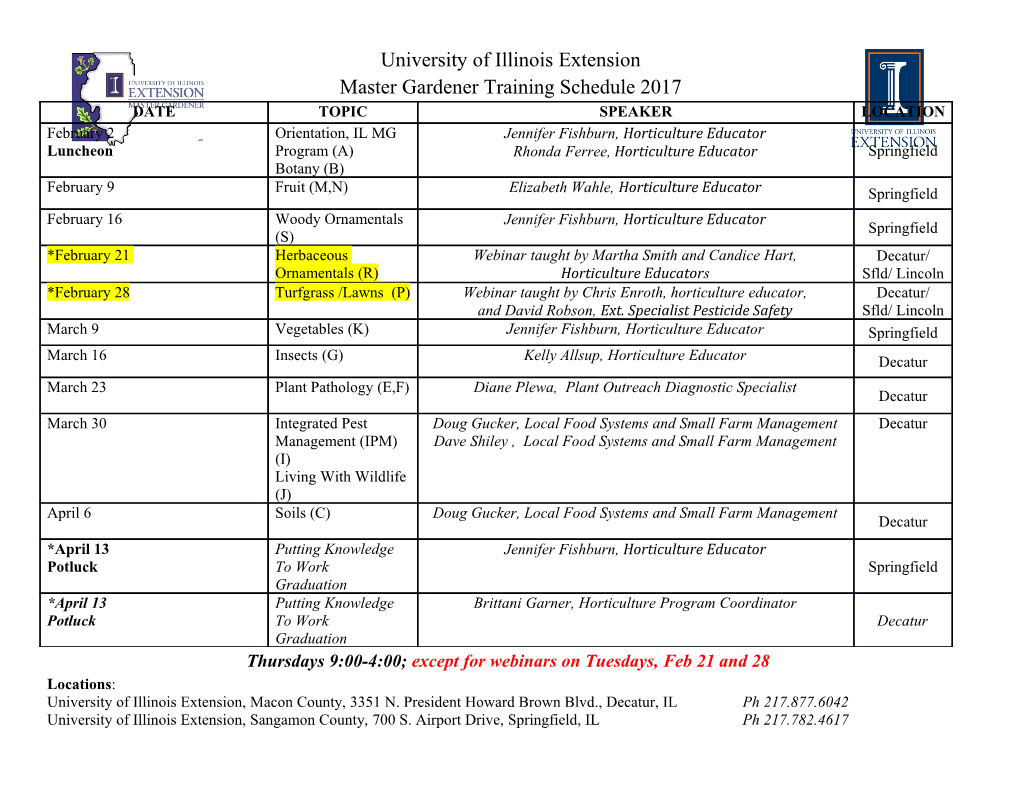
EPA-450/2-77-022 November 1977 (OAQPS NO. 1.2-079) OAQPS GUIDELINES CONTROL OF VOLATILE ORGANIC EMISSIONS FROM SOLVENT METAL CLEANING I U.S. ENVIRONMENTAL PROTECTION AGENCY 1 Office of Air and Waste Management Office of Air Quality Planning and Standards I,\ a0- Research Triangle Park, North Carolina 2771 1 328 1 I, RADIAN LIBRARY DURHAM, N.C. II i. This report is issued by the Environmental Protection Agency to report technical data of interest to a limited number of readers. Copies are available free of charge to Federal employees, current contractors anc! grantees, and nonprofit organizations - in limited quantities - from the Library Services Office (MD-35). Research Triangle Park, North Carolina 27711; or, for a fee, from the National Technical Information Service, 5285 Port Royal Road, Springfield, Virginia 22161. Publ ication No. EPA-45012-77-022 PREFACE The purpose of this document is to inform regional, State, and local air pol 1ution control agencies of the different techniques available for reducing organic emissions from solvent metal cleaning (degreasing) . Solvent metal cleaning includes the use of equipment from any of three broad categories: cold cleaners , open top vapor degreasers , and conveyori zed degreasers. A1 1 of these employ organic solvents to remove soluble impurities from metal surfaces. The diversity in designs and applications of degreasers make an emission 1imi t approach inappropriate; rather, regulations based on equipment specifications and operating requirements are recomnended. Reasonably available control technology (RACT) for these sources entails implementation of operating procedures which minimize solvent bss and retrofit of applicable control devices. Required control equipment can be as simple as a manual cover or as complex as a carbon adsorption system, depending on the size and design of the degreaser. Required operating procedures include covering degreasing equipment whenever possible, properly using solvent sprays, reducing the amount of solvent carried out of the unit on cleaned work by various means, promptly repairing leaking equipment, and most importantly properly disposing of wastes containing volatile organics. Not all controls and procedures will be applicable to a1 1 degreasers, a1 though in general specific operating requirements and control devices will be applicable to the majority of designs within each category of degreasers. Control of open top and conveyorized vapor degreasing is the most cost effective, followed by waste solvent disposal for a1 1 degreasing operations, manufacturing cold cleaning and maintenance cold cleaning. iii swi tches are : 1. Vapor level control thermostat, 2. Condenser water flow switch and thermostat, 3. Sump thermostat, 4. Solvent level control, 5. Spray safety switch. The first four safety switches 1isted above turn off the sump heat while the fifth turns off the spray. The most important safety switch is the vapor level control thermostat. This device is activated when solvent vapor zone rises above the designed operating level. This can occur if the coolant flow is interrupted, for example. When the hot vapors are sensed, the sump heater is turned off thus minimizing vapor escape. This thermostat should be a manual reset type for manually