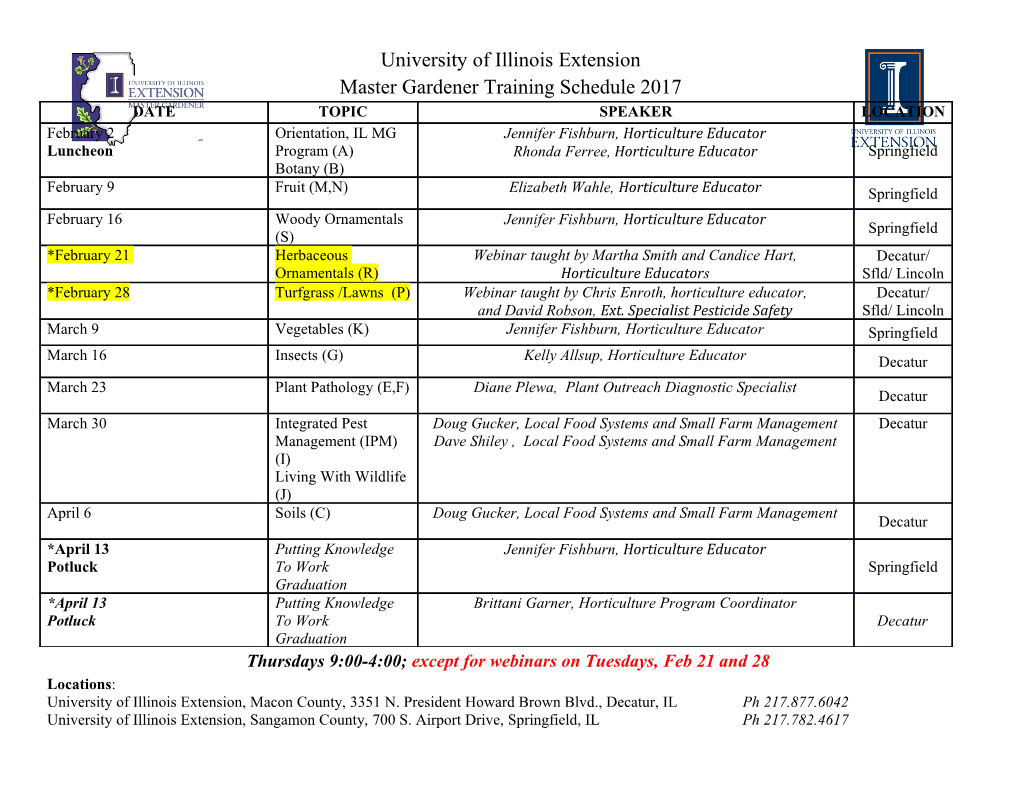
SERVO HYDRAULIC TECHNOLOGY IN FLIGHT CONTROL Workshop on Innovative Engineering for Fluid Power and Vehicular Systems ABIMAQ - São Paulo 14-15 May 2012 Mario F. Valdo OVER 55 YEARS OF EXPERIENCE IN MOTION CONTROL • Founded by Bill Moog, Art Moog and Lou Geyer in 1951 as "Moog Valve Company" – based on the first commercial servo valve • Founder’s culture of innovation and persistence still exist today: ─ Collaborative approach ─ "Can-do" mindset ─ Flexible organization ─ Dedicated solutions 1 Flight Control Technology A Global Company c Argentina Germany Russia Australia India Singapore Austria Ireland South Africa Brazil Italy South Korea Canada Japan Spain China Lithuania Sweden Costa Rica Luxembourg Switzerland Denmark Netherlands United Arab Emirates Finland Norway United Kingdom France Philippines United States 2 Flight Control Technology GROUPS MOOG INC. US$2.33 Billions (FY 2011) Space & Industrial Compo- Medical Aircraft Defense Group nents Devices Group Group Group Group $850 M $629 M $356M $353 M $142 M 36% 27% 15% 15% 7% 3 Flight Control Technology HIGH PERFORMANCE MOTION CONTROL Military & Commercial Aircraft Satellites, Missiles & Launch Vehicles Defense & Surveillance Industrial Machinery Test & Simulation Infusion Pumps (medical) Components (slip rings, fiber optic joints, air moving, resolvers, encoders) 4 Flight Control Technology HIGH PERFORMANCE MOTION CONTROL Closed loop control of physical variables (servocontrol): • position • velocity • aceleration • force • pressure Servocontrols Technology: • Electro-hydraulic : servovalves, servopumps • Electro-mechanical : servomotors • Electro-pneumatic: proportional pneumatic valves 5 Flight Control Technology AIRCRAFT MARKET - OFFERING Integrated Flight Control Systems • Primary Flight Control Systems • High Lift Systems • Maneuvering Leading Edge Systems Critical Control Applications • Engine Controls • Active Vibration Control • Weapons Bay Door Drive • Braking and Steering Critical Control Products • Flight Control Computers & Software • Cockpit Controls • Control Electronics & Power Drives • Actuators – Electrohydraulic, Electromechanical and Electrohydrostatic • Related Components 6 6 Flight Control Technology AIRCRAFT AXIS OF MOTION Y X Z 7 Flight Control Technology FLY CONTROL SURFACES Leading Edge Trailing Edge RUDDER Slats ELEVATOR Flap Wing Tip Trim Tab Spoilers AILERON Trailing Edge Leading Edge 8 Flight Control Technology ROLL - AILERONS X An animation of an airplane rolling via its ailerons 9 Flight Control Technology PITCH -ELEVATORS Y An animation of an airplane pitching via its elevators 10 Flight Control Technology YAW- RUDDER Z An animation of an airplane yawing with its rudder 11 Flight Control Technology AIRCRAFT FLIGHT CONTROLS In the drawing, a red arrow shows the way the control stick is being tilted. Small green arrows show the swing of the respective control surfaces and indicate the direction of the forces acting on the cable. The bent wires show the generic routing of control cables in the aircraft and connect the controls with the control surfaces. In smaller or older aircraft, the lines represent actual cables that link controls to control surfaces. In more modern