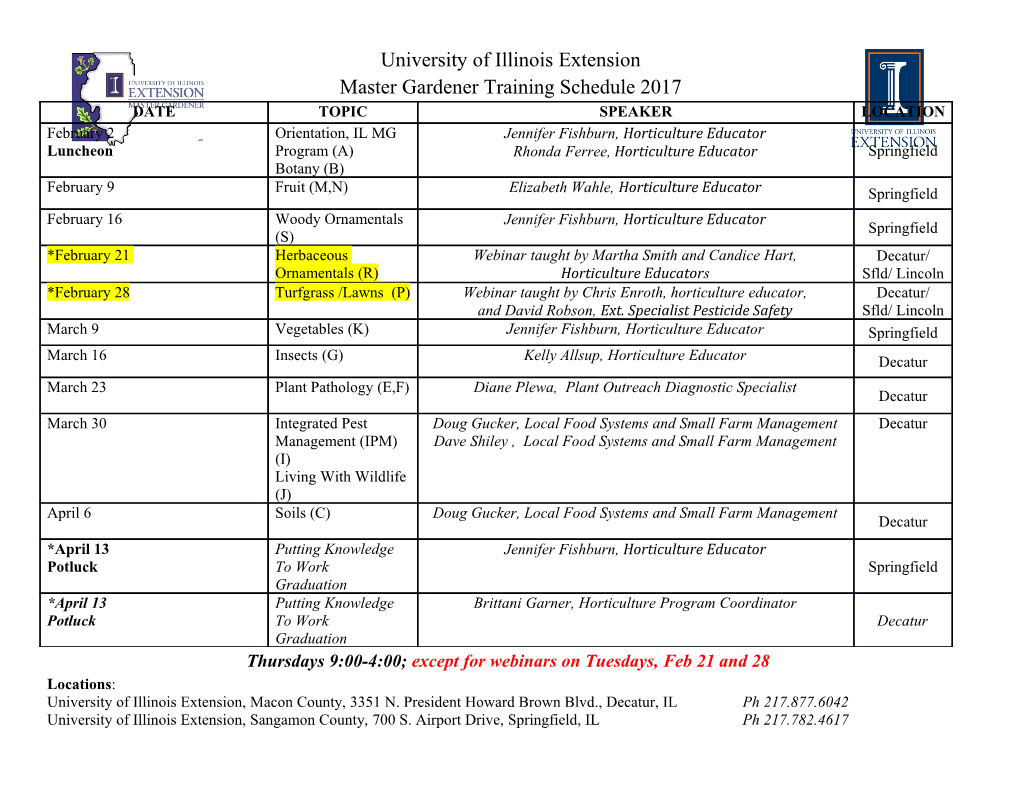
DEGREE PROJECT IN TECHNOLOGY, FIRST CYCLE, 15 CREDITS STOCKHOLM, SWEDEN 2020 Electric Load Driven Longboard JOHAN ANDERSSON RICKARD HÖGLUND KTH ROYAL INSTITUTE OF TECHNOLOGY SCHOOL OF INDUSTRIAL ENGINEERING AND MANAGEMENT Electric Load Driven Longboard JOHAN ANDERSSON RICKARD HOGLUND¨ Bachelor’s Thesis at ITM Supervisor: Nihad Subasic Examiner: Nihad Subasic TRITA-ITM-EX 2020:29 Abstract Keywords: mechatronics, longboard, brushless direct cur- rent motor, Hall effect sensor, load cell, Wheatstone bridge, LiPo battery, Arduino, ODrive This bachelor’s thesis aims to show an extensive overview of all the parts that build up an electric load driven long- board and see if a load controlled longboard can be seen as a safe, comfortable and convenient alternative to the more common remote controlled longboard. The thesis will also answer how weight can be measured on a longboard in the most effective way, what the most comfortable riding tech- nique is and what a good motor-battery configuration to be able to travel at 30 km/h and 10 km would be. The longboard measures the weight distribution with load cells located between the deck and the trucks. An Arduino translates the input from the load cells to a certain speed and then sends it to an ODrive which controls a BLDC mo- tor that is powered by two LiPo batteries. The results show that a load controlled longboard can very well be seen as a good alternative if right riding technique is used. The best technique is when the longboard acceler- ates when the rider tilts and keeps a constant speed when the rider stands straight. The best way to measure the weight is to fasten the trucks with hinges which lets the load cells register weight without anything interfering. Not all tests could be done because of Covid-19 but a measured top speed of 15 km/h with a high gear ratio is a promising result for the future when more suitable gear ratios will be tested to try to reach the goal of 30 km/h. Referat Elektrisk lastdriven longboard Nyckelord: mekatronik, longboard, borstl¨os likstr¨omsmotor, Hall effekt sensor, lastcell, Wheatstone brygga, LiPo batte- ri, Arduino, ODrive Det h¨ar kandidatexamensarbetet str¨avar efter att visa en omfattande ¨overblick p˚aalla delar som bygger upp en elekt- risk lastdriven longboard och se om en laststyrd longboard kan ses som ett s¨akert, komfortabelt och beh¨andigt alterna- tiv till den vanligare radiostyrda longboarden via handkon- troll. Det h¨ar arbetet kommer ocks˚asvara p˚ahur vikt kan m¨atas p˚aen longboard p˚aett s˚aeffektivt s¨att som m¨ojligt, vad som ¨ar den mest bekv¨ama ˚akstilen och vad ¨ar en bra motor-batteri konfiguration f¨or att kunna ˚akai 30 km/h och n˚a10 km skulle vara. Longboarden m¨ater viktf¨ordelningen med lastceller som ¨ar placerade mellan br¨adan och truckarna. En Arduino om- vandlar indatan fr˚anlastcellerna till en specifik hastighet som den sedan skickar till en ODrive som kontrollerar en borstl¨os likstr¨omsmotor som i sin tur ¨ar driven av tv˚aLiPo batterier. Resultaten