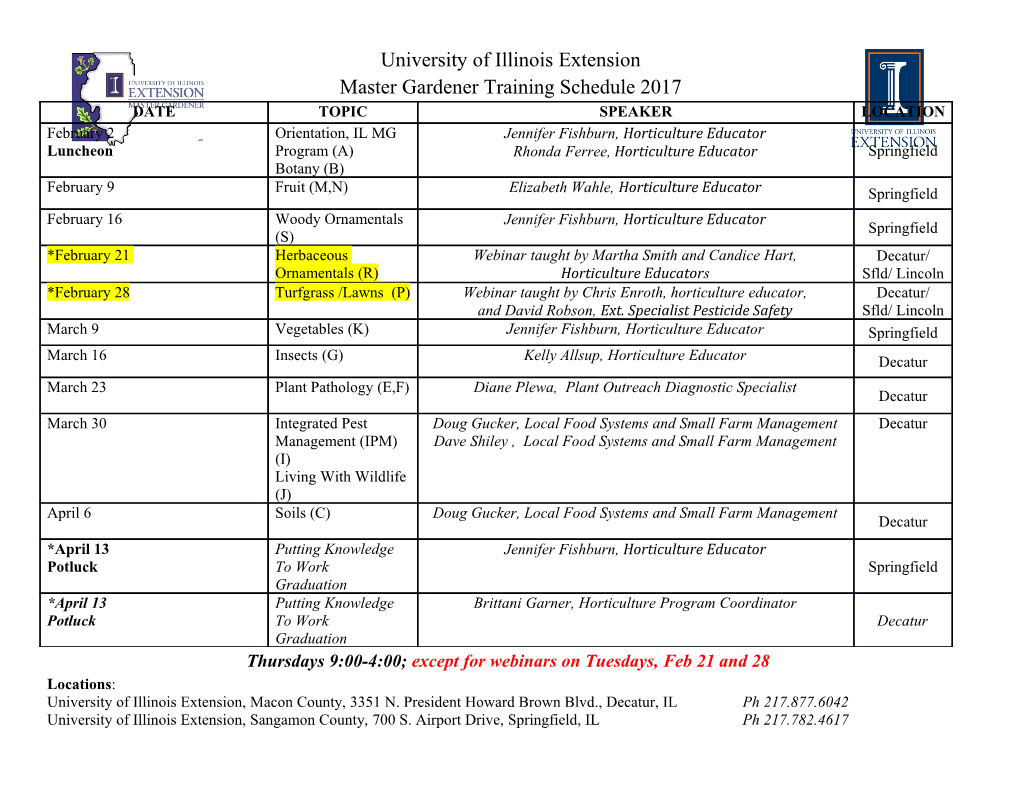
3,690,949, ‘United States PatentOf?ce Patented Sept. 12, 1972 1 2 3,690,949 or potassium gluconate, and sodium hydroxide. The solu ALKALINE BATH FOR NONETCHING REMOVAL tion is heated to elevated temperature, generally about OF SCALE FROM TITANIUM WORKPIECES 175° F. up to just below the boiling point of the solution Daniel Y. Ng, Brooklyn, N.Y., assignor to Purex and preferably between about 200°—30\0° F. Corporation, Ltd., Lakewood, Calif. The mixture dissolved in the solution consists essentially No Drawing. Filed Oct. 26, 1970, Ser. No. 84,110 of sodium or potassium nitrite at 2-25 weight percent and Int. Cl. C23g 1/22 preferably 5 weight percent sodium nitride, sodium or US. Cl. 134—2 16 Claims potassium nitrate at 2-25 Weight percent and preferably 5 weight percent sodium nitrate, sodium or potassium 10 gluconate at 2 to 25 weight percent and preferably 5 ABSTRACT OF THE DISCLOSURE weight percent sodium gluconate and the balance to 100 Titanium scale, generally comprising oxides and nitrides percent of sodium hydroxide. of titanium, may be removed from titanium workpieces The workpiece which may be degreased by conventional without simultaneously rapidly etching the workpiece by procedures in advance of scale removal, is subjected to subjecting the workpiece to a solution in water of from 15 the action of the treating solution having the composition 2 to 10 pounds per gallon of the mixture consisting essen indicated above, by applying the solution to the workpiece, tially of sodium or potassium nitrite, 2-25 weight per e.g. by spraying, brushing, ?ow coating and, particularly cent, sodium or potassium gluconate 2-25 weight percent, by immersion in a bath comprising the solution. When sodium or potassium nitrate, 2-25 weight percent, and immersed in a bath this may range from ?ve minutes up to sodium hydroxide, balance to 100 weight percent, e.g., by 20 thirty minutes or more, e.g. up to 8 hours for badly immersing the workpiece in an elevated temperature bath scaled forgings and castings. Multiple immersions in suc at temperatures between about 200° F. and 300° F. cessive or the same aqueous bath can be used where de sired. The titanium workpiece following treatment is free of BACKGROUND OF THE INVENTION 25 scale particularly of heat scale and welding discoloration (1) Field of the invention and the workpiece surface is left suitable for use subse quently in welding, bonding, plating or painting. Thus, This invention has to do with the removal of scale, such the descaling solution herein disclosed serves as a cleaner as oxides, nitrides, carbides and the like from the surfaces and a pickel for titanium. of titanium workpieces. Titanium scale and particularly 30 Titanium alloys can be similarly treated as titanium oxides of titanium constitutes virtually the most refractory workpieces. Titanium alloys with such materials as alu of all known materials. Titanium oxides have very high minum, vanadium, molybdenum, iron and nickel, e.g. up melting points and are resistant to almost all types of to 10 percent by weight of the alloy, may be cleaned by chemical attack. Many uses of titanium require the re the indicated procedures, as can niobium and