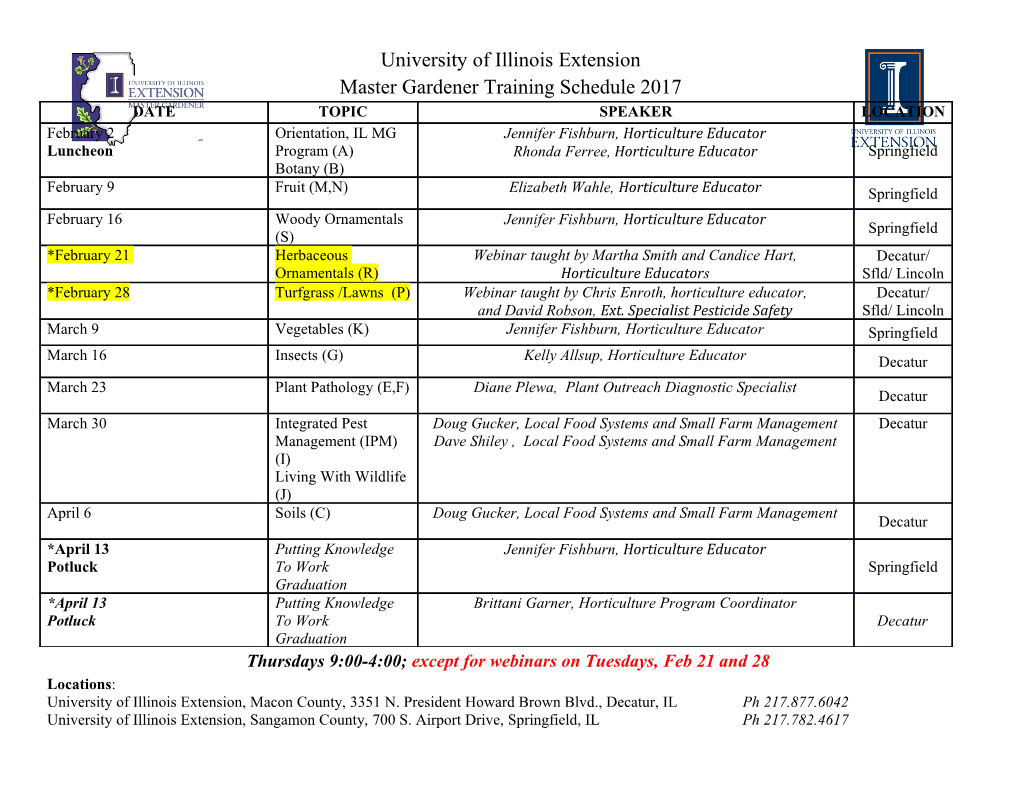
cen58933_ch15.qxd 9/9/2002 10:20 AM Page 785 CHAPTER COOLING OF ELECTRONIC 15 EQUIPMENT lectronic equipment has made its way into practically every aspect of modern life, from toys and appliances to high-power computers. The re- CONTENTS Eliability of the electronics of a system is a major factor in the overall re- 15–1 Introduction and liability of the system. Electronic components depend on the passage of History 786 electric current to perform their duties, and they become potential sites for ex- 15–2 Manufacturing of Electronic Equipment 787 cessive heating, since the current flow through a resistance is accompanied by heat generation. Continued miniaturization of electronic systems has resulted 15–3 Cooling Load of Electronic Equipment 793 in a dramatic increase in the amount of heat generated per unit volume, com- 15–4 Thermal Environment 794 parable in magnitude to those encountered at nuclear reactors and the surface of the sun. Unless properly designed and controlled, high rates of heat gener- 15–5 Electronics Cooling in Different Applications 795 ation result in high operating temperatures for electronic equipment, which 15–6 Conduction Cooling 797 jeopardizes its safety and reliability. The failure rate of electronic equipment increases exponentially with 15–7 Air Cooling: Natural Convection and Radiation 812 temperature. Also, the high thermal stresses in the solder joints of electronic 15–8 Air Cooling: Forced components mounted on circuit boards resulting from temperature variations Convection 820 are major causes of failure. Therefore, thermal control has become increas- 15–9 Liquid Cooling 833 ingly important in the design and operation of electronic equipment. 15–10 Immersion Cooling 836 In this chapter, we discuss several cooling techniques commonly used in electronic equipment such as conduction cooling, natural convection and radiation cooling, forced-air cooling, liquid cooling, and immersion cooling. This chapter is intended to familiarize the reader with these techniques and put them into perspective. The reader interested in an in-depth coverage of any of these topics can consult numerous other sources available, such as those listed in the references. 785 cen58933_ch15.qxd 9/9/2002 10:20 AM Page 786 786 HEAT TRANSFER 15–1I INTRODUCTION AND HISTORY The field of electronics deals with the construction and utilization of devices that involve current flow through a vacuum, a gas, or a semiconductor. This exciting field of science and engineering dates back to 1883, when Thomas Edison invented the vacuum diode. The vacuum tube served as the foun- dation of the electronics industry until the 1950s, and played a central role in the development of radio, TV, radar, and the digital computer. Of the several computers developed in this era, the largest and best known is the ENIAC (Electronic Numerical Integrator and Computer), which was built at the Uni- versity of Pennsylvania in 1946. It had over 18,000 vacuum tubes and occu- pied a room 7 m ϫ 14 m in size. It consumed a large amount of power, and its reliability was poor because of the high failure rate of the vacuum tubes. The invention of the bipolar transistor in 1948 marked the beginning of a new era in the electronics industry and the obsolescence of vacuum tube tech- nology. Transistor circuits performed the functions of the vacuum tubes with greater reliability, while occupying negligible space and consuming negligible power compared with vacuum tubes. The first transistors were made from ger- manium, which could not function properly at temperatures above 100°C. Soon they were replaced by silicon transistors, which could operate at much higher temperatures. The next turning point in electronics occurred in 1959 with the introduction of the integrated circuits (IC), where several components such as diodes, transistors, resistors, and capacitors are placed in a single chip. The number of 1010 GSI components packed in a single chip has been increasing steadily since then at an amazing rate, as shown in Figure 15–1. The continued miniaturization of 9 10 electronic components has resulted in medium-scale integration (MSI) in the 1960s with 50–1000 components per chip, large-scale integration (LSI) in 8 10 ULSI the 1970s with 1000–100,000 components per chip, and very large-scale inte- gration (VLSI) in the 1980s with 100,000–10,000,000 components per chip. 7 10 Today it is not unusual to have a chip 3 cm ϫ 3 cm in size with several mil- 6 lion components on it. 10 VLSI The development of the microprocessor in the early 1970s by the Intel Corporation marked yet another beginning in the electronics industry. The ac- 105 companying rapid development of large-capacity memory chips in this decade made it possible to introduce capable personal computers for use at work or