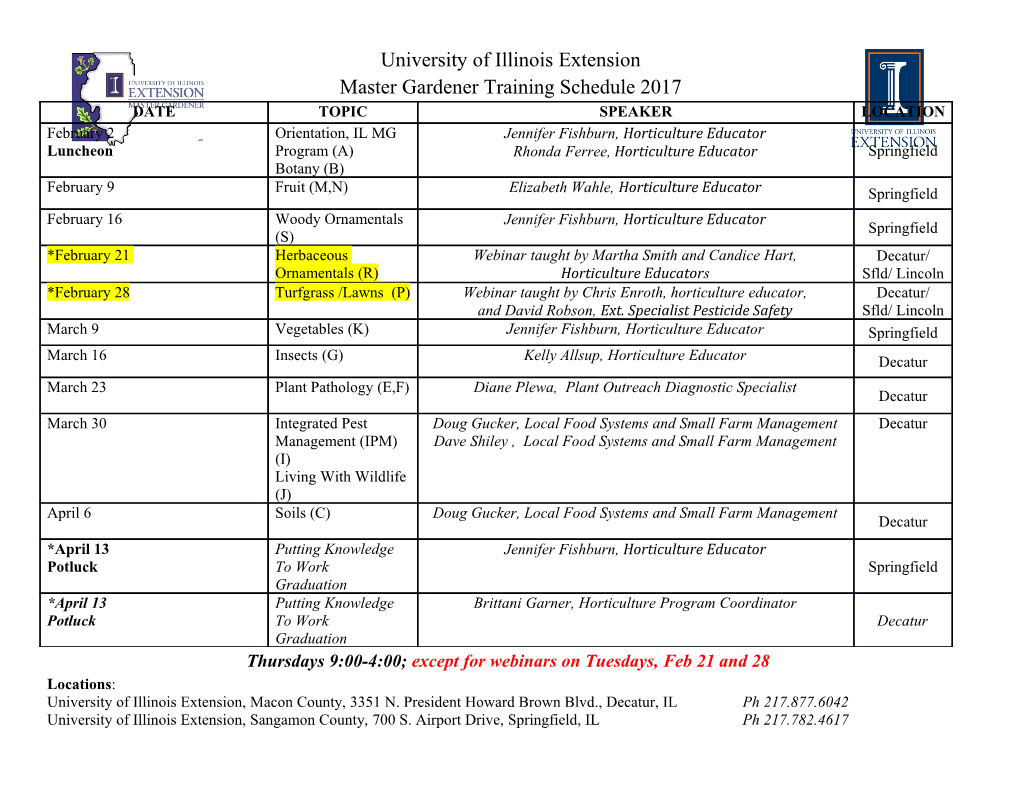
ILSB Report 206 hjb/ILSB/210922 ILSB Report / ILSB-Arbeitsbericht 206 (supersedes CDL–FMD Report 3–1998) A SHORT INTRODUCTION TO BASIC ASPECTS OF CONTINUUM MICROMECHANICS Helmut J. B¨ohm Institute of Lightweight Design and Structural Biomechanics (ILSB) Vienna University of Technology updated: September 22, 2021 c Helmut J. B¨ohm, 1998, 2021 Contents Notes on this Document iv 1 Introduction 1 1.1 Inhomogeneous Materials ............................ 1 1.2 Homogenization and Localization ....................... 4 1.3 Volume Elements ................................ 6 1.4 Overall Behavior, Material Symmetries .................... 7 1.5 Major Modeling Strategies in Continuum Micromechanics of Materials .. 9 1.6 Model Verification and Validation ....................... 14 2 Mean-Field Methods 16 2.1 General Relations between Mean Fields in Thermoelastic Two-Phase Materials 16 2.2 Eshelby Tensor and Dilute Matrix–Inclusion Composites .......... 20 2.3 Some Mean-Field Methods for Thermoelastic Composites with Aligned Rein- forcements .................................... 23 2.3.1 Effective Field Approaches ....................... 24 2.3.2 Effective Medium Approaches ..................... 30 2.4 Other Analytical Estimates for Elastic Composites with Aligned Reinforce- ments ...................................... 32 2.5 Mean-Field Methods for Nonlinear and Inelastic Composites ........ 35 2.5.1 Viscoelastic Composites ........................ 35 2.5.2 (Thermo-)Elastoplastic Composites .................. 36 2.6 Mean-Field Methods for Composites with Nonaligned Reinforcements ... 41 2.7 Mean-Field Methods for Non-Ellipsoidal Reinforcements .......... 45 2.8 Mean-Field Methods for Coated Reinforcements ............... 48 2.9 Mean-Field Methods for Conduction and Diffusion Problems ........ 48 3 Bounding Methods 55 3.1 Classical Bounds ................................ 55 3.2 Improved Bounds ................................ 59 3.3 Bounds on Nonlinear Mechanical Behavior .................. 60 3.4 Bounds on Diffusion Properties ........................ 61 3.5 Comparisons of Mean-Field and Bounding Predictions for Effective Thermo- elastic Moduli .................................. 61 3.6 Comparisons of Mean-Field and Bounding Predictions for Effective Con- ductivities .................................... 68 ii 4 General Remarks on Modeling Approaches Based on Discrete Micro- structures 70 4.1 Microgeometries and Volume Elements .................... 70 4.2 Boundary Conditions .............................. 77 4.3 Numerical Engineering Methods ........................ 80 4.4 Evaluation of Results .............................. 86 5 Periodic Microfield Approaches 90 5.1 Basic Concepts of Periodic Homogenization ................. 90 5.2 Boundary Conditions .............................. 92 5.3 Application of Loads and Evaluation of Fields ................ 100 5.4 Periodic Models for Composites Reinforced by Continuous Fibers ..... 104 5.5 Periodic Models for Composites Reinforced by Short Fibers ......... 110 5.6 Periodic Models for Particle Reinforced Composites ............. 116 5.7 Periodic Models for Porous and Cellular Materials .............. 