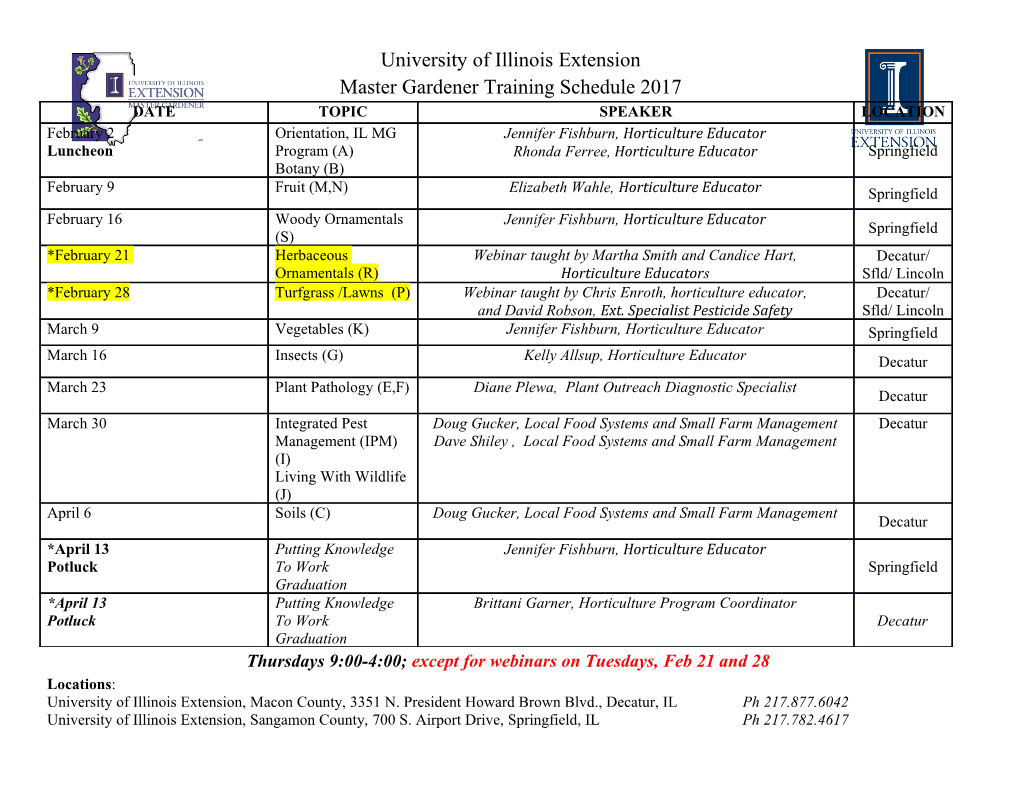
View metadata, citation and similar papers at core.ac.uk brought to you by CORE provided by UTHM Institutional Repository DESIGN AND SIMULATION BY USING SMART POWER MODULE (SPM) TO INCREASE EFFICIENCY IN MOTOR DRIVE APPLICATION SOFWAN BIN RAMLI A project report submitted in fulfillment of the requirement for the award of the Degree of Master of Electrical Engineering Faculty of Electrical and Electronic Engineering Universiti Tun Hussein Onn Malaysia DECEMBER 2013 ABSTRACT Motors are the major source of energy consumption in appliances. Since governmental and agency regulations continue to mandate reduced energy consumption, inverter technology is being increasingly accepted and used by a wide range of users in the design of their products. Power modules for inverterized motor drive applications are also part of a current trend due to the advantages that offer such as space-savings and ease of assembly. Integrated power modules seem to be the solution chosen by most researchers, designers or producers in the field of motor drive applications. Fairchild Semiconductor has developed a series of Smart Power Module (SPM®) devices for a highly efficient integrated solution. They concentrate on the development of an intelligent integrated power module using the new concept of building structure and advanced packaging technology that is the means of achieving an excellent, cost-effective solution. This module offers tremendous advantages such as increased reliability, design flexibility, simple construction, easy assembly, increase motor efficiency and cost-effectiveness of the inverter power stage for home appliance applications. The objective of this project is to perform simulation of SPM® via Fairchild Motion Design Tool and analysis the data by using switching loss calculation design tool via Microsoft excel to determine the efficiency of MOSFET and IGBT in smart power module. In this thesis, there will be further explanation about IGBT and MOSFET, Brushless DC motor (BLDC), Universal motor, motor efficiency and power loss. iii CONTENTS Page DECLARATION i ACKNOWLEDGEMENT ii ABSTRACT iii CONTENTS iv LIST OF FIGURES viii LIST OF TABLE x LIST OF GRAPH x LIST OF SYMBOLS AND ABBREAVIATIONS xi CHAPTER I : INTRODUCTION 1.1 General Background of Electric Motor 1 1.2 Universal Motor 3 1.2.1 Properties of Universal Motor 3 1.2.2 Applications of Universal Motor 5 1.3 DC Motor 7 1.3.1 Brush DC Motor 7 1.3.2 Brushless DC Motor 8 1.3.3 Permanent magnet stators 8 1.4 Smart Power Module (SPM) 9 1.5 Problem Statement 11 1.6 Objectives and Scopes 11 1.6.1 Objective 11 1.6.2 Scope of Work 12 1.6.3 Thesis Overview 13 CHAPTER II : LITERATURE REVIEW 2.1 Introduction 14 iv 2.2 Direct Current Motor (DC Motor) 14 2.2.1 Principle of DC Motor 14 2.2.2 Detailed Description of a DC Motor 16 2.2.3 Working or Operating Principle of DC Motor 18 2.2.4 Construction of DC Motor 22 2.2.5 Permanent magnet stators 23 2.2.6 Electrical connections between the stator and rotor 24 1) Series connection 24 2) Shunt connection 25 3) Compound connection 25 2.3 Electricity consumption by electrical motor systems 26 2.4 Motor Efficiency 28 2.5 Brushless DC Motors (BLDC) 30 2.5.1 Brushless vs. brushed motors 31 2.5.2 Controller implementations 32 2.5.3 Variations in construction 33 2.5.4 Applications of BLDC 34 2.6 Improving Energy Efficiency and Reliability in Motor Control Applications 38 2.7 Electric Motor