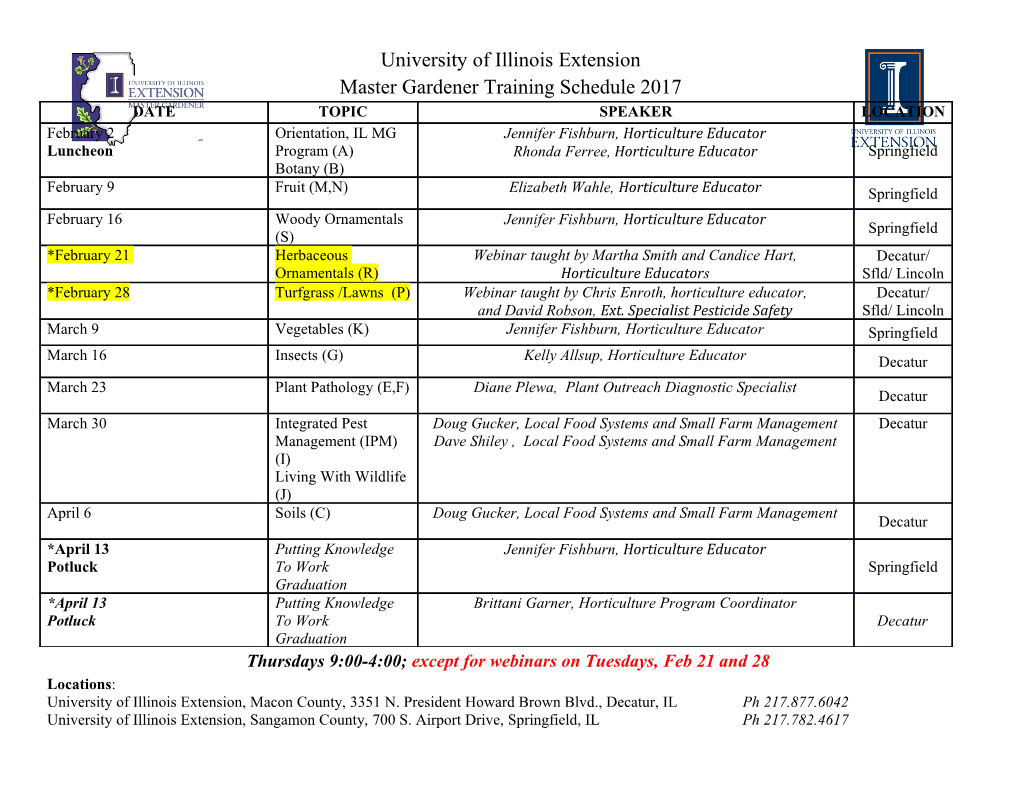
Lasers in Manufacturing Conference 2015 Flow diagnostics produced by selective laser melting of cutting nozzles S.Ulricha, S.Lorenza S. Jahna, S.Sändiga, B.Fleckb aGünter-Köhler-Institut für Fügetechnik und Werkstoffprüfung GmbH bErnst-Abbe-Hochschule Jena Abstract The increasing spread of laser technology in materials processing leads inter alia increasingly individual solution strategies in order to cope with the growing demands on the process control. The focus of this work is the fluidic analysis of the cutting nozzles, which were usually produced either by selective laser melting or conventional methods. The Schlieren measurement was utilized in order to visualize flows. Through the adjustment of optical components, the Schlieren-Aufnahmegerät 80 was coupled with a high speed camera. Based on these measurement results, the influence of manufacturing technology has been evaluated on the flow behaviour. With the help of cutting tests a direct proof of the achievable quality of the cutting edge has been evaluated. The results from both research methods provide a statement on the quality of the gas stream and the achievable cutting quality of manufacturing technology. Keywords: laser cutting, selektiv laser melting, nozzle, flow visualization 1. Introduction Nowadays, the decisive factors for financial success are on the one hand innovative products, and on the other hand the acquisition of knowledge through research and development. In materials processing, the application of lasers in technological fields like cutting and welding, enables shorter lead times. The understanding of the process plays a crucial role for the quality of the component. Regarding cutting, the quality of the cut edge and the dimensional accuracy is affected by many parameters. Among others, the quality of the gas jet has been identified as a crucial factor determining the efficiency of the melt ejection [VDI93]. It can be assumed, that there is a complex interaction between gas and melt flow, so the quality of the formative processes in the kerf is closely related to the gas jet. With increasing complexity of the * Stefan Ulrich. Tel.: +49-3641-204-116; fax: +49-3641-204-110. E-mail address: [email protected]. components, the selective supply of gas to the knitting point is more difficult. Nevertheless, for the production of high-quality components, the use of alternative designs is necessary. Currently, these nozzles are manufactured elaborately and subject to production technical restrictions. In order to manufacture complex internal geometries selective laser melting is an alternative technique to traditional methods. Using this method, complex components can be built monolithically in a single production step. The current development of cutting nozzles is often dominated by experimentally trials, therefore, the developer relies on experience and conventional nozzle concepts. This heuristic method often leads to solutions, but which have not exploited the full potential of an arbitrary 3D geometry to influence the cutting gas flow. An alternative to this “trial and error” method is to measure or calculate the flow field. The use of simulation programs requires extensive knowledge in the field of fluidic mechanics. Under transient conditions, e.g., pressure shock, and simultaneously complex structures one encounters with the limits of numerical simulation, making it difficult to accurately predict the influence of a structure or even more the actual flow processes. As an alternative to simulation, a variety of diagnostic methods can be applied to gain knowledge on the outflow behavior. In the field of non-contact methods, the Schlieren measurement has been established in order to visualize flows. This method bases on the physical phenomenon, that a beam of light is reflected differently depending on the refractive index. As the index of refraction of the gas is determined by the type of gas and the applied pressure one can gather knowledge of local pressure and in a continuous measurement on the gas flow. The resulting image is a very good source for interpretation one. In previous investigations on the influence of the inner contour, the main points of study were the flow and the formulation of recommendations for manufacturing [KOV09, SHA06]. In the framework of this work, the impact of the selective laser melting technology on the flow behavior will be investigated and discussed. Due to the selective laser melting process, the components have a higher surface roughness and a lower contour accuracy of conventional method. 