123 5.8 Periodic Models for Some Other Inhomogeneous Materials ......... 127 5.9 Periodic Models Models for Diffusion-Type Problems ............ 130 6 Windowing Approaches 132 7 Embedding Approaches and Related Models 137 8 Hierarchical and Multi-Scale Models 143 9 Closing Remarks 147 Bibliography 149 iii Notes on this Document The present document is an expanded and modified version of the CDL–FMD report 3–1998, “A Short Introduction to Basic Aspects of Continuum Micromechanics”, which, in turn, is based on lecture notes prepared for the European Advanced Summer Schools Frontiers of Computational Micromechanics in Industrial and Engineering Materials held in Galway, Ireland, in July 1998 and in August 2000. Related lecture notes were used for graduate courses in a Summer School held at Ameland, the Netherlands, in October 2000 and during the COMMAS Summer School held in September 2002 in Stuttgart, Germany. All of the above documents, in turn, are closely related to the micromechanics section of the lecture notes for the course “Composite Engineering” (317.003) offered regularly at Vienna University of Technology. The course notes “A Short Introduction to Continuum Micromechanics” (B¨ohm, 2004) for the CISM Course on Mechanics of Microstructured Materials held in July 2003 in Udine, Italy, may be regarded as a compact version of the present report that employs a somewhat different notation. The course notes “Analytical and Numerical Methods for Modeling the Thermomechanical and Thermophysical Behavior of Microstructured Mate- rials” (B¨ohm et al., 2009) are also related to the present report, but emphasize different aspects of continuum micromechanics, among them the thermal conduction behavior of inhomogeneous materials and the modeling of cellular materials. The present document is being updated periodically to reflect current developments in continuum micromechanics as seen by the author. The latest version can be downloaded as https://www.ilsb.tuwien.ac.at/links/downloads/ilsbrep206.pdf. The August 12, 2015 version of this report can be accessed via the DOI: 10.13140/RG.2.1.3025.7127. A Voigt/Nye notation is used for the mechanical variables in chapters 1 to 3. Tensors of order 4, such as elasticity, compliance, concentration and Eshelby tensors, are written as 6 6 quasi-matrices, and stress- as well as strain-like tensors of order 2 as 6-(quasi-)vectors. × These 6-vectors are connected to index notation by the relations σ1 σ11 ε1 ε11 σ2 σ22 ε2 ε22 σ σ ε ε σ = 3 33 ε = 3 33 , σ4 ⇔ σ12 ε4 ⇔ γ12 σ σ ε γ 5 13 5 13 σ σ ε γ 6 23 6 23 iv 1 where γij =2εij are the shear angles (“engineering shear strains”). Tensors of order 4 are denoted by bold upper case letters, stress- and strain-like tensors of order 2 by bold lower case Greek letters, and 3-vectors by bold lower case letters. Conductivity-like tensors of order 2 are treated as 3 3 matrices and denoted by calligraphic upper case letters. All other variables are taken× to be scalars. In using the present notation it is assumed that the 4th order tensors show orthotropic or higher symmetry and that the material axes are aligned with the coordinate system where appropriate. Details of the ordering of the components of ε and σ will not impact formulae. It is worth noting that