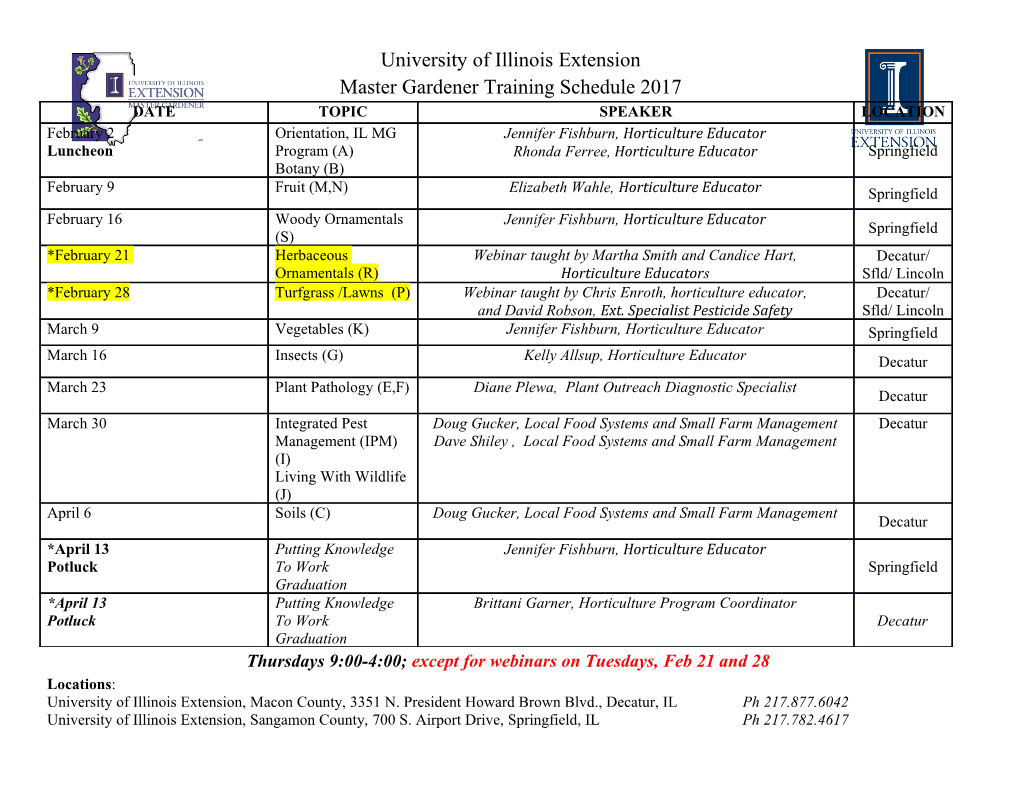
Layout:Layout 1 2/7/07 10:02 AM Page 58 BRAZING & SOLDERING TODAY Challenges in Attaining Lead-Free Solders The switch to cadmium-free brazing alloys has been a little easier than finding a lead-free solder that performs similar to the one standard from the past BY PHILIP BASKIN ver the last 15 years, there have is similar to what occurred in the brazing nature was learned, it was widely agreed been many changes in the solder- industry as the conversion took place to that it was appropriate to remove it for the OOing and brazing industries as a re- make Cd-free BAg alloys. long-term health and safety of brazers. sult of chemical and metallurgical regula- One of the commonalities between the ead is being removed from con- tions that have changed the industrial Cd-free BAg alloys and the Pb-free soft sumer electronics soldering be- standards for making products. solders has been the heightened melt- LLcause when it leaches into the soil point of the filler metal alloys. The eutec- from a landfill, lead is deposited into water Impact of Removing tic of 63Sn/37Pb melts at 183°C (361°F). and the soil, which is detrimental to the By replacing lead with silver, copper, environment. Lead oxide is created during Cadmium and Lead and/or other alloy additions, and raising soldering, and the objective of removing the percentage of tin to 91–99.3% of over- lead is to create a safer environment. The The brazing industry in the early 1990s all composition, the melting point of cur- actual amount of lead used by the elec- removed cadmium (Cd) from the BAg rent conventional Pb-free solders is in the tronics industry totals 0.3–0.5%1 of the (boron-silver) alloys. Cadmium, a toxin, range of 217°–227°C (423°–440°F). An- overall lead use. The battery and ammu- was added to lower the melting point for other factor affected by the removal of nition industries represent more than 60% silver brazing filler metals. It promoted ex- lead is the density of the alloys having been of total lead use. cellent flow of the filler metal, and left a converted from a heavier 63Sn/37Pb to clean, shiny postbraze joint. With the re- lighter tin-based alloy. Common Alloys and moval of cadmium, the melting point/flow ue to the removal of major com- phase increased 40°–70°F, BAg filler metal position elements (Cd and Pb) Some Differences flow was slowed down, and the postbraze from filler metals in brazing and finish did not have the same shiny, bright DD While brazing and soldering employ electronics soldering applications, a more finish as the Cd-bearing alloy, which had restricted flow of the respective filler met- different alloys, there are certain com- set the visual standard. als occurred. Processes required a com- monalities to the filler metal metallurgy in any companies experiencing the plete reengineering to determine changes Pb-free solders and BAg alloys. Silver, lead (Pb)-free conversions to made to the overall physical characteris- copper, tin, zinc, and nickel are all com- MMmeet WEEE and RoHS stan- tics, efficiency, and durability of the newly mon ingredients in solders and BAg alloys. dards are experiencing similarities with manufactured products, as well as how to However, the alloy percentages and the SMT and PTH assembly applications as address the engineering of all the parts, formulation are very different to meet the those brazing companies that went Cd- the process, and long-term quality. temperature, strength, and heating re- free in the 1990s. While the term “drop- quirements for different applications. in” is used as a standard to explain the en- hen looking at the melting gineering required to be Pb-free, the Improving Health points (Table 1) of tin and lead, overall manufacturing process, metallur- and the Environment WWthere is less than a 100°C differ- gical evaluations, and strength/stress tests ence between the two metals. The combi- for the ‘old’ parts that have been produced Today, the brazing world speaks of cad- nation of these metals in a 63Sn:37Pb ratio for years have encountered more obsta- mium as an element whose properties cles than could have been imagined. This were much appreciated, but when its toxic 1. Source, Alpha/Fry Metals. PHILIP BASKIN ([email protected]) is with Superior Flux & Mfg. Co., Cleveland, Ohio. 58 MARCH 2007 Layout:Layout 1 2/7/07 10:02 AM Page 59 BRAZING & SOLDERING TODAY lenges meet today’s PCBs as those that Table 1 — Melting Points of Various Alloys Table 2 — Different Alloy Compositions in challenged PCBs more than 25 years ago: Use • component and board sensitivity to Tin (Sn) Melting Point 232°C being overheated Lead (Pb) Melting Point 