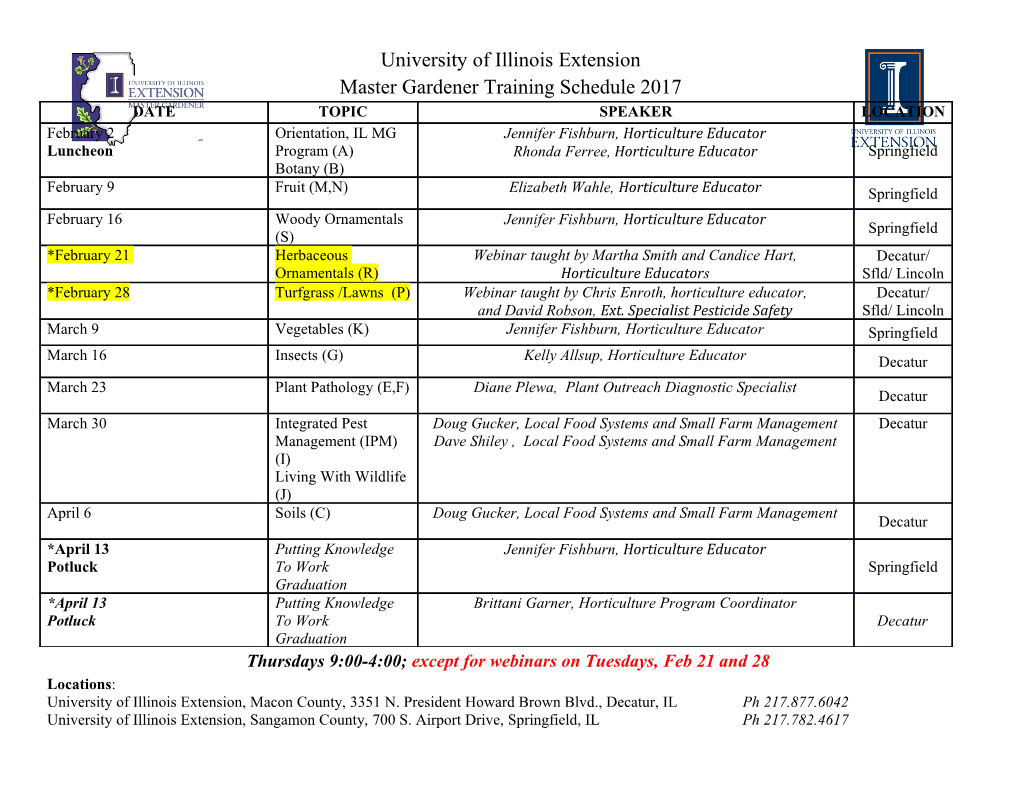
ASM Specialty Handbook Carbon and Alloy Steels Copyright © 1996 ASM International® J.R. Davis, Editor All rights reserved www.asminternational.org General Introduction to Carbon and Alloy Steels STEELS constitute the most widely used cate­ large quantities to very precise specifications. (200 to 300 MPa. or 30 to 40 ksi) with excellent gory of metallic material, primarily because they They also provide a wide range of mechanical ductility to yield strengths exceeding 1400 MPa can be manufactured relatively inexpensively in properties, from moderate yield strength levels (200 ksi) with fracture !Q!!ghness levels as high as 110 MPa;lffi (100 ksi"Vin.). As shown in Table 1, carbon steels-steels Table 1 Net shipments of U.S. steel mill products-all grades containing less than 2% total alloying elements­ are by far the most frequently used steel (more 1992 1991 than 90% of the steel shipped in the United States Thns(a) Steel product~ % Thns(n) % is carbon steel). Alloy steels-steels containing a Ingots and steel for castings 215 0.3 244 0.3 total alloy content from 2.07% up to approxi­ Blooms, slabs, billets 2,255 2.7 2,305 2.9 mately 10%-rank second. Tool steels, as well as Wire rods 4,511 5.5 4,366 5.5 the more highly alloyed (minimum 11% Cr) Structural shapes ~75 mm, or 3 in.) 5,081 6.2 5,245 6.7 stainless steels, are both produced in lower ton­ Steel piling 454 0.6 430 0.5 Plates (cut lengths) 4,362 5.3 4,275 5.4 nages than are either carbon or alloy steels. Tool Plates (in coils) 2,740 3.3 2,667 3.4 steels and stainless steels will not be addressed in Rllil• this article as these materials are reviewed in Standard (over 27 kg. or 60 !b) 435 0.5 382 0.5 previously published Volumes of the ASM Spe­ All other 5 0.0 16 0.0 cialty Handbook series. Railroad accessories 122 0.1 89 0.1 It should be noted that there is widespread """Hot rolled 5,806 7.1 5,431 6.9 inconsistency regarding the use of the terms "al­ Bar-size light shapes 1,119 1.4 1,157 1.5 loy steels" and "low-alloy steels." For the pur­ Reinforcing 4,781 5.8 4,859 6.2 poses of this Handbook, the terms are synony­ Cold finished 1,458 1.8 1,341 1.7 Tho! steel 64 0.1 51 0.1 mous/interchangeable, i.e., they both refer to Pipe and tubing steels, exclusive of tool steels, containing ap­ Standard pipe 1,062 1.3 970 1.2 proximately 2 to 10% total alloying content. Oil country goods 979 1.2 1,077 1.4 Tills article will review steelmaking practices Line 1,110 1.3 1,439 1.8 used to produce carbon and a11oy steel products, Mechanica1 790 1.0 744 0.9 Pressure 48 0.1 49 0.1 describe the various systems used to classify car­ Structural 142 0.2 151 0.2 bon and alloy steels, and discuss the effects of Pipe for piling 35 0.0 24 0.0 alloying elements on the properties and/or char­ Stainless 32 0.0 34 0.0 acteristics of steels. Although emphasis has been Wire-drawn 900 1.1 865 1.1 placed on wrought steels, steel castings and pow­ Black plate 230 0.3 249 0.3 Tmplate 