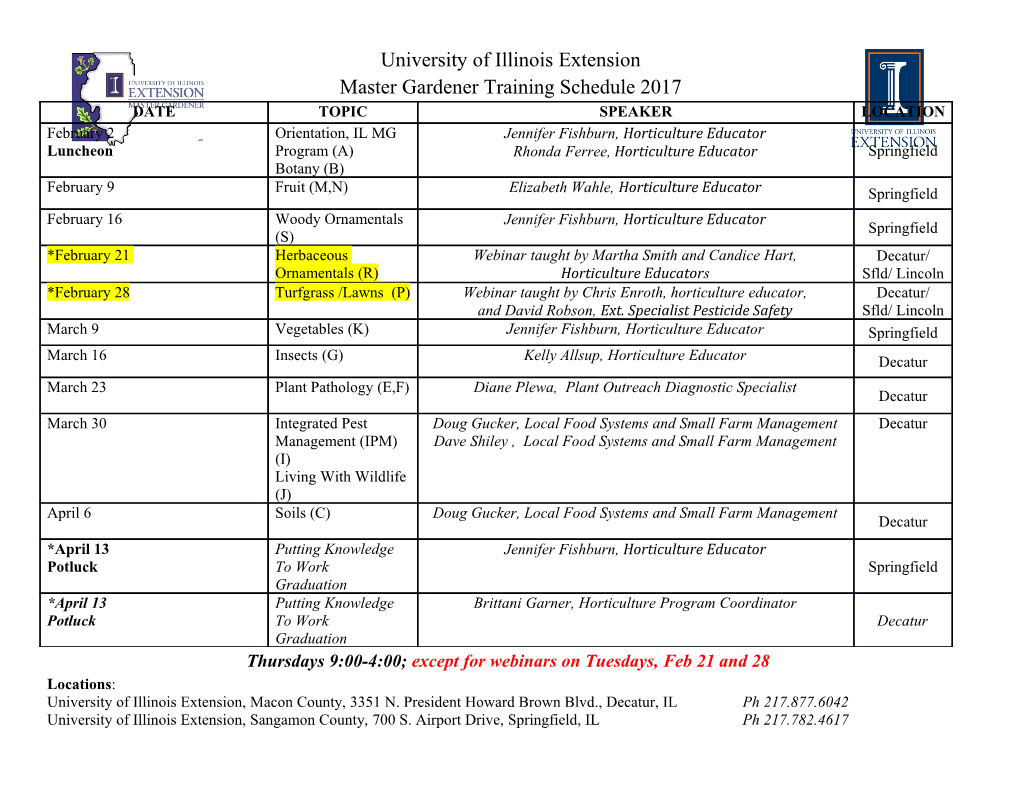
International Materials Reviews ISSN: 0950-6608 (Print) 1743-2804 (Online) Journal homepage: http://www.tandfonline.com/loi/yimr20 Plant fibre-reinforced polymers: where do we stand in terms of tensile properties? Marta Fortea-Verdejo, Elias Bumbaris, Christoph Burgstaller, Alexander Bismarck & Koon-Yang Lee To cite this article: Marta Fortea-Verdejo, Elias Bumbaris, Christoph Burgstaller, Alexander Bismarck & Koon-Yang Lee (2017) Plant fibre-reinforced polymers: where do we stand in terms of tensile properties?, International Materials Reviews, 62:8, 441-464, DOI: 10.1080/09506608.2016.1271089 To link to this article: http://dx.doi.org/10.1080/09506608.2016.1271089 © 2017 The Author(s). Published by Informa UK Limited, trading as Taylor & Francis Group Published online: 20 Jan 2017. Submit your article to this journal Article views: 720 View related articles View Crossmark data Full Terms & Conditions of access and use can be found at http://www.tandfonline.com/action/journalInformation?journalCode=yimr20 Download by: [Imperial College London Library] Date: 14 September 2017, At: 07:38 INTERNATIONAL MATERIALS REVIEWS, 2017 VOL. 62, NO. 8, 441–464 https://doi.org/10.1080/09506608.2016.1271089 FULL CRITICAL REVIEW Plant fibre-reinforced polymers: where do we stand in terms of tensile properties? Marta Fortea-Verdejoa, Elias Bumbarisa, Christoph Burgstallerb, Alexander Bismarck a,c and Koon-Yang Lee d aPolymer and Composite Engineering (PaCE) Group, Faculty of Chemistry, Institute for Materials Chemistry and Research, University of Vienna, Vienna, Austria; bTransfercenter für Kunststofftechnik GmbH, Wels, Austria; cPolymer and Composite Engineering (PaCE) Group, Department of Chemical Engineering, Imperial College London, London, UK; dThe Composites Centre, Department of Aeronautics, Imperial College London, London, UK ABSTRACT ARTICLE HISTORY This article reviews the tensile properties of various plant fibre-reinforced polymers reported in Received 12 March 2015 literature. We critically discuss the use of plant fibres as reinforcement for the production of bio- Accepted 5 December 2016 based, renewable or green polymer composites. The tensile properties of these composites are KEYWORDS compared against various (non-)renewable engineering/commodity polymers and Natural fibres; composites; commercially available randomly oriented glass fibre-reinforced polymers (GFRP). Composites cellulose; short fibre containing random short plant fibres possess similar properties to randomly oriented GFRP at composites; biocomposites; a lower overall part weight. Unidirectional plant fibre-reinforced polymers offer better polymer matrix composites performance than randomly oriented GFRP and have the potential to be adapted in applications requiring better mechanical performance, especially in applications where the use of costly synthetic fibres might be less attractive. Plant fibres can also be regarded as fillers to replace the more expensive polymers and improve the green credentials of the final composite parts. These features may motivate the industry to move towards plant fibre- based products. Introduction applications in the textile [13] and food packaging The