: Metal Matrix Composites; PMCs: Polymer Matrix Composites; CMCs: Ceramic Matrix Composites Introduction and SiC, Al O , TiB , WC, CNTs are a few examples for reinforcing With rapid change in technology and recent development 2 3 2 secondary phase materials [9]. Addition of reinforcement SiC to in engineering materials and there processing technique have alumina leads to improvement in hardness and wear resistance, made an engineer to replace the conventional material with thus increasing its applicability. Many processing technique advance materials in order to increase weight to strength are available for MMC’s but most widely used technique is Stir ratio, easy processing technique, advance high resistance to casting method. Here Stir Casting method is implemented for atmospheric changes, Nowadays engineers have came up with lot the fabrication of Aluminum matrix composites [1]. In order to of development in structural materials in order for application change in properties of Metal matrix composite are subjected mainly in aerospace and automotive industries Properties to under the secondary processing techniques like forging, rolling extrusion etc. here we focusing on effect of Aluminum and improved elevated temperature properties compared to like high specific strength, stiffness, better wear resistance metal matrix composite when subjected to hot extrusion and it the conventional metals and alloys. Composite materials have was found that with Equal channel angular extrusion desirable almost replaced the conventional material due to its very good mechanical, chemical, wear properties tribiological properties and its very high strength to weight ratio, easy of manufacturing. enhancement in material properties is achieved due to ultra-fine grain refinement [2]. For uniform dispersion of material blade operating temperature at semisolid stage i.e. 630o for Al (6061). sub division namely Polymer Matrix Composite, Metal Matrix angle should be 45° or 60°, For good wet ability we need to keep As these composite material have broadly classified into three Composite and Ceramic Matrix Composite. Metal matrix reinforcement in the molten metal. Preheating of mould helps in composite (MMC) Aluminum alloys are widely used in aerospace At full liquid condition it is difficult uniform distribution of the reducing porosity as well as increases mechanical properties [1]. and automobile industries due to their low density and good Improved die design and surface treatment will play an important mechanical properties, better corrosion resistance and wear, low role in the economic production of high quality composites with excellent structures and properties [3,4]. Two new approaches metals and alloys. The properties of monolithic materials are thermal coefficient of expansion as compared to conventional improved with the addition of reinforcements. Aluminum, copper, forming behavior of metal matrix composites (MMC) have been magnesium and titanium are a few examples of matrix materials (Cold Forging and Thixo forging) towards an improvement of the investigated. Cold Forming was performed with two aluminum JOJ Material Sci 4(4): JOJMS.MS.ID.555642 (2018) 001 Juniper Online Journal Material Science based MMCs (Al6082 with Al2O3 processing may change the constituents (phases, shape) of Al O particles) [5-7]. Some of the work has done on hot rolling and the composite. 2 3 short fibers and Al6061 with aging due hot rolling one can achieve large plastic deformation and it is found that Tensile strength and hardness have increased Composite Material Composite material is a system of materials consisting of Effect of Secondary Processing and Nanoscale Reinforcement on two or more different materials combined at macroscopic level and wear rate is decreased [8]. Further the effort was made on the Mechanical Properties of Al-TiC Composites with an average basically consisting of a Matrix phase and a reinforcing phase. of 45nm, reinforcement were synthesized using low energy a) Matrix Phase: The primary phase, having a continuous planetary ball mill followed by hot extrusion Microstructural character, is called matrix. Matrix is usually more ductile and characterization of the materials results uniform distribution less hard phase. It holds the dispersed phase and shares a load with it. results that hardness nano-TiC particulates has increased, elastic of reinforcement, grain refinement . Properties characterization modulus, 0.2% yield strength [9,10]. b) Dispersed (Reinforcing) Phase: The second phase (or phases) is embedded in the matrix in a discontinuous form. a) Primary Processing of Composites: Production of This secondary phase is called dispersed phase. Dispersed composite material by combining ingredient materials (e.g. phase is usually stronger than the matrix, therefore it is powdered metal and loose ceramic particles, or molten metal sometimes called reinforcing phase. Classification of Composite Based on Matrix Phase and fibre preforms), but not necessarily to final shape or Polymer-matrix composites (PMCs) finalb) microstructureSecondary Processing: Processing steps which follow primary processing, and aim to alter the shape Metal-matrix composites (MMCs) or microstructure of the material (e.g.. shape casting, forging, extrusion, heat-treatment, machining). Secondary Ceramic-matrix composites (CMCs) Classification of Composites based on Reinforcing Phase (Figure 1) Figure1: Classification of Composites based on reinforcing phase. Liquid State Fabrication of Metal Matrix Composites The methods of liquid state fabrication of Metal Matrix iv. Squeeze Casting Infiltration Composites: v.Infiltration: Pressure is Die a liquid Infiltration state method of composite materials i. Stir Casting fabrication, in which a preformed dispersed phase (ceramic particles, fibers, woven) is soaked in a molten matrix metal, ii. Infiltration which fills the space between the dispersed phase inclusions iii. Gas Pressure Infiltration (Figure 2). How to cite this article: Abdul N, Mir Safiulla. A Review on Secondary Process of Hot Extrusion on Aluminum Metal Matrix Composite. JOJ Mater Sci. 002 2018; 4(4): 555642. DOI: 10.19080/JOJMS.2018.04.555642 Juniper Online Journal Material Science Figure 2: Different Infiltration process. Solid State Fabrication of Metal Matrix Composites i. Diffusion bonding Solid State Fabrication of Metal Matrix Composites: is the ii. Sintering (powder metallurgy) process, in which Metal Matrix Composites are formed as a result Diffusion Bonding: Diffusion Bonding is a solid state of bonding matrix metal and dispersed phase due to mutual fabrication method, in which a matrix in form of foils and a diffusion occurring between them in solid states at elevated temperature and under pressure. There are two principal groups of solid state fabrication of Metal Matrix Composites: dispersed phase in form of long fibers are stacked in a particular order and then pressed at elevated temperature (Figure 3). How to cite this article: Abdul N, Mir Safiulla. A Review on Secondary Process of Hot Extrusion on Aluminum Metal Matrix Composite. JOJ Mater Sci. 003 2018; 4(4): 555642. DOI: 10.19080/JOJMS.2018.04.555642 Juniper Online Journal Material Science Figure 3: Diffusion Bonding and Sintering Process. Sintering fabrication of Metal Matrix Composites: is a process, in which a powder of a matrix metal is mixed with a by means of mechanical stirring. Stir casting of metal matrix particles, short fibers) is mixed with a molten matrix metal composites was initiated in 1968, when S. Ray introduced subsequent compacting and sintering in solid state. alumina particles into an aluminum melt by stirring molten powder of dispersed phase in form of particles or short fibers for aluminum alloys containing the ceramic powders [11,12]. Vapor Deposition a) Physical Vapor Deposition: Mechanical stirring in the furnace is a main component of A typical stir casting process is illustrated in Figure 4 [13]. through a thick cloud of vaporized metal, coating
Details
-
File Typepdf
-
Upload Time-
-
Content LanguagesEnglish
-
Upload UserAnonymous/Not logged-in
-
File Pages6 Page
-
File Size-