2,715 3.3 2,754 3.5 der metallurgy (PIM) products are also briefly Tm-free steel 904 1.1 964 1.2 described. This article also serves as a roadmap to Tin--coated sheets 78 0.1 74 0.1 the other articles in this Volume that provide Shee~ supplemental or more detailed information on the Hot rolled 13,361 1.62 13,161 16.7 fabrication characteristics of steels or their per­ Cold rolled 12,692 15.4 11,532 14.6 Sheets and strip formance in various environments/applications. Ga1vanized hot dipped 8,199 10.0 6,910 8.8 Electrolytic 2,390 2.9 2,099 2.7 All other metallic coated 1,348 1.6 1,146 1.5 Electrica1 436 0.5 458 0.6 Steel Processing Technology Strip Hot rolled 550 0.7 533 0.7 Figure 1 represents the steelmaking flowlines Cold rolled 832 1.0 755 1.0 for flat (sheet and strip) steel products (the same Thtal steel mill products 82,241 100.0 78,846 100.0 Carl>on 76,625 93.2 73,480 93.2 melting, refining, and casting methods are used to Stainless 1,514 1.8 1,449 1.8 p'roduce other steel produCts such as structural Alloy (other than stainless) 4,101 5.0 3,917 5.0 shapes, bars, rods and wire, and pipe and tube). Liquid iron, commonly referred to as pig iron, is (a) Thousands of net tons. Source: American Iron and Steel Institute produced in a blast furnace from iron ore, lime- 4 I General Introduction A Pellets Direct aIron ore ~ Sinter ~ -- Limestone -Crushed Coal Coke ovens Slag Molten iron Molten steel Note: Vacuum treatment Electric furnace of liquid steels is frequently used for making super­ Scrap refined metals for advanced technology end uses. Ladle metallurgy Note: Ladle metallurgy is aLime and flux - Open hearth furnace used to control conditions within the ladle to improve productivity in preceding and subsequent process­ ing steps and the quality of the final product-these conditions can include temperature, pressure, chemistry, and bath agitation through stirring. Oxygen Basic oxygen furnace or 0-BOP Fig. 1 Flow diagram showing the principal steelmaking steps involved in converting raw materials into flat mill product forms. Source: American Iron and Steel Institute stone, and coal (coke), but contains excessively the silicon, manganese, and carbon to acceptably materials, which have a major influence on the high levels of silicon, manganese, carbon, and low levels in the resulting steel. The steel is then final quality, formability, and cost. other elements. This liquid iron, together with tapped or poured into refractory-lined ladles. scrap and fluxing agents, is then introduced into During this tapping operation, alloying elements Steelmaking Furnaces and Processes either a basic oxygen furnace or an electric fur­ that will detennine the final chemistry of the steel The most commonly used steehnaking fur­ nace for further refining with oXygen that reduces are added to the ladle along with deoxidizing naces are the basic oxygen furnace, acid or basic General Introduction to Carbon and Alloy Steels I 5 Continuous casting 000000000000000 