Efficiency 39 2.7.1 Fairchild Product Solutions for Motor Control Applications 40 2.7.2 Motion SPM® (Smart Power Modules) 40 2.8 FSBF10CH60B Smart Power Module 41 2.8.1 General Description 41 2.8.2 Features 41 2.8.3 Applications 41 2.8.4 Physical structure of SPM 42 2.9 Insulated Gate Bipolar Transistor (IGBT) and MOSFET 45 2.10 Fairchild Motion Control Design Tool 47 v CHAPTER III: METHODOLOGY 3.1 Fairchild Motion Control Design Tool 48 3.1.1 Input-Output Description 48 3.1.2 Simulation on 3-Phase PWM Inverter Loss & Temperature Analysis for SPM2 50 3.2 Fairchild Power Train Discrete - Device Power Loss and Analysis 51 3.2.1 Power Factor Correction; AC Input 51 3.2.2 Offline & Isolated DC-DC; AC Input 51 3.2.3 Non-Isolated DC-DC; DC Input 51 3.2.4 Simulation on MOSFET FDS8884 52 3.3 Switching Loss Calculation Design Tool 53 3.4 Project Methodology 53 3.5 Project Flow Chart 54 CHAPTER IV: DATA ANALYSIS AND RESULTS 4.1 Simulation on 3-Phase PWM Inverter Loss & Temperature Analysis 55 4.1.1 Input parameter that being used in this project 55 4.1.2 Simulation result of SPM2 56 4.2 Simulation on MOSFET FDS8884 63 4.2.1 Input parameter that being use in this project 63 4.2.2 Simulation result for MOSFET FDS8884 64 4.3 Switching Loss Calculation Design Tool 67 CHAPTER V: DISCUSSION AND ANALYSIS 5.1 Introduction 68 5.2 Program output from simulation of SPM 69 5.2.1 Summary table 69 5.2.2 Data Used in the Simulation 70 vi 5.2.3 Junction Temperature versus Time 70 5.2.4 Distribution of Losses 71 5.2.5 IGBT and MOSFET Temperature rise versus RMS Phase Current 72 5.2.6 Total Module Loss and Maximum Allowable Case Temperature versus RMS Phase Current 72 5.2.7 Total Module Loss and Maximum Allowable Case Temperature versus Switching Frequency 73 5.2.8 Thermal Resistance Limited by Tj and Thermal Resistance Limited by Ts versus RMS Phase Current 73 5.2.9 Modulation Signal and Current versus Time 74 5.3 Electric Motor Efficiency 74 5.4 Smart Power Module 75 5.5 Conclusion 77 REFERENCES 78 APPENDIX A 81 APPENDIX B 84 vii List of Figure Page Figure 1: Various electric motors, compared to 9 V battery 2 Figure 2: Universal motor of a vacuum cleaner 6 Figure 3: A brushed DC electric motor 9 Figure 4: Smart Power Module 10 Figure 5: Flow Diagram 12 Figure 6: Fleming left hand rule 15 Figure 7: Principles of DC motor 15 Figure 8: Electric current flow in DC motor 16 Figure 9: Basic construction of a dc motor 18 Figure 10: Fleming left hand rule 18 Figure 11: Principle of DC motor 19 Figure 12: Basic principle of DC motor 21 Figure 13: Torque of DC motor 21 Figure 14: Basic principle of DC motor 22 Figure 15: Construction of dc motor 23 Figure 16: Motor from a 3.5" floppy disk drive 30 Figure 17: Category and Trend of Motor Technology 37 Figure 18: EMDS energy consumption by sector 38 Figure 19: Energy efficient motor strategy 39 Figure 20: Fairchild motor control 40 Figure 21: Top and bottom view of SPM 42 Figure 22: Pin configuration of SPM 43 Figure 23: Pin descriptions of SPM 43 Figure 24: Typical VCE(SAT) (Collector-to-Emitter Voltage) Comparison of IGBT 45 Figure 25: Typical Turn-Off Switching Power Loss (at TJ=25°C, 125°C) Comparison of IGBT 45 Figure 26: Output Characteristics of a MOSFET BUZ 312 (1000 V) 46 Figure 27: Output Characteristics of an IGBT BUP 314 (1000 V) 46 viii Figure 28: Fairchild motion SPM tool 47 Figure 29: Example for input parameter 47 Figure 30: Input parameter for simulation SPM2 50 Figure 31: Input