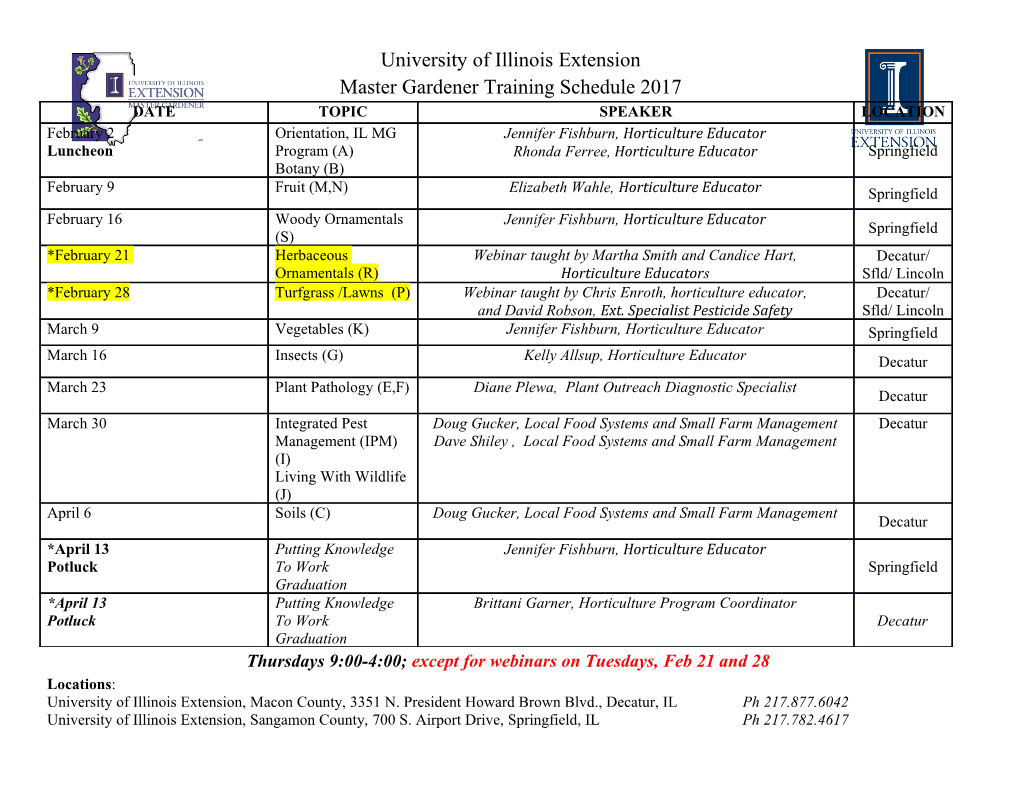
Table of Contents Variables and Acronyms 4 Section I: Executive Summary 5 1.1 Solution Design Summary…………………………………………………………………. Section II: Management Summary 6 2.1 Team Organization and Management……………………………………………… Figure 1: Management Chart…………………………………………… Figure 2: Time Schedule……………………………………………… Section III: Conceptual Design 7 3.1 Mission Statement and Design Requirements……………… Figure 3: Competition Flight Path……………………………... 3.2 Considered Concepts and Designs………………………….. Figure 4: Wing Sweep Design…………………………………. Figure 5: Wing Slide Design…………………………………… Figure 6: Wing Fold Mechanism Design……………………….. Table 1: Concept Scoring…………………………………… Figure 7: Gate Latch Drop Mechanism……………………. Figure 8: Moving Arms Drop Mechanism……………………………. Figure 9: Rubber band pylon drop mechanism…………………. Figure 10: Servo-actuated dual-pin drop mechanism……………... Table 2: Pros and Cons of Drop Mechanisms…………………….. Section IV: Preliminary Design 19 4.1 Methodology……………………………………………………… Figure 11: Design Methodology Flow……………………... 4.2 Design/Sizing…………………………………………………….. Figure 12: Coefficients of Lift and Drag Graphs (NACA 4412)......... Table 4: Preliminary Aircraft Sizing…………………. Figure 13: Equations for Determining Generated Thrust…. 4.3 Mission Model………………………………………………………………. Table 5: Power Performance Estimates……… Figure 14: SolidWorks CFD Analysis Method………………… Figure 15: Critical Angle of Attack………. Table 7: Lift Based on AOA and Flap Setting……... 1 Figure 16: Lift vs AOA at Various Flap Settings……. Table 8: Drag Based on AOA and Flap Setting…….. Figure 17: Drag Based on AOA and Flap Setting…………………... 4.4 Performance Estimations………………………………………. Figure 18: Flight Simulator Testing……………………. Section V: Detail Design 30 5.1 Design Structure and Parameters…………………………………………………….. Table 9 Final Parameters………………………………………………….. 5.2 Structural Capabilities…………………. Figure 19: FEM analysis of the landing gear using MATLAB……………. Figure 20: Main Landing Gear………………. Figure 21: Shear Moment Diagram for Wing……………………. Figure 22: Tail and Control Servos………………. 5.3 Systems and Subsystems……………………………………………………………………… Figure 23: Models for the Wing Fold Mechanism……………… Figure 24: Drop Mechanism……….. Figure 25: Radome and Control Servo………………. Table 10: Store Weight Balance………………………………………………………………… 5.4 Flight and Mission Performance………………………………………………………………. Drawing Package…………………………………………………………………………….. Section VI: Manufacturing Plan 38 6.1 Review of Processes………………………………………………………………………….. Figure 26: Hot wire cutting a wing…………... 6.2 Selected Process…………………………………………………………………………….. Table 11: Manufacturing Flow Timeline……………………………………………… Figure 27: Team construction meeting, assembling radome and drop mechanisms... Section VII: Testing Plan 44 Table 12: Component Testing Plan……………………….. 7.1 Test Objectives…………………………………………………….. 7.2 Flight Test Schedule and Flight Plan…………………. 7.3 Test and Flight Checklists………… Table 13: Flight test schedule…………………………... Figure 28: Flight test log………………. 2 Section VIII: Performance Results 47 8.1 Performance of Subsystems…………………………………….. Table 14: Battery endurance…………………. 