Slab Conventional ingot teeming Cold strip Ingot breakdown mill Batch annealing of stacked coils Tin mill products ~ Temper rolling Galvanized and other coated flat rolled products Fig. 1 (continued) Flow diagram showing the principal steelmaking steps involved in converting raw materials into flat mill product forms. Source: American Iron and Steel Institute electric furnaces, and basic open-hearth furnaces. operation. However, the open-hearth process large tiltable vessel lined with basic refractory The distinction between acid and basic is made now has been superseded largely by the faster and material and the necessary accessory equipment. according to the character of the furnace lining more efficient basic oxygen process. As a result, After the furnace is charged with molten pig iron and the flux used in the furnace. A basic furnace it wi11 not be discussed further. Table 2 compares (which usually comprises 65 to 75% of the is required to reduce the phosphorus content from steel production by type of furnace and steel charge), scrap steel, and fluxes, a lance is brought that of typical pig iron to the maximum amount grade. down near the surface of the molten metal and a allowable in most grades of steel. The Basic Oxygen Process (BOP). A sche­ jet of high-velocity oxygen impinges upon the Historically, the open-hearth process was the matic representation of a basic oxygen furnace is metal The oxygen reacts with carbon and other principal steehnaking process for hig'hMtonnage shown in Fig. 2. This arrangement consists of a impurities in the steel to form liquid compounds 6 I General Introduction Table 2 U.S. raw steel production (in thousands of nettons) by type offurnace and steel grade See also Table 3. O~nhearth Baslcox~~"Eroces.'l y~ Carbon Alloy Total Carbon Alloy 1btal Carbon Alloy "'"'"' ........ Total 1992 53,745 3,896 57,642 28,713 4,602 1,993 35,308 1991 1,407 2 1,408 48,895 3,819 52,714 27,577 4,319 1,878 33,774 1990 3,209 287 3,496 53,808 4,663 58,471 29,573 5,330 2,037 36,939 1989 4,229 213 4,442 53,677 4,671 58,348 28,325 4,902 1,926 35,154 1988 4,915 203 5,118 52,918 5,042 57,960 28,989 5,657 2,199 36,846 Source: American Iron and Steel Institute /Belt conveyor = Storage bins for lime, fluospar, iron ore pellets, dolomitic lime, and so on o, -------- %hole lance t Reinforced mouth of furnace ~Oxygen lance Crane Iron droplets Slag pol Three-phase I Hot metal transfer foaming slag ladle on transfer car I Molten iron Dissolving bundles of scrap 5m (a) (b) Fig. 2 Principal zones and component parts of a basic oxygen furnace for the production of steel in a melt shop. (a) Typical plant layout. (b) Basic oxygen furnace vessel that dissolve in the slag and gases that escape lance. ln all other respects, it is similar to the the bottom refractory plug for the vessel that from the top of the vessel.
Details
-
File Typepdf
-
Upload Time-
-
Content LanguagesEnglish
-
Upload UserAnonymous/Not logged-in
-
File Pages10 Page
-
File Size-