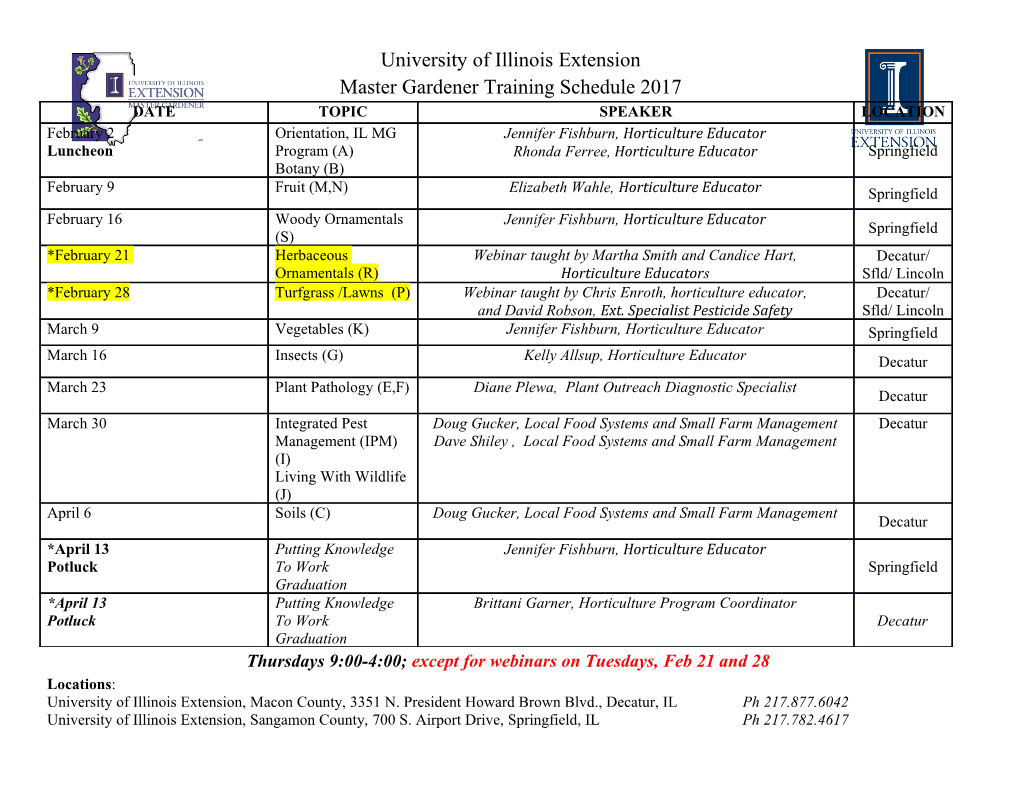
Impact of Core Shape and Material on the Acoustic Noise Emission of Medium Frequency, Medium Voltage Transformers Peng Shuai, Jurgen¨ Biela Laboratory for High Power Electronic Systems, ETH Zurich¨ Email: [email protected] Keywords <<Transformer>>, <<Acoustic noise>>, <<Optimisation>> Abstract Acoustic noise emission of transformers is mainly due to core vibration induced by reluctance force and magne- tostriction which is highly dependent on the core material and geometry. This paper investigates the vibration and acoustic noise of nanocrystalline cores with different geometric shapes based on FEM simulation and experimental measurements. Furthermore, the optimal design of medium frequency transformers (MFT) by using different core materials and geometric shapes is analyzed to find the most suitable core for MFT design with high efficiency, high power density and low acoustic noise emission. 1 Introduction In recent years, the application of solid state transformers (SST) (e.g. Fig. 1) in smart grids and traction systems have been widely investigated, e.g. [1, 2]. As key component of SST, the isolated DC-DC converter with integrated medium frequency transformer (MFT) is the focus of many publications. Much effort has been put on the optimal design of the MFT aimed on high power density and high efficiency [3, 4]. Due to the cooling and isolation requirement, the size reduction of the MFT by increasing the operating frequency is limited in the higher frequency range. This can be seen in Fig. 2 for the optimal design of MFT based on nanocrystalline cores. More detail about the design and optimization of the MFT can be found in [4]. In the considered application, the optimal switching frequency, which results in a minimal volume, is only a few kHz and leads to acoustic noise emission. The vibration and acoustic noise emission of electromagnetic devices is not a new research area. However, the focus in the past has been on electrical machines and line frequency transformers, which have been thoroughly investigated, e.g. in [5–7]. The applicability of these results on the MFT is limited because of the following reasons: Firstly, vibration is highly related to the magnetic and mechanical properties of the material (especially in case of magnetostriction). Magnetic cores of electrical machines and line frequency power transformers usually employ SiFe based electrical steels, which is not suitable for MFT due to the high power losses. Secondly, the mechanisms of noise generation in electrical machines differs from that in transformers, since electrical machines have rotating parts and a large air gap in the magnetic path. Moreover, due to the operation in kHz range, MFTs are smaller in size and weight compared to line frequency transformers for the same power level. Therefore, the mechanical properties of MFTs such as eigenfrequencies are significantly different from line frequency transformer. Figure 1: Example configuration of medium frequency solid state transformer. Figure 2: Minimized volume for a MFT design with VIT- ROPERM 500F for switching frequencies from 1 kHz to 16 kHz, detail in [4]. In a recent publication [8], vibration and acoustic noise measurements have been performed on several magnetic cores composed of various materials and with different geometric shapes. The comparison of measurement results basically indicate that the ring core based on nanocrystalline material exhibits lower vibration and noise emission. However, this kind of core may increase the total boxed volume of the transformer. As a trade-off between the power density and acoustic performance, the oval core is suggested for MFT design but its acoustic performance has not been verified. Although the acoustic noise emission is directly related to the vibration of the structure, the quantities of sound, e.g. the sound pressure level (SPL), indicate only the overall information about the vibration of the structure. In contrast, the vibrational quantities, e.g. surface velocities, directly indicate the local vibrational intensity, which is more practical for the analysis of the origin of the noise. In section 2, the basics of vibration modeling for magnetic cores are introduced, where a numerical model based on 2D FEM to simulate the core deformation is presented. This model is used to estimate the deformation of cores with different geometric shape in static case. In section 3, vibration and acoustic measurements are performed on several nanocrystalline cores (VITROPERM 500F) including rectangular, ring and oval shapes. In section 4, the optimal designs of MFT in terms of power density for different core materials and geometric shapes are compared. As conclusion, the results in previous sections are combined and the best core material/shape for MFT design which is not only quiet but also compact and efficient is identified. 