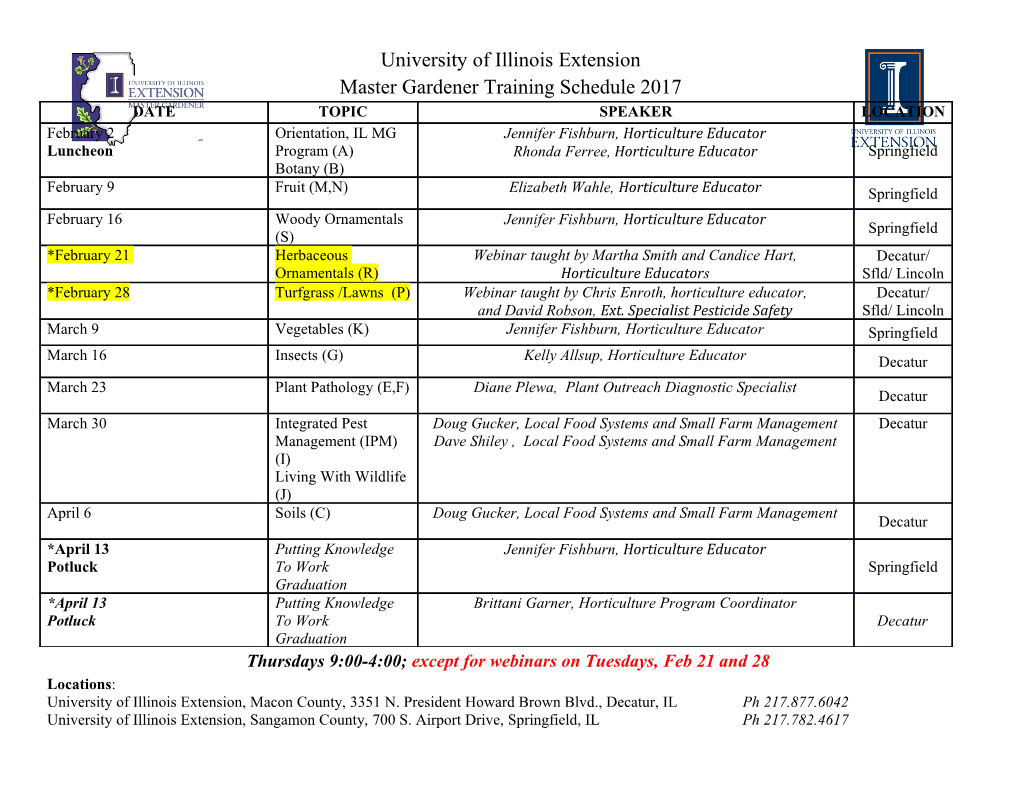
Investing in Quality: Identifying the True Value of Advanced Weld Inspection Technology By Michael T. Buelsing B.S. and B.A. Mechanical Engineering University of San Diego, 2010 Submitted to the MIT Sloan School of Management and the Department of Mechanical Engineering in partial fulfillment of the requirements for the degrees of Master of Business Administration, and Master of Science in Mechanical Engineering In conjunction with the Leaders for Global Operations program at the Massachusetts Institute of Technology June 2016 2016 Michael T. Buelsing, all rights reserved The author hereby grants to MIT permission to reproduce and to distribute publicly paper and electronic copies of this thesis document in whole or in part in any medium now known or hereafter created. Signature of Author: Signature redacted Mechanical Engineering, MIT Sloan School of Management May 06, 2016 Certified by: Signature redacted Roy Welsch, Thesis Supervisor Professor, MIT Sloan School of Management Certified by: ______ Signature redacted Thomas Ea 9, Thesis Supervisor Professor, Departmnt-pf Materials Scienceand Engineering Certified by: Signature redacted D vId Hardt, Thesis Reader Professor, Department of Mechanical Engineering Accepted by: ______Signature redacted Rohan Abeyaratne, Chairman, Committee on Gx~uate Students Department of Mechanical Engineering Accepted by: Signature redacted INSTITUTE MASSACHUSElTS kt6a er's'n, Iiirectb'orMITSloan~MBA Program MASSACHUSETTS INSTITUTE MIT Sloan School of Management OF TECHNOLOGY JUN 0 8 2016 LIBRARIES ARCHIVES This page is intentionally left blank. 2 Investing in Quality: Identifying the True Value of Advanced Weld Inspection Technology By Michael T. Buelsing Submitted to the MIT Sloan School of Management and the Department of Mechanical Engineering on May 06, 2016 in partial fulfillment of the requirements for the degrees of Master of Business Administration and Master of Science in Mechanical Engineering ABSTRACT The quality of Caterpillar's welds is becoming increasingly important as their equipment is made leaner with the goals of increased performance, lighter weight and lower unit cost. Due to the inherently variable nature of arc welding, non-destructive weld evaluation is critical to ensure that welding processes remain in control, and that defective parts are quarantined and repaired before being released downstream. The "conventional" ultrasonic weld inspection technology in use at present has several limitations: e Areas within common joint configurations cannot be adequately inspected due to geometry constraints e Discontinuity evaluation requires subjective real-time human interpretation by highly trained operators e The data produced by the instrumentation is unconducive to recording for off-line analysis e Imprecise defect sizing leads to Type I and Type II inspection errors - the unnecessary rework of good parts, and the inappropriate release of non-complying parts This project addressed these limitations of conventional ultrasonic weld inspection by identifying and evaluating alternative commercially available technologies and by initiating the internal development of specific proprietary technologies tailored to Caterpillar's needs. Through collaboration with Caterpillar's non-destructive evaluation (NDE) community, as well as outside vendors, a technology known as "phased array" was selected and validated in the laboratory and production environments. Although phased array was not new to Caterpillar, its adoption within the production facilities had previously been limited. Thesis Supervisor: Dr. Roy Welsch Title: Professor of Statistics and Engineering Systems, MIT Sloan School of Management Thesis Supervisor: Dr. Thomas Eagar Title: Professor of Materials Engineering and Engineering Management, Department of Materials Science and Engineering 3 This page is intentionally left blank 4 ACKNOWLEDGEMENTS This thesis would not have been possible without the financial, technical, and personal support of many. I'd first like to thank my supervisors and project stakeholders at Caterpillar: Greg Dubay, Don Stickel, Jean Bridge, Dong Fei, and Glenn Bergevin among others. In addition to your mentorship, you helped to make my time in Peoria both enjoyable and memorable. I'd also like to express particular gratitude to Denise Johnson, without whom this project would not have been possible. Next I'd like to thank my academic advisors: Thomas Eagar and Roy Welsch. Your guidance went beyond the research. The LGO internship program would cease to function without advisors such as yourselves who serve as the ambassadors of MIT. I'd like to thank the LGO faculty and staff, as well as my fellow classmates, for making the past two years exceptional. And finally, I'd like to thank my family and my girlfriend for motivating me and encouraging me to pursue the LGO program. 