at 104 VLSI Components per chip home at an affordable price. Electronics has made its way into practically everything from watches to household appliances to automobiles. Today it is 103 difficult to imagine a new product that does not involve any electronic parts. The current flow through a resistance is always accompanied by heat 102 MSI generation in the amount of I 2R, where I is the electric current and R is the SSI 101 resistance. When the transistor was first introduced, it was touted in the news- papers as a device that “produces no heat.” This certainly was a fair statement, 100 considering the huge amount of heat generated by vacuum tubes. Obviously, 1960 1970 1980 1990 2000 the little heat generated in the transistor was no match to that generated in its Year predecessor. But when thousands or even millions of such components are FIGURE 15–1 packed in a small volume, the heat generated increases to such high levels that The increase in the number of its removal becomes a formidable task and a major concern for the safety and components packed on a chip over reliability of the electronic devices. The heat fluxes encountered in electronic the years. devices range from less than 1 W/cm2 to more than 100 W/cm2. cen58933_ch15.qxd 9/9/2002 10:20 AM Page 787 787 CHAPTER 15 Heat is generated in a resistive element for as long as current continues to flow through it. This creates a heat build-up and a subsequent temperature rise at and around the component. The temperature of the component will continue rising until the component is destroyed unless heat is transferred away from it. The temperature of the component will remain constant when the rate of heat removal from it equals the rate of heat generation. Individual electronic components have no moving parts, and thus nothing to wear out with time. Therefore, they are inherently reliable, and it seems as if they can operate safely for many years. Indeed, this would be the case if com- ponents operated at room temperature. But electronic components are ob- served to fail under prolonged use at high temperatures. Possible causes of failure are diffusion in semiconductor materials, chemical reactions, and creep in the bonding materials, among other things. The failure rate of electronic de- vices increases almost exponentially with the operating temperature, as shown in Figure 15–2. The cooler the electronic device operates, the more reliable it 10 failure rate at T is. A rule of thumb is that the failure rate of electronic components is halved 9 f = —–—————— T failure rate at 75°C for each 10°C reduction in their junction temperature. 8 T f 7 15–2I MANUFACTURING OF ELECTRONIC 6 5 EQUIPMENT 4 Failure factor factor Failure The narrow band where two different regions of a semiconductor (such as the 3 p-type and n-type regions) come in contact is called a junction. A transistor, 2 for example, involves two such junctions, and a diode, which is the simplest 1 0 semiconductor device, is based on a single p-n junction. In heat transfer analy- 20 40 60 80 100 120 140 sis, the circuitry of an electronic component through which electrons flow 75 and thus heat is generated is also referred to as the junction. That is, junctions Temperature, °C are the sites of heat generation and thus the hottest spots in a component. In FIGURE 15–2 silicon-based semiconductor devices, the junction temperature is limited to The increase in the failure rate of 125°C for safe operation. However, lower junction temperatures are desirable bipolar digital devices with for extended life and lower maintenance costs. In a typical application, nu- temperature (from Ref. 15). merous electronic components, some smaller than 1 m in size, are formed from a silicon wafer into a chip. The Chip Carrier The chip is housed in a chip carrier or substrate made of ceramic, plastic, or glass in order to protect its delicate circuitry from the detrimental effects of the environment. The chip carrier provides a rugged housing for the safe han- dling of the chip during the manufacturing process, as well as the connectors between the chip and the circuit board. The various components of the chip carrier are shown in Figure 15–3. The chip is secured in the carrier by bond- Lid Bond wires ing it to the bottom surface. The thermal expansion coefficient of the plastic Case is about 20 times that of silicon. Therefore, bonding the silicon chip directly Leads to the plastic case would result in such large thermal stresses that the reliabil- Chip ity would be seriously jeopardized. To avoid this problem, a lead frame made of a copper alloy with a thermal expansion coefficient close to that of silicon Lead frame Bond Pins is used as the bonding surface.
Details
-
File Typepdf
-
Upload Time-
-
Content LanguagesEnglish
-
Upload UserAnonymous/Not logged-in
-
File Pages70 Page
-
File Size-