2 FEM Model for Core Vibration Acoustic noise emission of MFTs basically involves: • generation of electromagnetic force by the electrical excitation of power electronic converters; • structural vibration of magnetic cores and windings induced by magnetic force and magnetostriction; • sound radiation from the surfaces of the transformer bodies and sound wave propagation in air. Accordingly, to calculate the acoustic noise emission of MFT, three physical models need to be taken into account. Due to the complexity of the physical process, analytical methods are usually only applicable for simple geometries and their accuracy is limited. For more accurate results, the couplings between these physical models need to be considered. Obviously, this requires more complicated models and more computational effort. For these reasons, the vibration/acoustic modeling of transformer is usually based on numerical methods, e.g. FEM. Table I: Properties of some magnetic materials [9]. Saturation Saturation Loss @ Material flux magnetostriction 0.2T/20kHz density [T] [µm/m] [W/kg] 6.5% SiFe 1.8 0 60 (50 µm) MnZn ferrite 0.45∼0.55 -2∼0 10∼15 Fe-based amorphous 1.56 27 8∼10 Metglas 2605SA1 Co-based amorphous 0.58 <0.2 3 VITROVAC 6025 Nanocrystalline VITROPERM 1.2 <0.5 1.8 500F Figure 4: Model of the laminated structure of tape wound Figure 3: Modeling process of core vibration. core. 2.1 Introduction of FEM model for core vibration As shown in Fig. 3, the calculation of core vibration includes three steps: • A. the electromagnetic model for solving the magnetic field distribution according to the electrical excitation; • B. the model for calculating magnetic forces and magnetostrictive strain based on the field distribution; • C. the mechanical model to solve the displacement (static case) or velocity/acceleration (dynamic case) due to the magnetic force and the magnetostriction. For calculation of the SPL, the acoustic model (D) as shown in the block with dashed line can be added after the mechanical model. In this work, the modeling only focuses on the core vibration. 2.1.1 Electromagnetic model (A in Fig. 3) In electromagnetic model, the electrical excitation and the mag- netic properties of the material together with the magnetic boundary conditions are employed to determine the magnetic field distribution, i.e. the local values of flux density and magnetic field strength. 2.1.2 Magnetic force and magnetostriction calculation (B in Fig. 3) In this step, the magnetic field dis- tribution is used as input to calculate the magnetic force (including Maxwell force and Lorentz force) and the magnetostriction. The Maxwell force is acting on the boundaries (surfaces) between two magnetic media with different magnetic permeabilities, which is typically associated with air-gap regions and joints of cores in transformers. The Maxwell stress tensor can be calculated according to the local distribution of the magnetic field as 1 s = ~H · (~B ·~n) − (~H ·~B) ·~n (1) m 2 where sm is the Maxwell stress tensor, ~H is the magnetic field strength, ~B is the magnetic flux density and~n is the vector in normal direction to the surface. For laminated cores, the effects of Maxwell force at the joints of core lamination sheets and between the sheets are introduced in [7]. ~ The Lorenz force is acting on the current-conducting windings and its volume force density f v is calculated as ~ ~ ~ f v = J × B (2) where~J is the current density in the conductor and ~B is the magnetic flux density at the location of the conductors. Magnetostriction model is an important part of the core vibration model. Generally, magnetostriction is described as the relative dimension change of the material in the direction of the applied magnetic field. However, magne- tostriction is also dependent on the mechanical stress s. Therefore, the magnetostrictive strain l in the direction of magnetic field can be expressed as a function of magnetic field strength and the mechanical stress, i.e. l = f (H;s). In case of SiFe, the magnetostriction is anisotropic and the saturation magnetostriction ls is dependent on the Si content. The 6.5% SiFe has approximately zero-magnetostriction [9], which is excellent in terms of acoustic per- formance. In case of amorphous and nanocrystalline alloys, the magnetostriction is isotropic. The saturation flux density Bs of Fe-rich amorphous alloy (e.g. Metglas 2605SA1) is relative high but the value of ls is also large. On the other hand, Co-rich amorphous alloy (e.g. VITROVAC 6025) could reach near-zero magnetostriction but the value of Bs is relative low. For Fe-based nanocrystalline alloy such as VITROPERM 500F, the Si content can be controlled at around 15-16at% (atomic percent) so that a near-zero magnetostriction can be achieved after nanocrystallization [9]. In Table I, the properties of some core materials are listed. Among these materials, the nanocrystalline alloy is the most suitable for MFT application due to the low specific loss and near-zero magne- tostriction. Also, its relative hight saturation flux density enables high power density designs. For the considered materials, only the Joule magnetostriction is taken into account, which means the volume of the material is constant.
Details
-
File Typepdf
-
Upload Time-
-
Content LanguagesEnglish
-
Upload UserAnonymous/Not logged-in
-
File Pages11 Page
-
File Size-