parameter for simulation MOSFET 52 Figure 32: Efficiency summary from simulation of MOSFET 53 Figure 33: Flow chart of this project 54 Figure 34: Characteristic for SPM2 55 Figure 35: Input parameter for simulation of SPM2 56 Figure 36: Output value from simulation of SPM2 56 Figure 37: Output value from simulation of SPM2 57 Figure 38: High-Side IGBT or MOSFET losses and junction temperature versus time 57 Figure 39: Low-Side IGBT or MOSFET losses and junction temperature versus time 57 Figure 40: High-Side diode losses and junction temperature versus time 58 Figure 41: Low-Side diode losses and junction temperature versus time 59 Figure 42: High-Side conduction and switching losses 59 Figure 43: Low-Side conduction and switching losses 60 Figure 44: Average IGBT or MOSFET and Diode junction temperature rise versus RMS motor phase current 60 Figure 45: Average IGBT or MOSFET and Diode junction temperature versus RMS motor phase current 61 Figure 46: Total module loss and maximum allowable module case temperature versus RMS motor phase current 61 Figure 47: Total module loss and maximum allowable module case temperature versus module switching frequency 62 Figure 48: Maximum allowable heatsink thermal resistance 62 Figure 49: Modulation signal (green trace) and High-Side IGBT/MOSFET or Low-Side diode current (blue trace) vs. time 63 Figure 50: Input parameter for simulation MOSFET FDS8884 63 ix Figure 51: Schematic diagram for simulation MOSFET FDS8884 64 Figure 52: Output waveform 64 Figure 53: Input waveform 65 Figure 54: Switching waveform 65 Figure 55: Efficiency of MOSFET FDS8884 66 Figure 56: Power loss of MOSFET FDS8884 66 Figure 57: Efficiency summary table 67 Figure 58: Efficiency chart 67 Figure 59: Input parameter for simulation of SPM2 69 Figure 60: Output value from simulation SPM2 69 Figure 61: Distribution of losses 71 Figure 62: Characteristic of IGBT and MOSFET 72 Figure 63: Total module loss 72 Figure 64: Total module loss 73 Figure 65: Maximum allowable heat sink 73 Figure 66: Modulation signal 74 Figure 67: Energy efficiency statistic 74 Figure 68: Efficiency of SPM 75 Figure 69: IGBT characteristic 76 List of Table Page Table 1 : Comparison of Motor Trend Technology 41 Table 2: Collector-Emitter Saturation Voltage & IGBT Turn-On/Off Switching Loss 48 List of Graph Page Graph 1: High-Side IGBT 70 Graph 2: Low-Side IGBT 70 Graph 3: High-Side diode losses 71 Graph 4: Low-Side diode losses 71 x List of Symbols and Abbreaviations DC Direct Current AC Alternating Current SPM Smart Power Module RPM Rounds Per Minute EMI Electromagnetic Interference EMF Electromagnetic Field PM Permanent Magnet Hz Hertz IGBT Insulated Gate Bipolar Transistor RMS Root Mean Square BLDC Brushless Dc Motors PWM Pulse-Width Modulation VCE Collector-To-Emitter Voltage N.C Normal Condition S.F.C Single Fault Condition µ Micro kW Kilo Watt FDT Fairchild Design Tools IEC International Electrotechnical Commission EMDS Electric Motor Drive Systems HVAC Heating And Air Conditioning HVIC High-Voltage Integrated Circuit PT Punch Through NPT Non Punch Through BJT Bipolar Junction Transistor PMSM Permanent Magnet Synchronous Motors xi CHAPTER I INTRODUCTION 1.1 General Background of Electric Motor An electric motor is an electric machine that converts electrical energy into mechanical energy.
Details
-
File Typepdf
-
Upload Time-
-
Content LanguagesEnglish
-
Upload UserAnonymous/Not logged-in
-
File Pages38 Page
-
File Size-