with a notation like the present one some coefficients of Eshelby tensors differ compared to index notation, compare Pedersen (1983). The tensorial product between two tensors of order 2 as well as the dyadic product between two vectors are denoted by the symbol “ ”, where [η ζ]ijkl = ηijζkl, and ⊗ ⊗ [a b]ij = aibj, respectively. The contraction between a tensor of order 2 and a 3-vector ⊗ is denoted by the symbol “ ”, where [ζ n]i = ζijnj. Other products are defined implicitly by the types of quasi-matrices∗ and quasi-vectors∗ involved. A superscript T denotes the transpose of a tensor or vector. Constituents (phases) are denoted by superscripts, with (p) standing for a general phase, (m) for a matrix, (i) for inhomogeneities of general shape, and (f) for fibers. Axial and trans- verse properties of transversely isotropic materials are marked by subscripts A and T , respectively, and effective (or apparent) properties are denoted by a superscript asterisk ∗. The present use of phase volume fractions as microstructural parameters is valid for the microgeometries typically found in composite, porous and polycrystalline materials. Note that for penny shaped cracks a crack density parameter (O’Connell and Budiansky, 1974) is the proper choice. 1 1 T This notation allows strain energy densities to be obtained as the scalar product U = 2 σ ε. Further- ∠ ∠ ∠ ∠ −1 T more, the stress and strain “rotation tensors” Rσ and Rε follow the relationship Rε = [(Rσ ) ] . v Chapter 1 Introduction In the present report some basic issues of and some of the modeling strategies used for studying static and quasistatic problems in continuum micromechanics of materials are discussed. The main emphasis is put on application related (or “engineering”) aspects, and neither a comprehensive theoretical treatment nor a review of the pertinent litera- ture are attempted. For more formal treatments of many of the concepts and methods discussed in the present work see, e.g., Mura (1987), Aboudi (1991), Nemat-Nasser and Hori (1993), Suquet (1997), Markov (2000), Bornert et al. (2001), Torquato (2002), Milton (2002), Qu and Cherkaoui (2006), Buryachenko (2007), Kachanov and Sevostianov (2013) as well as Kachanov and Sevostianov (2018); Yvonnet (2019) is specialized to numerical continuum micromechanics. Shorter overviews of continuum micromechanics were given, e.g., by Hashin (1983), Zaoui (2002) and Kanout´eet al. (2009). Discussions of the history of the development of the field can be found in Markov (2000) and Zaoui (2002). Due to the author’s research interests, more room is given to the thermomechanical behavior of two-phase materials showing a matrix–inclusion topology (“solid dispersions”) and, especially, to metal matrix composites (MMCs) than to materials with other phase topologies or phase geometries, or to multi-phase materials. 1.1 Inhomogeneous Materials Many industrial and engineering materials as well as the majority of biological materials are inhomogeneous, i.e., they consist of dissimilar constituents (“phases”) that are dis- tinguishable at some (small) length scale(s). Each
Details
-
File Typepdf
-
Upload Time-
-
Content LanguagesEnglish
-
Upload UserAnonymous/Not logged-in
-
File Pages198 Page
-
File Size-