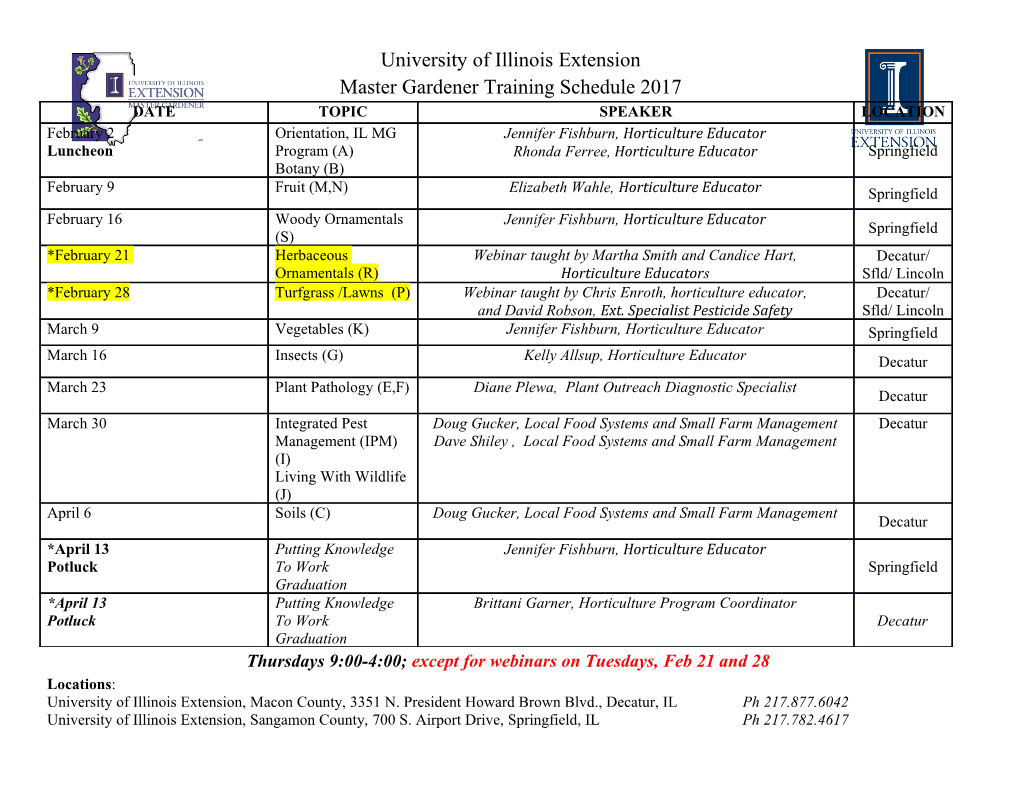
metals Article Compound Layer Design for Deep Nitrided Gearings Stefanie Hoja * , Matthias Steinbacher and Hans-Werner Zoch Leibniz-Institut für Werkstofforientierte Technologien-IWT, Badgasteiner Straße 3, 28359 Bremen, Germany and MAPEX, Center for Materials and Processes, Universität Bremen, Bibliothekstraße 1, 28359 Bremen, Germany; [email protected] (M.S.); [email protected] (H.-W.Z.) * Correspondence: [email protected]; Tel.: +49-421-218-51395 Received: 2 March 2020; Accepted: 27 March 2020; Published: 31 March 2020 Abstract: Deep nitriding is used to obtain a nitriding hardness depth beyond 0.6 mm. The long nitriding processes, which are necessary to reach the high nitriding hardness depths, mostly have a negative influence on the hardness and strength of the nitrided layer as well as on the bulk material. The compound layer often is considered less, because in most practical cases, it is removed mechanically after nitriding, to avoid spalling in service. However, in former investigations, it was shown, that thick and compact compound layers have the potential for high flank load capacity of gears. The investigations focus on the simultaneous formation of a high nitriding depth and a thick and compact compound layer. Beside the preservation of the strength, a challenge is to control the porosity of the compound layer, which should be as low as possible. The investigations were carried out using the common nitriding and heat treatable mild steel 31CrMoV9, which is often used for gear applications. The article gives an insight on the development of multistage nitriding processes studied by short- and long-term experiments aiming for a specific compound layer build-up with low porosity and high strength of the nitride layer and core material. Keywords: nitriding; nitrocarburizing; two-stage treatment; process design; compound layer; white layer; nitriding hardness depth 1. Introduction High performance gears are usually subjected to heat treatment in order to achieve optimum performance for the respective application. Thermochemical surface layer heat treatment, such as case hardening, carbonitriding, nitriding or nitrocarburizing are common treatments, since the highest stress is in the surface layer of the teeth and a tough core is positive for the service behavior [1]. Studies have shown that nitriding treatment can improve the load-bearing properties of gears with regard to different stresses. König et al. provide an overview of nitriding applications for gearings [2]. The necessary hardening depth of the surface layer depends on the normal modulus of the gearing [3]. For nitriding, a nitriding hardening depth of approximately 0.6 mm is regarded as the economic limit value. Therefore case hardening is frequently used for larger gears, since higher case depths can be achieved in a shorter time. Nevertheless, nitriding offers some process-related advantages compared to case hardening, such as better protection against scuffing, wear and corrosion, higher surface hardness, a temperature-stable surface layer for use at higher temperatures, as well as less dimensional and shape changes and thus generally no need for reworking [4]. Deep nitriding differs from conventional nitriding in aiming higher nitriding hardness depths of approximately 0.8–1.0 mm. In order to achieve those nitriding hardness depths, long nitriding periods and/or high nitriding temperatures are necessary, which leads to losses of strength in the nitriding layer and in the core. In order to minimize these losses in strength caused by tempering effects during nitriding, the maximum possible nitriding temperature is limited depending on the material [5]. Metals 2020, 10, 455; doi:10.3390/met10040455 www.mdpi.com/journal/metals Metals 2020, 10, 455 2 of 12 Investigations on deep nitriding were already carried out in the 1980s [6], when the nitriding plant technology was not yet sufficiently developed to enable controlled and reproducible nitriding treatments to be carried out in gas or plasma. For this reason, more recent investigations concern also nitriding processes for achieving high nitriding hardness depths [4,7–9]. In [4] material-oriented two-stage processes for deep nitriding were developed with the aim of achieving high nitriding hardness depths with the highest possible strength. These processes were carried out according to the two-stage principle developed by Floe [10,11], where a closed compound layer was formed during the first stage. The temperature was kept low at 520 ◦C in order to obtain finely distributed precipitates in the diffusion layer. In the second stage at elevated temperature, diffusion was carried out into the depth and the growth of the compound layer was restricted by a low nitriding index. By this process control, negative effects on the strength of the material could be kept within limits and stress-compatible nitriding layers with high nitriding hardness depths with sufficient strength of the base material could be reliably and reproducibly produced by modern process technology. Nitriding increases the rolling