aircraft, a computer take of the pilot inputs and send commands electronically to control surface actuators. Control surfaces: A) aileron, C) elevator, D) rudder. B) control stick Rudder = yaw (turn around Z) Ailerons= roll (turn around X) Elevators = pitch (turn around Y) 12 Flight Control Technology AEROSPACE X INDUSTRIAL COMPONENTS 13 Flight Control Technology NOZZLE-FLAPPER SERVOVALVE mechanical feedback 14 Flight Control Technology NOZZLE-FLAPPER SERVOVALVE – detailed view Torque motor Nozzle-flapper Orifice Orifice Q Q Feedback wire Bushing & Spool Control ports Actuator (load) 15 Flight Control Technology APPLYING COMMAND..... I 1- Electric current generates a 2- The magnetic field magnetic field… generates torque.... 3- Flapper moves to the side... T T 4- Pressure 4- Pressure reduces here increases here A B 5- Spool moves and pulls the feedback wire..... 16 Flight Control Technology REACHING THE FINAL POSITION (defined by the current command ) 6- When : I feedback wire torque = electric current torque the flapper gets centralized! 7- Centralized flapper T T means that pressures are the same in both sides of the spool . A B 8- Spool stays in a position proportional to the current command. 17 Flight Control Technology JET PIPE SERVOVALVE Torque motor Pipe Receptor Feedback wire Bushing & Spool Control ports Actuator (load) 18 Flight Control Technology INTEGRATING A POSITION TRANSDUCER ( to implement electronic spool position loop control and diagnostics) Integrated or external electronics to close the spool position loop EFB= electrical feedback (position transducer) 19 Flight Control Technology EFB SERVOVALVE SPOOL POSITION CLOSED LOOP Zero Error Pressure amplifier + Torque Motor + Flow P.D. command - Orifices Spool Position Nozzle flapper Position Spool Spool P.D.Transducer position (output) 20 Flight Control Technology High-flow configuration Integrated Control Electronics Linear Motor Position Transducer Spool Spring 21 Flight Control Technology SPOOL POSITION CLOSED LOOP Zero Error amplifier + + Flow P.D. PWM command - Spool Position Linear Motor Spool Position Transducer Spool P.D. Spring position (output) 22 Flight Control Technology LVDT LINEAR VOLTAGE DISPLACEMENT TRANSDUCER Voltage proportional Fixed body to core position Secundaries P S Primary 1 (syncronous) Oscilator Demodulator S2 Fixed amplitude and Core output [volts] frequency P linear range stroke S1 Core connected [mm] to the S movable part 2 23 Flight Control Technology ACTUATOR POSITION CONTROL CLOSED LOOP Servoamplifier ZERO GAINS: P, I, D Valve P + + command + Position Command I + - + D Servovalve with integrated spool position transducer SCALE and electronics Oscilator Position feedback DC = ≈ Demodulator Actuator LVDT Position Transducer 24 Flight Control Technology ACTUATOR POSITION CONTROL DIGITAL CLOSED LOOP : Complex Algorithms + Diagnostics + Fieldbus Digital Controller TRACKING CONTROLLER P Flag Handler Function Blocks Valve position control Demand Pressure with Demand F T I D/AD/A I force limiting control T F Fieldbus PRESSURE D D Interface CONTROL A/DA/D Pa Ratio A/DA/D Pb TRIGGER Effective (Actual) D DETECTION Pressure Feedback Max/Min Error Window Flag Pressure Trigger Gen.r Latched TRUE (T) when