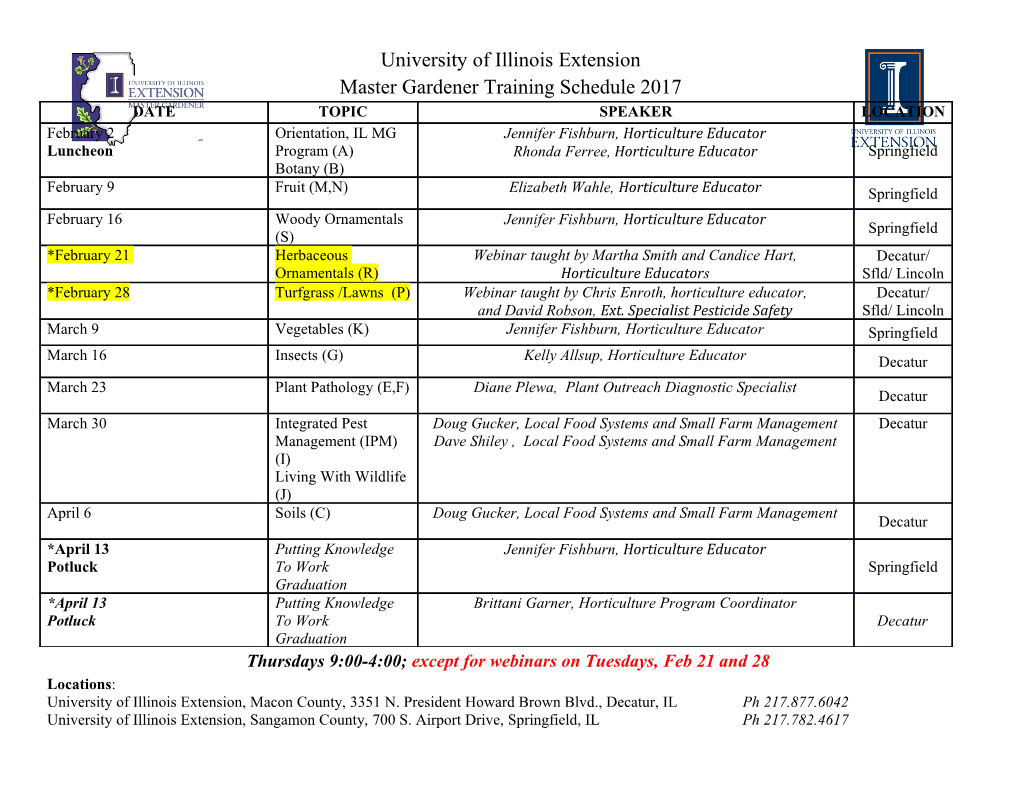
Carburizing of Low-Alloyed Chromium Materials – An Overview Sven Bengtsson1, Theodora Marcu2, Alexander Klekovkin3 1Höganäs AB, Höganäs, Sweden, 2 University of Trento, Trento, Italy, 3North American Hoganas Inc, Hollsopple, PA, USA ABSTRACT Case carburizing followed by quench and temper is a well established method of reaching very high properties for components like gears and sprockets. The well established materials on Fe-Cu-Mo-Ni base can all be case hardened using standard equipment and processes. Cr-containing PM materials, with their increased sensitivity to oxidation (and local carbon level), require special considerations. In this paper an overview of how different methods to carburise low alloyed chromium alloyed PM steels will be presented. Among methods discussed are gas carburizing, carbonitriding and vacuum carburizing. Specific emphasis is on selection of appropriate process with regard to density of the components and the formation of carbides. INTRODUCTION In many practical cases the performance of the structural component depends on the mechanical properties of the surface [1,2]. There are many heat treatment methods that focus on improving the properties of the surface. In this paper Gas Carburizing [3-6], Carbonitriding [3,5] and Vacuum Carburizing [3,7-12] will be discussed. These processes aim at achieving a high carbon concentration of carbon at the surface, gradually decreasing towards the core [3]. After austenitizing and quenching high-carbon martensite is formed at the surface while the core will transform into low-carbon martensite, bainite, pearlite, ferrite or a mixture thereof depending on cooling rate and alloy system. A secondary, but very important effect is that the high-carbon martensite will expand on formation and it will expand more than low-carbon martensite or any of the other structures that may form in the core. With a thin expanded surface region compressive stresses will form that are balanced by tensile stresses in the core, but since normally the core is much larger in cross-sectional area the tensile stresses will be lower while the compressive stresses will be significant. These compressive stresses will improve especially the fatigue performance of structural parts loaded in bending; a typical example is bending fatigue of a gear tooth. Presented at PM2008 in Washington, USA on June 9, 2008 1 In case carburizing, a process developed for solid steel, a low carbon (0,15-0,25 wt.% C) low alloy steel is heated to carburizing temperature in the austenite regime (typically 925 oC / 1700 oF) in a gas mixture consisting of CO, CO2, N2 and H2 [e.g. 3]. The nitrogen gas is virtually inert and its only function is as a dilutant and as carrier of heat. The mixture can be created in different ways, but its function as a carburizing agent is depending on the equilibrium of CO, CO2, H2, H2O and of the alloy system [1]. Examining this equilibrium in detail it is found that the amount of H2O is sufficient to oxidize materials based on the Fe-Cr system (e.g. Fe-1.5wt.%Cr alloy). For solid steel parts (e.g. DIN 16MnCr5, AISI 51200) this results in a thin oxidized layer [3,13]. This layer is often removed by e.g. grinding of gear teeth, while sometimes it is accepted. Some oxygen also penetrates the grain boundaries close to the surface forming a thin oxide network [3]. The formation of these oxides causes a depletion of carbon and possibly Chromium resulting in a less hardenable material and a softer structure close to the oxides. The compressive residual stresses will not form to the same extent if oxides are present at the surface [14]. Clearly it is desirable to avoid the formation of these oxides. Carbonitriding is basically the same process as Case Carburizing [3, 5, 15]. The major difference is that Ammonia (NH3) is added, normally towards the end of the carburizing period. The Ammonia decomposes on the surface of the components (and also on the furnace itself) into atomic nitrogen that can penetrate the component and into hydrogen gas. The nitrogen will diffuse into the part in a similar way as carbon does, driven by the concentration difference between the surface and the core. The nitrogen in solution in the austenite will increase the hardenability and therefore, the carbonitriding can be used to obtain martensite in alloy systems that would not normally transform into martensite after an ordinary case carburizing. The problem with oxidation is also present in this system since the equilibria are the same with the exception of the added ammonia. The ammonia influences the carburizing equilibria to small degree only, except that the amount of hydrogen gas increases slightly. However, since the addition of ammonia is normally (at least for PM parts) added towards the end of the austenitization, the oxidation has already taken place and will not revert even if the furnace conditions should