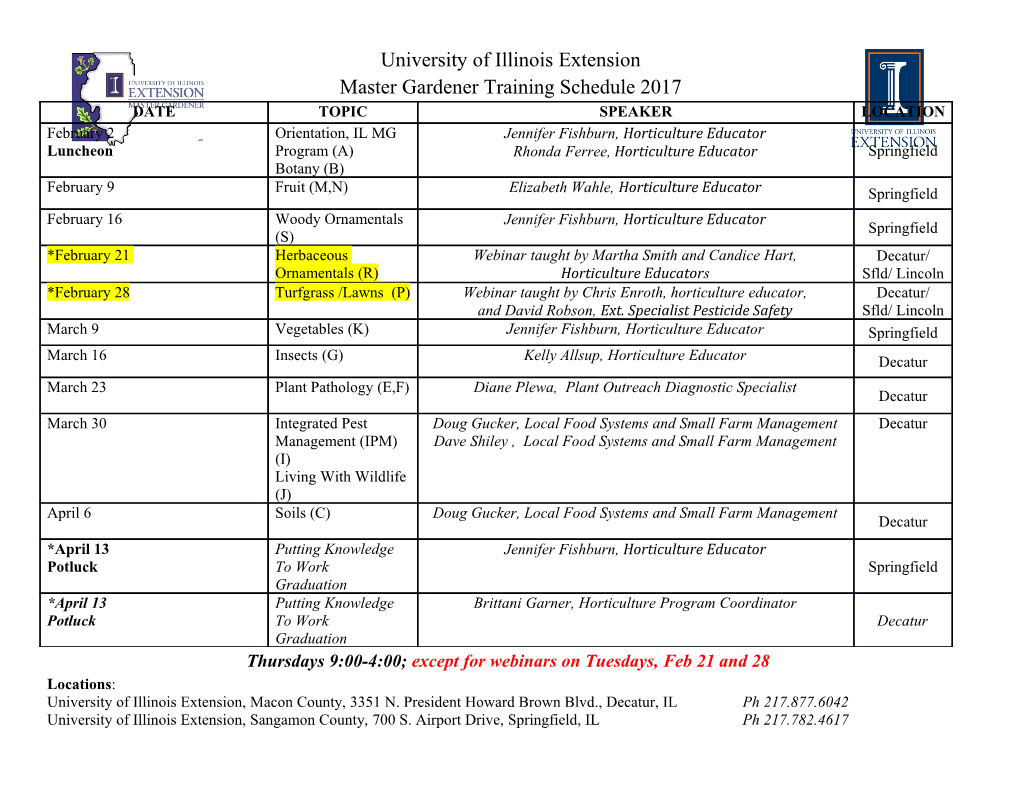
MEMBRANES FOR VAPOR/GAS SEPARATION Richard W. Baker Membrane Technology and Research, Inc. 1360 Willow Road, Suite 103, Menlo Park, CA 94025 Email: [email protected] Keywords: Membranes, vapor/gas separation, membrane system process design, polyolefin plant resin degassing, gasoline vapor recovery systems, monomer recovery systems. ABSTRACT The first small membrane units for separating organic vapors from air were installed in the late 1980s. By the mid-1990s, MTR was selling million-dollar systems to petrochemical plants to recover olefins from polyolefin manufacture. About the same time, licensees of GKSS technology in Europe began installing large systems to capture gasoline vapors from tank farms and fuel terminals. The market for vapor separation systems is now at least $20-30 million per year. More than 100 large systems, with a value of $1-5 million each, have been installed. In addition, at least 500 small systems, with a value of $10,000-$100,000 each, are operating to capture vapor emissions from retail gasoline stations, industrial refrigerator units and petrochemical process vents.(1-4) This chapter covers the development of vapor/gas separation technology and its emergence as a recognized sector of the membrane separation business. Separations of organic mixtures, such as light hydrocarbon streams, and of organic/water mixtures, present different technical challenges and are not discussed here. 2 VaporGas_Sep MEMBRANES AND MODULES Gas transport through dense polymer membranes is governed by the expression: DK p− p ii( io i) l ji = (1) l 3 2 where ji is the volume (molar) flux expressed as [cm (STP) of component i]/cm @s; R is the pi pi membrane thickness, o is the partial pressure of component i on the feed side, and l is the partial pressure of component i on the permeate side. The diffusion coefficient, Di, reflects the mobility of the individual molecules in the membrane material; the gas sorption coefficient, Ki, with units [cm3(STP) of component i/cm3 of polymer] @ pressure, reflects the number of molecules dissolved in the membrane material. The product DiKi can be written as -i, which is called the membrane permeability, and is a measure of the membrane's ability to permeate gas. The best measure of the ability of a membrane to separate two gases, i and j, is the ratio of their permeabilities, αi/j, called the membrane selectivity, which can be written as (2) - ii⎡ DK⎤⎡i ⎤ αij/ ==⎢ ⎥⎢ ⎥ - DK jj⎣ ⎦⎣j ⎦ The ratio Di/Dj is the ratio of the diffusion coefficients of the two gases and can be viewed as the mobility selectivity, reflecting the different sizes of the two molecules. The ratio Ki/Kj is the ratio of the sorption coefficients and can be viewed as the sorption or solubility selectivity, reflecting the relative solubility of the two gases. In polymer materials, the diffusion coefficient decreases with increasing molecular size, because large molecules interact with more segments of the polymer chain than do small molecules. Hence, the mobility selectivity, Di/Dj, always favors the permeation of small molecules over large ones. The sorption coefficient of gases and vapors is a measure of the energy required for the gas to be sorbed by the polymer, and increases with increasing condensability of the permeant. This dependence on condensability means that the sorption coefficient usually increases with molecular size, because large molecules are normally more