Pressure High Commands, Max Rate Position Servovalve Supervision Demand Limit P POSITION Position Feedback CONTROL Flight A/DA/D X Computer Flight Pilot commands envelope Aircraft real-time data P/V P/V Position Transducer Pressure Transducers Flight Control Technology REDUNDANCY: the “soul” of modern flight control In large and military airplanes each flight control surface is either: • operated by 2 or more actuators in “parallel” (active-bypass-damper modes) • operated by one actuator with redundant servovalves, transducers, electrical conections and oil supply connections • amixoftheabove: Flight Control Actuation System Integrator for the B-2 Spirit A quadraplex system controls the B-2’s flight control surfaces and is comprised of Flight Control Computers, Actuator Control Electronics, Servoactuators, Sensors, System Software and Redundancy Management 4 electronics driving 2 redundant actuators The B-2 Spirit Actuation System features: • Quadraplex redundant electrical and hydraulic systems • Advanced electronic controls with fault diagnostics • 4000 psi Hydraulic system 4 redundant fieldbuses • Redundancy management connections to the flight computer 2 oil supply lines per actuator 2 actuators controlling the same surface REDUNDANCY requires complex “decision” algorithms implemented by the aircraft flight control software 26 Flight Control Technology NASA – SPACE SHUTTLE TRUST VECTOR ACTUATORS (Designed in 1973) 4 redundant servovalves, only one is active (mechanical-hydraulic selection) 27 Flight Control Technology REDUNDANCY MODES IN ELECTROHYDRAULIC ACTUATORS Damper Active Bypass (or blocked) PT PT PT 28 Flight Control Technology TYPICAL REDUNDANCY- AILERONS Active – Active on each surface Active – Standby on each surface Sized for hinge moment with both active Sized for hinge moment with one active • Normal mode 1: active , active • Normal mode 2: active , bypass • First Failure 1: damped , active • First Failure 2: bypass , active • Second failure1: damped , damped • Second failure 2: damped , damped Hydraulic Electro-hydraulic actuators Systems 4B 3B 4A 3A 3 4 2B 1B 2A 1A 2 1 Flight control surfaces damped = damped or blocked, depending on the flight control design 29 Flight Control Technology TIPYCAL REDUNDANCY- ELEVATOR Active – Active on each surface Active – Standby on each surface Sized for hinge moment with both active Sized for hinge moment with one active • Normal mode: active , active • Normal mode: active , bypass • First Failure: bypass , active • First Failure: bypass , active • Second failure: damped , damped • Second failure: damped , damped Electro-hydraulic actuators Hydraulic Systems 2B 1B 2A 1A 1 2 Flight control surfaces 3030 Flight Control Technology TYPICAL REDUNDANCY - RUDDER Electro-Hydraulic Actuators 1A Active – Active - Active Sized for hinge moment with all active 1B • Normal mode : active , active , active 1 • First Failure: bypass , active , active 1C • Second failure: damped , bypass , active • Third failure: damped, damped , damped Flight control surface Hydraulic Systems 3131 Flight Control Technology ELECTRO-HYDRAULIC
Details
-
File Typepdf
-
Upload Time-
-
Content LanguagesEnglish
-
Upload UserAnonymous/Not logged-in
-
File Pages73 Page
-
File Size-