improve slightly. Vacuum carburization [3, 7-9] (also referred to as low pressure carburizing) is performed by heating the part in a vacuum furnace to austenitization temperature and introducing a carburizing gas at low pressure into the chamber for a short period of time [1, 3, 10, 16]. The carburizing period is often referred to as the boost step. After this step the steep concentration profile crated during the short time is allowed to be “smoothed out” by diffusion. The boost/diffusion steps are repeated until a satisfactory case depth is reached. The parts are then quenched in gas, normally 6-20 bar of N2, or in oil [17]. Since the vacuum carburization is carried out in vacuum or with a carburizing or inert gas, there is no problem with oxidation. Problems encountered are uneven carburization or problems with quenching in gas. Gas quenching gives a slower quench rate compared to oil and water. If the parts are large or if the parts in the batch are packed tightly the available quench rate may be inadequate. The sintered density is an important parameter since it controls the surface available to the atmosphere [1, 3, 11, 19, 20]. At low densities (<6.8 g/cc) it is very difficult to control the case depth. The penetration of the carburizing gas is so quick that the entire part is carburized [18]. At a higher density it becomes easier to obtain a well defined case depth. At a density above 7.3 g/cc the material starts to behave very much as solid steel [18]. The gas penetration into the parts seems to be insignificant. These findings are true for all three carburizing methods. A consequence of the fast penetration of carburizing gas into the part is that carbides are formed at the surface that would not form in a solid steel of the same chemistry. These carbides are difficult to dissolve during later stages and should be avoided. The alloy system is also important for a successful hardening. The hardenability plays a more significant role the larger the parts become [21,22]. If gas quenching is employed this can be an issue already at sizes of 500 g. Furthermore, the equilibrium at the gas / part interface is also influenced by the alloying system. A steel with Chromium as an alloying element takes up more carbon from the atmosphere compared to a Presented at PM2008 in Washington, USA on June 9, 2008 2 part of pure iron. If Nickel is used as an alloying element the carbon uptake is less than pure iron. In recent years the cost for Molybdenum and Nickel has increased significantly. Furthermore, alternatives in the form of pre-alloyed powders based on Fe-Cr-Mo alloying system have been entering the market. These powders require sintering at low dew points in order avoid oxidation. These requirements apply in principle to the heat treatment process as well. In order to understand how severe the oxidizing problems for these materials are and in order to compare the outcome of a number of competing heat treatments the present investigation was performed. Processes The thermal treatments selected for this investigation are gas carburizing, carbonitriding and vacuum carburizing. Naturally there are more processes available, but these are three of the most interesting surface heat treatments for producing high performance PM parts. The description of the processes aims at showing the main characteristics of the methods without considering the details of all variants available. In some cases pre-treatments, are necessary. It can be the removal of remove surface contaminants, e.g. calibration oil. The presence of these contaminants may change the carburization behaviour. If the density is low it may be necessary to close the surface porosity by steam treating the parts. The heating of the parts must be uniform and the temperature during carburization must be the same for all parts. The furnace atmosphere must also have easy and uninterrupted access to all part surfaces that should be carburized. If parts are stacked on top of each other it can create a shadowing effect that prevents carburization of the surfaces that are not directly in contact with the atmosphere. There must also be free access to all surfaces that should be quenched. This is true regardless whether gas quenching or oil quenching is applied. The parts are then heated to the carburizing temperature. Here two contradicting lines of evolution of the processes are seen. A low carburization temperature will give less distortion after quench directly from the carburizing temperature. However, if the temperature is increased, the carburizing time will decrease significantly and hence the total process time [9]. Since the carburization is controlled by diffusion the temperature is the most powerful parameter in controlling the depth and amount of carbon diffusion into the parts [9, 23].
Details
-
File Typepdf
-
Upload Time-
-
Content LanguagesEnglish
-
Upload UserAnonymous/Not logged-in
-
File Pages15 Page
-
File Size-