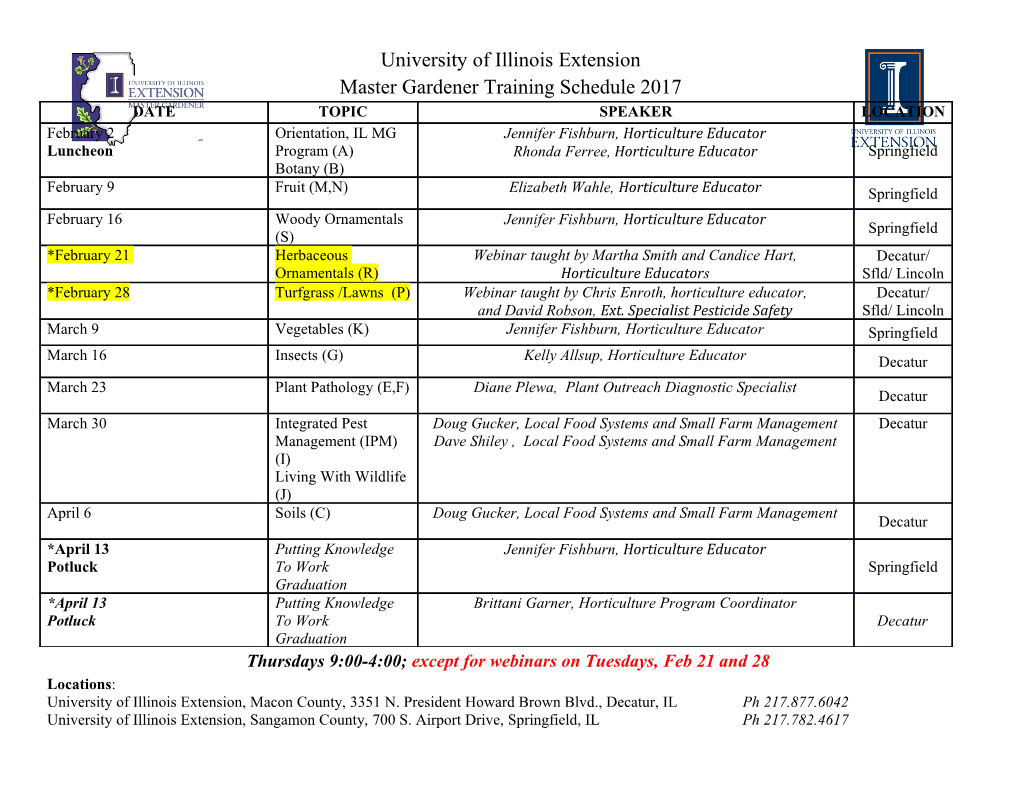
VARIABLE GEOMETRY WING-BOX: TOWARD A ROBOTIC MORPHING WING by Amin Moosavian B.Eng., Aerospace Engineering, Ryerson University, 2008 M.Eng., Aerospace Engineering, Ryerson University, 2010 A dissertation presented to the School of Graduate Studies at Ryerson University in partial fulfillment of the requirements for the degree of Doctor of Philosophy in the Program of Aerospace Engineering Toronto, Ontario, Canada, 2014 Copyright © Amin Moosavian 2014 Author’s Declaration I hereby declare that I am the sole author of this dissertation. This is a true copy of the dissertation, including any required final revisions, as accepted by my examiners. I authorize Ryerson University to lend this dissertation to other institutions or individuals for the purpose of scholarly research. I further authorize Ryerson University to reproduce this dissertation by photocopying or by other means, in total or in part, at the request of other institutions or individuals for the purpose of scholarly research. I understand that my dissertation may be made electronically available to the public. iii Abstract Variable Geometry Wing-box: Toward a Robotic Morphing Wing © Amin Moosavian, 2014 Doctor of Philosophy Aerospace Engineering Ryerson University The ability to vary the geometry of a wing to adapt to different flight conditions can significantly improve the performance of an aircraft. However, the realization of any morphing concept will typically be accompanied by major challenges. Specifically, the geometrical constraints that are imposed by the shape of the wing and the magnitude of the air and inertia loads make the usage of conventional mechanisms inefficient for morphing applications. Such restrictions have served as inspirations for the design of a modular morphing concept, referred to as the Variable Geometry Wing-box (VGW). The design for the VGW is based on a novel class of reconfigurable robots referred to as Parallel Robots with Enhanced Stiffness (PRES) which are presented in this dissertation. The underlying feature of these robots is the efficient exploitation of iv redundancies in parallel manipulators. There have been three categories identified in the literature to classify redundancies in parallel manipulators: 1) actuation redundancy, 2) kinematic redundancy, and 3) sensor redundancy. A fourth category is introduced here, referred to as 4) static redundancy. The latter entails several advantages traditionally associated only with actuation redundancy, most significant of which is enhanced stiffness and static characteristics, without any form of actuation redundancy. Additionally, the PRES uses the available redundancies to 1) control more Degrees of Freedom (DOFs) than there are actuators in the system, that is, under-actuate, and 2) provide multiple degrees of fault tolerance. Although the majority of the presented work has been tailored to accommodate the VGW, it can be applied to any comparable system, where enhanced stiffness or static characteristics may be desired without actuation redundancy. In addition to the kinematic and the kinetostatic analyses of the PRES, which are developed and presented in this dissertation along with several case-studies, an optimal motion control algorithm for minimum energy actuation is proposed. Furthermore, the optimal configuration design for the VGW is studied. The optimal configuration design problem is posed in two parts: 1) the optimal limb configuration, and 2) the optimal topological configuration. The former seeks the optimal design of the kinematic joints and links, while the latter seeks the minimal compliance solution to their placement within the design space. In addition to the static and kinematic criteria required for reconfigurability, practical design considerations such as fail-safe requirements and design for minimal aeroelastic impact have been included as constraints in the optimization process. The effectiveness of the proposed design, analysis, and optimization is demonstrated through simulation and a multi-module reconfigurable prototype. v Acknowledgements Foremost, I want to thank my supervisor Prof. Jeff Xi. I am extremely grateful to him for giving me the opportunity to work on this project and for providing guidance throughout my studies. His encouraging attitude and openness to new ideas along with his comprehensive knowledge of robotics and mechanisms have been immensely inspiring and instrumental to what has been accomplished. Furthermore, I want to thank my co-supervisor, Prof. Seyed Hashemi for all the guidance, helpful feedback, and insightful discussions during the course of this work. I have the utmost respect and gratitude for both of them, personally and professionally. I have learnt a tremendous amount from them over the years, and consider myself lucky to have studied under their supervision. I wish to express