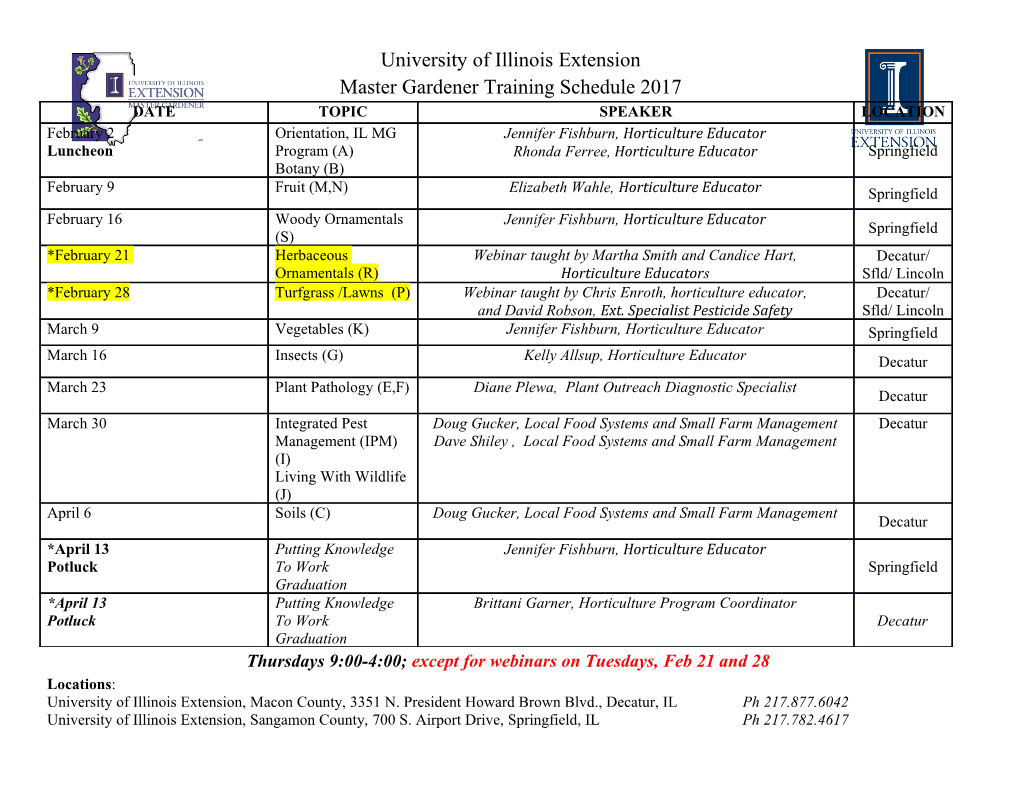
MICROSTRUCTURE AND MECHANICAL PROPERTIES OF ADDITIVELY MANUFACTURED PARTS WITH STAIRCASE FEATURE by TAHMINA KEYA Y. KEVIN CHOU, COMMITTEE CHAIR ALEXEY N. VOLKOV, COMMITTEE CO-CHAIR MARK L. WEAVER A THESIS Submitted in partial fulfillment of the requirements for the degree of Master of Science in the Department of Mechanical Engineering in the Graduate School of The University of Alabama TUSCALOOSA, ALABAMA 2017 Copyright Tahmina Keya 2017 ALL RIGHTS RESERVED ABSTRACT This thesis focuses on a part with staircase feature that is made of Inconel 718 and fabricated by SLM process. The objective of the study was to observe build height effect on the microstructure and mechanical properties of the part. Due to the nature of SLM, there is possibility of different microstructure and mechanical properties in different locations depending on the design of the part. The objective was to compare microstructure and mechanical properties from different location and four comparison groups were considered: 1. Effect of thermal cycle; 2. External and internal surfaces; 3. Build height effect and 4. Bottom surfaces. To achieve the goals of this research, standard metallurgical procedure has been performed to prepare samples. Etching was done to reveal the microstructure of SLM processed Inconel 718 parts. Young’s modulus and hardness were measured using nanoindentation technique. FEM analysis was performed to simulate nanoindentation. The conclusions drawn from this research are: 1. The microstructure of front and side surface of SLM processed Inconel 718 consists of arc shaped cut ends of melt pools with intermetallic phase at the border of the melt pool; 2. On top surface, melted tracks and scanning patterns can be observed and the average width of melted tracks is ~ 100-150 µm; 3. The microstructure looks similar at different build height; 4. Microstructure on the top of a stair is more defined and organized than the internal surface; 5. The mechanical properties are highest at the bottom. OM images revealed slight difference in microstructure in terms of build height for this specific part, but mechanical properties seem to be vary noticeably. This is something to be kept in mind while designing or determining build orientation. External and internal surfaces of a ii stair at the same height showed difference in both microstructure and mechanical properties. To minimize that effect and to make it more uniform, gradual elevation can be considered when suitable as far as design modification is concerned. Above all, this study reveals important information about the pattern of microstructure, thus heat transfer mechanism inside a part which is useful to understand the SLM process. iii LIST OF ABBREVIATIONS AND SYMBOLS AM Additive Manufacturing SLM Selective Laser Melting EBAM Electron Beam Additive Manufacturing ASTM American Society for Testing and Materials CAD Computer Aided Design STL STereoLithography CNC Computer Numerical Control UTS Ultimate Strength HIP Hot Isostatic Pressing SEM Scanning Electron Microscopy OM Optical Microscopy EBSD Electron Backscatter Diffraction XRD X-Ray Powder Diffraction EA, η Energy Density U, v Scanning Velocity P Laser Power SP Scan spacing Cc Machine Compliance E Young’s modulus Er Reduced Young’s modulus E0 Young’s modulus at 100% density iv ν Poisson’s ratio σ Stress σy Yield strength εp Plastic strain n Strain hardening exponent H Hardness Ar Residual Area left by indenter P Porosity a Material Constant n Material Constant v ACKNOWLEDGEMENTS I would like to thank my advisor, Dr. Y Kevin Chou for guiding me throughout this research. I thank Dr. Alexey Volkov for being in the committee in spite of being busy and being patient about time constraint I had. I’m grateful to Dr. Mark L. Weaver for being extremely supportive throughout my graduate studies. He allowed me to use his lab equipment from the very beginning and always helped me whenever I had any issues regarding nanoindentation or MTE labs. Last but not the least, he is serving as one the valuable members of the committee too. A very special thanks goes to Dr. Paul Allison. At the end of my research when the Hysitron Triboindenter machine was no longer cooperating with me, Dr. Allison trained me in Agilent Technologies Nanoindenter G200 using his tip even during spring break. I also got to learn some theoretical details about nanoindentation from him. He as well as Dr. Luke Brewer held on their own experiments for the sake of my graduation. I thank both of them. The CAF staffs Mr. Rich Martens, Mr. Johnny Goodwin, Mr. Robert Holler and Mr. Robert Fanning were very supportive in sample cutting and in SEM analysis. I’m thankful to have some great group members like Dr. Bo Cheng, Mr. Xiaoqing Wang and Mr. Subin Shrestha who helped me from my 1st day in USA. All of them supported me