visar att en laststyrd longboard kan mycket v¨al ses som ett bra alternativ om r¨att ˚akstilanv¨ands. Den b¨asta stilen ¨ar att longboarden accelererar n¨ar ˚akarenlu- tar sig och h˚alleren konstant hastighet n¨ar ˚akarenst˚ar rakt. Det b¨asta s¨attet att m¨ata vikt ¨ar att montera truc- karna p˚ag˚angj¨arn som l˚aterlastcellerna m¨ata vikt utan att n˚agotst¨or. Alla tester kunde inte utf¨oras p˚agrund av Covid-19 men en uppm¨att topphastighet p˚a15 km/h med en h¨og utv¨axling ¨ar ett lovande resultat f¨or framtiden n¨ar l¨ampligare utv¨axlingar kommer testas f¨or att f¨ors¨oka n˚a m˚aletp˚a30 km/h. Acknowledgements We would like to thank our supervisor Nihad Subasic for his feedback through- out this project and making sure it could all continue despite the situation that was present during this project. We also wish to show gratitude to Seshagopalan Thorapalli Muralidharan for being a huge help when the project became very chal- lenging. He came up with helpful ideas and helped us getting parts manufactured that was needed for the longboard. We would also like to thank Staffan Qvarnstr¨om for ordering parts and teaching us how to solder. Contents 1 Introduction 1 1.1 Background . 1 1.2 Purpose . 1 1.3 Scope . 2 1.4 Method . 2 2 Theory 3 2.1 Deck . 3 2.2 Trucks and Wheels . 3 2.3 Motor . 3 2.4 Hall effect sensor . 5 2.5 Battery . 6 2.6 Powertrain . 7 2.7 Load Cells . 7 2.8 Control Unit . 8 2.8.1 Microcontroller . 8 2.8.2 Motor controller . 9 3 Demonstrator 10 3.1 Powertrain . 10 3.1.1 Motor . 10 3.1.2 Battery . 10 3.1.3 Gear Ratio and Wheels . 12 3.1.4 ODrive . 13 3.1.5 Arduino Uno . 13 3.1.6 Programming . 13 3.1.7 Gears and Timing Belt . 16 3.2 Load Cells . 17 3.3 Design . 18 3.3.1 Layout . 18 3.3.2 Load Cell Mounting . 18 3.3.3 Motor Mount . 21 4 Results 22 4.1 Load cell placement and weight distribution . 22 4.2 Riding Technique . 22 4.3 Top Speed . 23 4.4 Distance . 23 5 Discussion and Conclusion 24 5.1 Discussion . 24 5.2 Conclusion . 26 6 Recommendations and Future Work 27 Bibliography 28 Appendices 30 A Configuration for the ODrive 32 A.1 Motor configuration . 32 A.2 Encoder configuration . 33 B Code for the Arduino 34 B.1 Prototype and definitions header file . 34 B.2 Code where both HX711 are used . 35 B.3 Code where only one HX711 is used . 42 C MATLAB code 49 D Pictures of the final product 54 List of Figures 2.1 Parts of the BLDC motor [4]. 4 2.2 Motor used to drive the longboard [5]. 5 2.3 Hall effect principle with no magnetic field in the left image and with a magnetic field present in the right image [7]. 6 2.4 The powertrain setup used on the longboard. Made with Microsoft Pow- erpoint. 7 2.5 Load cell amplifier used to connect the load cells with the Arduino [12]. 8 2.6 Load cell used to measure the weight distribution [13]. 8 2.7 The ODrive used to control the motor [17]. 9 3.1 Battery used to power the longboard [20]. 12 3.2 A flowchart of the code. The velocity is measured in Hall effect sensor counts per second. Made with draw.io . 15 3.3 Calculated needed distance between the gears. Made with MATLAB. 