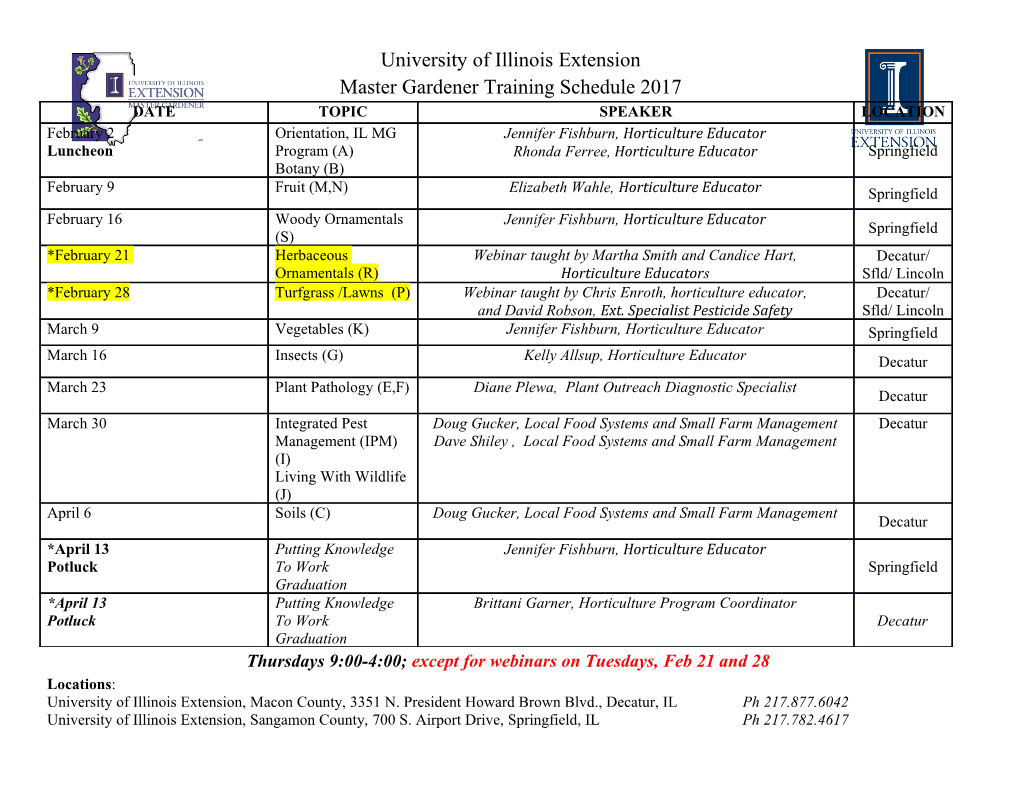
Aspects of aero-engine nacelle drag Matthew Robinson1, David G. MacManus2 Cranfield University, Bedfordshire, United Kingdom, MK43 0AL Christopher Sheaf3 Rolls-Royce plc, P.O Box 31 Derby, United Kingdom, DE24 8BJ Abstract To address the need for accurate nacelle drag estimation, an assessment has been made of different nacelle configurations used for drag evaluation. These include a sting mounted nacelle, a nacelle in free flow with an idealised, freestream pressure matched, efflux and a nacelle with a full exhaust system and representative nozzle pressure ratio. An aerodynamic analysis using numerical methods has been carried out on four nacelles to assess a near field drag extraction method using computational fluid dynamics. The nacelles were modelled at a range of aerodynamic conditions and three were compared against wind tunnel data. A comparison is made between the drag extraction methods used in the wind tunnel analysis and the chosen computational fluid dynamics approach which utilised the modified near field method for evaluation of drag coefficients and trends with Mach number and mass flow. The effect of sting mounting is quantified and its influence on the drag measured by the wind tunnel methodology determined. This highlights notably differences in the rate of change of drag with free stream Mach number, and also the flow over the nacelle. A post exit stream tube was also found to create a large additional interference term acting on the nacelle. This term typically accounts for 50% of the modified nacelle drag and its inclusion increased the drag rise Mach number by around = 0.026 from = 0.849 to = 0.875 for the examples considered. ∆ 1 Corresponding Author: Matthew Robinson, PhD Student Researcher, Centre for Propulsion, Cranfield University, Email: [email protected] 2 Head of Gas Turbine Technology Group, Propulsion Engineering Centre, Cranfield University 3 Installation Aerodynamics specialist 1 Nomenclature Abbreviations AGARD Advisory Group for Aerospace Research and Development ARA Aircraft Research Association BPR By Pass Ratio CFD Computational Fluid Dynamics CFL Courant-Friedrich-Lewy DPW Drag Prediction Workshop ELFIN European Laminar Flow Investigation GCI Grid convergence index ISA International standard atmosphere LARA Laminar flow Research Action MFCR Mass flow capture ratio MS/FS Model scale/Full scale N Nacelle configuration NE Nacelle/exhaust configuration NS Nacelle/sting configuration NACA National Advisory Council for Aeronautics NASA National Aeronautics and Space Administration NLF Natural Laminar Flow PM/RE Pressure matched/Realistic efflux boundary conditions RANS Reynolds-averaged Navier-Stokes RMS Root mean squared SST Shear stress transport UHBPR Ultra-High By-pass ratio Symbols A Area [m2] cD Nacelle drag coefficient [-] cf Skin friction coefficient [-] cp Pressure coefficient [-] d Diameter [m] D Nacelle drag force [N] F Force [N] k Turbulent kinetic energy [Jkg-1] L Length [m] Mass flow rate [kg s-1] M Mach number [-] ̇ n Unit normal [-] P Total pressure [Pa] r Radius [m] Re Reynolds number [-] 2 Rex Reynolds number per unit length [m-1] V Velocity [ms-1] [x, y, z] Cartesian coordinates [-] α Incidence [°] β Boat tail angle [°] ρ Density [kgm-3] τ Shear stress [Pa] Force [N] ω Specific rate of dissipation [s-1] Subscripts a