condensable than smaller ones. Hence the sorption selectivity, Ki/Kj, favors the permeation of larger, more condensable molecules, such as hydrocarbon vapors, over permanent gases, such as oxygen and nitrogen. It follows that the effects of permeant molecular size on the mobility and sorption selectivities are opposed. Because of the competing effects of the mobility selectivity term and the sorption selectivity term in Equation (2), the selectivity of gas pairs is different in glassy and rubbery polymers. This difference is illustrated by the data in Figure 1. $ In glassy polymers, such as polyetherimide, the rigid nature of the polymer chains means the mobility selectivity term in Equation (2) is dominant. Permeability falls with increasing permeant size, and small molecules permeate preferentially. When used to separate an organic vapor from nitrogen, amorphous glassy membranes preferentially permeate nitrogen. 3 VaporGas_Sep $ In rubbery polymers, such as polyisoprene, the sorption selectivity term is dominant. Permeability increases with increasing permeate size, and large molecules permeate preferentially. When used to separate an organic vapor from nitrogen, rubbery membranes preferentially permeate the organic vapor. 104 C H 103 4 10 C5H12 C2H6 C3H8 2 10 O 2 CH4 Polyisoprene He (a rubbery polymer) N2 10 He Permeability 1 (Barrer) O2 10-1 N2 Polyetherimide 10-2 (an amorphous glassy polymer) C3H8 CH4 C4H10 -3 10 C2H6 10-4 ~ 0 20 40 60 80 100 120 140 160 180 200 220 240 van der Waals molar volume (cm3/mol) Figure 1. Permeability as a function of molar volume for a rubbery and a glassy polymer, illustrating the different balance between sorption and diffusion in these polymer types. From the discussion above, it appears that vapor/permanent gas separations can be performed with either rubbery vapor-selective membranes or glassy gas-selective membranes. In practice, almost all commercial plants use rubbery membranes, predominantly membranes made from silicone rubber (polydimethyl siloxane) [PDMS]. Rubbery membranes are preferred for several reasons: 1. Rubbery polymers tend to have much higher permeability than glassy polymers. (As Figure 1 shows, polyisoprene is over 100 times more permeable than polyetherimide to oxygen.) The higher the permeability, the smaller is the membrane area required to permeate a given volume flow of gas. Therefore, in system design, higher permeability translates to fewer membrane modules, and lower capital cost. 2. The vapor/permanent gas selectivity of most glassy polymers is very dependent on organic vapor partial pressure. At low vapor concentrations (or partial pressures), the selectivity of the membrane approaches the selectivity predicted by the ratio of pure gases. However, as the organic vapor concentration (partial pressure) increases, the amount of vapor sorbed in the polymer also increases. The vapor plasticizes the polymer, which becomes rubbery. In the plasticized material, the nitrogen permeability increases, but the organic vapor 4 VaporGas_Sep permeability increases even more. The membrane then switches from being a glassy, permanent-gas-selective membrane to being a rubbery, organic vapor-selective membrane. Examples of the few exceptions to this behavior are the perfluoro polymers Teflon7 AF (DuPont) and HyflonJ AD (Solvay Solexis).