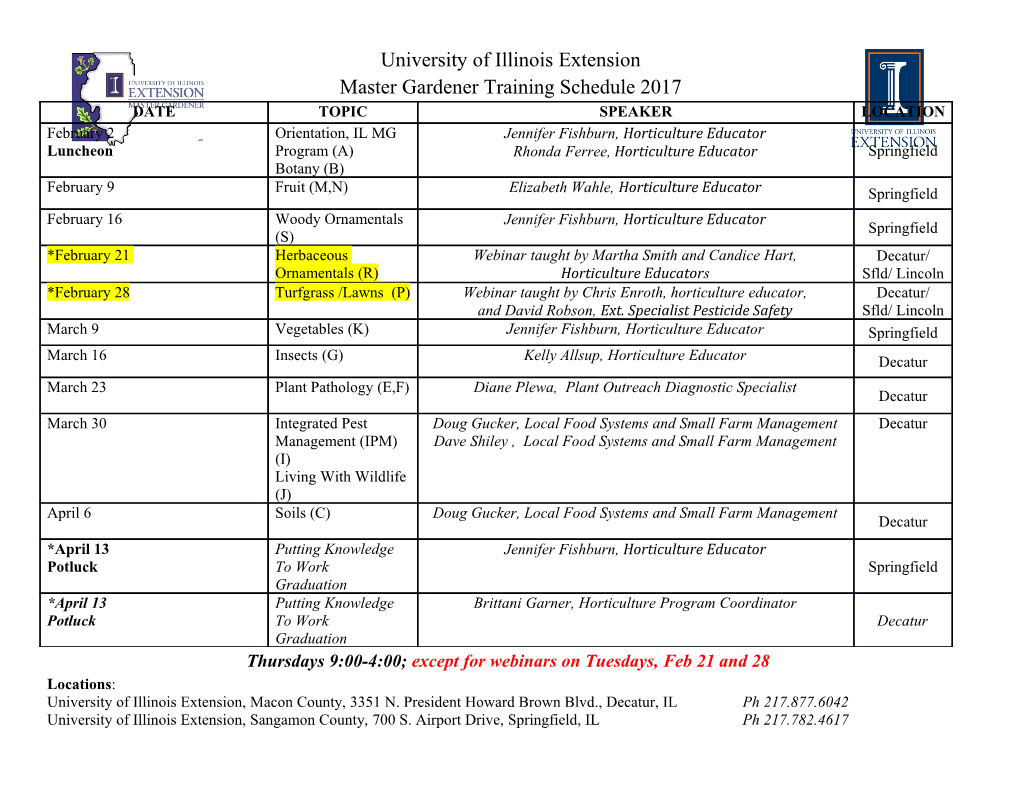
Hydraulic Design of Large-Diameter Pipes Fabia´n A. Bombardelli1 and Marcelo H. Garcı´a, M.ASCE2 Abstract: The Hazen–Williams formula is frequently used for the design of large-diameter pipes, without regard for its limited range of applicability. This practice can have very detrimental effects on pipe design, and could potentially lead to litigation. Available evidence shows that the application of the formula is accurate only if the operation of the pipe is located within the transition or smooth, turbulent-flow regimes. Most working ranges for water-supply pipes usually fall outside such conditions. This paper presents an analysis which highlights the potential implications of current use of the Hazen–Williams formula for the design of large-diameter pipe systems. DOI: 10.1061/͑ASCE͒0733-9429͑2003͒129:11͑839͒ CE Database subject headings: Pipe flow; Resistance coefficients; Roughness; Pipe design. Introduction with the help of the Hazen–Williams equation. After only 5 years in service, it was found that the network was inadequate in deliv- Worldwide population growth has brought along a clear need to ering the amount of water it had been designed for. The authors increase the capacity of water-supply and sewerage systems. were asked to analyze why the recently built pipeline could not Pipes having large diameters are commonly found in modern meet that water demand. The analysis consisted of: ͑1͒ reviewing water-distribution networks located in major metropolitan areas. the literature concerning issues such as range of validity and ac- Consequently, the misuse of any design formulation to estimate curacy of the Hazen–Williams formula; ͑2͒ revisiting the original flow resistance in large pipes can lead to serious practical draw- dataset employed by Hazen and Williams to develop the equation; backs. More specifically, those systems might not be able to meet and ͑3͒ using pressure-head and velocity measurements taken in- the demand they were designed for, thus reducing their useful life. dependently by two consulting engineering firms to estimate flow The Hazen–Williams formula, which dates back to the early resistance ͑i.e., resistance coefficients͒ in the pipeline system in 1900s, has traditionally been regarded as a general, simple tool to ͑ ͒ question. compute head losses in pipes carrying water Chen 1992 . The In what follows, the analysis inspired by the case study is equation includes a conveyance coefficient usually assumed to be presented, followed by a discussion of the results, and the con- constant for a certain pipe-wall material, regardless of the pipe clusions. size or the flow range. This fact can result in deficient designs under a wide set of conditions. Unfortunately, the formula is cur- rently being used outside of its actual range of validity throughout Preliminary Theoretical Considerations the United States and worldwide. Furthermore, in many cities and and Analysis some counties throughout the States, any computation dealing with water flow in pipes is simply rejected if the Hazen–Williams There are a number of equations commonly used to estimate flow formula is not used, without any regard for its intrinsic limitations resistance in channels and pipes. They are: ͑Diskin 1960; Jain et al. 1978; Liou 1998; Christensen 2000; • Manning equation Locher 2000; Swamee 2000͒. 