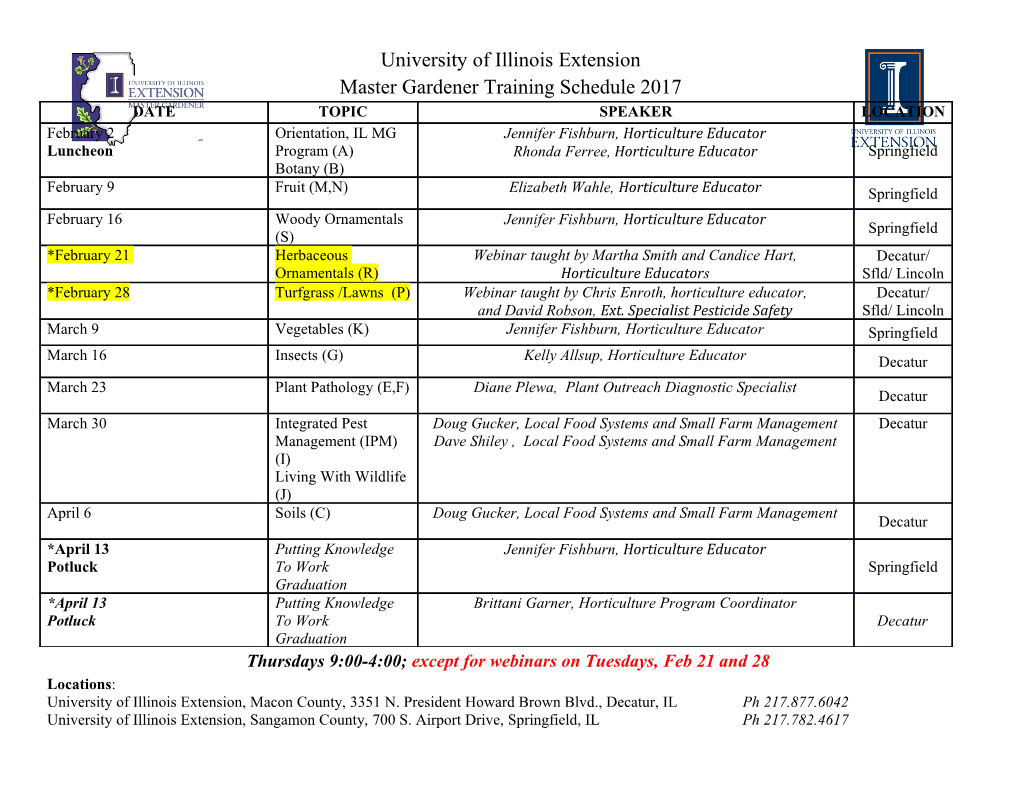
A LATHE-TURNED DRUM SET Jeff Salter umans have been crafting nineteenth century, drum manufac- portions before it would swing freely drums since prehistoric times. turers such as Leedy, Ludwig, Rogers, on the lathe. H Early drums were rudimen- and Gretsch were making modern An Internet search produced a table tary, consisting of a membrane, usu- drums a part of the fabric of our soci- listing dimensional shrinkage values ally animal skin, stretched over some ety. Now, after a fascinating two-year for various species of wood. We turned sort of hollow shell. Originally, drum project, I’m proud to count myself as a cylinder 19" (48cm) in diameter in the shells were carved out of logs. In the a member of this illustrious fraternity hopes of yielding an 18" (46cm) bass eighteenth century, drum builders of drum builders. drum after drying and final machin- began steam-bending thin plies of I’ve been drumming for about as ing. With the blank roughed to size wood into cylindrical shells. By the long as I’ve been woodworking, and (Photo 1), we cut a series of concentric since the earliest days, my friends have cylinders using the McNaughton coring asked, “Why not make your own drum tool fitted with a straight blade. We Rough-turn the log set?” In January 2013, everything I quickly found the dangers of plunging needed was in place to realize that the tool into endgrain by hand, when a goal, to create a drum set of solid wood massive catch ripped the cylinder from shells cored from a single cherry log. the tailstock and faceplate. We remounted the cylinder, and I Roughing the drum shells rigged up a machinist’s slide to hold the One of my woodturning buddies, Bert slicing tool (Photo 2). This improvement Olton, obtained a 24"- (61cm-) diam- provided greater control of the feed rate eter cherry log and had it delivered and cutting action by securely holding to the Huron Valley Woodturners the cutter exactly on center. The cutter club in Ann Arbor, Michigan, where produced a spray of wet sawdust as it several club members helped mount cut into the log. We found we needed a large piece onto Russ Clinard’s to clear the kerf with compressed air to large-capacity lathe. We mounted the keep the blade from binding as it pro- 1 heavy green blank on a large face- gressed deeper into the blank. A freshly cut cherry log is trued on plate and engaged the tailstock for Each coring cut was made halfway the lathe. support. The blank was so large, we through from one side before turning needed to use a chain saw to remove the piece around to cut from the other 26 American Woodturner June 2016 Copyright 2016, American Association of Woodturners. All rights reserved. 26_Drumset.indd 26 5/3/16 2:38 PM FEATURE Cut the drum shells 2 3 4 The author’s shopmade machinist’s sled, After cutting halfway in, the log is reversed so The author with his drum shells in securely holding a long, straight cutting tool, the cut can be completed from the other end. progress. Notice how the grain travels provides the needed stability and control for Shims at the headstock end provide stability vertically rather than horizontally, as on slicing deep into the log’s endgrain. during the cut. commercially made laminate drums. side. For added safety, prior to making the corner of the basement. Two years interior using a tool with a ring-type the final plunge cut on the outermost later, I set upon the task of machin- cutter and chip breaker to limit the shell, I inserted shims into the kerf on ing the shells to their final diameter depth of cut. the headstock side to support the shell and wall thickness. I began with the I cut the outside diameter to fit a as it broke free (Photo 3). We continued smaller shells. They dried slightly out commercially made Mylar® drumhead in this manner until all the shells were of round, so I mounted them to the (Photo 6). Commercial drumheads are cut (Photo 4). lathe with a loose-fitting jam chuck so made in full inch increments and fit as to not distort their shape. I secured over drum shells ⅛" (3mm) smaller Re-turning the shell to a wooden jam chuck using than the head size. With the outside I took the shells home, recorded their shims, a few corner blocks, and some cut to final dimension, I returned diameter, and left them to air dry in hot-melt glue (Photo 5). I trued up the to the inside and cut the final wall Remount and finish-turn After air drying, the out-of-round drum shells are remounted using a jam chuck. The outside and inside are turned true and reduced to the final wall 5 6 7 thickness, 5⁄16". woodturner.org 27 Copyright 2016, American Association of Woodturners. All rights reserved. 