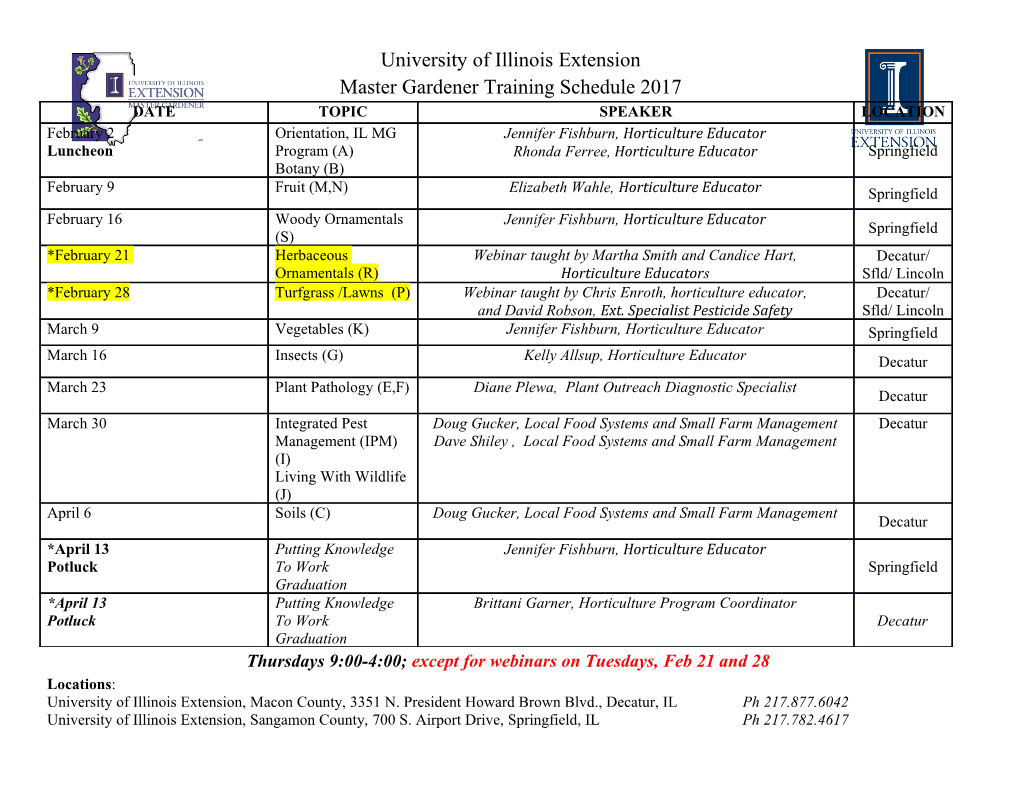
Chapter 29 Smart Polymer Nanoparticles for High-­ Performance Water-Based Coatings José Paulo S. Farinha, Susana Piçarra, Carlos Baleizão, and J.M.G. Martinho Abstract The increasing pressure to reduce the use of volatile organic compounds (VOCs) within the coatings industry has led to the development of waterborne sys- tems. Water-dispersed polymer nanoparticles (i.e., latex) have been successfully used to this end, but the resulting films usually present less strength, hardness, and resistance to chemicals than solvent-borne coatings. A method to enhance the prop- erties of these films is through chemical polymer chain cross-linking when the film is formed. This approach requires a careful balance of the cross-linking reaction rate and the polymer diffusion rate across the initial nanoparticle boundaries, and it has been extensively studied and used in industrial coatings. Herein, waterborne coat- ings based on reactive polymer nanoparticles and the first attempts to use “smart” polymer nanoparticles where the cross-linking is triggered by a stimulus which occurs after the desired extent of interdiffusion are reviewed. Different types of cross-linking that have the potential to be used in smart waterborne coatings, involv- ing functional groups such as alkoxysilanes, carboxylic acids, carbodiimide, aziri- dine, isocyanates, and polyols, where the trigger can be a change in pH, temperature, or water content, are also discussed. Keywords Waterborne coatings • Reactive latex • Smart nanoparticles • Polymer dispersions J.P.S. Farinha (*) • C. Baleizão • J.M.G. Martinho Centro de Química-Física Molecular, IN-Institute of Nanoscience and Nanotechnology, Instituto Superior Técnico, University of Lisbon, 1049-001 Lisboa, Portugal e-mail: [email protected] S. Piçarra Escola Superior de Tecnologia de Setúbal, Instituto Politécnico de Setúbal, 2910-761 Setúbal, Portugal © Springer International Publishing Switzerland 2016 619 M. Hosseini, A.S.H. Makhlouf (eds.), Industrial Applications for Intelligent Polymers and Coatings, DOI 10.1007/978-3-319-26893-4_29 620 J.P.S. Farinha et al. 29.1 Introduction Driven by environmental concerns, the coatings industry has moved from solvent-­ borne coatings toward waterborne coatings, in order to reduce volatile organic com- pound (VOC) releases, as forced by environmental concerns. Coatings based on aqueous dispersions of polymer nanoparticles (latex coatings) were found to be a good alternative to solvent-borne coatings, although generally with inferior performance essentially due to subpar properties such as strength, hardness, and solvent resisting capabilities. Nevertheless, polymer films with good properties can be obtained from latex dispersions containing large polymer chains, when the length over which the chains diffuse is comparable to their radius of gyration, resulting in interfacial healing between adjacent polymeric nanoparticles [1, 2]. However, the diffusion of large poly- mer chains is slow, requiring the use of VOCs to achieve reasonable film formation times. Alternatively, interparticle healing can be achieved by incorporating reactive groups in the nanoparticles, so that upon contact between the nanoparticles, the reac- tive groups form cross-links across adjacent particles. This approach has been used to improve the performance of zero VOC coatings in thermoset latex coatings. The different stages involved in the formation of a polymer film from a water disper- sion of polymer nanoparticles (latex) are depicted in Fig. 29.1 [3, 4]. After water evapo- ration, film drying leads to a densely close-packed arrangement of the polymer particles (stage I). This is followed by particle deformation via capillary, osmotic, and surface forces, which occurs if the film is above the “minimum film formation temperature” Fig. 29.1 Film formation from a water dispersion of polymer nanoparticles 29 Smart Polymer Nanoparticles for High-Performance Water-Based Coatings 621 (near the polymer’s glass transition temperature, Tg, in the presence of water), to yield a nascent film constituted by space-filling polyhedral in close contact (stage II). These transparent void-free films still have weak interfaces between the particles, which are strengthened by polymer chain diffusion among adjacent particles. Diffusion occurs at temperatures above the Tg of the polymer, until complete healing of the interface by interdiffusion of the polymer chains and formation of entanglements across the inter- faces between particles, to form a mechanically rigid film (stage III). The degree of entanglements formed between particles determines how strong the interface is. Thermoplastic latex films without chemical cross-links usually show poor perfor- mance since the interfaces generated during healing are relatively sharp due to the slow diffusion of polymer chains with molecular weight above the entanglement molecular weight. This has driven many efforts to develop high-performance ther- moset latex films by cross-linking the polymer chains during the healing of the interfaces. This process must be fully controlled since cross-linking retards and even stops polymer diffusion. Thus, a fine balance between polymer interdiffusion and the rate of cross-linking is required to optimize the film’s mechanical properties [5]. In addition, the cross-linking reaction must not occur during storage of the dispersion, should not produce VOCs, and the final film must have a performance com- parable to that of organic solvent-based coatings. 