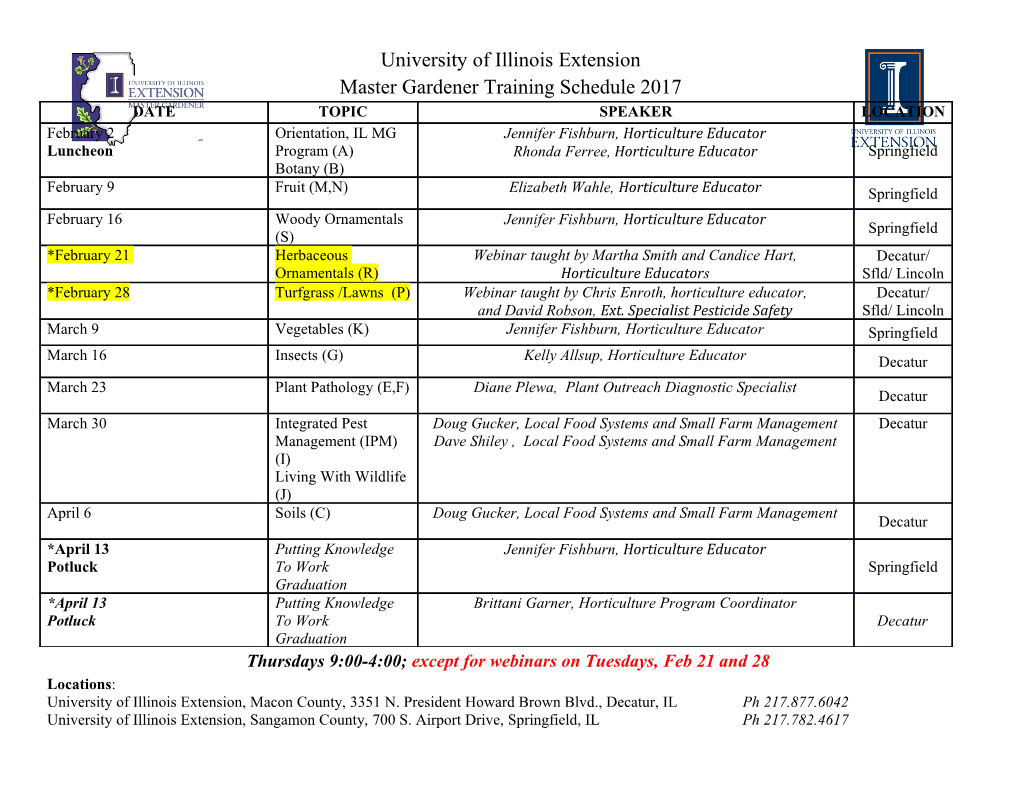
*Manuscript Click here to view linked References 1 2 3 4 5 6 7 8 9 Generalized Reynolds number and viscosity definitions 10 11 for non-Newtonian fluid flow in ducts of non-uniform 12 13 cross-section 14 15 16 D. Cresp´ı-Llorensb, P. Vicenteb, A. Viedmaa 17 a 18 Dep. Ing. T´ermica y de Fluidos. Universidad Polit´ecnica de Cartagena. Dr. 19 Fleming, s/n (30202). Cartagena (Spain). 20 bDep. Ing. Mec´anica y Energ´ıa. Universidad Miguel Hern´andez. Av. Universidad, s/n 21 (03202). Elche (Spain). [email protected] 22 23 24 25 26 Abstract 27 28 29 This work presents and experimental study of the generalization method 30 31 of the Reynolds number and the viscosity of pseudoplastic fluid flow in ducts 32 of non-uniform cross-section. This method will permit to reduce 1 degree of 33 34 freedom of hydrodynamical and thermal problems in those ducts. A review 35 36 of the state of the art has been undertaken and the generalization equation 37 38 proposed for ducts of uniform cross section has been used as a starting point. 39 40 The results obtained with this equation have not been found satisfactory and 41 42 a new one has been proposed. 43 44 Specifically, the procedure has been developed for two models of scraped 45 46 surface heat exchanger with reciprocating scrapers. For both models, the 47 48 scraper consists of a concentric rod inserted in each tube of the heat ex- 49 50 changer, mounting an array of plugs that fit the inner tube wall. The two 51 52 models studied differ in the design of the plug. 53 54 The procedure to perform the generalization method out of experimental 55 data is accurately detailed in the present document. 56 57 58 59 Preprint submitted to Journal name February 6, 2015 60 61 62 63 64 65 1 2 3 4 5 6 7 8 9 Keywords: non Newtonian, viscosity, generalized Reynolds number, 10 11 non-uniform cross-section, Power Law 12 13 14 15 16 17 18 19 20 21 22 23 24 25 26 27 28 29 30 31 32 33 34 35 36 37 38 39 40 41 42 43 44 45 46 47 48 49 50 51 52 53 54 55 56 57 58 59 2 60 61 62 63 64 65 1 2 3 4 5 6 7 8 9 1 Nomenclature 10 11 n 12 2 m flow consistency index (rheological property), [Pa.s ] 13 14 15 3 D inner diameter of the heat exchanger pipe, [m] 16 17 4 D inner diameter of the viscometer pipe, [m] 18 v 19 20 5 d diameter of the insert device shaft, [m] 21 22 23 6 Dh hydraulic diameter Dh = D d, [m] 24 − 25 26 7 Lp pipe length between pressure ports of test section, [m] 27 28 8 29 Lv viscometer pipe length between pressure ports, [m] 30 31 9 N number of measures for each experiment 32 33 34 10 P pitch of the insert devices, [m] 35 36 37 11 p pressure, [Pa] 38 39 40 12 pL pressure drop by length unit, [Pa/m] 41 42 3 13 Q flow rate, [m /s] 43 44 