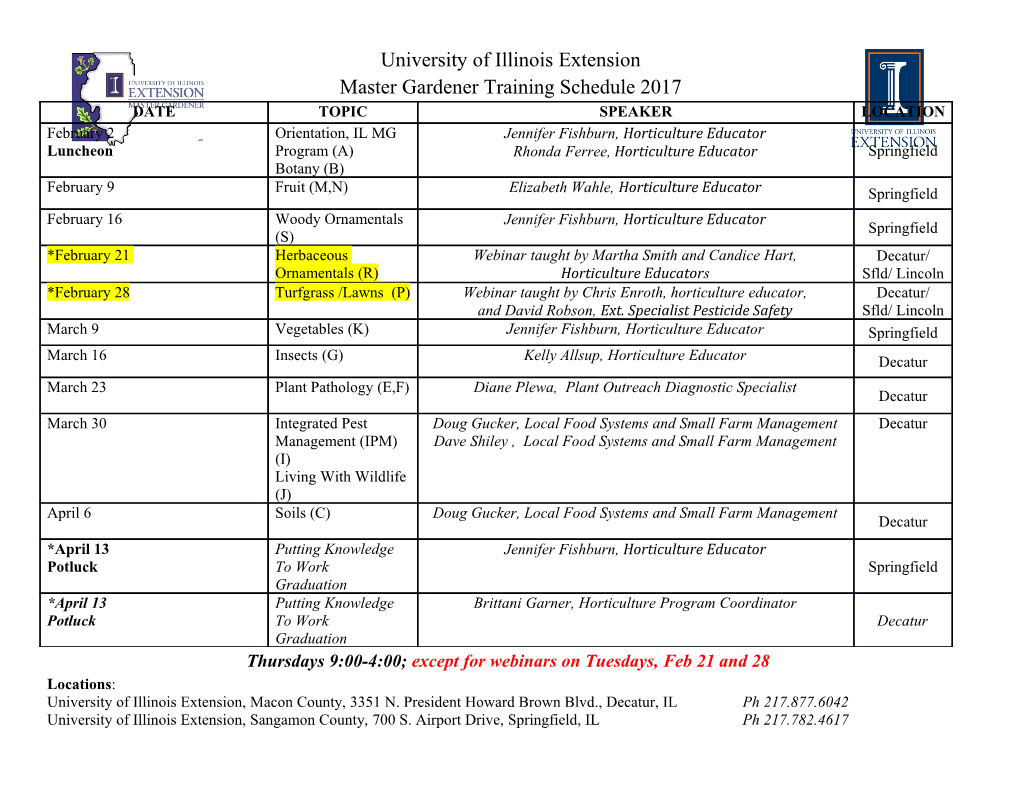
REPORT REFERENCE: 5.1 REGULATORY AND OTHER COMMITTEE REPORT NAME OF COMMITTEE: Planning and Regulation DATE OF MEETING: 15/03/2010 SUBJECT: County Matter Application To extend existing quarry at land to the south east of Ancaster Quarry, King Street, Heydour – Block Stone Ltd S43/2746/09 REPORT BY: Executive Director (Development Services) NAME OF CONTACT OFFICER: Victoria Bankes Price CONTACT OFFICER TEL NO: Lincoln (01522) 782070 CONTACT OFFICER EMAIL ADDRESS: [email protected] IS THE REPORT EXEMPT No IS REPORT CONFIDENTIAL? No SUMMARY Planning permission is sought by Block Stone Ltd to extend the existing dimension stone (limestone) quarry at land to the south east of Ancaster Quarry, King Street, Heydour. The proposal is to extend the 1.5ha existing quarry for mineral extraction by an additional area of 0.29ha. The extension area adjoins the south eastern boundary and is currently in agricultural use. It is estimated to contain 10,000m³ of saleable reserves which the applicant proposes to work over a period of approximately 16 years. Page 1 Following consideration of the relevant development plan policies and the comments received through consultation and publicity it is recommended that conditional planning permission be granted. DISCUSSION Background 1. In 1998 planning permission was granted (Ref S42/0399/03) to re-open and extend part of a small abandoned limestone quarry in Heydour known as ‘Ancaster Quarry’ in order to obtain a source of dimension stone for use in construction projects across the UK and abroad, including use in the renovation of historic buildings. 2. Under the provisions of the Environment Act 1995, the Ancaster Quarry was due for its First Period Review in 2003. In response the developer submitted two separate but interrelated applications: the first specifically for the First Periodic Review (Ref: S42/0399/03); and the second, for a small south eastern extension to the quarry (Ref: S42/0400/03). 3. Those applications were considered simultaneously by the Planning and Regulation Committee on 24 February 2003. In the case of the review application, new conditions were imposed on the existing quarry and, in the case of the extension application, the resolution was that planning permission should be granted subject to conditions, including the standard requirement for the development to be commenced within a period of five years. Unfortunately due to an oversight by the developer the permission for the extension was not implemented and has now lapsed. These reserves are still, however, required and as a result the developer is seeking a new planning permission to effectively replace the one that lapsed. The Application 4. Planning permission is sought by Blockstone Ltd to extend Ancaster Quarry, King Street, Heydour. The proposal is to extend the existing 1.5ha quarry by 0.29ha by working the adjoining agricultural land. 5. The applicant intends to work the proposed extension in the same manner as the existing quarry. Ancaster Quarry is worked intermittently for limestone, usually 2 or 3 times a year for a period of a few weeks. The limestone is usually extracted from the working face by hydraulic excavator. The following techniques are also used when appropriate: handheld drill and black powder (black powder causes fewer fractures and results in more usable stone compared to other explosives) to loosen large blocks from the quarry face; chainsaw to cut out blocks from the face; hand held rock drill to split and shape blocks. 6. The limestone blocks selected as suitable for ‘cut building stone’ are then numbered and stored in the eastern part of the quarry ready for collection. They are transported by articulated lorries to a cutting shed in Derbyshire or directly to customers. Smaller blocks and pieces of limestone that are not suitable for building stone are collected Page 2 separately and used for walling and rockery stone. Stone not suitable for these uses is placed in the tip area and would be used in backfilling the quarry as part of the restoration scheme. No waste stone would be removed from the site for use as aggregate. 