8.2 Performance of Final Aircraft……………………………………. Section IX: Bibliography 49 3 Abbreviations, Acronyms, Symbols, and Variables Acronym Description AIAA American Institute of Aeronautics and Astronautics AOA Angle of Attack CAD Computer Aided Design CFD Computational Fluid Dynamics DBF Design Build Fly FEM Finite Element Method NACA National Advisory Committee for Aeronautics PLA Polylactic Acid RC Remote Control RFP Request for Proposal RPM Revolutions per Minute UW University of Washington AR Aspect Ratio b Wingspan [m] c Chord [m] Cd Coefficient of Drag CG Center of Gravity [m] Cl Coefficient of Lift d Diameter [m] D Drag [N] F Force [N] g 9.81 m/s^2 L Lift [N] P Power [W] Pr Power Required [W] S Surface Area [m^2] Slo Rolling Takeoff Distance [m] T Thrust [N] t Time [s] Tr Thrust Required [W] Vh Horizontal Tail Coefficient Vv Vertical Tail Coefficient w Weight [N] rho Density [kg/m^3] 4 1. Executive Summary 1.1 Solution Design Summary For the academic year 2018-2019, the Design Build Fly team at the University of Washington designed, built, and tested a remote-controlled aircraft named Squawk 7700. This aircraft must be capable of supporting aircraft carrier operations. It must also have folding surfaces that allow for a stowed configuration. Physically, the aircraft must have a minimum wingspan of four feet, and be able to take off from a 4x10 ft. ramp angled at five degrees from horizontal. In its stowed state, the aircraft must also be able to roll through a 3x2 ft. box without interference. The nose and landing gear must fit within the box depth of 2 ft. Finally, the aircraft must be able to transition from folded to flight configuration remotely, as well as mechanically locking itself. At the time of competition, the plane must also complete the three flight missions and a single ground mission. First, the aircraft must complete a flight with no payload onboard. Following that, the aircraft must be able to fly the course with the radome attached to successfully complete the Reconnaissance mission. The third mission involves the attack stores, where a minimum of four must be mounted onto the plane, with one dropped independently on the downwind leg of each flight. Lastly, members of the ground crew must be able to quickly equip and detach the stores and radome elements from the aircraft during the ground mission. 1.2 Design Solution Summary After analyzing all mission and physical requirements, it was determined that drag resulting from the stores and radome would be the most significant challenge this year. The other significant challenge was to achieve enough lift rapidly in order to takeoff in such a short distance. Therefore, it was decided that maximizing lift and reducing empty weight were the most critical components for the design. A monoplane configuration that utilizes an extended chord wing and large flaps was identified as the best solution to maximize lift while keeping system complexity to a minimum. The aircraft must be capable of flying around 20 mph to meet the five minute time window for each mission, therefore, weight minimization was emphasized as a critical design requirement. The aircraft body was constructed primarily from polystyrene due to its light weight and excellent durability, with a carbon fiber spar running through the wing to maintain rigidity, and a carbon