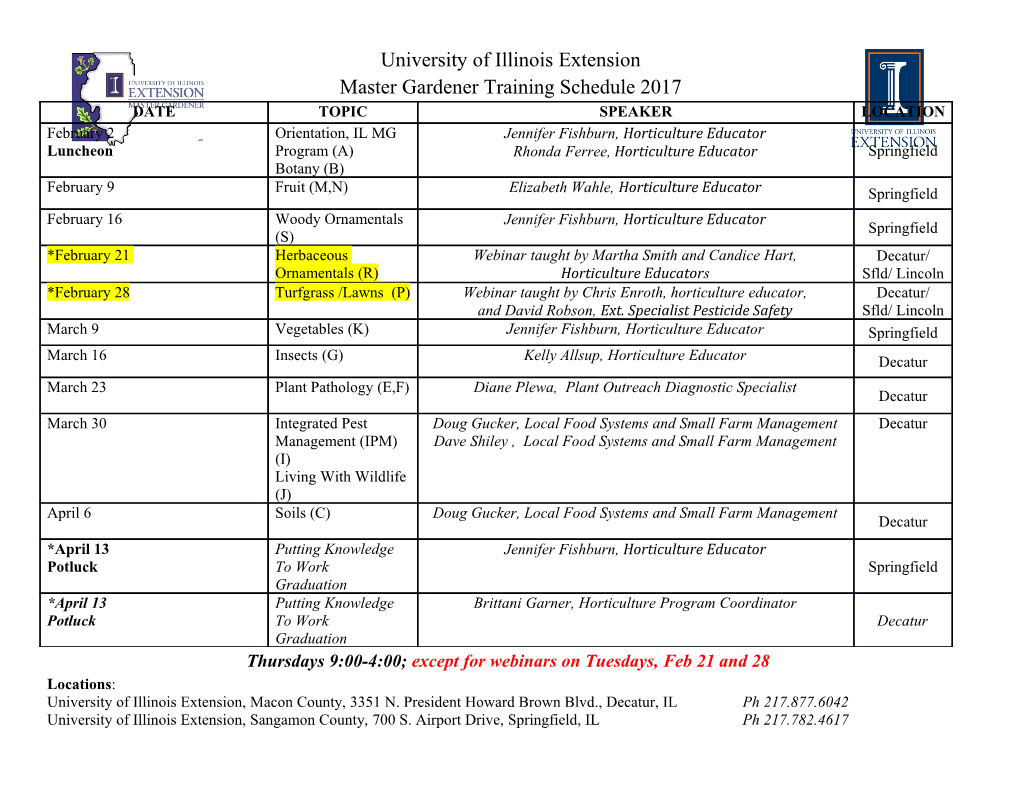
I-STIR™ Friction Stir Welding Solutions Ensure the successful transition of FSW from your laboratory to your production floor. R EALIZETHE P ROMISEOF F RICTION S TIR W ELDING such factors as budgetary limitations, time constraints, and your organization’s level of FSW process development expertise, you You have recognized the promise of friction stir welding (FSW)- must choose a realistic approach that is appropriate to your specific circum- the potential benefits of this rapidly maturing technology are stances – a faulty strategy will prove costly numerous: reduced assembly costs, higher quality joining, and time-consuming. stronger and lighter joints, less pollution, and significantly I-STIR Technology: A Uniquely Qualified reduced production cycle times. Bringing FSW to the production floor, how- FSW Solution Provider ever, is neither a simple nor risk-free As a leading provider of precision force and endeavor. Successfully implementing this motion control systems and recognized rapidly evolving process requires consider- innovator of cutting edge FSW technology, able process expertise, a sound develop- I-STIR Technology is uniquely qualified to ment plan, and reliable, technologically help you mitigate these risks and formulate advanced equipment. Carefully weighing a sound FSW process development strate- gy. We can provide you with the level of FSW process development expertise that you require to understand the full benefits of this promising technology, explore its feasibility for a given applica- tion, and create and implement a sound process development strategy that meets your organization’s unique needs within the constraints of available technology, time and budget. Your solution may entail the formulation and implementation of a detailed FSW process development plan, the delivery of one of our proven develop- ment systems, a transfer of technology, or merely the performance of a feasibility study. No matter what your needs, I-STIR Technology is the best-qualified organiza- tion to ensure the successful transition of FSW from your laboratory to your produc- tion floor. I-STIR Technology is a leading provider of precision force and motion control systems and a recognized innovator of cutting edge FSW technology. 2 I-STIR™ Friction Stir Welding Development Model From our deep understanding of complex FSW processes and tooling gained from a wide variety of development efforts we have developed Intelligent Stir Welding for Industry and Research (I-STIR), an FSW development model that employs an inter-organizational team approach and a progressive three-phase program to put FSW into production as efficiently and cost- effectively as possible. Employing the I-STIR model, we can equip you with the world’s most versatile and reliable FSW development systems and, if necessary, We employ a progressive three-phase pro- provide additional levels of guidance to gram to help you put FSW into production ensure the successful transition as efficiently and cost-effectively as possible. of FSW from your laboratory to your production floor. The I-STIR model’s progressive, phased Collaborative Team Approach controls, and process knowledge required development program is based upon a best One of the primary strengths of the I-STIR to move the friction stir welding process practices model developed through decades model is its team approach to friction stir past the laboratory stage and into produc- of producing complex, turnkey systems. welding development, which emphasizes tion. Team members from both organiza- Adapted for friction stir welding, this pro- the free and efficient flow of ideas and tions are encouraged to maintain frequent, gram consists of three phases: Application information. You supply design, analysis, direct contact with their counterparts to Assessment, Process Development & materials and process engineering expertise review the various design and manufactur- System Design, and Implementation for specific to your industry, while I-STIR ing program aspects. Production. Technology provides the critical design, PHASE IPHASE II PHASE III Application Assessment Process Development & System Design Implementation for Production •Customer •Requirements •Design Concept •Weld •Customer Specifications Specifications •Experience Specifications Specifications •Analysis •Analysis •Drawings •Functional NPUT •Experience •Experience •Experience Specifications I •Experience System Conceptual Detail Design/ Fabrication/ Process Installation/ Product Requirements Design Certification Preparation Development Activities •Requirements • Design Concept •Drawings •FSW System •Accepted System Specification •Weld •Specification •Certified Processes •Output Specifications Updates UTPUT •Process O Modifications 3 V ERSATILE I-STIR™ F RICTION S TIR W ELDING E QUIPMENT I-STIR