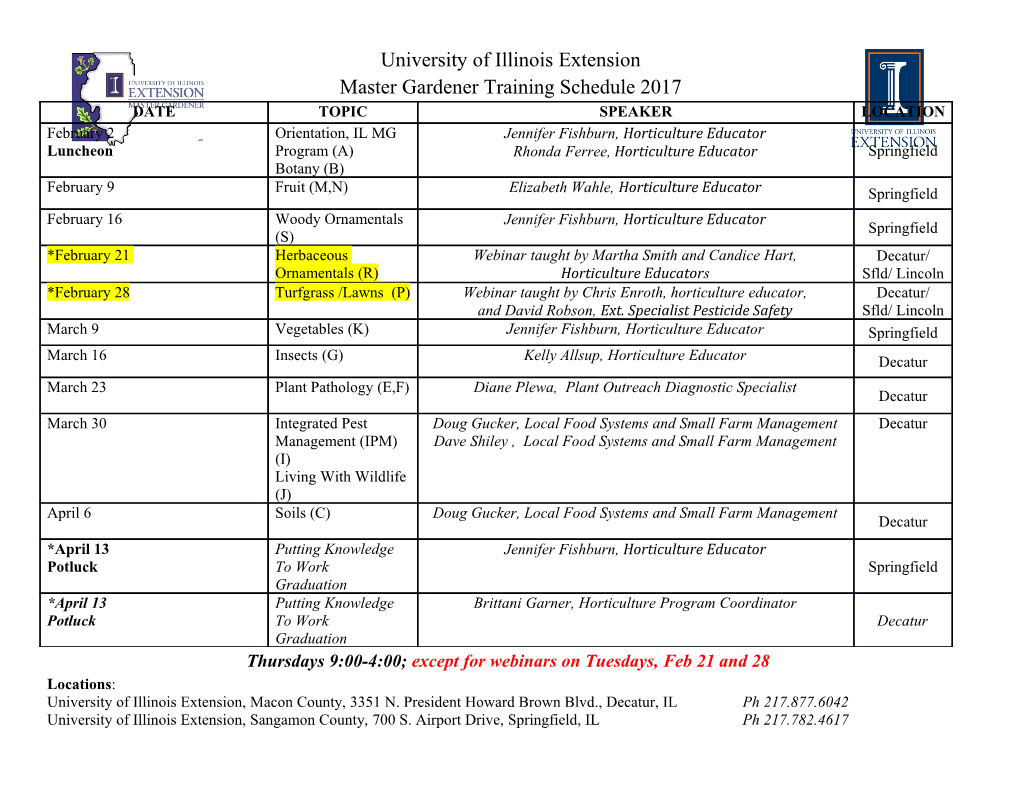
INTRODUCTION TO STEREOLOGICAL PRINCIPLES George F. Vander Voort1 Although the fundamental relationships for stereology, the foundation of quantitative metallography, have been known for some time, implementation of these concepts has been restricted when performed manually due to the tremendous effort required. Further, while humans are quite good with pattern recognition, as in the identification of complex structures, they are less satisfactory for repetitive counting. Many years ago, George Moore (1) and members of ASTM Committee E-4 on Metallography conducted a simple counting experiment. About 400 people were asked to count the number of times the letter ―e‖ appeared in a paragraph without striking out the letters as they counted. The correct answer was obtained by only 3.8% of the people. Results were not Gaussian, however, as only 4.3% had higher values while 92% had lower values, some much lower. The standard deviation was 12.28. This experiment revealed a basic problem with manual ratings. In this case the subject was one very familiar to the test subjects, yet only 3.8% obtained the correct count. What degree of counting accuracy can be expected when the subject is less familiar, such as microstructural features? Image analyzers, on the other hand, are quite good at counting but not as competent at recognizing features of interest. Fortunately, there has been tremendous progress in the development of powerful, user-friendly image analyzers over the past two decades. Chart methods for rating microstructures have been used for many years to evaluate microstructures, chiefly for conformance to specifications. At this time, true quantitative procedures are replacing chart methods for such purposes and they are gaining usage in quality control and research studies. Examples of the applications of stereological measurements have been reviewed by Underwood (2). Basically, two types of measurements of microstructures are made. The first group includes measurements of depths i.e., depth of decarburization, depth of surface hardening, or thickness of coatings or platings. These measurements are made at a specific location (the surface) and may be subject to considerable variation. To obtain reproducible data, these surface conditions must be measured at a number of positions on a given specimen and on several specimens if the material being sampled is rather large. Standard metrology methods are used and these can be automated. Metrology methods are also used for individual feature analysis of particle size and shape measurement. The second group of measurements belongs to the field referred to as stereology. This is the body of measurements that describe the relationships between measurements made on the two-dimensional plane of polish and the characteristics of the three- dimensional microstructural features sampled. To facilitate communications, the International Society for Stereology (ISS) has proposed a standard system of notation, as shown in Table 1 (3). This table lists the most commonly used notations; there are other, newly developed procedures where the notation has not been standardized. 1 Consultant, Struers Inc. These measurements can be made manually with the aid of templates outlining a fixed field area, systems of straight or curved lines of known length, or a number of systematically spaced points. The simple counting measurements, PP, PL, NL, PA and NA, are most important and are easily made. These measurements are useful by themselves and can be utilized to derive other important relationships. These measurements can also be made using semi-automatic tracing tablets or automatic image analyzers. In this chapter, the basic rules of stereology are described with emphasis on how these procedures are applied manually. Other chapters describe how these ideas can be implemented using image analysis. Image analysis users should understand these principles before using them. When developing a new measurement routine, it is good practice to compare image analysis data with data developed manually. It is easy to make a mistake in setting up a measurement routine and one needs a check against such occurrences. SAMPLING Sampling of the material is an important consideration as the measurement results must be representative of the material. Ideally, random sampling would be best, but this can rarely be performed, except for small parts like fasteners where a specific number of fasteners can be drawn from a production lot at random. However, with a large forging or casting, it is generally impossible to select specimens at random from the product mass and test specimens are generally taken from excess material added to the bulk for such purposes. For a casting, it may be possible to trepan sections at locations that will undergo machining at some later step. The practice of casting a small ―keel block‖ for test specimens may produce results markedly different than would be obtained from the casting if there is a large difference in size, solidification and cooling rates. After the specimens are