29.1.1 Theory of Polymer Diffusion and Cross-Linking The mechanical strength and toughness of a latex film (its ability to store and dis- sipate energy during deformation) is strongly influenced by the formation of entan- glements across the interface during healing. However, it was shown that these properties can be further improved if the chains are anchored at opposite sides of the initial interface by cross-links created during polymer interdiffusion [6]. A theoretical model for diffusion and cross-linking within polymer films was developed by de Gennes [7, 8] to explain the coupling between diffusion and reac- tion, as well as the influence of long-chain branches and cross-linking on the prop- erties of thermoset latex films. The model defines three main regimes [7]. In the first regime, the cross-linking reactions are much slower than polymer interdiffusion, leading to complete interfacial healing prior to significant gel development, with the properties of the resulting film being similar to those of the bulk material. The second regime is defined by comparable rates of reaction and interdiffusion, yield- ing a nonequilibrium interface in which a considerable amount of cross-links are developed during polymer diffusion and the mean chain length between cross-links spans the interface. The third and final regime corresponds to the case where the reaction outpaces diffusion, so that the polymer chains are trapped inside their original particles and there is no interface healing. In this last case, adhesion is entirely caused by the dangling polymer chain ends that diffuse upon completion of the reaction, a situation akin to that of films created from pre-cross-linked latex nanoparticles that show very poor mechanical properties [7]. 622 J.P.S. Farinha et al. The model considers a linear monodispersed statistical copolymer composed of two blocks, A and A*, with a total number of monomers, N, higher than the critical number of monomers for entanglements, Ne. Each polymer chain contains one of its A* sites functionalized with a small group X that can react upon encountering any of the A* sites of another polymer chain to form a cross-link, with each chain form- ing a single cross-link (considered enough to stop the diffusion and immobilize the involved chains). A nondimensional parameter α is defined as the ratio of two char- acteristic times: the diffusion time, Tdiff, and the reaction time, Treac: T a = diff (29.1) Treac The diffusion time, Tdiff, is considered in the context of the de Gennes theory of reputation [9, 10] as the time needed for a chain to diffuse out of its original confin- ing tube: N 3 TTdiff ==rep t 0 (29.2) Ne where τ0 is the relaxation time of one monomer. The reaction time, Treac, is defined as the time for one cross-link to form in each chain and can be expressed in terms of the rate constant of the cross-linking reac- tion, k, the number of monomers between cross-links, Nc, and the number of A* * sites not bearing the functional group, A0 : Nc 1 Treac @ * (29.3) N kA0 When the cross-linking density is low, NNc @ , and α is given by a = kA*T (29.4) 0 rep This means that α is the number of cross-links that a given chain forms in each dis- placement from the confining tube. This is a virtual number because the model assumes that each chain can only make a single cross-linking. The parameter a can also be understood as the number of cross-links that a given chain would form, if it were able to react an infinite number of times. Values of a 1 define the fast-reaction regime in which reaction is much faster than interdiffusion, and hence all chains are fixed by cross-links before diffusing across the interface. In this case, no cross-links bridge the interface, and adhesion is due entirely to pullout of the dangling chain ends that cross the interface. A cross- over occurs at a = 1, from the fast to the slow regime. In the slow regime (a 1), the cross-linking reaction is much slower than interdiffusion, and consequently the interface heals before significant cross-links are formed, thus becoming similar to the bulk network. 29 Smart Polymer Nanoparticles for High-Performance Water-Based Coatings 623 The adhesion energy of a polymer film depends mainly on the polymer chain length, all other parameters being fixed. For short chains (fast diffusion), the system is in the slow-reaction regime (a 1), and the adhesion energy is independent of chain length, presenting its highest value.
Details
-
File Typepdf
-
Upload Time-
-
Content LanguagesEnglish
-
Upload UserAnonymous/Not logged-in
-
File Pages27 Page
-
File Size-