2 45 14 S main cross-section, [m ] 46 47 48 15 ub bulk velocity, [m/s] 49 50 51 16 Dimensionless numbers 52 53 54 17 n flow behaviour index (rheological property) 55 56 18 Re Reynolds number, Re = ρubDh/µ 57 58 59 3 60 61 62 63 64 65 1 2 3 4 5 6 7 8 9 19 2 f Fanning friction factor, f = ∆pDh/2Lρub 10 11 12 20 ξ pressure drop constant dependent on the duct geometry 13 14 15 21 a to e correlation constants 16 17 22 Greek Symbols 18 19 −1 20 23 α exponent of Reb in experimental correlations, [s ] 21 22 −1 23 24 γ shear rate, [s ] 24 25 25 µ fluid viscosity (exact definition indicated by the subindex), [Pa.s] 26 27 28 26 φ function of n 29 30 3 31 27 Ψ unknown function, [kg/m ] 32 33 28 3 34 ρ fluid density, [kg/m ] 35 36 29 τ shear stress, [Pa] 37 38 39 30 Subscripts 40 41 42 31 b Reynolds number or viscosity defined by Eq. 2 43 44 32 g Reynolds number or viscosity defined by Eqs. 18 and 19 45 46 47 33 MR defined by Metzner and Reed (1955) (Eqs. 4and 5) 48 49 50 34 DL defined using the equation from Delplace and Leuliet (1995) (Eqs. 51 52 35 6 and 7) 53 54 36 ξ = an generalization based on pressure drop in annulus, where ξ is ob- 55 56 37 tained from Kozicki et al. (1966)) 57 58 59 4 60 61 62 63 64 65 1 2 3 4 5 6 7 8 9 38 ξ = exp ξ in Eqs. 6 and 7 is obtained by experimental correlation 10 11 12 39 v belonging to the viscometer 13 14 15 40 w at the inside pipe wall 16 17 18 41 1. Introduction 19 20 21 42 Many fluids in the food and chemical or petrochemical industries are 22 23 43 non-Newtonian. In such applications the determination of parameters such 24 25 44 as the friction factor and the Nusselt number is necessary for the calculation 26 27 45 of pressure losses and heat transfer rates or temperature distributions in heat 28 29 46 exchangers. This can be achieved experimentally or theoretically by solving 30 47 31 the appropriate transport equations for typical common geometries (circular 32 48 ducts, flat ducts, etc.). An important characteristic of these fluids is that 33 34 49 they have large apparent viscosities; therefore, laminar flow conditions occur 35 36 50 more often than with Newtonian fluids. 37 38 51 Pseudoplastic fluids are the most common non-Newtonian fluids in the 39 40 52 process industry Chhabra and Richardson (2008); Cancela et al. (2005). For 41 42 53 this fluids, in a certain range of shear stress, the viscosity decreases as shear 43 44 54 stress increases. To describe this behaviour, various mathematical models 45 46 55 can be used. Among them, the Power Law model is widely used because of 47 48 56 its simplicity. The model can be used to explain the viscosity of a specific 49 50 57 fluid in a limited range of shear rates. The Power Law model (Eq. 1) has two 51 58 52 parameters: the flow behaviour index n and the flow consistency index m. 53 59 Thus, the hydrodynamic and thermal problems have one additional degree 54 55 56 57 58 59 5 60 61 62 63 64 65 1 2 3 4 5 6 7 8 9 60 of freedom, which increases their complexity. 