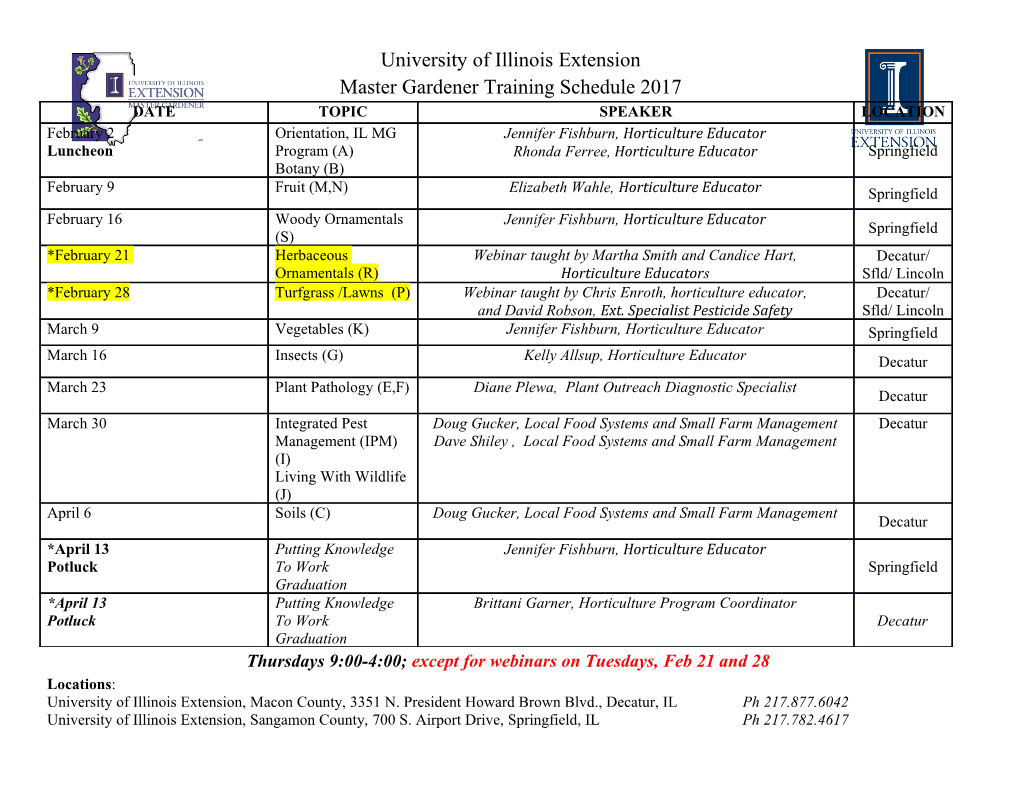
Overview of Altair's Thermal Control System and the Associated Technology Development Efforts Ryan A. Stephan NASA Johnson Space Center 2101 NASA Road One Houston, Texas 77058 281-483-7182 [email protected] Abstract—In early 2004, President Bush announced a bold Constellation Program, there are several project offices. vision for space exploration. One of the goals included in One of these projects includes the development of NASA's this vision is a return to the moon by 2020. In response to new lunar larder vehicle. The overall mission architecture this vision, NASA established the Constellation Program, for this vehicle, Altair, is very similar to Apollo's which includes several project offices. architecture. One of the Constellation projects is Altair, which is the next This paper will provide the reader with an overview of the generation Lunar Lander. The future Altair missions are Altair vehicle. In addition, Altair's thermal control system, very different than the Lunar missions accomplished during including the functionality and the hardware, will be the Apollo era. As such, there are several project risks and discussed. The paper will also describe the technology design challenges that have never before been addressed. development process and the various technology Due to the unique thermal environment associated with this developments currently underway. mission, many of these risks and design challenges are associated with the vehicle's thermal control system. 2. ALTAIR OVERVIEW NASA's Exploration Systems Mission Directorate (ESMD) includes the Exploration Technology Development Program The current lunar mission architecture requires the use of (ETDP). ETDP consists of several technology development two separate launch vehicles (Ares I and Ares V). In projects. The project chartered with miti gating the addition to these assets, a successful mission also requires aforementioned risks and design challenges is the Thermal an Earth Departure Stage (EDS), an Orion crewed vehicle, Control System Development for Exploration Project. and the aforementioned Lunar lander. The larger of the two launch vehicles, Ares V, first lifts the EDS and the Altair The current paper will summarize the Altair mission profile, into Low Earth Orbit (LEO). Shortly thereafter, the second the operational phases, and the thermal design challenges launch vehicle, Ares I, launches Orion into LEO with four unique to this particular vehicle. The paper will also crewmennbers on the vehicle. Orion and the Altair/EDS describe the technology development efforts being stack rendezvous in LEO and the EDS propels the now performed to mitigate the risks and design challenges. The integrated stack on a trajectory to the moon. The EDS is technology development project is performing a rigorous then jettisoned after the translunar injection burn. The development effort that includes thermal control system translunar cruise takes approximately three days to fluids, evaporators, heat exchangers, and Lunar surface complete. After the vehicles are at the moon, Altair is used radiators. to insert the vehicles into a 100 kin, circular Low Lunar Orbit (LLO). The vehicles spend approximately 24 hours in LLO before Altair separates from Orion and begins its TABLE OF CONTENTS descent to the Lunar surface. The entire descent phase takes 1. INTRODUCTION .................................................................1 approximately four hours to complete. Once on the surface, 2. ALTAIR OVERVIEW ...........................................................1 the Lunar surface phase is started and lasts for seven days. 3. ALTAIR THERMAL CONTROL SYSTEM OVERVIEW ........... 2 Throughout this time, the crew will perform up to seven 4. ALTAIR THERMAL TECHNOLOGY DEVELOPMENT extravehicular activities. Each EVA includes two EFFORTS...............................................................................5 crewmnembers for eight hours. In total, approximately 112 5. CONCLUSION ...............................................................9 man-hours will be spent outside of the pressurized cabin. 