contact fatigue life of gears, whereas the generated compressive residual stresses within the diffusion layer are responsible for the enhancement of the fatigue strength [12,13]. Until now, the primary objective of nitriding process development was to achieve high nitriding hardness depths with economical process duration and little attention has been paid to the compound layer during. In random tests on the tooth flank load-bearing capacity, one of the investigated variants, which had a comparatively thick, compact compound layer due to a higher nitriding temperature, showed particularly good load-bearing capacity behavior. It was remarkable that the compound layer remained almost undamaged after the load-tests at high load levels, whereas in the other tested variants with a thinner compound layer, defects in the compound layer occurred after only a few load cycles [14]. Additionally the authors of [15] showed in their work, that a control of the nitriding parameters is necessary because the crystalline structure profile of the compound layer is important for the gear performance. The composition of the compound layer (γ’-nitride/"-nitride/alloying element nitrides) and the shape of the porous zone also play a significant role in the tribological load-bearing capacity [16]. The "-nitride has a higher hardness than the γ’-nitride and due to its hexagonal structure, the "-nitride has a low number of sliding systems, which prevents the wear partners from approaching each other over an area down to atomic distances. For this reason, the adhesion tendency of "-nitride layers is low. The pore content and the pore distribution and size also have an influence on the wear behavior. Depending on the wear load, sometimes γ’-layers show better wear properties and sometimes thin, slightly porous "-compound layers [17–19]. The current investigations deal with the simultaneous achievement of high nitriding hardness depths and a thick, compact compound layer. In addition to maintaining the strength properties, another challenge is to ensure that the compound layer does not become too porous. 2. Materials and Methods 2.1. Reference State The deep nitrided material 32CDV13 (0.32% C, 0.33% Si, 0.55% Mn, 3.00% Cr, 0.90% Mo and 0.29% V) showed a remarkable load-bearing potential in [14]. The gears were deep nitrided in a material-oriented two-stage treatment in a controlled gas nitriding process with steel retort. In the first stage at 520 ◦C in 15 h with a nitriding potential of KN = 1, a compound layer and fine nitride precipitates were formed in the first approximately 0.25 mm of the diffusion zone. In the second stage, the temperature was increased to 570 ◦C for 130 h and at the same time the nitriding potential was reduced to KN = 0.5. The second stage was mainly used for rapid diffusion of the nitrogen into the material in order to achieve the desired nitriding hardness depth. The compound layer of the reference material 32CDV13 formed on the tooth flank is shown in Figure1. Table1 shows the compound layer thickness (CLT), the thickness of the porous zone (CLT P) Metals 2020, 10, x FOR PEER REVIEW 3 of 11 and nitriding hardness depth (NHD) averaged over the tooth area. Despite the low nitriding potential of KN = 0.5 in the diffusion phase, a relatively thick compound layer has been formed due to the comparatively high temperature and long duration required for nitriding. The nitrogen and carbon profiles of the reference compound layer determined by Glow Discharge Optical Emission Spectroscopy (GD-OES) are shown in Figure 2. In the area of the porous zone, the nitrogen concentration of approximately 9–9.5 mass-% was slightly higher than in the Metalscompact2020 ,area10, 455 of the compound layer below. Here the nitrogen concentration was about 6.5 mass3 of-%. 12 Taking into account the alloying elements, which also bind nitrogen as nitride, it can be assumed that Metalsthe compound 2020, 10, x FOR layer PEER consists REVIEW mainly of γ'-nitride and that in the area of the porous zone ε-nitrides3 of 11 and nitriding hardness depth (NHD) averaged over the tooth area. Despite the low nitriding potential have also been formed. A X-ray phase analysis with Cr Kα radiation (surface measurement) showed andof K nitriding= 0.5 in hardness the diff usiondepth phase,(NHD) aaveraged relatively over thick the compound tooth area. Despite layer has the been low formednitriding due potential to the a compoundN layer composition of approximately 14% ε-nitride and approximately 86% γ'-nitride, ofcomparatively KN = 0.5 in the high diffusion temperature phase, and a longrelatively duration thick required compound for nitriding. layer has been formed due to the which confirms the considerations made on the basis of the nitrogen profile. comparatively high temperature and long duration required for nitriding. The nitrogen and carbon profiles of the reference compound layer determined by Glow Discharge Optical Emission Spectroscopy (GD-OES) are shown in Figure 2.
Details
-
File Typepdf
-
Upload Time-
-
Content LanguagesEnglish
-
Upload UserAnonymous/Not logged-in
-
File Pages12 Page
-
File Size-