operated degreasers. For conveyorized degreasers, the vapor level control thermostat should activate an alarm system. These controls should be checked frequently. The condenser water flow switch and thermostat turn off the sump heat when either the condenser water stops circulating or the condenser water becomes warmer than specified. If the condenser water flow swi tch and thermos tat is properly adjusted, then it will serve as a back-up for the safety vapor thermostat and also assure efficient operation of the condenser coils. In summer months, the cooling water for condensing coils often becomes too warm. In this case, the thermostats in a condenser water flow switch can signal a need for improvement, such as increasing the water flow rate. This 16 problem occurred during a test performed for EPA. As oils, greases and other contaminants build up in the solvent, the boiling point of the mixture increases. Both the sump thermostat and solvent 3-1 5 TABLE 1. CONTROL SYSTEMS FOR COLD CLEANING Control System A Control Equipment: 1. Cover 2. Facility for draining cleaned parts 3. Permanent, conspicuous label. sumnarizing the operating requirements Operating Requirements: 1. Do not dispose of waste solvent or transfer it to another ~arty, such that greater than 20 percent of the waste (by weight) can evaporate into the atmosohere.* Store waste. solvent on1 v in covered containers. 2. Close degreaser cover whenever not handling parts in the cleaner. 3. Orain cleaned parts for at least 15 seconds or until dripping ceases. Control System B Control Equipment: 1. Cover: Same as In System A, except if (a) solvent volatility is reater than 2 kPa (15 mn Hg or 0.3 psi) measured at 3B°C (10O0F),** 9b) solvent is agitated. or (c) solvent is heated, then the cover must be designed so that i: can be easily operated with one hand. (Covers for larger degreasers may require mechanical assistance, by spring loading, cdunterweiqhtinq or Dowered svsterns.) 2. Drainage facility: Same as in System A, except that if solvent volatility is greater than about 4.3 kPa (32 mn Hg or 0.6 psi) veasured at 38°C (lOO°F), then the drainage facility nust be internal. so that oarts are enclosed under the cover while draining. The drainage facility may be external for applications where an internal type cannot fit into the cleaning system. 3. Label : Same as in System A 4. If used, the solvent spray must be a solid, fluid stream (not a fine, atomized or shower type spray) and at a pressure which does not cause excessive splashing. 5. Major control device for highly volatile solvents: If the solvent volatility is D 4.3 kPa (33 n Hg or 0.6 psi) measured at 38°C (lOO°F), or if solvent is heated above 50'C (12O0FJ, then one of the following control devices must be used: a. Freeboard that gives a freeboard ratiow* 20.7 6. Nater cover (solvent must be insoluble in and heavier than water) c. Other system of equivalent control, such as a refrigerated chiller or carbon adsorption. Operating R~rprirrn~ntq: Sawe as in System P *Water and solid waste regulations must also be comolied with. **Senerally solvents consisting primarily gf mineral :pirits [:?oddard) have tolatilities < 2 CPa. ***Freeboard ratio is defined aj the freoocard Aeignt divided by the uidth of the degreaser. Two levels of control for each type of degreaser have