(6) These polymers, because of the inert nature of their perfluoro chemistry, have exceptionally low sorptions for most organic vapors and so retain their glassy nature, even in the presence of high concentrations of organic vapors. Membranes made from these polymers have found a limited use in separating air from gasoline vapor vent streams at retail gas stations. 3. Rubbery membranes provide better selective purge capability. The final reason that rubbery, vapor-permeable membranes are usually preferred is illustrated in Figure 2, which shows flow schemes for two types of membrane systems used to recover the vapor component from a vapor/inert gas vent gas stream. The objective of this very common type of process is to produce an inert vent gas purge stripped of as much of the organic vapor component as possible. In the first design shown in Figure 2(a), a glassy polymer membrane is used to treat the vent gas. The inert gases permeate the membrane, and the vapor-enriched residue gas is recycled to the process. The advantage of this design is that the pressure of the recovered vapor-containing residue gas is only slightly below the pressure of the feed gas. This allows the residue gas to be recycled to the process with minimal recompression. However, the membrane must be very selective to prevent excessive amounts of vapor passing through the membrane. Few glassy polymer membranes are sufficiently selective to make this design practical. (a) Vapors retained by a glassy membrane Recovered vapor recycle Glassy to reactor membrane Vapor and inert Inerts in vent gas permeate purge (b) Vapor permeated by a rubbery membrane Recovered feedstock recycle to reactor Rubbery Vapor and inert membrane vent gas Inerts in residue purge Figure 2. The two principal designs for membrane vent-gas systems. 5 VaporGas_Sep In the design shown in Figure 2(b), a rubbery membrane is used. The vapor to be recovered permeates the membrane, leaving a residue stream enriched in the inert components. The advantage of this design is that even modestly selective membranes can produce an inert vent gas stream almost completely depleted of vapor. All of the organic vapor component is recycled back to the process. The disadvantage of this design is that the vapor-rich permeate to be recycled to the reactor is at low pressure and must be recompressed. Silicone rubber composite membranes have been used in almost all of the vapor separation systems installed to date. Silicone rubber is extremely permeable and has adequate vapor/inert gas selectivities for most applications. Polyoctylmethylsiloxane (POMS), closely related to silicone rubber (polydimethylsiloxane), has been suggested as a material with slightly better selectivity but has not been widely used.(7) For a few years, there was also a good deal of interest in the polyacetylene polymers poly(1-trimethylsilyl-1-propyne) (PTMSP), poly(p-tert-butyl diphenylacetylene)PptBDPA and poly(4-methyl-2-pentyne) (PMP).(8,9) These glassy polymers, because of the rigidity of their polymer backbones, have extraordinarily high free volumes and very unusual gas permeation properties. In particular, the polymers are even more permeable and more selective to condensable vapors than silicone rubber, the industry benchmark polymer. Unfortunately, the high cost of the polymers and their poor chemical and physical stability have prohibited commercial use, and most researchers have now abandoned work with these materials.
Details
-
File Typepdf
-
Upload Time-
-
Content LanguagesEnglish
-
Upload UserAnonymous/Not logged-in
-
File Pages25 Page
-
File Size-