2. Operating principle and experimental setup of flow diagnostics When fluids or gases are subject to a temporal or local change density, pressure and temperature variations arise. As a result thereof, inhomogeneity occurs for deflecting the propagating direction of light in an optically transparent medium, i.e. a change in the optical refractive index n in the flow field. That implies the change in density ρ takes place primarily by the expansion of the gas stream from the nozzle. The Schlieren measurement technology allows for visualizing the local change of the refractive index density and refractive index are linearly interdependent [SET01]. (1) Developed by A. Toepler, an arrangement (see Fig. 1) is nowadays used in industrial monitoring and research applications most commonly [HER93]. The rays of the light source can be projected via a condenser in the plane of the aperture, which is located in the focal plane of the first schlieren lens. Using this lens a parallel beam path in the measuring area between the two lenses –the object field- is generated. In the back focal plane of the schlieren head are simultaneously the real image of the gap and the knife edge (Foucault-level). The "radiation beam" from the measurement area is mapped by the second schlieren lens in the Foucault- level and then falls on the table. If there is a change in refractive index, arise in the focal plane of the objective two slit images (an image of the original radiation and an image of the deflected radiation). Hence, the insertion of the knife edge causes a change in the intensity. [SET01]. (2) schlieren slit filament aperature ds=60 µm hemiplanar adjustable mirror mapping lens matt screen schlieren schlieren objective objective objective for projektion condensor camera on light source dn/ds table tripod Fig. 1. Schlieren-Aufnahmegerät 80 coupled with high-speed camera (Toepler´s dual-field-lens schlieren arrangement) Depending on the cutting position, the schliere appears dark on light background or light on dark background, the second variant due to the light sensitivity of the eye is the more appropriate (see Fig. 2). The quality of the Schlieren image and the sensitivity of the test object are determined by: the type of knife edge the knife edge and aperture orientation the light source a uniform illumination of the measuring field the focal length of the schlieren lenses exposure time distributed slit image slit image knife-edge schlieren objective knife-edge Fig. 2. Knife-edge arrangement in a double lens structure (left: lateral view, right: front view) To the visual evaluation of the real gas flow, a modified system was used (Schlieren-Aufnahmegerät 80 of the Carl Zeiss AG). To meet the requirements of the measuring task, the apertures were initially modified and the construction was coupled with a high-speed camera (Fastcam SA4 of Photron). The sensitivity of the measuring set-up could be increased by the reduction of the gap width of the aperture to 60 µm and substitute the cutting edge by a filament aperture. In addition, the reduction of the gap width led to the reduction of the resolution of the picture. By the increased sensitivity of the construction the smallest pressure differences can be visualized therefore. A crucial factor for a high-quality image is the setting of the exposure time. A longer exposure time yields a brighter schlieren photograph (up to the overexposure). By changing the gap and filament orientation the different gradient directions can be visualised, i.e., representation of the ray border or the compression front. 3. Flow characterization For the flow characterization, mainly the results from the optical analysis are used. Fig. 3 depicts that the flow gas is divided into three areas: the conical core with constant density (supersonic inviscid core) [MAR77, GAU70] the transition zone with variable density (supersonic mixing region) and the similarity area in which a free jet is completely formed and it is for mixing with the secondary fluid (subsonic mixing zone) [SHA06]. Especially during laser cutting, the core area should be within the kerf to guarantee a controlled melt ejection. At sufficient high pressure, expansion and compression waves are visible in the schlieren image, (see Fig. 3). At the nozzle outlet opening in the formation of expansion waves, which intersect at the beam axis and are reflected at the free jet boundary.. The reflected waves continues as compression waves (compression front), intersect in the gas jet axis and are reflected back as an expansion wave. This process continues periodically until the energy is consumed by friction between the edge beam and environment [CAR56]. intersection point supersonic compression inviscid core shock length boundary of the free jet expansion wave supersonic supersonic supersonic mixing region secondary fluid compression wave subsonic mixing zone Fig. 3. Free jet of a non-conformist exit opening (left: schematic view, right: compression and expansion behaviour) For the study, the copper nozzle (HG 10.281 by Precitec) was used because it has a wide industrial relevance. To ensure comparability for the investigation, the same nozzle was produced with the selective laser melting process. At 푝 = 1.5 푏푎푟 and 푝 = 6.0 푏푎푟 recordings of the free jet have been made. The gas jet exits the nozzle with a shortened supersonic inviscid core, which leads to a more rapid expansion of the supersonic mixing region. The reason for that are production-related influences, which amongst others yield a varying the layer thickness or an increased surface roughness of the component.
Details
-
File Typepdf
-
Upload Time-
-
Content LanguagesEnglish
-
Upload UserAnonymous/Not logged-in
-
File Pages9 Page
-
File Size-