2/3 1/2 KnR S In this paper, an analysis illustrating the implications of cur- Uϭ (1) rent use of available resistance formulations is presented. The n ͑ ͒ case study that motivated the analysis refers to a large water- • Dimensionally homogeneous Manning formula Yen 1992b supply system for a major metropolitan area, originally designed g1/2R2/3S1/2 Uϭ (2) ng 1 Research Assistant, Ven Te Chow Hydrosystems Laboratory, Dept. of • Chezy equation Civil and Environmental Engineering, Univ. of Illinois at Urbana- Champaign, 205 North Mathews Ave., Urbana, IL 61801. On leave from UϭCR1/2S1/2 (3) Instituto Nacional del Agua ͑INA͒, Argentina. E-mail: • Darcy–Weisbach equation [email protected] 1/2 1/2 2Chester and Helen Siess Professor, and Director, Ven Te Chow Hy- 2g h f Uϭͩ ͪ D1/2ͩ ͪ (4) drosystems Laboratory, Dept. of Civil and Environmental Engineering, f L Univ. of Illinois at Urbana-Champaign, 205 North Mathews Ave., Ur- • Hazen–Williams equation bana, IL 61801. E-mail: [email protected] ϭ 0.63 0.54 Note. Discussion open until April 1, 2004. Separate discussions must U KHWCHWR S (5) be submitted for individual papers. To extend the closing date by one month, a written request must be filed with the ASCE Managing Editor. where U indicates the cross-sectional averaged velocity; ϭ ϭ ϭ The manuscript for this paper was submitted for review and possible R hydraulic radius; S slope of the energy grade line; D pipe ϭ ϭ publication on July 30, 2001; approved on May 14, 2003. This paper is diameter; L length of the reach of the pipe; h f energy loss in part of the Journal of Hydraulic Engineering, Vol. 129, No. 11, Novem- the pipe reach ͑expressed as per unit weight of fluid͒; ϭ ϭ ber 1, 2003. ©ASCE, ISSN 0733-9429/2003/11-839–846/$18.00. g acceleration of gravity; Kn and KHW unit conversion factors; JOURNAL OF HYDRAULIC ENGINEERING © ASCE / NOVEMBER 2003 / 839 Fig. 1. Predictions obtained with the Hazen–Williams formula plotted in the Moody diagram ͓adapted from Diskin ͑1960͔͒. Operational points of the pipes pertaining to the case study ͑measurements by the two consulting engineering firms͒. ͑ ͒ and n, ng , C, f, and CHW refer to the resistance/conveyance co- and slope. Vennard 1958 highlighted that one of the disadvan- 1/2 ͑ ͒ efficients. Kn is equal to 1 m /s International System, SI or to tages of the equation was related to ‘‘the impossibility of applying 1.486 ft1/3 m1/6/s if English units are employed ͑Yen 1992b͒. For it to all fluids under all conditions.’’ Nevertheless, Diskin ͑1960͒ KHW , values of 0.849 and 1.318 are used in each of the above was apparently the first to strongly acknowledge the limitations systems, respectively ͑Jeppson 1977͒. Hazen and Williams evalu- associated with the formula and to undertake a rather careful ϭ ated the factor 1.318 as a means of keeping CHW C, for a slope analysis of its range of validity. Diskin first rearranged the Ϫ3 ͑ ͒͑ of 10 and a hydraulic radius of 0.305 m 1ft Williams and Hazen–Williams equation in the shape of