327.4°C 96.5Sn/3.5Ag 221°C E • consistent solder paste printing/ Silver (Ag) Melting Point 960.5°C 96.5Sn/3Ag/0.5Cu 218–220°C screening (a) Copper (Cu) Melting Point 1083°C 96.2Sn/2.5Ag/0.8Cu/0.5Sb 218°C E • semiconductors and components re- Nickel (Ni) Melting Point 1455°C 95Sn/5Sb 232–240°C quiring a metallurgical consistency with Indium (In) Melting Point 155°C 91Sn/9Zn 199°C E the assembly solder Bismuth (Bi) Melting Point 271°C SnBalance/0.7Cu/0.3Ni(b) 227°C E Antimony (Sb) Melting Point 630°C • consistent flow on pads and leads ® • noncracking, solid joints. (a) AIM Castin . Today’s boards, incorporating ball grid (b) Nihon Superior SN100C. array (BGA) components, flip chips, mini- quad flat pack (QFP) and much tighter yields a eutectic at 183°C — 49°C lower spaces between circuit leads, pads and than the melting point of tin. Silver-based mount technology (SMT) reflow of solder components, make for a more challenging BAg and Cu-based BCuP alloys are stan- paste was at its infancy, the double-sided solder paste application process and qual- dards for metal joining filler metals in the printed circuit board (PCB) was a new ity control of the soldering to the PCB, but brazing industry. Today, one of the most method of building PCBs to place more still incorporate the same disciplined tem- used solders, the SAC alloys, are combi- than twice the number of chips on both peratures to the process as were required nations of tin/silver/copper — all of which sides of the PCB. This improved the over- more than 25 years ago for the double- are components in BAg 7, 18, 21, 28, 34, all value of PCBs by using space far more sided boards. 36, and 37. Naturally, the difference lies in efficiently than the wave soldered plated- In addition to the SMT reflow using the ratios. Again, the BAg alloys are silver- through holes (PTH) and taking up less 96.5Sn/3.5Ag, there were wave solder PTH based, whereas Pb-free solder alloys are placement of space where the boards were applications where a higher-temperature all Sn-based. However, this does not housed. solder was required to meet the atmos- change the melting point of the silver and o achieve this objective, dual sol- phere and environmental heat that would copper. While the melting point of the dering processes were required. In have melted the 63Sn/37Pb and caused SAC alloys is higher than that of the Sn-Pb step one, 96.5Sn/3.5Ag solder board failure in sensitive operations areas. TT Again, while not common, wave soldering solder alloy, the addition of these very- paste was applied to the first side of the high melting point alloys to tin still brings board. With a eutectic at 221°C, this tem- with these Pb-free alloys was used for spe- the solder below the 232°C melting point perature was 38°C above the eutectic cialty applications on aerospace, automo- of tin. The true eutectic composition of a melting point of the Sn63/Pb37 alloy. tive, and other control boards requiring a SAC alloy is 93.6Sn/4.7Ag/1.7Cu at 217°C. Given this temperature difference, step higher-temperature solder. Even though However, the alloy most commonly used is two involved soldering the second side of today it is known as a Pb-free solder, that the SAC305, 96.5Sn/3Ag/0.5Cu. This alloy the board with the lower melting point tin- may not have been the objective for using has a eutectic at 218°C, however, there is lead solder and operating at a reflow tem- this specific solder. This Sn96.5/Ag3.5 bi- no true eutectic for this alloy, rather a perature of 210°–215°C max. This pre- nary alloy met the process requirements plastic phase at 218°–220°C. vented the silver solder side from meeting and helped to establish a base for what has liquidus and made dual-sided reflow become Pb-free solder. nother aspect to be considered Still Searching for the processes possible. To accomplish this, one of the chemical formulations incorpo- from the original days of using the Single Replacement Sn/Ag reflow alloy is that the stan- rated for the flux medium/binder of the AA spherical solders was a single dard flux formulations were rosin mildly With all of the Pb-free studies that have medium/binder that could maintain the activated (RMA) and rosin fully activated been conducted or are planned for the fu- consistency of printing, solder flow, and (RA) fluxes. Soldering was done using a ture, there is still no single alloy composi- temperature differences the distinctly dif- vapor-phase process capable of incorpo- tion that has taken the role of replacing ferent solders required.
Details
-
File Typepdf
-
Upload Time-
-
Content LanguagesEnglish
-
Upload UserAnonymous/Not logged-in
-
File Pages4 Page
-
File Size-