ever-growing problem associated with global industries [14]. Nevertheless, its engineering appli- waste, the public’s growing awareness on sustainability, cations are still lacking due to its low heat distortion environmental legislative pressures such as the EU temperature (∼60°C) and limited melt strength [15]. end-of-life vehicle [1], landfill of waste products [2] Poly(hydroxyl butyrate) (PHB) is another bio-derived and waste electrical and electronic equipment direc- polyester that is synthesised by microorganisms, such tives [3], as well as the growing demand for more as Ralstonia eutropha [16]. The high production cost environmental friendly products have reinvigorated associated with the synthesis of PHB and its brittle the interest in bio-based materials in the consumer nature [17] limits its applications in everyday use. industry [4,5]. Polymer manufacturers are required to To ensure a sustainable future, we need to produce consider the lifecycle of their materials and evaluate bio-derived materials that can compete with or poten- the environmental impact of their products starting tially replace the ‘big four’ polymers – polypropylene from sourcing of raw materials over processing to dis- (PP), polystyrene (PS), polyethylene (PE) and polyvinyl Downloaded by [Imperial College London Library] at 07:38 14 September 2017 posal of the final product. As a result, numerous chloride (PVC) [18]. However, the performance of bio- research efforts have been poured into the synthesis, derived polymers still trails traditional petroleum-based manufacturing and production of bio-derived poly- engineering polymers. To address this challenge, a com- mers [6–9]. While there are some commercial suc- posite strategy, i.e. combining bio-derived polymers cesses in bio-derived polymers, their applications in with bio-based reinforcements could be used to bridge our everyday life still remain somewhat limited. Take this property-performance gap. In this context, plant poly(lactic acid) (PLA) for example, a commercially fibres are seen as an ideal reinforcement for bio-based available and fully bio-derived and biodegradable poly- polymer matrices due to their renewability and wide mer with tensile moduli and strengths in the range of availability [19]. In fact, plant fibre-reinforced polymer ∼4 GPa and ∼70 MPa, respectively [10,11]. PLA can composites are already widely used in the automotive be regarded as one of the best performing bio-derived industry. More than 98% of plant fibre-reinforced poly- polymers [12] and has already found commercial mer composites produced in the European Union in the CONTACT Koon-Yang Lee [email protected] The Composites Centre, Department of Aeronautics, Imperial College London, South Kensington Campus, SW7 2AZ, London, UK © 2017 The Author(s). Published by Informa UK Limited, trading as Taylor & Francis Group This is an Open Access article distributed under the terms of the Creative Commons Attribution License (http://creativecommons.org/licenses/by/4.0/), which permits unrestricted use, distribution, and reproduction in any medium, provided the original work is properly cited. 