fiber longeron running through the fuselage. At the rear of the aircraft, the horizontal and vertical stabilizers mount directly to the carbon fiber spar in a conventional tail arrangement. Mechanisms for a wing folding design, radome, and dropping the attack stores posed unique challenges. These components had to be able to perform their required functions while adding minimal 5 weight and drag to the design. It was determined that the drop mechanism, wing folding mechanism, and radome would be constructed almost entirely out of polystyrene or 3D printer filament in order to minimize their weight and allow for replacement components to be easily and cheaply created. In addition, it needed to be ensured that the radome and attack stores were easily attachable and removable. Therefore, simplifying their design as much as possible became a necessity. The monoplane configuration proved to be ideal for fold-down mechanisms that were effective at reducing the wingspan of the plane for its stowed configuration. A hinging and mechanically locking mechanism was designed that allowed for the wings to fold directly downward on both sides, which allowed the plane to be reduced to the required sizing for stowing. This mechanism was designed to be 3D-printed, and entirely contained within the wing in order to have minimal impact on aircraft drag. 2. Management Summary 2.1 Team Structure The 2018-2019 UW DBF team consists of approximately 30 students who participate as an extracurricular activity. The roster consists of 2 seniors, 5 juniors, and 23 sophomores or freshmen. The team is filed under the UW as a student-led club, augmented by guidance from the faculty advisor, Dr. Chris Lum. Furthermore, individuals who are employed in the aviation industry offered suggestions. The leadership structure of UW DBF is outlined in the management chart in Figure 1. All members of the leadership team take on a specific administrative role alongside their primary engineering role. Figure 1: Management Chart 6 Figure 2: Program Schedule Figure 2 outlines the methods of tracking project progress. Major milestones are marked by vertical lines, and the fly-off dates are marked by the dashed line. The design process began with a detailed analysis of the RFP and an examination of competition scoring. Initial design research maximized the score, while keeping production complexity and cost as low as possible. Once a preliminary design concept was selected, work began on sizing, airfoil selection, and motor selection. During the initial design phase, design refinement through simulation, as well as rapid prototyping were the primary areas of focus to identify and resolve any major issues before flight. Upon selection of the motor, propeller, airfoil, and general design, the aircraft was constructed. After additional testing and submission of this report, the aircraft will be optimized for competition by reducing weight and improving component quality. 3. Conceptual Design 3.1 Mission Requirements There are three flight missions and one ground mission that must be completed at competition. The following
Details
-
File Typepdf
-
Upload Time-
-
Content LanguagesEnglish
-
Upload UserAnonymous/Not logged-in
-
File Pages55 Page
-
File Size-