6. ACKNOWLEDGEMENTS ............................................9 Once the seven days have elapsed, the ascent module carries 7. REFERENCES ................................................................9 the four crewmenbers back to the awaiting Orion capsule where the vehicles rendezvous in LLO. Once aboard Orion. the Altair ascent module is jettisoned back to the Lunar 1. INTRODUCTION surface and Orion's service module pushes the crew back to In response to the president's 2004 vision for space Earth where the Orion crew module lands safely in the exploration, NASA is planning a human return to the moon ocean i. prior to 2020. In preparation for this mission, NASA has established the Constellation Program. Within the Altair consists of three functional components as shown in crewmembers, the overwhelming majority of the avionics; Figure 1. and a small ascent engine are included in the AM design. The AM is nominally pressurized to 10.2 psia while docked Airlock with Orion and 8.3 psia while on the lunar surface. The AL is attached to the AM through a docking tunnel and is maintained at the same pressure as the AM throughout the mission. The AL is used to ingress and egress the vehicle Ascent during extravehicular activities. This implies that the AL is Module depressurized and repressurized several times. As mentioned above, Altair is designed to take a crew of four to the Lunar surface and support operations for up to seven days. These mission requirements far exceed the Apollo capability of two crewmembers for a total of three days on the Lunar surface. In addition to these differences, another major difference is that Altair is required to perfoml the Lunar orbit insertion burn. On Apollo, the command/service module was tasked with performing the Lunar orbit insertion burn. However. because Orion had to be optimized for earlier LEO nvssions, the Lunar orbit insertion burn will be performed by Altair, which resulted in vca%-CI n a much heavier vehicle. Module 3. ALTAIR THERMAL CONTROL SYSTEM Figure 1. Altair Lunar Lander showing three functional OVERVIEW components (Airlock, Ascent Module, and Descent Module). Some degree of thernnal control is required for all types of spacecraft from the simplest satellites to the most complex The largest and most massive component is the Descent manned space vehicles. In its most basic form, thermal Module (DM). The DM is an unpressurized module and control is the maintenance of all vehicle surfaces and consists of composite struts and includes the main components within an appropriate temperature range. For propulsion system required to perform the Lunar orbit satellites, this requires that the thermal control system must insertion burn, lunar descent, and landing on the lunar maintain all of the equipment within its operating surface. The main propulsion system is composed of eight temperature range. Similar to satellites, the thermal control massive propulsion tanks. Of these tanks, four of them system for manned space vehicles must also maintain all of contain liquid hydrogen while the remaining four tanks are the equipment within its operating temperature. In addition filled with liquid oxygen. The propellant within these tanks to component level temperature maintenance, the manned is required to fuel the engine. The two smaller strictures spacecraft thermal control system must also safely maintain are referred to as the Ascent Module (AM) and the AirLock the internal cabin temperature within the appropriate (AL). As indicated by the name, the AM is used to return temperature requirements for crew comfort. the crew to Orion after the Lunar surface stay. The four An effective thermal control system must provide three There are a total of 33 coldplates included in the Altair basic functions. The three functions are heat acquisition, thermal control system. The overwhelming majority of heat transport, and heat rejection. Heat acquisition is the these coldplates are located on the vehicle's ascent module. process of transferring thermal energy from the heat source The coldplates are required to acquire excess thermal energy to the thermal control system. On the Altair Lander; heat from various avionics components and maintain these acquisition is accomplished usin g various coldplates and devices within their acceptable temperature limits. The heat exchangers as shown in Figure 2. Fi gure 2 is the heat-generating components include computers, inertial current thermal control system schematic. measurement units, monitors, etc. There are two types of heat exchangers included in the system design. The first Cold fates 20% PG/80% water 6 Internal Coldplates AM T HFC-245fa E H2O U Tank s, tloop p LCG Cabin FC 4 H/X H/X H/X ¢ fuel cell T T gas feed w HX _ _ fuel tali - U electronics ---' 9 Externs PumP A Cold lates T T _ p P FM T T ----------------- _----- filter IDJ PumP^ d) _X N = T--- -- ----- ------------------------------------------------------- -------------------------' PYro -------------------------- ------ AL 3 Internal T Coldplates radiator A radiator B T X ;, x radiator C r radiator D Figure 2. Altair Lander thermal control system schematic. 3 heat exchanger type is an air/liquid heat exchanger and 8000 acquires energy from an air loop and transfers it to the liquid LEO TLC: LLO LSO thermal control loop. There are two air/liquid heat 7000 exchangers included in the thermal control system design. m The second type of heat exchanger
Details
-
File Typepdf
-
Upload Time-
-
Content LanguagesEnglish
-
Upload UserAnonymous/Not logged-in
-
File Pages9 Page
-
File Size-