my gratitude to the defense committee, Prof. Brian Surgenor from Queens’s University, Prof. Vincent Chan from the Dept. of Mechanical Engineering, Prof. Puren Ouyang, and Prof. Anton de Ruiter from the Dept. of Aerospace Engineering, for all their invaluable remarks and suggestions regarding this thesis. This work was funded by the Natural Sciences and Engineering Research Council of Canada (NSERC) and Bombardier Aerospace (BA). I would like to thank NSERC, and BA, especially Dr. Fassi Kafyeke and Dr. Patrick Germain, for all their support. I would also like to thank the government of Ontario and Ryerson University for the vi various Ontario and Ryerson graduate scholarships and awards which helped to support this research. Furthermore, I would like to thank my colleagues at the Intelligent Systems and Robotics Laboratory for their support. A special thanks goes out to my good friend and colleague, Mike Rizoiu, for all the stimulating conversations we had about this project and his assistance with the prototype. Finally, a very special thanks goes out to my wonderful family, especially my amazing parents, and my lovely fiancée, Marlena, for their vast support and continuous encouragement. vii To My Parents viii “It is possible to fly without motors, but not without knowledge and skill.” Wilbur Wright ix Contents Author’s Declaration ............................................................................... iii Abstract .................................................................................................. iv Acknowledgements .................................................................................. vi Contents ................................................................................................... x List of Tables .......................................................................................... xv List of Figures ....................................................................................... xvi Acronyms .............................................................................................. xxi Nomenclature ....................................................................................... xxii Chapter 1 Introduction ............................................................................ 1 1.1 Motivation .................................................................................................... 3 1.2 Objectives ..................................................................................................... 3 1.3 Variable Geometry Wing-box ...................................................................... 4 1.4 Thesis Organization ..................................................................................... 6 Chapter 2 Background and Literature Review ........................................ 7 2.1 Morphing DOFs ......................................................................................... 10 2.1.1 Variable Sweep ....................................................................................... 11 2.1.2 Variable Span ......................................................................................... 12 x 2.1.3 Variable Twist ........................................................................................ 12 2.1.4 Variable Dihedral (Cant) ........................................................................ 12 2.2 Airfoil Morphing ........................................................................................ 13 2.3 Morphing Skins .......................................................................................... 14 2.4 Morphing for Control vs. Improved Performance ...................................... 15 2.5 Actuation Concepts .................................................................................... 16 2.5.1 VGTMs for Wing Morphing ................................................................... 18 2.5.2 Embedded Actuation .............................................................................. 20 Chapter 3 Morphing Mechanism Design ............................................... 22 3.1 Reconfigurability ........................................................................................ 23 3.2 Manipulator Redundancy ........................................................................... 25 3.3 Robot Design .............................................................................................. 29 3.4 Class Synthesis ........................................................................................... 35 3.5 Architecture Design ................................................................................... 37 3.6 Modularity in Design ................................................................................
Details
-
File Typepdf
-
Upload Time-
-
Content LanguagesEnglish
-
Upload UserAnonymous/Not logged-in
-
File Pages244 Page
-
File Size-