been identified here as examples of reasonably avai 1able control technology (RACT). In general, control level A shows proper operating practice and simple, inexpensive control equipment. Control level B consists of level A plus additional requi rements to improve the effectiveness of control. The degree of emission reduction for both individual items and control levels are discussed in the text. Specific requirements can be modified to achieve whatever level of control is necessary. Control systems for cold cleaners are shown in Table 1, thosefbr open top vapor degreasers in Table 2, and those for conveyorized degreasers in Table 3. Two exemptions are recommended. First, conveyorized degreasers smaller 2 than 2.0 m of air/vapor interface should be exempt from a requirement for a major control device. This would not be cost effective and would tend to move the small conveyorized degreaser users to open top vapor degreasers which emit more solvent per unit work load. Second, open top vapor degreasers 2 smal ler than 1 m of open area should be exempt from the application of refrigerated chi 1lers or carbon adsorbers. Again, requi rement for these would not be cost effective. TABLE 3. CONTROL SYSTEMS FOR CONVEYORIZED DEGREASERS Control System A Control Equipment: None Operating Requirements : 3 2 2 1. Exhaust ventilation should not exceed 20 m /min per m (65 cfm per ft ) of degreaser opening, unless necessary to meet OSHA requirements. Work place fans should not be used near the degreaser opening. 2. Minimize carry-out emissions by: a. Racking parts for best drainage. b. Maintaining verticle conveyor speed at < 3.3 m/min (11 ft/min) 3. Do not dispose of waste solvent or transfer it to another party such that greater than 20 percent of the waste (by weight) can evaporate into the atmosphere. Store waste solvent only in covered containers. 4. Repair solvent leaks imnediately, or shutdown the degreaser. 5. Water should not be visibly detectable in the solvent exiting the nater separator. Control System B Control Equipment : 1. Major control devices; the degreaser must be controlled by either: a, Refrigerated chiller, 2 2 b. Carbon adsorption system, with ventilation L 15 m2/min per m (50 cfm/ft ) of air/vapor area (when down-time covers are open), and exhausting <25 ppm of solvent by volume averaged over a complete adsorption cycle, or c. System demonstrated to have control efficiency ?quivalent to or better than either of the above. 2. Either a drying tunnel, or another means such as rotating (tumbling) basket, sufficient to prevent cleaned parts from carrying out solvent liquid or vapor. 3. Safety switches a. Condenser flow switch and thermostat - (shuts off sump heat if coolant is either not circulating or too wan). b. Spray safety switch - (shuts off spray pump or conveyor if the vapor level drops excessively, e.g. > 10 cm (4 in.)). c. Vapor level control thermostat - (shuts off sump heat when vapor level rises too high). 4. Minimized openings: Entrances and exits should silhouette work loads so that the average clearance (between parts and the ed~eof the degreaser opening) is either <10 cm (4 in.) or <I0 percent of the width of the opening. 5.
Details
-
File Typepdf
-
Upload Time-
-
Content LanguagesEnglish
-
Upload UserAnonymous/Not logged-in
-
File Pages229 Page
-
File Size-