7. As with the existing quarry the limestone would be worked to a depth of approximately 65m as the limestone below this depth is not a suitable colour or quality for building stone. The wastage factor is currently around 50%. The applicant anticipates that this could decrease as new markets are constantly being sought for smaller pieces of stone that are not suitable for cut building stone. Operational Proposals 8. As stipulated above the applicant intends to work the proposed extension using the existing methods. The topsoil would be stripped in one operation which would take 2- 5 days and would be transported through the old quarry area for storage. The overburden would most likely be stripped in one operation and placed in the worked out quarry area. Extraction within the extension area would generally take place from the northwest to southwest. Output Limits 9. The current planning permission at Ancaster Quarry limits the output of stone for the quarry to 3000m³ per annum unless otherwise agreed by the Minerals Planning Authority. To date the output has been in the region of 1000m³ per annum. The applicant states however that demand for the buff coloured limestone from Ancaster Quarry is increasing and that some yearly outputs are up to 3000m³. The applicant has suggested that a similar condition limiting output from the extension area to 3000m³ would be appropriate. Working Hours 10. The current planning permission restricts working hours for all of the quarry’s operations (except essential maintenance and safety operations) to weekdays between the hours of 07:00 and 19:00hours. No working is allowed on the weekends or Bank Holidays. The applicant proposes that these working hours should be maintained for the proposed extension area. Restoration 11. The quarry would be restored for nature conservation purposes. The existing quarry is being progressively restored by the partial backfilling of previously worked out areas with clay overburden and waste stone. An outline restoration scheme including the extension area was approved in 2004 as part of the current planning permission. The applicant states that the appropriate backfilling has taken place to date. 12. Clay overburden stripped from the extension area would be placed in the current quarry void and infilling would progress in a south easterly direction. There would not be sufficient overburden and waste stone to restore the whole quarry to the original ground levels. Infilling in the western corner of the quarry has taken place to the height of the adjoining land, around 90m AOD. The restored levels would grade down from the west and north to around 77m AOD, just below the top of the limestone at 80m AOD. The tip area would be levelled off as the tipping proceeds and once 0.2ha Page 3 is available for restoration it would be spread with top soil to a depth of 100-200mm to create a soil suitable for the establishment of indigenous trees and shrubs. Tree and shrub planting would take place during the next available planting season. As further tip areas of 0.2ha become available these would be topsoiled and planted. 13. All topsoil stripped from the quarry would be stored in mounds until required for restoration. These mounds would be no higher than 3 metres. The overburden from the extension would be used for restoring the western half of the existing quarry. Waste stone would be used to fill the lower levels of the extension area and some overburden would be retained to cover the waste stone prior to topsoiling. The upper faces of the clay overburden of the extension area would be left at an angle of between 1:2 and 1:3 and would be allowed to re-vegetate naturally. These would be similar to the old quarry faces in the south eastern part of the quarry which have become well vegetated over time. The limestone faces beneath the clay would be left as steep rock faces to form geological features within the quarry. 14. The floor of the extension area would be topsoiled and restored to woodland by planting with trees and shrubs. The northern and eastern quarry faces would not be topsoiled and would be allowed to naturally regenerate. Indigenous trees and shrubs would be used; the applicant states that the species mix should be agreed with the Mineral Planning Authority at a later date. The applicant proposes to plant the quarry floor with clumps of 2-3 trees at 2.5m centres at 20-25m intervals. All of the trees would be staked and protected with rabbit guards. 15. Each 0.2ha area planted would be managed for a period of 5 years to ensure a 95% success rate for all planting at the end of that period. The afteruse of the quarry would be for nature conservation. Environmental and Economic Impacts Geology 16. Ancaster Quarry lies within an area of sedimentary rocks of Jurassic age. The Lincolnshire Limestone which is the main building stone within the quarry is a yellow to buff coloured limestone which occurs in beds up to 1m thick. The limestone is 8- 10m thick. The limestone is overlain by Upper Estuarine beds which comprise of a series of grey, highly fossiliferous mudstones containing a single thin limestone band; the mudstone is around 10-12m thick. Market Need 17. The market for building stone fluctuates and the applicant states that output from the quarry is expected to be up to 3,000m³ per annum. Flood Risk 18. The applicant has stipulated that the site is not considered to be at risk from flooding from rivers or surface water run off.
Details
-
File Typepdf
-
Upload Time-
-
Content LanguagesEnglish
-
Upload UserAnonymous/Not logged-in
-
File Pages23 Page
-
File Size-