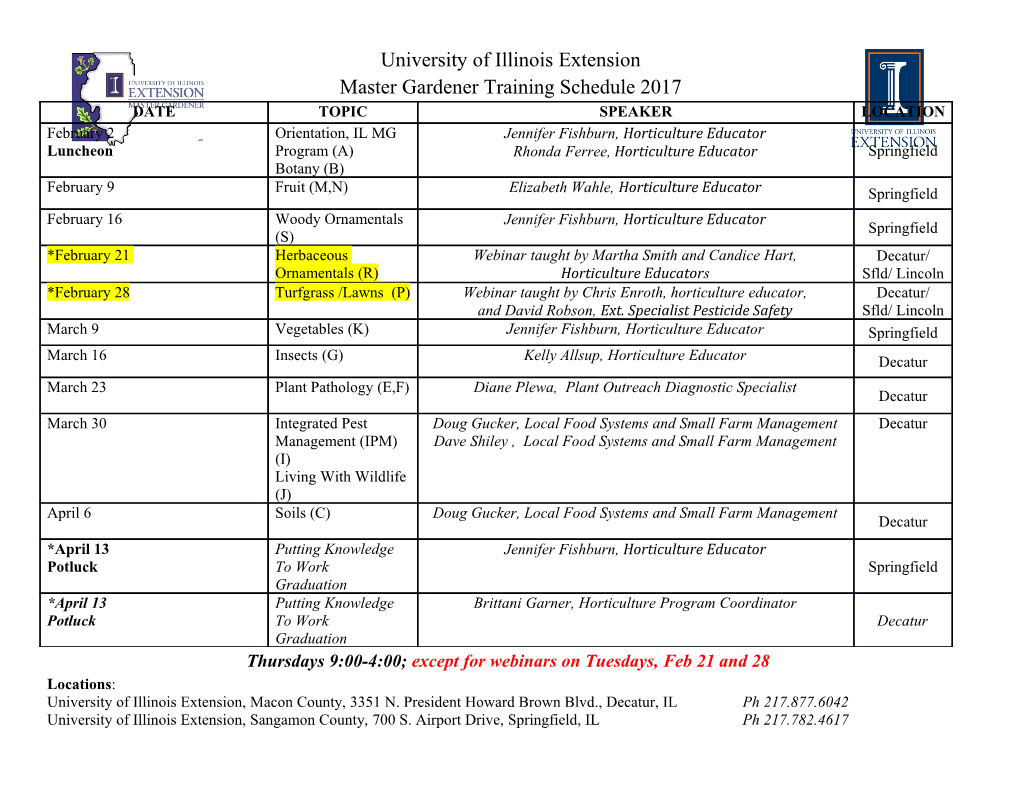
metals Article Probability-Statistical Estimation Method of Feed Influence on As-Turned Finish of Steels and Non-Ferrous Metals Petro Kryvyi 1, Volodymyr Dzyura 1, Nadiya Tymoshenko 2, Pavlo Maruschak 1, Justas Nugaras 3 and Olegas Prentkovskis 4,* 1 Department of Industrial Automation, Ternopil National Ivan Pul’uj Technical University, Rus’ka str. 56, 46001 Ternopil, Ukraine; [email protected] (P.K.); [email protected] (V.D.); [email protected] (P.M.) 2 Department of Higher Mathematics, Lviv Polytechnic National University, Ukraine, Bandera str. 12, Lviv 79013, Ukraine; [email protected] 3 Antanas Gustaitis0 Aviation Institute, Vilnius Gediminas Technical University, Linkmenu˛g. 28, LT-08217 Vilnius, Lithuania; [email protected] 4 Department of Mobile Machinery and Railway Transport, Faculty of Transport Engineering, Vilnius Gediminas Technical University, Plytines˙ g. 27, LT-10105 Vilnius, Lithuania; [email protected] * Correspondence: [email protected]; Tel.: +370-5-274-4784 Received: 11 October 2018; Accepted: 15 November 2018; Published: 19 November 2018 Abstract: Based on the experimental data on the roughness parameter Ra, which stands for the mean arithmetic deviation of the profile, as obtained in the process of turning test specimens from different materials with constant elements of the cutting mode (depth a and velocity v) and structural-geometric parameters of the cutting tool, but with different feed rates f, the probability-statistical method for estimating the influence of feed rate f on the resulting surface roughness by the parameter Ra is proposed using the theory of a small sample. Keywords: brass; steel; silumin; duralumin; roughness parameter; turning 1. Introduction One of the most important indicators of the surface quality after processing is its roughness, which to a large extent, provides for enhanced service properties of machine parts. For the quantitative evaluation of the surface roughness formed by turning, the current standard [1] envisages a set of appropriate parameters. The roughness of the surface formed by finish turning or thin turning should be evaluated by the parameter Ra, which stands for the arithmetic mean deviation of the profile [2,3]. In this paper, the effect of feed rate on this roughness parameter is investigated. Of all structural and geometric parameters of the cutting tool (cutter), such as the nose radius r; the outlet of the cutter l; the axial moment of inertia of the cutter holder section Iy; the tool cutting edge angle of the major, k1 and minor, kr1 cutting edges; the rake, g and clearance, a angles; and, the technological elements of the cutting mode a and v, the greatest influence on the parameter Ra comes from the cutting feed f. Taking into account the geometrical models of the cut-off layer and the remaining layer when finishing with a cutter that has nose radius r, i.e., when r ≥ a, it is recommended to determine the parameter 2 Ra according to the formula Ra = f /8 · r, kRa > 0, where kRa is the coefficient of proportionality and Rz is the microroughness height of the profile at ten points [2,3]. Thus, with increasing f, the function Ra = f ( f ) is a growing function according to the parabolic law. However, the above formula for determining Ra does not take into account the simultaneous action of many variable factors that are Metals 2018, 8, 965; doi:10.3390/met8110965 www.mdpi.com/journal/metals Metals 2018, 8, 965 2 of 12 stochastic in nature, especially the feed rate, and therefore, it is logical to assume that the parameter Ra is a random variable. Therefore, based on the above, the influence of the feed rate f on the surface roughness parameter Ra formed by the finish turning should be evaluated in the probabilistic aspect. The analysis of the existing literary sources [2–16] has shown that many scientists have paid much attention to the development of methods for conducting research on the formation and prediction of surface roughness obtained by turning. At the same time, it has been established from the analysis of literary [17–23] sources that there is no unanimous opinion about the nature of the feed effect on roughness, in particular, on the parameter Ra. Thus, one of the first scientific papers [22] dedicated to the research on the influence of cutting elements, geometric parameters of the cutter, and the value of its wear on roughness, indicates that an increase in the feed rate within the range of 0.07 ≤ f ≤ 0.26 mm/rev leads to a monotonous increase in the roughness parameter, such as the maximum height of roughness Hmax, which, according to [1], corresponds to the greatest height of roughness Rzmax. At the same time, the influence of s on Hmax