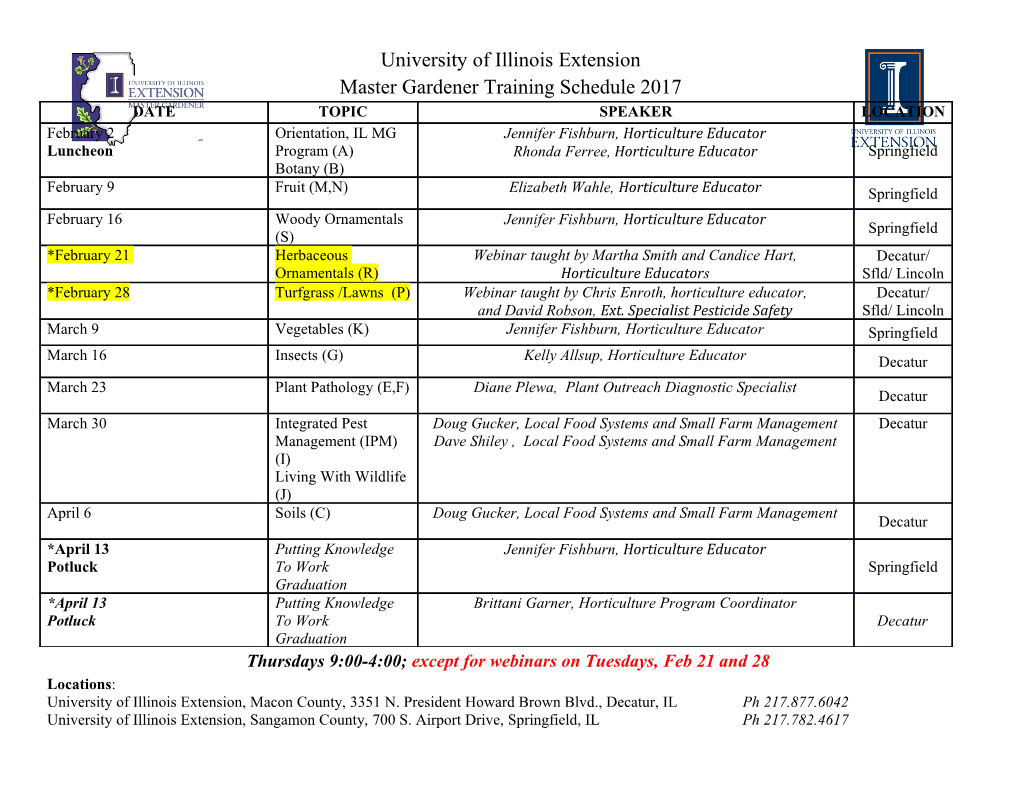
An embedded controller for an active magnetic bearing and drive electronic system A dissertation presented to The School of Electrical, Electronic and Computer Engineering North-West University In partial fulfilment of the requirements for the degree Magister Ingeneriae in Electrical and Electronic Engineering by Rikus le Roux Supervisor: Prof. G. van Schoor Assistant-supervisor: Mr. J. Jansen van Rensburg Project manager: Dr. E.O. Ranft November 2009 Potchefstroom Campus i ii Declaration I hereby declare that all the material incorporated in this thesis is my own original unaided work except where specific reference is made by name or in the form of a numbered reference. The word herein has not been submitted for a degree at another university. Signed: Rikus le Roux Date iii iv Project information Personal contact details: Name : Mr. R.R le Roux Organization : North-West University, School for Electrical and Electronic Engineering Address : Private bag X6001, Potchefstroom 2520 Telephone : (018) 299 4298 Fax : (018) 299 1977 E-Mail : [email protected] Supervisor contact details: Name : Prof. G. van Schoor Organization : North-West University, School for Electrical and Electronic Engineering Address : Private bag X6001, Potchefstroom 2520 Telephone : (018) 299 1962 Fax : (018) 299 1977 E-Mail : [email protected] Project manager: Name : Dr. E.O Ranft Organization : North-West University, School for Electrical and Electronic Engineering Address : Private bag X6001, Potchefstroom 2520 Telephone : (018) 299 1975 Fax : (018) 299 1977 E-Mail : [email protected] Assistant-supervisor: Name : Mr. J. Jansen van Rensburg Organization : North-West University, School for Electrical and Electronic Engineering Address : Private bag X6001, Potchefstroom 2520 Telephone : (018) 299 4298 Fax : (018) 299 1977 E-Mail : [email protected] v vi Summary The North-West University is currently conducting research in the area of active magnetic bearings (AMBs). The aim of this research is to establish a foundation for the development of AMB systems to be used in industrial applications. These systems should be reliable, effective and economical. The main research objective for this project is to further develop key technologies in order to realize an economical, reliable high-speed AMB drive system to be used in high-speed machinery. The proposed system is the AMB and drive electronic system (ADES), which is a digital control system for controlling AMBs in an industrial environment. The development of the ADES was a group effort. The focus of this dissertation was on selecting and implementing a suitable controller to be used in the ADES. The specification for the ADES was obtained from an industrial high-speed helium blower system. Selecting the controller was done by concurrently evaluating the conceptual main controller architectures and proposed system architectures. The system architecture is based on an industrial form factor, called compact peripheral component interconnect (PCI), or cPCI, which is an industrial version of PCI. The architectures were evaluated by performing trade-off studies and by weighing each architecture against a decision matrix, which weighs the architectures according to robustness, efficiency, cost, risk, reliability, flexibility and expandability. The selected system architecture includes a single board computer (SBC) with two PCI mezzanine cards (PMCs); a Virtex®-5 field programmable gate array (FPGA) based PMC module, for scheduling real-time tasks, and a Profibus PMC module, which will be used in future iterations of this project to interface the ADES with a programmable logic controller (PLC). The specified functions were designed, verified and implemented on the selected controller. The digital control was implemented on the FPGA-embedded PowerPC whereas the communication and filters were implemented on the FPGA. The sensitivity analysis placed the system into zone C, which implies a system normally considered unsatisfactory for long-term continuous operation. The system may operate in this condition for a limited period, until a suitable opportunity arises for remedial action. It was also determined that the system is stable for a step-input added to the reference position. Due to the stability of the control, it was possible to suspend the rotor at its designed rating of 19,000 r/min, but due to the high sensitivity rating, prolonged operation at this speed is not recommended. The selected architecture is versatile and powerful. The FPGA as a co-processor can be used to alleviate the load on the PowerPC, if additional features are required and not enough clock cycles are left on the PowerPC to implement them. The solution is compact, powerful and robust. These features, together with the industrial-based architecture of the system, make the ADES a suitable