Technology has developed an array of leading-edge friction stir welding systems capable of providing the advanced capability and versatility required for research, process development, prototyping and production: The I-STIR PDS (Process Development System) solution is a fully instrumented research system that is capable of simultaneous force-controlled operation of three independent axes (X, Z, and Pin). This system features Adaptable Adjustable Pin Tool (AdAPT™) weld head technology, enabling it to perform self-reacting welds and join materials of varying thickness. The I-STIR PDS can support up to 5 DOF to produce welds with double curvature. The I-STIR PDS has successfully joined materials less than 1mm and up to 40mm in thickness. The I-STIR PDS Jr. solution is a single-axis system designed to perform linear welds. As a lower cost alternative to I-STIR PDS, this system features many of the same innovations as the PDS solution, such as AdAPT weld head technology. The PDS Jr. has been deployed to perform process research. The I-STIR™ 10 Gantry is a 5-DOF system capable of producing parts requiring multi-axis welding. This system features AdAPT™ weld head technology and a 10-ton forge load capacity, which is needed for thicker section welds and hard metals. The I-STIR Aero system is a 5-DOF system for use with thin-gauge aluminum alloys. Capable of pro- ducing high-speed welds of complex contours, this system features data collection of all critical param- eters so that Statistical Process Control (SPC) can be used to ensure quality. The system’s control software is compatible with most standard CAM programs. The I-STIR Aero system is also capable of performing basic machining tasks such as drilling, trimming and rough machining. F LEXIBLE I-STIR™ GUIDANCE Early in the design cycle of the Following the I-STIR development model, a Eclipse 500 jet aircraft, Eclipse Aviation powerful team of aircraft design and FSW Corporation explored the efficiency and process development talent was assembled. reliability of using friction stir welding in Eclipse supplied the critical design, analy- the production of primary aircraft struc- sis, materials and process engineering tures. By successfully integrating FSW into expertise to address the service-life details Solution Profile: the production of the Eclipse 500 the com- of the aircraft; and I-STIR Technology sup- Eclipse Aviation Corporation pany could eliminate 60 percent of the plied the design, controls, and process rivets from the aircraft’s design, resulting expertise needed to move the FSW process We can work closely with you from the out- in reduced assembly costs, better quality past the laboratory stage and into produc- set, guiding you through application assess- joining and stronger and lighter joints. tion. Using the I-STIR PDS, the team pro- ment, process development, and implemen- Because FSW is significantly faster than duced thousands of development welds & tation for production to ensure that the other structural joining processes the air- prototype panels in support of the FAA cer- process you implement and the equipment craft’s cycle time in production would tification effort. you deploy are the best possible match for decrease drastically as well. your unique FSW application. This collaboration yielded the first produc- tion application of friction stir welding technology for the fabrication of primary The I-STIR Aero system represents the world’s first aircraft structures, the I-STIR Aero system. production application of friction stir welding technol- This 5-DOF system features AdAPT™ weld ogy for the fabrication of primary aircraft structures. head technology and is capable of produc- ing high-speed welds of complex contours in thin-gauge aluminum alloys. The sys- tem’s control software is compatible with most standard CAM programs, and additional sensors enable data collection of all critical parame- ters so that Statistical Process Control (SPC) can be used to ensure weld quality. Eclipse Aviation has since used the system to manufacture many of the skin assemblies on the Eclipse 500. The successful joining of these first components represents a major step forward in the validation and certification of friction stir welding in the assembly of this aircraft. Photos courtesy of Eclipse Aviation Corporation 4 The Universal Weld System (UWS) is Solution Profile: capable of producing Universal Weld System precise, high quality friction stir welds on We can play a supporting role, augmenting complex curvature your in-house process development expert- components. ise in whatever consultive capacity you require to ensure that you deploy the best possible equipment for your unique FSW application. When Lockheed
Details
-
File Typepdf
-
Upload Time-
-
Content LanguagesEnglish
-
Upload UserAnonymous/Not logged-in
-
File Pages14 Page
-
File Size-