in various ways and are no less than my family. vi I thank all the staffs of department of Mechanical Engineering not only for their academic support, but also their personal help in my critical days. I also thank staffs from department of MTE too. This research is supported by CFD Research Corporation (Huntsville, AL) through a NASA STTR project. Marshall Space Flight Center (Huntsville, AL) fabricated experimental samples. Last but not the least, I thank my family, my friends and my fiancé Dr. Robert Mitchell Guice without whom I would never be where I am today. vii CONTENTS ABSTRACT .................................................................................................................................... ii LIST OF ABBREVIATIONS AND SYMBOLS .......................................................................... iv ACKNOWLEDGEMENTS ........................................................................................................... vi LIST OF TABLES ........................................................................................................................ xii LIST OF FIGURES ..................................................................................................................... xiii CHAPTER 1: INTRODUCTION ................................................................................................... 1 1.1 Additive Manufacturing ............................................................................................................ 1 1.2 Selective Laser Melting ............................................................................................................ 5 1.3 Ni alloys and Inconel 718 ......................................................................................................... 8 1.4 Motivations and Objectives .................................................................................................... 11 1.5 Uniqueness of the Present Work ............................................................................................. 12 1.6 Organization of the Thesis ...................................................................................................... 13 CHAPTER 2: LITERATURE REVIEW ...................................................................................... 14 2.1 Introduction ............................................................................................................................. 14 2.2 Additive Manufacturing: Microstructure and Mechanical Properties .................................... 14 2.3 Selective Laser Melting: Microstructure and Mechanical Properties ..................................... 18 2.4 Selective Laser Melting: Effect of Build Height .................................................................... 25 CHAPTER 3: EXPERIMENTAL DETAILS ............................................................................... 27 viii 3.1 Part Fabrication ....................................................................................................................... 27 3.2 Metallographic Sample Preparation ........................................................................................ 29 3.2.1 Cutting.................................................................................................................................. 29 3.2.2 Mounting .............................................................................................................................. 33 3.2.3 Polishing .............................................................................................................................. 33 3.2.4 Etching ................................................................................................................................. 34 3.3 Microstructure Study .............................................................................................................. 35 3.3.1 Optical Microscopy .............................................................................................................. 35 3.3.2 Scanning Electron Microscopy (SEM) ................................................................................ 35 3.3.3 Motic Stereoscope ................................................................................................................ 36 3.4 Nanindentation ........................................................................................................................ 37 3.4.1 Hysitron Triboindenter ......................................................................................................... 37 3.4.2 Nanoindenter G200 .............................................................................................................. 40 3.5 Finite
Details
-
File Typepdf
-
Upload Time-
-
Content LanguagesEnglish
-
Upload UserAnonymous/Not logged-in
-
File Pages115 Page
-
File Size-