controller for controlling AMBs in an industrial system. vii viii Acknowledgements Great thanks go out to M-Tech Industrial, THRIP and the North-West University. Thank you for funding this project and for the opportunity to further my studies. I would also like to thank the following people for their contribution, support, knowledge and expertise throughout this project: Prof. George van Schoor, my supervisor, for his guidance, support and advice Mr. Jacques Jansen van Rensburg, my assistant-supervisor and friend, for his insight, advice and friendship Dr. Eugén Ranft, project manager, for managing and driving the project Mr. Cobus Potgieter, our industrial partner and consultant, who provided technical expertise, guidance, advice and VHDL training Dr. André Niemann, for his invaluable insights, input and for helping to design the filters Mr. Roelof Burger, for his design of the user interface Mr. Morné Neser, for his input and help regarding object orientated embedded C, as well as helping to solve general embedded C issues Ms. Elsebi Gadney, for her friendship over the last couple of years. Without her, this project would have been a whole lot less entertaining. My family, for their unwavering love, support, encouragement and prayer My girlfriend, Nicolene Swart, for her love, patience and support The McTronX research group and in the specific André, Elna, Elsebi, Gordon, and Kristoff, for their friendship and late night coffee breaks I would like to thank everyone who designed, built or implemented components cardinal to the success of the project. Without your hard work, there would not be a system to control or a rotor to suspend. Above all, I would like to thank our Heavenly Father, for this amazing opportunity He bestowed upon me. ―I can do everything through Him who gives me strength.‖ ix x “When you go through deep water and great trouble, I will be with you. When you go through rivers of difficulty, you will not drown! When you walk through the fire of oppression, you will not be burned up; the flames will not consume you. I will be with you…” Isaiah 43:2 (LB) xi xii “There is no extra magic inside the FPGA……… Just the usual magic.” Göran Bilski (Xilinx Employee) xiii xiv Table of contents Project information ....................................................................................................................... iii Summary ..................................................................................................................................... v Acknowledgements ..................................................................................................................... ix Table of contents ....................................................................................................................... xiv List of figures ........................................................................................................................... xviii List of tables ............................................................................................................................... xxi List of abbreviations and acronyms ......................................................................................... xxiii CHAPTER 1 ................................................................................................................................. 1 Introduction .................................................................................................................................. 1 1.1 Digital controllers ............................................................................................................ 1 1.2 Background..................................................................................................................... 2 1.2.1 High speed helium blower ..................................................................................... 2 1.2.2 Active magnetic bearings ....................................................................................... 3 1.2.3 Basic AMB operating principle ............................................................................... 4 1.2.4 Components of an AMB ......................................................................................... 4 1.3 System architecture ........................................................................................................ 5 1.3.1 Current system ....................................................................................................... 5 1.3.2 Proposed system ................................................................................................... 6 1.4 Problem statement ........................................................................................................
Details
-
File Typepdf
-
Upload Time-
-
Content LanguagesEnglish
-
Upload UserAnonymous/Not logged-in
-
File Pages217 Page
-
File Size-