10 11 n 12 τ = mγ (1) 13 14 61 For example, let us consider the study of pressure drop in fully developed 15 16 62 flow in pipes for forced convection. The list of significant variables can be 17 18 63 pL = Ψ(D,ub, ρ, m, n). Through the Pi Theorem the problem simplifies to 19 20 64 three non-dimensional numbers f = Ψ(Re, n). Consequently, the relation 21 22 65 between Re and the friction factor will be different for fluids with different 23 24 66 n. With the previous list of variables, the Reynolds number for power law 25 67 fluids would be, 26 2−n n 27 ρub D ρubD Reb = = (2) 28 m µb 29 n−1 30 68 , where viscosity would be defined by µb = m(ub/D) . Other viscosity 31 32 69 definitions, with the same dimensional equations, are possible and will be 33 34 70 more useful for the study of pressure drop in heat exchangers. 35 71 Metzner and Reed (1955) where the first to use the so called generalization 36 37 72 method. They analytically obtained the relation between the friction factor 38 39 73 f and the Reynolds number Reb for the fully developed laminar flow in a 40 41 74 pipe. Then, they defined a new Reynolds number ReMR, being the one 42 43 75 which multiplied by the friction factor gave the same result that the one 44 45 76 given by a Newtonian fluid. 46 47 48 49 f ReMR =16 (3) 77 × 50 ρu2−nDn ρu D 51 b b ReMR = n−1 n = (4) 52 m 8 ((3n + 1)/(4n)) µMR 53 78 , being the generalized viscosity for the flow in pipes 54 − 55 n 1 n ub n−1 3n +1 56 µMR = m 8 (5) 57 Dh 4n 58 59 6 60 61 62 63 64 65 1 2 3 4 5 6 7 8 9 79 Kozicki et al. (1966) obtained a relation between friction factor and Reynolds 10 11 80 number for various simple geometries (circular pipes, parallel plates, concen- 12 13 81 tric annuli and rectangular, isosceles triangular and elliptical ducts) as a 14 15 82 function of two parameters. Afterwards, Delplace and Leuliet (1995) re- 16 17 83 duced those parameters to one. Therefore, the definition of Metzner and 18 19 84 Reed (1955) can be applied to geometries with uniform cross-section as a 20 21 85 function of a single geometric constant. 22 2−n n ρub Dh 23 ReDL = n (6) 24 n−1 24n+ξ m ξ (24+ξ)n 25 86 × 26 n−1 n ub n−1 24n + ξ 27 µDL = m ξ (7) Dh (24 + ξ)n 28 87 29 f ReDL =2ξ (8) 30 × 31 88 For duct geometries of uniform cross-section different from the ones stud- 32 33 89 ied by Kozicki et al.
Details
-
File Typepdf
-
Upload Time-
-
Content LanguagesEnglish
-
Upload UserAnonymous/Not logged-in
-
File Pages40 Page
-
File Size-