tantalum moval of the natural oxide coating or an oxide coating 35 metals. induced by metal treating processes such as heat treating, EXAMPLE 1 anodizing or oxides produced in the use of a part. All parts and percentages are by weight (2) Prior art A titanium scale removal bath was prepared as follows: The heretofore accepted method for descaling titanium 40 A mixture of 5 percent sodium nitrite, 5 percent sodium and removing the oxides from workpiece surfaces has nitrate, 5 percent sodium gluconate, and correspondingly included an alkaline precleaning step, sometimes fol 85 percent sodium hydroxide was mixed dry. An exo lowed by an alkaline conditioning step and a post treat thermic reaction took place with introduction of water. ment in a bath of nitric-hydro?uoric acid. Titanium oxide The mixture was dissolved at the rate of 8 pounds per has been thought to be impervious to alkaline solutions 45 gallon of bath in water. The water solution was heated to and accordingly, efforts at improving the cleaning of 260° F. Titanium workpieces having oxides and nitride titanium workpieces have been directed primarily at the scale on their surfaces resulting from heat treating were development of more vigorous and more effective acids. immersed in the bath for periods ranging from 5 minutes In copending application Ser. No. 837,950, assigned to thirty minutes. The workpieces were removed from to the same assignee as this application, now US. Pat. 50 the bath, when the scale thereon had been removed, rinsed 3,553,015, a highly effective alkaline descaling system is and dried. The workpiece surfaces were noted to be clean disclosed. However, that system etches titanium work and suitable for welding, bonding, plating or painting pieces and where etching is not wanted, its use is not de operations. sirable. The present system is as effective in descaling but CONTROL A without etching the workpiece. 55 Example 1 is duplicated but omitting the sodium glu SUMMARY OF THE INVENTION conate. There was no appreciable removal of scale in an It has now been discovered that a highly alkaline solu hour and a half. tion such as an aqueous solution of sodium hydroxide is CONTROL B effective to remove scale from titanium workpieces where 60 Example 1 is duplicated employing a mixture of sodium the scale removing solution contains certain amounts of hydroxide and sodium gluconate. The resulting bath at sodium or potassium nitrate, nitrite and gluconate salts. tacked the titanium oxide, but at a slow rate, requiring Sodium gluconate may be formed in situ in a descaling at least ?ve times as long for removal. In addition, smut bath comprising the solution of reaction product of was produced on ‘the vtitanium surface which was re gluconic acid and sodium hydroxide. 65 movable only with a dip in 5-30 percent HNO3. DESCRIPTION OF THE PREFERRED ‘CONTROLS C, D AND E EMBODIMENTS Example 1 is duplicated but omitting the sodium hy in carrying out the present invention, a treating solution droxide, sodium nitrite or sodium nitrate. The resulting is prepared by dissolving in water from 2 to 10 pounds baths were ineffective for removing titanium scale from and preferably about 8 pounds of a mixture of sodium or titanium workpieces. potassium nitrite, sodium or potassium nitrate, sodium Accordingly, combination of any two of the cleaning 3,690,949 4 bath components is not effective as a descaler due to slow Weight percent ness of attack on the substrate and oxide and uneconomi Sodium or potassium nitrite _________________ .