26_Drumset.indd 27 5/4/16 10:01 AM True the outside surface The author’s shopmade jig, a specialized router table, holds the largest drum shells, which are too big for his lathe. To true the outside surface, the drum is rotated on an axle so that it passes over a router bit protruding upward. 8 9 thickness to 5⁄16" (8mm) and added a ride on the axle and are used to both position the rails parallel to the rota- 45-degree bearing edge with a slight clamp the shell in place and act as a tional center of the shell to ensure back cut where the drum head would sizing template (Photo 8). The shell the router would cut a uniform wall seat (Photo 7). I sanded both the inside was cut to a true cylinder by rotating thickness as it tracked from one end and outside before removing the drum it above a ½" (13mm) router bit and to the other. With each rotation, I from the lathe. shifting the sled laterally with each shifted the router laterally and cut revolution. This process continued a surface concentric to the exterior Router jigs until the shell diameter matched the surface. I repeated this process, The 16" (41cm) floor tom and 18" bass template (Photo 9). taking light cuts until I reached drum were too large to mount to my The setup for machining the inte- a final wall thickness of 5⁄16". The lathe. So I constructed a couple of rior consisted of a couple of angle routing process left the surfaces quite router setups to do the final machin- iron rails and a cradle made up of rough, requiring several hours of ing. The setup for machining the four roller-skate wheels. The angle sanding before I was happy with the exterior consisted of a sled with an iron was positioned to guide the surface quality. axle set at the appropriate center router laterally while the exterior of height for each shell. Two plywood the shell rolled on the roller-skate Trim and sand disks, cut to the final shell diameter, wheels (Photo 10). I was careful to To cut the shells to length, I used the table saw with the roller-skate cradle affixed to the top (Photo 11). I started the saw with the blade fully retracted True the inside surface below the table, then raised it up and A router and rail system is used to rotated the shell atop the roller-skate true the inside wheels, being sure to hold the shell of the largest drum shells and against the saw’s fence. I then added a bring the wall to 45-degree bearing edge to the shells at final thickness. The drum shell the router table. rotates on roller- After final sanding, the shells skate wheels. were ready for finishing with instrument-grade lacquer, expertly applied by my friend Brian Lenehan. The shells received several sealing coats of lacquer prior to hand sanding and then another five finish coats, followed by more hand 10 sanding and buffing to produce a high luster. 28 American Woodturner June 2016 Copyright 2016, American Association of Woodturners. All rights reserved. 26_Drumset.indd 28 5/3/16 2:38 PM FEATURE Drum hardware with the adhesive used to bind the “Yeah, man, it’s a cool kit—they really I fitted each shell with twelve or plies together, limit their resonance. are fantastic.” sixteen drum lugs, depending on Solid shells, not inhibited in this What started as a lofty goal spurred its size. I chose to apply arch-style way, lend themselves to a more on by friends through the years has led lugs, which I purchased from Drum organic sound, warm tone, and to the creation of a one-of-a-kind, state- Foundry (drumfoundry.com). Using sensitivity that sounds good at of-the-art drum set that will live on as a circular template, I marked the posi- any volume. a family heirloom. Undoubtedly, the tion of the lug mounting holes over Admittedly, I am biased, so I brought drums contain the spirit of the majestic blue painter’s tape (Photo 12). After I the set to a nationally renowned drum cherry tree from which they came, but carefully drilled all the holes, it was shop in Naperville, Illinois, Maxwell they also sing the names of all those who time to put it all together. Assembling Drums, for an expert opinion. participated in their birth. No one singu- all those lugs took a long time, but the Graciously, Steve Maxwell, Jr., agreed lar skill was required for this project, but excitement of finishing the project to give them a critique.
Details
-
File Typepdf
-
Upload Time-
-
Content LanguagesEnglish
-
Upload UserAnonymous/Not logged-in
-
File Pages4 Page
-
File Size-