5 This page is intentionally left blank. 6 TABLE OF CONTENTS A bstract ........................................................................................................................................... 3 A cknow ledgem ents......................................................................................................................... 5 Table of Contents ............................................................................................................................ 7 Figures............................................................................................................................................. 8 T a b le s .............................................................................................................................................. 9 N otations ....................................................................................................................................... 11 1 Introduction................................................................................................................................ 13 1.1 Com pany Background ............................................................................................... 13 1.2 Project M otivation ..................................................................................................... 13 1.3 Thesis Overview ........................................................................................................... 14 2 W elding and Weld D efects ............................................................................................... 17 2.1 Introduction to W elding ............................................................................................. 17 2.2 Types and Causes of W eld Defects .......................................................................... 18 2.3 Fatigue: The N ature of W eld Failure ......................................................................... 19 2.4 Design for Fatigue.................................................................................................... 21 2.5 D efect Prevention.......................................................................................................... 26 2.6 W eld Inspection ............................................................................................................ 26 3 W eld Inspection Technology ............................................................................................. 29 3.1 Overview of N DT for W elding ..................................................................................... 29 3.2 Conventional U ltrasonic Testing ............................................................................... 31 3.3 Phased Array Ultrasonic Testing ............................................................................... 36 4 V alidation of Phased Array U ltrasonic Testing ................................................................ 41 4.1 Experim ent D esign.................................................................................................... 41 4.2 Experim ent Results ................................................................................................... 43 7 5 Business Case For Im plem entation................................................................................... 45 5.1 C ost of Q uality Fram ew ork ...................................................................................... 45 5.2 Stakeholder Input ...................................................................................................... 48 5.3 Enterprise C O Q A nalysis......................................................................................... 52 6 C onclusion and N ext Steps ............................................................................................... 55 7 O pportunities for Future Projects....................................................................................... 57 7.1 Next Generation Weld Inspection System................................................................ 57 7.2 Opportunities Beyond Inspection Technology ......................................................... 57 A p p end ix ....................................................................................................................................... 59 Exhibit 1: Phased Array Study Data.................................................................................... 59 Exhibit 2: ANOVA Analysis of the Effect of Welding Parameters ..................................... 60 R eferen ces ....................................................................................................................................
Details
-
File Typepdf
-
Upload Time-
-
Content LanguagesEnglish
-
Upload UserAnonymous/Not logged-in
-
File Pages61 Page
-
File Size-