442 M. FORTEA-VERDEJO ET AL. year 2012 were used in the automotive industry [20]. Table 2. Estimated cost of various plant fibres in its loose form Daimler AG replaced the door panels of the Mercedes- and E-glass fibres. −1 a Benz E-class with flax and sisal fibre mat-reinforced Fibres Price (US$ kg ) epoxy resin [21]. A weight reduction of 20% and an Sisal 0.5–2.8 Hemp 0.5–5 improvement in the mechanical performance of the Kenaf 0.4–0.6 door panels were achieved. In 2005, Rieter Automo- Jute 0.3–0.9 Coir 0.3–0.4 tive won the JEC Composites Award for their plant E-glass fibre tow 0.9–1.5 fibre-reinforced thermoplastic under-floor module aThe price was estimated from wholesalers listed online (http://www. with integrated thermal, aerodynamic and acoustic alibaba.com). functions [22]. Jute fibre-reinforced polyesters are used as construction materials in India but the mar- The mechanical properties of plant fibre-reinforced ket size is relatively small [23]. Table 1 summarises polymer composites reported in the literature were col- the applications of plant fibre-reinforced polymer lated, juxtaposed and compared to the mechanical per- composites in the automotive industry [24]. It is formance of commercially available commodity and also worth mentioning at this point that the total engineering polymers, as well as commercially avail- usage of plant fibre-reinforced polymers exceeds able glass fibre-reinforced polymer composites that of wood fibre-reinforced polymers (90 000 versus (GFRP). 60 000 t in the European Union 2012) [20]inthe automotive industry as plant fibre-reinforced poly- Plant fibres – a brief introduction mers are stiffer compared to wood fibre-reinforced counterparts. Plant fibres are a subset of natural fibres, which also The use of plant fibres not only can address the includes animal fibres (wool, feathers and silk) and min- aforementioned property-performance gap between eral fibres (asbestos and basalt). Animal and mineral bio-derived and petroleum-derived polymers but also fibres have also been explored as reinforcement for com- serve as alternative to existing synthetic fibres, such posite materials [30–33]. Silk fibres, for example, were as glass fibres [25,26], as some plant fibres are available shown to be effective reinforcements for epoxy resins. at potentially lower cost but possess a tensile stiffness Plain woven silk fibre-reinforced epoxy composites similar to glass fibres (Table 2)[27,28]. As a result, were found to possess tensile stiffness and strength of the research into plant fibre-reinforced polymers up to 6.5 ± 0.1 GPa and 111 ± 2 MPa, respectively started to re-emerge in the field of composite science [34]. The tensile performance of these silk fibre-rein- and engineering over the last 25 years (see Figure 1) forced epoxy are comparable to flax fibre-reinforced [29]. Over this period, numerous researchers have epoxy composites. The impact strength of silk fibre- been studying the use of plant fibres to produce fully reinforced epoxy, however, exceeds those of flax fibre- or partially bio-based composites, also known as reinforced epoxy composites, indicating the suitability green or renewable composites. This article reviews of
Details
-
File Typepdf
-
Upload Time-
-
Content LanguagesEnglish
-
Upload UserAnonymous/Not logged-in
-
File Pages25 Page
-
File Size-