obtained, there is still a sampling problem, particularly in wrought material. Microstructural measurements made on a plane parallel to the deformation axis will often be quite different from those taken on a plane perpendicular to the deformation axis, especially for features such as nonmetallic inclusions. In such cases, the practice is to compare results on similarly oriented planes. Few people have the time to measure the microstructural feature of interest on the three primary planes in a flat product, such as plate or sheet, so that the true three-dimensional nature of the structure can be determined except, perhaps, in research studies. The sampling plan must also specify the number of specimens to be tested. In practice, the number of specimens chosen is a compromise between minimizing testing cost and the desire to perform adequate testing to characterize the lot. Excessive testing is rare. Inadequate sampling is more likely due to physical constraints with some components and a desire to control testing costs. In the case of inclusion ratings, the testing plan was established years ago by the chart method, ASTM E 45. The procedure was to sample billets at locations representing the top and bottom, or top, middle and bottom, of the first, middle and last ingots on a heat. The plane of polish is longitudinal 2 (parallel to the hot working axis) at the mid-thickness location. This yields six or nine specimens. The area examined is 160 mm2 per specimen, i.e., 960 or 1440 mm2 for 6 or 9 specimens, respectively. This small area would establish the inclusion content and would be the basis for decisions as to the marketability of a heat of steel that could weight from 50 to 300 tons. For bottom poured heats, there is no first, middle and last ingot and continuous casting eliminates ingots. So alternate sampling plans are needed. In the writer’s work with inclusion testing, characterization was improved by the use of at least 18 or 27 specimens per heat where the surface, mid-radius and center locations at each billet location (top and bottom or top, middle and bottom of the first, middle and last top poured ingots, or three ingots at random from a bottom poured heat). SPECIMEN PREPARATION In the vast majority of work, the measurement part of the task is quite straightforward and 90% or more of the difficulty is in preparing the specimens properly so that the true structure can be observed. Measurement of inclusions is done on as- polished specimens as etching only brings out other extraneous details that may obscure the detection of the inclusions. Measurement of graphite in cast iron is also performed on as-polished specimens. But, it is possible that shrinkage cavities, which are often present in castings, may cause interference with detection of the graphite as they have overlapping gray scales. When the specimen must be etched to see the constituent of interest, it is best to etch the specimen so that only the constituent of interest is revealed. Selective etchants are best. Preparation of specimens today is easier than ever with the introduction of automation in sample preparation equipment. Specimens prepared with automated devices exhibit better flatness than manually prepared specimens. This is especially important if the edge must be examined and measurements performed. The preparation sequence must establish the true structure, free of any artifacts. Automated equipment can produce a much greater number of properly prepared specimens per day than the best manual operator. Specimen preparation is discussed elsewhere in this text. VOLUME FRACTION It is well known that the amount of a second phase or constituent in a two-phase alloy can have a significant influence on its properties and behavior. Consequently, determination of the amount of the second phase is an important measurement. The amount of a second phase is defined as the volume of the second phase per unit volume, or volume fraction. There is no simple experimental technique for measuring the volume of a second phase or constituent per unit volume of specimen. The closest approach might be to use an acid digestion method. A cube of metal is weighed and then partially dissolved in an appropriate electrolyte that dissolves the matrix but not the phase of interest. The residue is cleaned, dried and weighed. The remains of the cube (after cleaning and drying) are weighed and the weight loss is calculated. The weight of the 3 undissolved second phase is divided by the weight loss to get an estimate of the volume fraction of the second phase knowing the densities of the matrix and second phase. This is a tedious method, not applicable to all situations, and subject to interferences. Three experimental approaches for estimating the volume fraction have been developed using microscopy methods: the area fraction, the lineal fraction and the point fraction. The volume fraction was first estimated by areal analysis by Delesse, a French geologist, in 1848.
Details
-
File Typepdf
-
Upload Time-
-
Content LanguagesEnglish
-
Upload UserAnonymous/Not logged-in
-
File Pages22 Page
-
File Size-