Afterbody c Centrebody combined Nacelle and sting combined CL Centre line DR Drag rise e Exit f Forebody i Highlight if Initial forebody interf Interference m Maximum nac Nacelle pre Pre-entry sting Sting section upstream of measurement plane t Total wc Wetted cowl ws Wetted sting upstream of measurement plane 0 Upstream infinity station ∞ Freestream * Modified 3 I. Introduction There is an ongoing need to improve aircraft performance to reduce fuel burn, emissions and operating costs [1, 2]. Improvement in engine technologies is needed to provide a significant part of the fuel burn reduction [2]. In recent decades, the on-going development of the aero-engine has followed a trend of increasing the bypass ratio (BPR) of a turbofan engine in order to improve its propulsive efficiency [3]. As the bypass ratio has increased, the fan diameter has grown substantially; whilst the core size has reduced relatively. Although the increase in fan diameter provides benefits to the uninstalled engine cycle, there are adverse effects due to nacelle drag, weight and installation difficulties that offset some of the cycle benefits. Therefore, as this trend for increasing fan diameter continues, it is important to reduce the drag penalty from a larger engine to allow improvements in overall aircraft fuel burn. A notable contributor to the drag of a modern aero-engine comes from the nacelle [4] [5]. The nacelle is optimised to balance the requirement to contribute as little drag as possible to the overall installation; while providing the quantity and quality of flow required by the engine and incorporating an exhaust system which satisfies cycle compatibility, efficiency, and noise suppression requirements over the full aircraft flight envelope [6]. As jet engines have increased in size, the nacelle design has become more critical. A previous study reported an overall engine installation contribution of around 14% of the drag for a civil twin-engine airliner [4], and an increase in diameter will cause greater nacelle drag and interference with the wing [5]. Significant work has been carried out to try to understand and mitigate the impact of large engines on the overall performance of aircraft. A study into the overall system performance of high BPR engine designs up to a BPR of 21.5 looked at improving three baseline engines and found that increases in fan diameter from 2.85m to 3.25m, with a BPR increase from 6.2 to 14.3, could provide improvements in overall fuel burn of 15-16% for an engine with a thrust class in the range of 350-390 kN [7]. However this study did not look at the detailed aerodynamic design of the nacelles or the interaction with the wing. Another assessment of ‘advanced’ engine and nacelle concepts looked to apply slimmer and shorter nacelles to engines in the thrust class range of 107-267kN. These engines incorporated novel nacelles for engines with geared cycles and demonstrated that with an optimal nacelle design, savings of 3% in fuel burn were possible from the advanced nacelle design for a large twin engine aircraft [8]. The Common Research Model (CRM) is an aircraft configuration comprising wing/body/nacelle/pylon/horizontal-tail [9]. It was developed as a model for wind tunnel and Computational Fluid Dynamics (CFD) analysis to be used to predict drag characteristics of modern wide body civil aircraft [9]. Principal experimental data for the CRM comes from the NASA Ames 11-ft wind tunnel and the NASA Langley National Transonic Facility [10]. The impact of the through-flow nacelle and pylon were seen to cause an increase in drag of around 20 drag counts, approximately 10% of overall aircraft drag, at the cruise Mach number of 0.85 and lift coefficient of 0.5. As engines increase in size, these influences on drag are expected to become more important and nacelle design will become of increasing importance. Consequently, there is a need to establish the required experimental and computational tools to enable the reliable evaluation of the nacelle performance. This includes aspects such as drag, critical drag-rise Mach number as well as spillage drag. Nacelle design A conventionally designed supercritical nacelle is characterised by a curvature driven acceleration over the forebody followed by constant deceleration [11]. For nacelles designed in this way, the peak Mach number reached in the initial acceleration is minimised. A nacelle in a transonic airflow will experience local regions of supersonic flow which typically 4 terminate in shock waves and contribute to the nacelle drag. As the freestream Mach number is increased, the peak local Mach number on the nacelle increases, which results in stronger shocks and the associated wave drag penalties. Although the design point condition is of vital importance, the off-design aspects are also crucial such as the nacelle performance at higher than cruise Mach numbers. The Mach number at which a rapid increase in drag with freestream Mach number arises is termed the drag rise Mach number and is often defined based on a drag gradient criterion as a function of the freestream Mach number. Though criteria for nacelles are not found in the published literature, several cases for full aircraft drag rise are available. For example, Roskam [12] defines the drag rise Mach number (MDR) based on a drag gradient (equation 1). The level of the criterion varies and Shevell [13] reports a value of 0.05 based on the same gradient. Roskam also discusses an alternative to the gradient based criteria as an increase of 0.002 in cD above the incompressible level. MDR is a key parameter for the assessment of nacelle configurations as a designer will tend to avoid being within 0.02 of the drag rise during cruise [14]. = 0.1 (1) The streamtube (Figure 1) which enters an aero-engine varies with the aerodynamic conditions and the engine mass flow requirement. Mass flow capture ratio (MFCR) is the ratio of the cross sectional area of this streamtube at upstream infinity divided by the highlight plane area (equation 2). An engine intake is sized for the maximum required mass flow for take- off and climb, so usually operates at a MFCR<1 during the cruise. = (2) Spillage drag has been defined as drag incurred when the value of MFCR falls below 1 if the force which acts on the pre entry streamtube is not balanced by the forebody suction [15]. This is a particular challenge at low engine power settings. The forebody of a nacelle is required to maintain sufficient suction to compensate for the change in momentum of the streamtube between the freestream and the highlight plane.
Details
-
File Typepdf
-
Upload Time-
-
Content LanguagesEnglish
-
Upload UserAnonymous/Not logged-in
-
File Pages24 Page
-
File Size-