was assessed at a depth of 0.5 ≤ a ≤ 1.0 mm, which is recommended for semi-rough and rough processing. In addition, the constructive and geometric parameters of the tools that were used in the research were not indicated. According to Arshinov [24], when cutting without a lubricating and cooling medium, an increase in the feed rate from f = 0.075 mm/rev to f = 0.21 mm/rev leads to an increase in the Ra values from 1.3 µm to 2.7 µm, this dependence being of linear nature. According to Isaev [4,5], the analysis of the effect of the feed rate s on the roughness parameter, such as the height of the profile roughness at ten ◦ ◦ ◦ 0 ◦ points Rz when turning steel EI 107 with a cutter having g = 15 , l = 0 , j = 45 , j = 20 , r = 1.75 mm shows the power dependence of Rz on f. The intensity of the influence of s on Rz depends on the feed rate value. When turning with the feed rate f < 0.05 mm/rev, its effect on Rz is weakened. At the same time, it follows from the calculation formulas of A.I. Isaev [4,5] that the dependence of Rz on f is linear and it is described by the function Rz = kRz · Ra. It was noted in [19] that among the elements of the cutting mode, such as a, f, v, the feed rate has the greatest influence on the roughness of the treated surface. Thus, when turning steel 45 with an increase in the cutting rate from 42 m/min to 84 m/min (twice), the height of roughness decreased by 1.5 times, and with a decrease in the feed rate from 0.3 mm/rev to 0.15 mm/rev (twice), the height of roughness decreased by six times. In addition, it was noted that in the processing of carbon steel with the feed rate f < 0.06 mm/rev, there was no decrease in the height of roughness, which contradicts the data given in [9,12,13]. The analysis of the empirical formulas for determining the roughness parameter given in [2–5,24,25] indicates different values of the power index yRa , which characterizes the influence of f on Ra. In addition, it is suggested in [2] that, depending on the material being processed, it may vary within the range 0.54 < yRa < 1.1. In [20], the theoretical dependences are given, which link the surface roughness to the elements of the cutting mode, in particular, the feed rate. Such models are inaccurate and many researchers are engaged in their improvement by introducing additional parameters. In [23], a surface imitation model is proposed for modeling the surface profile that was obtained by turning with known vibration characteristics. It was found that radially directed vibrations affect the surface roughness much more than tangentially directed or axial vibrations. A more detailed study of the influence of geometric parameters of the cutting tool and the hardness of the workpiece material on the surface quality and cutting force in the process of finish turning is given in [24,26]. An in-depth study of the influence of the cutting tool vibration on the formation of surface roughness in the course of dry turning is illustrated in [25]. Six parameters were investigated, in particular, the material of the workpiece and the length of the cutting tool. The dispersion analysis and the analysis of the interaction between experimental data showed that the feed rate and the rounding radius of the cutter nose are the most influential parameters. Smaller roughness was obtained at a high-speed processing with a low feed rate and a large rounding radius at the cutter nose. The analysis of the above-mentioned literary sources has shown that, at present, there are two views on the nature of the influence of f on Ra: according to the first view, this dependence is monotonically Metals 2018, 8, x FOR PEER REVIEW 3 of 13 Metals 2018, 8, 965 3 of 12 mm/rev) results in a decrease in roughness to a certain minimum value, and a further increase in s increasing,results in its and growth. to the second—an increase in the feed rate from low to high (f > 0.02 mm/rev) results in a decreaseThe analysis in roughness of a large to number a certain of minimumpublications value, describing and a further the results increase of research in s results on the in its influence growth. of f onThe the analysis roughness of a largeparameter number Ra did of publications not reveal the describing repetition the of results experiments, of research which on may the influence indicate ofa deterministicf on the roughness approach parameter in conductingRa did notsuch reveal studies. the repetitionGiven that of a experiments,large number which of factors may [2,16,25], indicate awhich deterministic by their nature approach are inrandom conducting variables, such act studies.
Details
-
File Typepdf
-
Upload Time-
-
Content LanguagesEnglish
-
Upload UserAnonymous/Not logged-in
-
File Pages12 Page
-
File Size-