the Darcy–Weisbach ͒ Hazen 1920 . A considerable number of papers has been devoted formula, in a similar way as previously done by Vennard ͑1958͒. to the determination of values for CHW pertaining to pipes made Thus he was able to obtain a power relation between f, C , D, ͑ HW of different materials, including polyethylene pipes Moghazi and R ͑the pipe Reynolds number, RϭUD/; is the water ͒ 1998 . Also, several papers have addressed the optimization of the kinematic viscosity͒, that reads for D in meters design of pipe networks, either using the Hazen–Williams for- mula ͓e.g., Datta and Sridharan ͑1994͒; and Niranjan Reddy et al. 1.852 0.2004͑100/CHW͒ 1 ͑1996͔͒, or modified formulations ͓Elimam et al. ͑1989͒; and f ϭ (6) 0.019 0.148 Charalambous and Elimam ͑1990͔͒. D R It has been well known since the beginning of the last century In Eq. ͑6͒, the value of water viscosity at 15°C was employed. ͑King et al. 1948͒, that the Darcy–Weisbach and Manning formu- las can be both used for computations in either open-channel or This expression demonstrates that CHW is not a constant for a pipe, fully rough turbulent flow. Thus it is possible to determine certain wall condition, as is interpreted in numerous engineering ͑ ͒ backwater profiles in open channels using the Darcy–Weisbach manuals Liou 1998 . Instead, it depends on the flow condition, equation or, conversely, to compute energy losses in pipes em- the pipe diameter and relative roughness, and the water tempera- ploying Manning’s equation, provided the convenient equivalence ture, through the kinematic viscosity, . Dϭ4R is considered, and reliable estimates for the resistance Based on this result, Diskin plotted Eq. ͑6͒ for different values ͑ ͒ coefficients are at hand ͑Yen 1992a, 2002͒. The Chezy equation of CHW and D into the Moody diagram Fig. 1 . Using this plot, can also be employed in either case. However, the Hazen– he was able to conclude that the formula is applicable ‘‘in part of Williams formula has quite a restricted range of application that the transition zone.’’ Diskin determined the ranges of Reynolds limits its use. numbers for which the original lines of the Moody diagram are In their classic monograph, Williams and Hazen ͑1920͒ stated parallel to the lines representing the predictions of the Hazen– that the exponents of their equation depended on pipe diameter Williams equation. Those limiting Reynolds numbers increase 840 / JOURNAL OF HYDRAULIC ENGINEERING © ASCE / NOVEMBER 2003 Table 1. Measurements Performed by Two Engineering Firms ͑Values Computed by Authors͒ ͑a͒ First line corresponds to the main pipe; second line pertains to another pipe in the system with another discharge. Pipe Velocity Losses Reach Slope diameter Area measured measured length of energy ng C ͑ ͒ ͑ 2͒ ͑ ͒ ͑ ͒ ͑ ͒ ͑ 1/6͒ ͑ 1/2 ͒ m m m/s m m line CHW fnm C f m /s R 2.286 4.104 1.076 9.604 13,692.53 0.00070 91 0.027 0.017 0.053 0.0034 54 2,450,000 1.829 2.627 0.960 1.884 3,213.506 0.00059 103 0.023 0.015 0.047 0.0029 59 1,750,000 ͑b͒ All measurements pertain to the main pipes.
Details
-
File Typepdf
-
Upload Time-
-
Content LanguagesEnglish
-
Upload UserAnonymous/Not logged-in
-
File Pages8 Page
-
File Size-