__. 2-25 cally long processing times. Sodium or potassium nitrate ________________ _- 2-25 CONTROL F Sodium or potassium gluconate ______________ __ 2-25 Sodium hydroxide, balance to 100. A titanium scale removal bath was prepared, according to the teachings of U.S. Ser. No. 837,950, as follows: A made up to a gallon with water and removing the work mixture of 18.5 percent sodium gluconate, 13.5 percent piece from the bath following scale removal. triethanolamine, and correspondingly 68 percent sodium 8. Method according to claim 7 in which said mixture contains 5 percent by weight of sodium nitrite. hydroxide was dissolved at the rate of 3.1 to 5 pounds per 10 gallon of bath in water. The water solution was heated to 9. Method according to claim 7 in which said mixture 200° F. Scaled titanium workpieces were removed from contains 5 percent by weight of sodium nitrate. the bath, rinsed and dried. The workpieces were noted to 10. Method according to claim 7 in which said mixture be clean and visibly etched to a dull matte ?nish to break contains 5 percent by weight sodium gluconate. up the sheen on ground areas and obliterate the grinding 11. Method according to claim 7 in which each salt is marks. present in an amount of 5 percent by weight in the mix In the typical practice of the present invention, contact ture. times between the solution and the workpiece will range 12. Method according to claim 7 in which said bath has between ?ve and ninety minutes with longer or shorter a temperature between 200° and 300° F. 13. Method according to claim 7 in which said work periods, depending on scale conditions, temperature of the 20 solution and concentration of the solution. piece is immersed in the bath for a period of 5 to 90 minutes. EXAMPLE 2 14. Method according to claim 7 in which said bath A solution having the composition given for the bath contains 8 pounds of said per gallon. in Example 1 and at 260° F. is sprayed onto a scaled 15. Method of descaling titanium comprising immers titanium workpiece in a closed chamber for 5 minutes. ing a scaled titanium workpiece for about 15 minutes in a The workpiece is thereafter rinsed and dried. The work bath heated to about 260° F., said bath being a solution piece surfaces are clean and free of scale. It is estimated of about 8 pounds per gallon of a mixture consisting the workpiece would have required 10 to 15 minutes to be essentially of cleaned in an immersion bath. 30 Weight percent I claim: Sodium nitrite _______________________________ __ 5 1. Method of descaling titanium comprising subjecting Sodium nitrate __ __ 5 a scaled titanium workpiece to a solution, heated to above Sodium gluconate ____________________________ .. 5 about 175° F., of from 2 to 10 pounds per gallon of a Sodium hydroxide, balance to 100.
Details
-
File Typepdf
-
Upload Time-
-
Content LanguagesEnglish
-
Upload UserAnonymous/Not logged-in
-
File Pages2 Page
-
File Size-