16 3.4 300 mm belt [21] used and the ring fitted between the wheel and gear. Made with Solid Edge. 16 3.5 Wheatstone bridge configuration with two load cells. Made with Mi- crosoft Powerpoint. 17 3.6 The two cases for the batteries, ODrive and Arduino. Made with Solid Edge. 18 3.7 Load cell placement of mount type 1, (dimensions not to scale). Made with Microsoft Powerpoint. 19 3.8 Deflection of metal plate under the load cells. Made with MATLAB. 19 3.9 Mounting type 1 and mounting type 2. Made with Solid Edge. 20 3.10 Mounting type 3. The hinges are placed on the near side of the load cell mount. Made with Solid Edge. 20 3.11 The motor mount. Made with Solid Edge. 21 A.1 The configuration of the motor in ODrive tool. 32 A.2 The configuration of the Hall sensor in ODrive tool. 33 D.1 The finished longboard . 54 D.2 Close up of the powertrain and the load cell mount with its load cells . 55 D.3 The underside of the longboard . 56 List of Tables 2.1 Motor specifications . 5 2.2 Load cell specifications . 8 3.1 Possible battery configurations . 11 List of Abbreviations BLDC - Brushless direct current CPR - Counts per revolution CPU - Central processing unit GPIO - General-purpose input/output I/O - Input/output Li-ion - Litium ion LiPo - Lithium polymer MCU - Microcontroller unit mAh - Milliampere hour PLA - Polylactide RPM - Revolutions per minute UART - Universal asynchronous receiver-transmitter Chapter 1 Introduction 1.1 Background A longboard is a type of skateboard. Due to its characteristics such as the length and the bigger and softer wheels it rolls a lot better and smoother and is therefore more often used for commuting and downhill riding. A longboard does require a bit of work from the user since the user have to kick to propel it forward. This can get quite exhausting after a while. Electric longboards already exists on the market. These make it possible to travel without having to kick but the rider has to use a remote controller to pilot it instead. The downsides of this is that the user can lose the controller, it can run out of battery and it can lose connection to the board. To be able to travel on a longboard without having to propel it by kicking or without having to use a remote controller presented itself as an interesting challenge, thus this project was chosen. 1.2 Purpose The purpose of this thesis is to examine how a load driven electrical longboard should be set up so a person can ride it comfortably and safe. The thesis strive to answer the following questions: • What is a good motor-battery configuration to have a top speed of 30 km/h and a range of 10 km? • What is a good way to consistently measure weight on a longboard? • How does a person control the longboard in the most comfortable way? • Can a load controlled longboard be seen as a safe, comfortable and convenient alternative to a remote controlled longboard? 1 CHAPTER 1.
Details
-
File Typepdf
-
Upload Time-
-
Content LanguagesEnglish
-
Upload UserAnonymous/Not logged-in
-
File Pages70 Page
-
File Size-